Portable instrumentation that evaluates a machine’s condition at the asset is widely used to collect vibration data to quickly and accurately identify developing faults in rotating machinery. Machine oil condition monitoring yields other useful and critical information on machinery health, complementing the data provided by vibration analysis. Now, the same advantages obtained with routebased vibration collection and analysis and thermography are possible with route-based oil condition monitoring.
Changing oil on a calendar basis is rarely done at the correct time. Most of the time, the oil in a machine is changed far too often because without knowing the oil condition, there is no alternative but to change the oil according to an elapsed time interval.
With the newly-developed maintenance approach described in this article, oil is tested before deciding to service or change the oil. The cost of testing oil is almost nothing compared to the cost of the oil itself, so following this approach will result in overall savings. If the oil is fit for continued service, it can remain in use, yielding savings in several areas. The cost of the oil, labor for frequent oil changes, oil disposal, and any tools and materials needed to complete the oil change are avoided. The costs incurred by the potential for damage due to the intrusive oil change process are also eliminated with route-based maintenance. Finally, skilled personnel may be employed in other areas rather than always servicing the oil. It just makes sense; change or service oil based on its condition, not on the basis of calendar time, operating hours, or distance traveled.
No one likes changing oil. It is time consuming, costs a lot of money and can introduce problems that did not previously exist. It takes people, time, effort and availability to get oil analysis results before executing an oil change. So why not just test the oil and keep using it when useful life remains?
A New Solution to an Old Problem
Things are changing with the introduction of a new walk-around, route-based infrared spectroscopy tool. This new tool (see Figure 1) allows a lubrication technician to follow a planned route from machine to machine, testing a few drops of oil from each sample point to obtain the total acid number (TAN) of the oil, water content and oxidation levels for machinery oils in just one minute. This allows a real-time decision as to whether or not to change the oil based on the actual oil condition and the alarm limits for that particular component for TAN or water content. Other parameters are measured for engine oils. Table 1 gives the parameters measured by the oil application category. A new ASTM method describes the use of this instrument in ASTM D7889 – 13 Standard Test Method for Field Determination of In-Service Fluid Properties Using IR Spectroscopy.

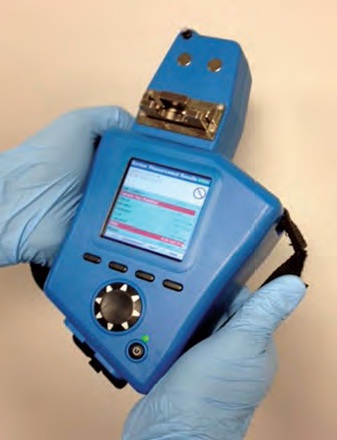
Figure 1: FluidScan® Q1100 Route-based IR spectroscopy tool.
Table 1 - Measured Fluid Properties by Oil Category
In addition to supporting an immediate oil change decision, all data, observations and other findings from walk-around oil analysis can be recorded on the handheld device and uploaded to a related software for trending, analysis and integration with vibration and other condition monitoring information.
A key element of this new solution is the ability to create and follow machinery oil condition inspection routes. A route is created on a desktop PC and downloaded to the device. The route information contains the measurement point identification along with the fluid type and the alarm limits associated with that lubricant.
Is This Like Route-Based Vibration Analysis?
With a route file, the technician is never going to make a mistake regarding measurement points, fluid identity, or alarm limits. Routebased oil analysis using infrared spectroscopy parallels walk-around vibration analysis, which is an accepted, proven practice for proactive and predictive maintenance in industrial plants. Proactively, it is used to detect root causes of failure and deterioration. Predictively, it is used to detect and trend rates of change as component damage progresses from incipient to catastrophic. The data collected by a device delivers outstanding returns on investment and results in more reliable plant operation.
Route-based oil analysis promises to be a powerful tool for proactive maintenance. Testing oil, rather than frequently changing it, extends drain intervals, thereby reducing costs.
Route-based vibration analysis was made possible in the 1980s with the introduction of lightweight, handheld, battery-operated fast Fourier transform (FFT) vibration analyzers, along with computer software to acquire and store the data, and analyze, trend, report and manage machine condition based on information derived from vibration waveform and spectral analysis.
Previously, a plant maintenance engineer experiencing a machine reliability problem would call for a pair of vibration experts to travel to the plant, install their sensors and vibration analyzers with data recorders, collect data for a day to analyze results, perhaps on the next day, and then report the results before packing up and leaving. That process took several days and only yielded results for one troublesome machine. Now, a typical walk-around vibration data collection and analysis program can instantly yield valuable data from a thousand machines.
The combination of oil and vibration analysis will provide far greater insight into the health of rotating industrial machinery, such as pumps, motors, compressors, gearboxes, fans, turbines and hydraulic systems. Oil analysis adds particulate contamination, water, other corrosive fluid contamination and inadequate lubrication details to information detected by vibration analysis so these issues can be corrected before damage occurs.
Keep the oil clean (free of abrasive dust and wear particles); keep the oil dry (free of moisture contamination) and fit for use (correct oil with the right viscosity and additive pack, and the correct oil level). Oil analysis can further complement vibration analysis for rotating machinery by detecting and trending particulate and ferrous wear debris, commonly resulting from abrasion, adhesion, fatigue and corrosion.
Figure 2: Correlation TAN and KF water by IR versus TAN by titration for in-service MIL 23699 oils.
Table 2 - Measured Fluid Properties and ASTM Methods
Laboratory Infrared Spectroscopy
Infrared spectroscopy has been used for decades to analyze in-service lubricants for detection of several troublesome issues. They include lubricant degradation from oxidation for any in-service lubricants and from nitration and sulfation for in-service engine oils, as well as lubricant contamination with either moisture or coolant. Most infrared spectrometers are benchtop instruments with graphical display outputs that must be read by a chemist to fully appreciate significance of subtle or obvious differences between baseline and reference spectra.
Recent technology developments1 have enabled infrared spectroscopy to measure and report TAN for industrial in-service lubricants and total base number (TBN) for in-service engine oils. This new capability, added to the many other measurements available from infrared spectroscopy, makes it a perfect choice in deciding whether to service or change the oil now. Table 2 provides measurement parameters and corresponding ASTM test methods, as well as a comparison to Fourier transform infrared spectroscopy (FTIR) methods.
Conclusion
A portable, handheld infrared oil analyzer now can be used on machinery oil condition routes, providing an immediate analysis to determine if the oil needs to be serviced or if it has remaining useful life. By testing oil in this manner, rather than automatically changing it, results in many benefits, including extended drain intervals and reduced costs.
References
- Spectro Incorporated. Using Infrared Spectroscopy for Determination of TAN and TBN in Machinery Lubrication Oils. Chelmsford, Massachusetts: Spectro Incorporated, April 2013.