In an address to the National Petrochemical and Refiners Association National Safety Conference in 2010, Jordan Barab, who is the Deputy Assistant Secretary for Occupational Safety and Health, said, "Bluntly speaking: Your workers are dying on the job and it has to stop."
Barab went on to say, "What I'm talking about is a set of practices that define the organization and influence the individuals who make up the organization. It goes without saying, but I'll say it anyway: Organizational safety culture must come from the top."

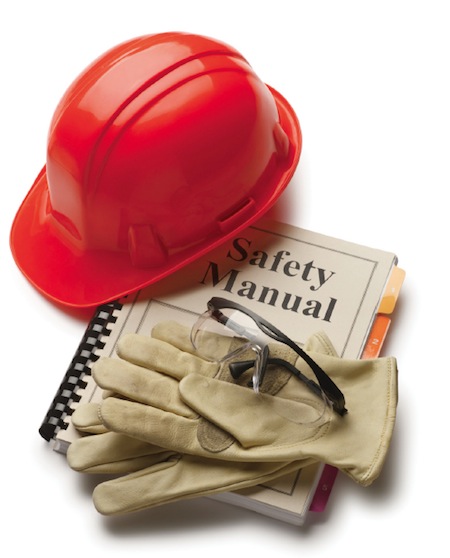
If we look at all industry in the US in 2009, there were 4,340 deaths. The injuries suffered by US workers are even more startling:
Total recordable cases 3,277,700
Cases involving days away from work 965,000
Cases involving sprains, strains, or tears 379,340
Cases involving injuries to the back 195,150
Cases involving falls 212,760
Think of it: if we fix some of the root causes of the fatalities or injuries more workers will go home to their families whole and intact.
There are many reasons for these injuries and fatalities. Some of the common ones include traffic accidents, falls, and a whole host of injuries and unfortunately fatalities from maintenance work. I want to discuss the maintenance-oriented injuries and fatalities. Following are some examples of serious accidents from OSHA records:
- A massive explosion destroyed a large storage tank containing a mixture of sulfuric acid and flammable hydrocarbons at the Motiva Enterprises Delaware City Refinery. One contract worker was killed, and eight others were injured. Sulfuric acid from collapsed and damage tanks polluted the Delaware River. The explosion occurred during welding operations to repair a catwalk above the sulfuric acid tank, when flammable hydrocarbon vapor was ignited by welding sparks.
- Crews were doing maintenance work on a generator while a pressure test was being done. That's when a manway blew off, after the compressed air inside was released, striking two contract workers, injuring them critically.
Why did these injuries occur?
Generally, accidents are grouped into 5 categories. According to Barab's address mentioned above, the areas are spread among many parts of the business.
Specification 44%
Changes after commissioning 20%
Operations and maintenance 15%
Design and implementation 15%
Installation and commissioning 6%
In this article, I want to focus on reliability of equipment. Problems in all of the categories above are causes of breakdowns. For example, in operations and maintenance a culture of expediency can contribute to procedures not being followed, design flaws, and workers not being careful. With all that going on, it is easy to see that non-standard situations can also occur.
Some of the accidents are the result of unsafe acts (hot work on a tank with an explosive mixture inside) or failing to follow procedures (pressure testing with personnel in harm's way). Of course, most accidents like these have several causes at the same time.
If we look at more maintenance-related fatal incidents, we can start to see a pattern.
- A tragic double fatality of welders on a petrochemical plant when an argon cylinder had been left leaking into the vessel they were due to work on. The first one went in and collapsed; the second, instead of raising the alarm first, went in after him, and they both died.
How are reliability and EHS related? The reasons behind the relationship are as follows:
Reason 1: Something was broken and had to be repaired. The breakdown caused the person to go into harm's way. So, lack of reliability can cause death and injuries.
Reliable equipment removes this cause, one of the common causes of accidents. We can be even more specific. Equipment running as designed does not require people to enter a confined space, repair (and touch) exposed electrical wires, pressure test a generator, sit on top of a tank and weld, or even fall off of a ladder.
How is reliability related to safety? Reliability removes risk from the equation, and the worker is not in harm's way. If no one was welding above the tank, the explosion would not have happened; if there was no repair needed, no one would gave been up on the ladder or on the roof.
