Schneider Electric Selects Simio for Wonderware MES Scheduling Capabilities
Now Wonderware MES 2014 software users have improved capabilities to determine the best detailed production schedule scenario to help meet delivery deadline challenges.
Schneider Electric offers the industry’s leading Wonderware manufacturing operations management software. Simio 3-D simulation-based planning and scheduling software innovations help users meet production deadlines more often at less cost. With this partnership, Simio and Schneider Electric will help customers improve productivity, increase business agility and deepen quality management while reducing the cost of compliance.
Tom Troy, director, operations & asset portfolio, Schneider Electric, predicts this game-changing partnership will benefit Wonderware and Simio users alike.
“The real-time production data our Wonderware MES software provides is essential for accurate, timely simulation-based scheduling,” Troy said. “This has been a challenge with traditional MES offerings. But our partnership with Simio allows our customers to easily add a real-time scheduling component, using a rules-based engine and deep simulation. It’s an offering unmatched in the market today. To remain competitive, manufacturers need to move beyond command and control and into operations optimization, problem resolution and workforce improvements. This partnership allows them to take that first step, and our customers will be able to rely on Wonderware and Simio offerings to lead the way.”
Simulation models point out problems in production schedules
According to Dr. Dennis Pegden, chief executive officer, Simio LLC, “Simio differs from traditional scheduling software because it provides planners and master schedulers a quick way to see the odds they will hit delivery and cost targets, especially after an unexpected situation occurs.” For example if a new, important order arrives or a machine breaks down, or workers don’t show up or supplies are late, users can re-run their schedule in minutes, taking into account the recent situation to find the best new production schedule scenario.

Color-coded key risk indicators (KRI) show problem orders
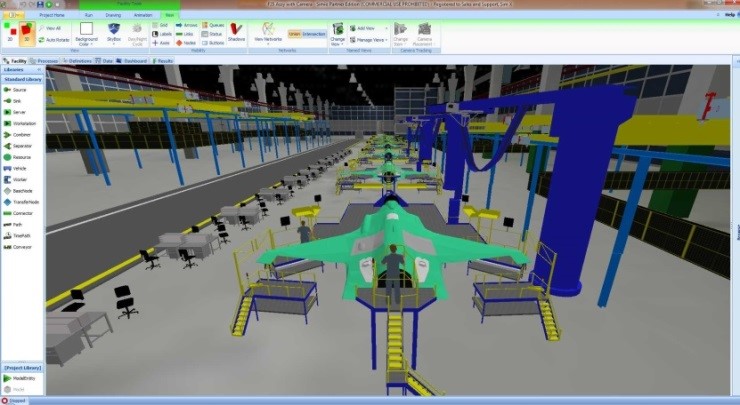
Once the schedule has been generated, Simio then re-runs, in minutes, a new schedule factoring in the recent problems that occurred. “Users can then see how changes in production can affect deliveries” Says Sturrock.
Payoff
The payoff users experience with Simio simulation-based scheduling is a higher percentage of on-time delivery accompanied by decreased overtime, meeting training goals and a more accurate way to evaluate capital investment proposals.
About Simio LLC
Simio LLC is a private company headquartered in Pittsburgh Pennsylvania dedicated to delivering leading edge solutions for the design, emulation, and scheduling of complex systems.
Simio was founded by a highly experienced team. C. Dennis Pegden, Ph.D., Founder and CEO of Simio LLC, has over 30 years of experience in simulation and scheduling and has been widely recognized as an industry leader. He led in the development of SLAM (marketed by Pritsker and Associates) and then founded Systems Modeling Corporation. Dennis led the creation of the market-leading simulation products SIMAN® and Arena®, as well as the finite capacity scheduling product Tempo. To learn more visit Simio.