Siete años de confiabilidad sostenida y Cambio Cultural en Alcoa Warrick Smelter
La historia comenzó en 1997, cuando Alcoa decidió aplicar el Sistema de Producción Toyota a nivel mundial en sus 250 locaciones. Se realizaron progresos significativos, pero laos líderes de la división Primaria de Metales de Alcoa no estaban viendo los resultados que esperaban. Un análisis interno de negocio a nivel de unidad demostró que a sus procesos de confiabilidad y activos les faltaba estabilidad, y este fue el motivo por el cual la manufactura esbelta se mantenía cautiva. La estabilidad es un elemento fundamental para el Sistema de Producción Toyota. Si uno está familiarizado con la Casa de Toyota, o cualquier otra casa para el caso, tener una base sólida es la clave para la sostenibilidad a largo plazo. (Ver Figura 1)

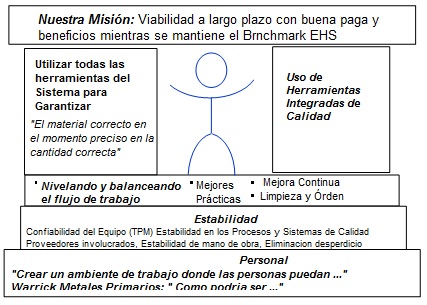
Figura 1
En el 2002 Vince Adorno, Vicepresidente de Ingeniería de Metales Primarios de Alcoa, decidió formar un equipo corporativo para desarrollar un modelo de negocio y una estrategia de implementación de confiabilidad. Se incluyeron consultores externos en este proceso para asegurar que las mejores prácticas y estimaciones razonables de los ahorros potenciales se incorporaron en la estrategia. También buscaron sus propios modelos de excelencia y mejores prácticas que se habían establecido en las plantas.
Durante estas sesiones, Ron Moore, del Grupo de Ron Moore dijo: "Usted tiene demasiado 'mantenimiento' en su esfuerzo de confiabilidad." El equipo de Alcoa acordó que se centrarían en la mejora de la organización de mantenimiento y se perderían oportunidades de mejora por no considerar el impacto de la operación en la confiabilidad del equipo. Sus esfuerzos en ese momento estaban siendo impulsados por los gerentes de mantenimiento e ingeniería en cada complejo industrial con poca participación de Operaciones. Además, una tasa alta de rotación de Administración, dificultaba un enfoque a largo plazo sobre confiabilidad, y estaba haciendo una capacitación continua y una necesaria recapacitación de los líderes clave.
Moore explicó que la organización de mantenimiento son responsables de muchas funciones, pero no tienen control directo sobre el éxito de estas funciones. Por esta razón, el éxito de la confiabilidad sólo se puede lograr a través de una colaboración activa entre el mantenimiento y operaciones. Moore llamó a este concepto "Confiabilidad basada en Operaciones" como se ilustra en la Figura 2.

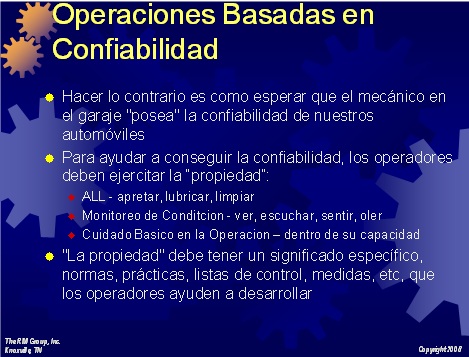
Figura 2
"La propiedad" debe tener un significado específico, normas, prácticas, listas de control, medidas, etc, que los operadores ayuden a desarrollar
La Estrategia
Los líderes corporativos comenzaron a desarrollar una estrategia que incluye un modelo en el que los gerentes de planta y los líderes operacionales manejaran su propio esfuerzo de confiabilidad. Además, querían que todos sean responsables de la confiabilidad, tal y como son en materia de seguridad.
La propiedad se inició a través del desarrollo de un modelo de negocio sólido para los esfuerzos de mejora de la confiabilidad. Este modelo de negocio se vería reforzada con los datos existentes de mejores prácticas en las plantas de Alcoa en la red, así como con los datos de referencia de otras plantas externas.
