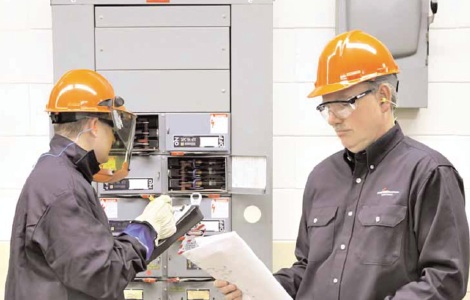
Competent and qualified permanent staff, contractors, or combinations of both are mandatory to ensure a smooth and well-functioning electrical system.
In the Ontario Health and Safety Act a "competent person" means "a person who,
- is qualified because of knowledge, training and experience to organize the work and its performance,
- is familiar with this Act and the regulations that apply to the work, and
- has knowledge of any potential or actual danger to health or safety in the workplace."
Furthermore, if they "organize the work and its performance," they are usually considered to be the supervisor. In electrical work, the supervisor is the "key component" when it comes to ensuring that work is completed safely, on time and in a manner in which it can be depended on by the process. This definition was written for health and safety, but it can be applied to work tasks at all levels and skills, not just safety. Defining what a qualified worker really means in the workplace is a point of debate in many instances. Competent, qualified electrical supervisors need to be developed and nurtured within their organizations. Too often, they are promoted from the ranks because of the great amounts of work they get done at the end of the day. This is admirable and important, but is just one segment of what an outstanding electrical supervisor must do.
They need to be masters of electrical safe work planning.
First and foremost, a truly competent and qualified electrical supervisor ensures staff safety, and secondly, takes great pride in the execution of their tasks in a timely manner. It must be in that order. Any other way is just not an acceptable cost morally, socially, or economically.
Electrical supervisors must be highly trained not only in the electrical skill sets required to complete the work, but in the skill sets to plan the work. Is this something your supervisory staff does? Do you have the training records to back it up? Does upper management go to the field and regularly audit the safe work planning skills of their electrical supervisors?
If the answers to the last three questions are "no," then your electrical workers are at risk, your electrical equipment is at risk and ultimately, the reliability of your plant is at risk.
How then do you proceed when looking for opportunities for improvement in the area of electrical safe work planning?
A simple five-step process is described here as one concept:
- Identification of "all" electrical hazards for any specific task
- Quantification of all identified hazards for any specific task
- Strategies based on the above two steps
- Document, document, document
- Communicate, communicate, communicate.
STEP 1:
All electrical hazards must be identified before starting work. In electrical work, this could include:
- low, medium and high voltage direct contact
- flashover
- induced
- step potentials
- arc flash/blast.
STEP 2:
All identified electrical hazards must then be quantified. This is relatively straight forward for electrical hazards A through noted above if done correctly, but not so evident for identified arc flash/blast hazards. They can be comprised of radiative and convective heat, dangerous decibels to ears, hazardous IR/UV to eyes, super heated noxious metal vapor harmful to lungs, shrapnel, molten metal and, of course, blast pressures. IEEE standard 1584 really only addresses the heat in cal/cm2. ArcPro software can do the same for single phase in open air with factors to be applied for three-phase in enclosures. Existing engineering formulas exist as well. The ongoing IEEE/NFPA Collaborative Research Project is doing much of this testing to give hard scientific evidence for most of these other hazards to be quantified. Additional information about this project can be viewed at: http://standards.ieee.org/about/arcflash/index.html
STEP 3:
Once all the hazards have been identified and quantified to current knowledge, supervisors must draft the required strategies to ensure safe work and no destruction of the electrical equipment, in particular from an arc flash/blast event.
The number one strategy bar none is TURN OFF THE POWER, complete with a comprehensive and effective Lockout-Tagout or Utility Work Protection Code. A high-level electrical supervisor is also a master of this strategy in the isolation and de-energization (grounding) of electrical equipment as required.
There should be justification for doing "energized work" from upper managers who are accountable and will sign off on it. Sometimes tasks like troubleshooting or diagnostics require energized work. If so, electrical utilities have very detailed and safe work practice procedures to follow. It is highly recommended that industrial establishments use the outstanding "Energized Electrical Work Permit" concept from current editions of the U.S.'s NFPA 70E or Canada's CSA Z462. Used correctly, these documents cover all the bases from an electrical safe work planning and due diligence viewpoint.
STEP 4:
Document, document, document.
It cannot be emphasised strongly enough just how important this step is. It is a critical component of Step 3. Electrical workers, and in particular electrical supervisors, who execute work using only "tribal knowledge" or verbal instructions as a work practice instead of written procedures, put themselves at risk of injury and put the plant's reliability at risk. If electrical task descriptions are not clear, concise and documented, the risk is much higher. Good documentation can also exonerate supervisors and upper managers from liability where extensive injury and/or destruction of plant equipment have taken place.
STEP 5:
Communicate, communicate, communicate.
An outstanding electrical supervisor who lowers the risk of injury to workers and reduces potential significant downtime to the plant is also a master communicator.
Master electrical supervisors know their crew. They get to know any electrical contractors that may be involved. They issue clear, concise and documented safety and work instructions at all times. They ensure that their crews listen and understand all portions of the work, otherwise they stop and regroup. They look for error likely situations and use repeat backs from their staff to ensure that they are totally engaged.
Upper managers need to audit supervisors' skill sets often for electrical safe work planning. If there are gaps, upper managers must get the supervisors the comprehensive training required.
Ultimately, every plant that wants to be safe, world-class, profitable and offer good, honest work to its community needs to ensure that their potential "Achilles heel" - their electrical system - is maintained by top guns in all phases of the work.
Having safe electrical work planning that is a recognized and valued component of your reliability chain and executed by competent and qualified electrical supervisors defines the statement, "Good Safety is Good Business."
Mike Doherty has over 36 years experience as a licensed industrial electrician, industrial instrumentation technician, control technician, electrical skills instructor, and utility safety department professional and electrical safety trainer across North America. He is Chair of CSA Z462 Technical Committee, Workplace Electrical Safety, Canada and an NFPA 70E Technical Committee Member, Electrical Safety in the Workplace - USA. www.ihsa.ca