A. Something breaks down and has to be repaired.
B. The breakdown causes a worker to be in harm's way.
C. Reliable equipment does not require maintenance workers to be put into harm's way.
D. The best solution to a hazard is to eliminate it.
Reason 2: Due to PM, the size and scope of repair is smaller, making for safer repairs.
The second part of the equation has been reported by Exxon-Mobil. They studied their maintenance-related accidents and found the following: "Accidents are 5 times more likely while working on breakdowns then they are while working on planned and scheduled corrective jobs."
High reliability implies an effective PM program that catches deterioration before it causes a failure. Since the asset is not yet broken, it is safer to work on.
A. PM activity catches deterioration early in the process before failure (and reliability is impacted).
B. At that point the repair is smaller, safer, and more manageable, resulting in fewer EHSS incidents.
C. PM also gives managers more time to plan and deal with hazards.
Reason 3: Hazards are eliminated or mitigated in the planning process.
High reliability also implies that the maintenance planners have time to plan the job properly. One aspect of planning is to consider all the hazards and figure out and describe a way to accomplish the work safely. The job plan that an experienced planner develops will reflect the safe way to do the job.
A planner should look at every job and see if any common hazards are present. Hazards would include: airborne contaminants, falls from heights, slipping and tripping, falling objects, eye damage (particle, chemical, or flash), chemicals (ingestion, skin exposure, or breathing), asphyxiation, radioactive exposure, fire, explosion, electrocution, entrapment and crushing, and temperature stress.
Every hazard identified is then eliminated (best option) or mitigated (second-best option). The safest plants are the ones where the safety of the workers is considered at every step in the job preparation process.
The planner plans the job to minimize downtime
The planner is specifically trained to look for hazards to safety, health, and environment.
Planners will mitigate or eliminate the hazard in the plan before the crew even leaves the shop.
The result is fewer EHS incidents and more reliable equipment.
Reason 4: Planned jobs allow fewer opportunities for the maintenance worker to improvise.
Improvisation is statistically less safe than following the job plan with the correct tools and spares. One of the building blocks of a reliable culture is adequate maintenance planning. Without planning, the workers are forced to make do with what spares and tools they can find. To do their job, they may have to improvise to make things work. Improvisation might be great in the theater but can be deadly in maintenance. My guess is that the following worker was making do with an improvised support:
Worker was performing maintenance on the back of a trash truck. The support gave way and the tailgate came down on the worker.
A. Improvisation is great in comedy.
B. Improvisation can be deadly in maintenance.
C. Adequate time for job planning means having the right tools, spares, equipment, skills, and drawings when the job starts.
D. The result is fewer EHS incidents and better reliability.
Reliability is the outcome of this intentional maintenance environment and is essential for a safe environment.
Action items
Management action items to transform the culture require minor modifications to the weekly and monthly Key Performance Indicators (KPI) used to run the plant or facility and for bonuses.
- The ratio of emergent maintenance work to planned and scheduled maintenance work should be maintained above 80% planned and scheduled to reduce emergent jobs.
- PM performance should be above 95%. More than 95% of the PMs generated are completed in ±10% of the PM interval.
- Schedule compliance above 85%. That means more than 85% of the jobs scheduled are completed sometime during the week in which they are scheduled.
- MTBF for major assets should be on an improving trend.
What if your plant doesn't measure up? Then it is time to change the culture. However, changing a culture takes time and will take three attributes:
- Follow-through to keep people's eye on the goals
- Resilience to get the plant back on track when the program goes off the track
- Positive attitude: just like when teaching a child to ride a bike, keep up a positive, encouraging attitude. Don't punish honest mistakes; make sure your people learn from them.
Exxon-Mobil studied their maintenance-related accidents and found that accidents are 5 times more likely while working on breakdowns then they are while working on planned and scheduled corrective jobs.
Good luck, Joel
Joel Levitt is a leading trainer of maintenance professionals. He has trained more than 15,000 maintenance leaders from 3,000 organizations in 20+ countries in over 500 sessions. Since 1980 he has been the President of Springfield Resources. He has 25 years of experience in many facets of maintenance. Levitt has served on the safety board of ANSI, Small Business United, and National Family Business Council and on the executive committee of the Miquon School. He is a member of AFE and Vice President of the Philadelphia chapter. www.MaintenanceTraining.net