Las reglas básicas para el retorno de la inversión era que no, y no debe, provenir del aplazamiento del mantenimiento. Los ahorros deben de venir del presupuesto de Reparación y Mantenimiento (R & M) de las instalaciones, con un entendimiento de que el aumento de la producción, a través de una mayor estabilidad, podría aumentar el rendimiento y eliminar los residuos. Esto se estima que será mucho mayor que el ahorro en mantenimiento.
El grupo estima que podría reducir los costos de reparación y mantenimiento (R & M) de 10% a 20% en un período de tres años, y predecir que por cada dólar de mantenimiento ahorrado por la eliminación de defectos, se darían cuenta de 1.5 a 6 veces más que en la Efectividad Total del Equipo (por sus siglas en inglés OEE, Overall Equipment Effectiveness) de ganancia. La estrategia de producción fue la implementación de OEE, calcular el valor de un incremento del uno por ciento en la OEE, y utilizar este conocimiento para eliminar los malos actores o defectos que posteriormente impulsan la mejora de la planta.
Después de haber desarrollado el caso de negocio para la mejora, el próximo reto del grupo era crear una estrategia para educar a la organización, determinar las lagunas existentes en las mejores prácticas de confiabilidad, e implementar los cambios necesarios. Un proceso de tres etapas se desarrolló con el fin de crear un Programa en Fases ordenado y sostenible. (Ver Figura 3)
Figura 3
La primera Etapa se centrará en educar a la planta de lo que significa la excelencia en confiabilidad, consolidando el patrocinio y la creando la alineación necesaria con el equipo de administración, los líderes sindicales y la fuerza laboral. La segunda etapa evaluaría el desempeño actual del sitio, utilizando un Modelo de Excelencia en Confiabilidad de 29'Elementos, o lo que Alcoa eventualmente llamaría "REX". (Ver Figura 4)
Modelo de Excelencia en Confiabilidad
Figura 4
Un plan maestro se crearía entonces para cerrar las brechas, y un modelo de negocio se desarrollaría para mostrar el valor de alcanzar la excelencia en la confiabilidad en cada sitio.
La tercera etapa sería la formación de un equipo de liderazgo para manejar los cambios y enfocaría a los equipos para ejecutar las tareas en el plan maestro que iba a cerrar las brechas en las mejores prácticas. Se le daría seguimiento a los beneficios, y los procesos de auditoría se iban a poner en marcha para garantizar la sostenibilidad. Se eligió una ubicación piloto para que sirviera como prueba del proceso. Aquí es donde Warrick entró en escena. . . .
Metales Primarios Warrick
En el otoño del 2003, Royce Haws, el Gerente de Planta de Warrick Smelter fue contactado por Vince Adorno, Vicepresidente de Ingeniería y Mantenimiento. Adorno informó a Haws que Warrick había sido recomendado como el sitio piloto para el proceso de la Etapa tres. Los costos de Warrick estaban entre los más altas en las unidades de negocio de Metales Primarios. También existía la posibilidad de que la planta cerrara prematuramente. Aunque los desafíos eran grandes, los líderes de la planta estuvieron de acuerdo en continuar.
Para sentar las bases del conocimiento para saber qué esperar y cómo manejarlo, Haws y su jefe de mantenimiento, Danny Reyes, comenzaron un viaje educativo para mejorar su conocimiento y la comprensión de las estrategias y técnicas para crear la excelencia en la confiabilidad en la manufactura y el mantenimiento.
Este programa de educación inicial fue seguida por una mejor evaluación de las mejores prácticas de confiabilidad con los datos recabados e incluyó entrevistas con gerentes, supervisores, técnicos y operarios. La puntuación de la planta fue de 441 de un total de 1000, lo que indica que Warrick estaba en un modo predominantemente reactivo, con el mayor enfoque en ser realmente buenos en la respuesta para el mantenimiento de emergencia. Las oportunidades de mejora eran considerables, pero un cambio de cultura importante sería necesario si el sitio quería lograr el caso de negocios que habían desarrollado. El liderazgo de la planta prestó especial atención al Plan Maestro en términos de lo que había que hacer para cerrar las brechas en el Mantenimiento, Operaciones y en la cultura, con el fin de tener éxito.
Un equipo de liderazgo se formó para dirigir lo que se llama ahora el esfuerzo "REX", incluyendo la creación de los principios rectores y medidas necesarias para dirigir la organización en un entorno dinámico. El equipo desarrolló y ejecutó un plan de comunicación que incluyó reuniones de tipo "Foros Abiertos". En estas reuniones los líderes de la Planta comunicarían a la organización porque estaban implementando REX. Explicaron el porqué la ayuda de todo el personal era necesaria para alcanzar las metas y disfrutar de la seguridad del empleo a largo plazo. Tanto el personal asalariado como el sindicalizado fueron elegidos para participar en los equipos de atención que diseñarían el estado futuro de los procesos de negocio, cómo cada parte de la organización necesita para funcionar y cuáles son sus funciones estaría en esta nueva forma de operar. La premisa central de esta nueva forma de pensar era que la parte operativa de la organización sería la propietaria de la confiabilidad de los activos.
Liderando el Cambio
El Compromiso del gerente de la planta fue escuchado claramente en las reuniones de Foro Abierto. Haws compartió que los costos de R / M de Warrick eran casi los más altos en el sistema de fundición de Alcoa y era necesario reducirlos un 15% -20%. "Yo señale que podíamos hacer esto de la Manera Estúpida o de la Manera Más Inteligente", explicó Haws. "La Manera Estúpida fue aplazar el Mantenimiento unos cuantos años, evitar el pago de los consultores externos, y yo pudiera esperar por una promoción antes de que la Alta Dirección descubriera que la reducción de costos no era sostenible".
Haws entendió lo que él llamo el enfoque estúpido, porque esa era la condición de la planta que heredó cuando se trasladó a Warrick cinco años antes. Sabía que la manera más inteligente era acercarse a esta nueva oportunidad como una transformación potencial de una instalación de 43 años de antigüedad. Warrick tuvo una "plataforma en llamas" o un caso de negocio para impulsar el cambio. Menos del 5% de la capacidad del mundo para la fundición de aluminio se realiza en plantas que tienen más de 50 años de antigüedad y Warrick tenía 43 años. En la década de 1970, había 33 fundidoras de aluminio operando en los EE.UU., actualmente sólo hay ocho.
Debido al respeto que los gerentes de área tenían para Haws, su jefe de planta, se "subieron al barco", y comenzaron a preguntar lo que podían hacer para ayudar, y comenzaron a aprender más acerca de este nuevo enfoque para el mantenimiento de activos de la planta. Es cierto, muchos se preocupaban de esta nueva iniciativa podría convertirse en otro programa del mes.
El equipo de liderazgo se fue a trabajar y redactó una declaración de misión, los planes de comunicación en la planta, los principios rectores y los acuerdos de participación. El equipo también desarrolló un método y proceso para la captura de los datos de producción que más tarde sería utilizado para el cálculo de la OEE y de la gráfica de Pareto para los malos actores.
Se eligieron parámetros de medición adicionales, pero lo más importante, la responsabilidad de estos parámetros adicionales tenían que ser determinados. Haws decidió que los gerentes de producción serían ahora los responsables de los parámetros de mantenimiento como el cumplimiento del PM, cumplimiento de la programación y del costo de mantenimiento. Ahora sería la responsabilidad de la organización de mantenimiento apoyar a Operaciones para el logro de las metas de las mejores prácticas. La organización de mantenimiento ahora sería responsable de más indicadores, como porcentaje de Planificación de trabajo y de la eficiencia de la programación, backlog, del diagnóstico de PdM vs el trabajo correctivo, por nombrar algunos.
"La Asignación de responsabilidad de esta manera, marcó el comienzo de un cambio cultural importante", señala Marcos Keneipp, quien se desempeñó como facilitador en la implementación de RES en Warrick. "Necesitamos de recursos externos para que nos enseñen a cambiar los principios de administración que necesitemos para continuar llevando a esta organización a través de este cambio cultural. Tanto los expertos en Excelencia de Confiabilidad como los expertos en Administración del cambio, Lyfe CYclee engineerings nos ayudó a navegar a través de los cambios técnicos y culturales. "
El equipo de liderazgo realizo otra pregunta clave: "¿Por dónde empezar" En un largo debate, el equipo consideró factores como el área de la planta traería los mayores beneficios económicos y donde el éxito era muy probable desde un punto de vista cultural y de liderazgo. El grupo decidió concentrarse en el área de los servicios de aluminio. El éxito en esta área piloto más tarde se convertiría en el modelo para el resto de la planta.
En un largo debate, el equipo consideró que factores como el área de la planta traería los mayores beneficios económicos y donde el éxito fue muy probablemente de un punto de vista cultural y de liderazgo. El grupo decidió concentrarse en el área de los servicios de aluminio. El éxito en esta área piloto más tarde se convertiría en el modelo para el resto de la planta.
Reingeniería del Procesos de Trabajo
El Equipo de Enfoque comenzó con la reingeniería de los procesos de administración del trabajo, los procesos de administración de materiales y procesos de ingeniería de confiabilidad. Se definieron las funciones y responsabilidades. Se presentaron nuevos procesos re-diseñados y funciones al equipo de liderazgo y fueron aprobados para su respectiva capacitación e implementación en el área piloto.
Las reuniones de Planeación y Programación fueron re-diseñadas a manera de que la planeación y la coordinación de los trabajos se realizará antes de la reunión por grupos más pequeños para que el enfoque en la reunión de "programación" fuera sólo eso, programar o decir "cuando" se haría el trabajo. Los gerentes de producción ahora se encargarían de priorizar y programar el trabajo con el departamento de mantenimiento fungiendo un papel de asesoramiento. Una verdadera alianza estaba empezando a formarse.
Cada semana un trabajo programado de la semana siguiente, era elegido para su revisión de la semana siguiente con el fin de criticar de lo bien que paso para que el grupo pudiera aprender de los éxitos y fracasos.
Los Operadores estaban poniendo mucha atención a la forma en la que operaban los Activos y empezaron a remitir solicitudes de trabajo en el Sistema Computarizado de Administración de Mantenimiento (SMMS por sus siglas en inglés). También comenzaron a recopilar Datos del Tiempo de Inactividad y comenzaron a trabajar con los ingenieros de Confiabilidad para elimina las fallas recurrentes. El cambio de las responsabilidades para la Confiabilidad estaba creando ahora la necesidad de ayuda por parte de los Ingenieros de Confiabilidad para que los Objetivos de la OEE se pudieran lograr.
Los Ingenieros de Confiabilidad corrigieron las jerarquías de los equipos y asignaron códigos de criticidad a los activos. Se realizaron análisis de efectos y modo simplificado de fallo en el área piloto de activos por los ingenieros que establecieron las bases para la optimización de PdM y PM.
Una atención especial se puso en las piezas y materiales tanto por el equipo de enfoque de Administración de Materiales como por los planificadores. Las partes obsoletas fueron puestas a disposición y se acondiciono un área especial para formar paquetes de piezas para poner todo el material junto para cada trabajo planificado. Un sistema de etiquetado con códigos de color se puso en marcha para facilitar el reconocimiento visual para conocer en que parte del proceso se encontraban las partes (piezas) o materiales. (Vea las figuras 5 y 6)
Figura 5
Figura 6
El Liderazgo activo dado resultados significativos
El proceso de implementación REX también incluyó un "Equipo de Liderazgo REX" responsable de impulsar la aplicación de la Etapa 3 del Plan Maestro. Esta Etapa incluyó casi 140 puntos de acción, 20 de estos eran propiedad del Equipo REX. A la fecha, siete años después, el Equipo de REX sigue reuniéndose mensualmente para discutir las oportunidades.
Se observo rápidamente una mejora en la productividad y en las asociaciones en el área piloto y, posteriormente, los planes de despliegue se desarrollaron para implementar los cambios en toda la planta. Los gerentes de operación fueron los responsables de implementarlos en sus respectivas áreas. Esto señaló a cada área que esto no era una "iniciativa del Departamento de Mantenimiento."
El progreso fue lento, pero los beneficios estaban aumentando. Cuando se inició este esfuerzo, los costos de mantenimiento eran excesivos. En 2004, Warrick se dio cuenta de una reducción del 11% en costes de R&M y otro 2,4 millones dólares/año en mejoras relacionadas con las utilidades de OEE en comparación con nuestra base REX 2003. Los beneficios continuaron en el 2005, con ganancias en OEE llegando a 4.4 millones de dólares por año y los costos anuales de mantenimiento se redujeron en un 15% de nuestra base de REX 2003.
Tan importante como los resultados fueron, el viaje para mejorar la confiabilidad no había terminado. El líder de Warrick Metales Primarios, creía que ahora se necesitaba optimizar las mejoras que había hecho con el fin de continuar con su progreso.
Optimizando Resultados para Continuar el Progreso
El año ahora era 2007 y el viaje no había terminado. A pesar de los importantes beneficios económicos logrados, la planta aún estaba lejos de la meta inicial fijada por los directivos de la planta. Lograr esa meta iba a requerir más cambios. Aun se necesitaban optimizar miles de tareas de prevención, modificar estructuras de organización, y el tramo de control para los planificadores tenía que ser ajustados. Un cambio cultural continuo era necesario para su éxito.
Joe Cohen, Gerente de Mantenimiento de la Fundición explica: "Teníamos que estar todos dentro. En otras palabras, cada uno de los veintinueve elementos [del Modelo de Excelencia de Confiabilidad] tuvo que ser enfocado y optimizado para lograr la mejor práctica." Esto requeriría que todos desempeñaran un papel. Hubo cierta tentación de "selección la cereza" de los 29 elementos, pero el liderazgo decidido abarcar todos los elementos. La Etapa 3 de REX, fue vista como un modelo integral con los elementos conectados en formas que no podrían ser separadas para lograr los resultados deseados.
El personal de mantenimiento y operaciones revisó cada tarde de PM durante los Eventos de PM kaizen. Las estimaciones eran inexactas y las tareas anticuadas. Las tareas de mantenimiento preventivo (PM) implementadas hace más de 20 años eran de 4 a 16 horas e incluía el tiempo para hacer una inspección y luego arreglar lo que se encontraba. Esto era debido principalmente a que el Departamento de Mantenimiento no sabía si el Departamento de Operaciones pondría a su disposición la maquina después para hacer el mantenimiento, por lo que se creía mejor hacerlo todo al mismo tiempo mientras la máquina estaba fuera de operación. Las máquinas estaban paradas por horas mientras se buscaban las piezas y herramientas especiales y equipos para hacer el trabajo.
En palabras de Kuhn, "nos quitamos lo estúpido." Las mejoras fueron visibles inmediatamente. Las reparaciones ya no se hacían durante el PM. Se reportaron los resultados, para después ser planificados y programados. Este fue un gran "abre ojos" para la organización. Muchas tareas se sustituyeron por las tareas basadas en la condición. El Mantenimiento Predictivo (PdM) fue llevado al siguiente nivel. En el 2003, el trabajo de PdM fue sólo el 1.5% de las horas totales de mantenimiento. Hoy en día alrededor del 14% del total de horas es de diagnóstico y trabajo correctivo de seguimiento. Kuhn señala que todavía hay muchas oportunidades de mejora: "lo ideal sería el quince por ciento de diagnóstico, y treinta y cinco por ciento de trabajo de seguimiento de corrección de PdM".
Anteriormente, el grupo de mantenimiento trataba de optimizar su enfoque de que" trabaje-hasta-que-falle". Kuhn comparte un ejemplo: ". Nos gustaría tener datos de análisis de aceite que indicaran que la falla funcional se había iniciado en una caja de engranajes de $ 15,000, pero trataría de hacerla funcionar por otros seis meses y esperanzados de reemplazarla justo antes de que le saliera humo por lo caliente" Hoy en día tienen nueve técnicos por hora, realizando diversas tareas de diagnóstico de PdM en toda la planta. El programa de mantenimiento preventivo y predictivo está basado en el modo de fallo. Además, actúan sobre los datos el mismo día, e inmediatamente planifican y programan el trabajo de seguimiento. Algunas tareas se trasladaron también a los operadores. Como resultado de este esfuerzo masivo, se eliminaron 55.000 horas-hombre del programa de PM. Una vez más, un número significativo de estas horas ahorradas fueron asignadas en los esfuerzos del diagnostico del mantenimiento predictivo y seguimiento de mantenimiento correctivo.
El objetivo era llegar más alto en la curva de Falla Potencial (curva PF).
Desde el comienzo de la iniciativa, se había producido un intento de enfocar la organización de mantenimiento en los tres tipos de mantenimiento: preventivo, de emergencia, y alivio del retraso (backlog). el Trabajo de emergencia se había mantenido alto, lo que continuaba desviando los recursos de PM y reducción en los trabajos de Backlog. el Liderazgo decidió instalar un equipo central que se encargaría de las emergencias a través de la planta, tanto para trabajos mecánicos y eléctricos, mientras que la mano de obra restante se centró en la ejecución de los trabajos de PM y del backlog planificado. El mensaje que el trabajo de emergencia es malo fue comunicada a través de signos en toda la planta. (Ver Figura 7)
Figura 7
Kuhn atendió el vacio de control para los planificadores. Ahora eran medidos en el porcentaje de trabajo planeado que en realidad estaban produciendo. Se revisaron los parámetros de los Planificadores debido algunas expectativas previas estaban conduciendo hacia un mal comportamiento. Anteriormente, golpear los números esperados por el corporativo era más importante que la calidad o eficiencia de la labor que se ponía en el programa. Los Lideres comunicaban a la organización que era aceptable que los números fueran más bajos, pero precisos, de modo que las barreras a las mejores prácticas podría ser eliminada. Keneipp, el implementados de REX en el complejo de Warrick, reflexiona: "Todos los esfuerzos estuvieron dirigidos a reducir los costos y aumentar el OEE, que fueron los resultados finales que estábamos tratando de lograr. La calidad de los trabajos de mantenimiento se convirtió en algo más importante que cuan rápido se reparaba algo. "
Las Órdenes de Trabajo en espera fueron expulsadas del Sistema. Datos más precisos de la reparación de los Activos, indicaron que la llamada de emergencia tenía un costo Promedio de $ 500 dólares. Kuhn comunico esta cifra a los Líderes de Operaciones que eran responsables del costo del Mantenimiento. Todo el Equipo se dio cuenta de que el Priorizar el trabajo correctamente ahorraría Dinero significativamente.
El almacén era también un área de alto costo, debido a la inexactitud de inventario y los altos índices de stock bajo. Con los años, esto contribuyo a que se acumularan "montones de partes" en torno a toda la planta donde los técnicos mantenían las piezas de repuesto para asegurar que estarían a la mano cuando fuera necesario. Otro problema fue que el 40% de las piezas de repuesto en el almacén eran "huérfanos", es decir, que no se asociaban con una factura de materiales.
Para mejorar la eficiencia, se pusieron en marcha programas de reabastecimiento de proveedores con entrega de piezas para el trabajo planeado. El almacén fue creado para albergar las piezas necesarias solo para las emergencias. El mejorar la confiabilidad de la planta era también reducir los costos de materiales. Las fallas de motor y caja de cambios ya no se producen semanalmente. Hoy en día, alrededor del 50% de las piezas de repuesto vienen directamente de los proveedores y casi no se almacenan. Este es un beneficio importante de la planeación y programación de trabajo de cuatro a seis semanas de antelación. "En realidad", Kuhn señala, "un almacén es sobre todo una gran contramedida para el mantenimiento de emergencia."
La Administración continuó reforzando el mensaje que la confiabilidad era muy importante. El plan de comunicación incluyó conversaciones uno-a-uno con los empleados y la concesión de incentivos. Por ejemplo, la calidad de la información sobre los PM había sufrido en los últimos años. Debido al hecho de que el trabajo de seguimiento correctivo era programado en raras ocasiones, los técnicos a menudo no llenaban los informes de PM. Ellos lo veían como una pérdida de tiempo. Para superar el problema, los técnicos fueron reconocidos por comentarios detallados sobre las órdenes de trabajo. Los operadores también fueron reconocidos por solicitudes de trabajo precisas y detalladas. Este tipo de comportamiento fue recompensado con tarjetas de regalo de $ 25 - $ 100 dólares. La Administración se enfoca en que las ordenes de trabajo solicitadas sean introducidas correctamente, los resultados programados y ejecutados, y los resultados comunicados a los empleados.
Sosteniendo los logros
Alcoa Warrick se ha encontrado con muchos baches en el camino en el largo viaje hacia la excelencia en la confiabilidad, pero se han logrado resultados significativos tanto cultural como económicamente. El reto en los últimos años ha sido mantener los logros. Varias áreas de enfoque han ayudado a asegurar la sostenibilidad:
Aprovechando el poder de Ingenieros de Confiabilidad: Cuando REX fue implementado por primera vez se descubrió que los actuales ingenieros de confiabilidad estaban, de hecho, haciendo todo el trabajo de ingeniería de proyecto. Dos ingenieros de confiabilidad ahora son asignados a centrarse exclusivamente en "los Principales 10 malos actores" y en el análisis de causa raíz de las fallas. Su trabajo es evitar fallos recurrentes y rastrear el beneficio en dólares en toda la planta. Los gerentes de operaciones les llaman para solicitar ayuda para que desaparezcan los problemas.
Liderazgo sólido a largo plazo: Este fue un factor clave de éxito. Haws, el gerente de la planta, se mantuvo en el timón y siguió pidiendo a sus gerentes cómo podía ayudar. Este tipo de apoyo permitió a los miembros del equipo directivo a asumir riesgos, como la reorganización y el cambio de las expectativas de los parámetros. El liderazgo activo es crucial para la creación de la asociación entre el mantenimiento y las operaciones que continúa a la fecha. Como prueba, la Fundición Warrick tiene una fuerza de trabajo directa asalariada de alrededor de 85 personas y 20 de estas personas están certificadas como CMRP (Certified Maintenance Reliability Professionals). Muchos de estos CMRPs están en operaciones.
Evaluar periódicamente los progresos: frecuentes reevaluaciones son otro factor clave para la sostenibilidad. LCE se le pidió que vuelva a evaluar la Fundición de Warrick en una frecuencia de 18 meses. Warrick inició con una puntuación de 444. En 18 meses, se puntuación mejoró a 555. Dentro de otros 18 meses mejoró a 603. Dieciocho meses más tarde el marcador se elevó a 719, colocando Warrick en el rango dinámico.
Conclusión
Entonces, ¿dónde está ahora Warrick, siete años después de su viaje REX?
La salud de los activos de la fundición de 50 años , mejora en gran medida a partir de 2003 cuando se inició REX. Mark Keneipp señala: "Recuerdo todos esos principales componentes como motores, cajas de cambio, y bombas de $ 10,000 a $ 25,000 que solkian fallar inesperadamente a horas intempestivas? Rara vez sucede ahora, y cuando sucede, realiamos un análisis de causa raíz para reducir las posibilidades de que vuelva a ocurrir. "Los resultados financieros son impresionantes. Los costos de mantenimiento por tonelada se han reducido en un 38% (ver Figura 9), y en el 2010 la ganancia OEE actual es de 5.8 millones dólares sobre la base 2003 REX. Los informes de progreso trimestrales se generan de manera que se pueden hacer comparaciones con otras plantas de Alcoa y las mejores prácticas se comparten a nivel mundial.
Figura 8
El viaje ha sido difícil, pero las recompensas han sido muchos. Alcoa Warrick ha eludido la amenaza de cierre y se ha convertido en un modelo para otras plantas para seguir en el camino a la excelencia.