The T3 sound locator acoustic horns in Figure 2 were used by the U.S. Army Signal Corps, the U.S. Army Coast Artillery Corps and others to listen for approaching aircraft and ships navigating area rivers. As Figure 3 shows, these types of sound locators were in use at Bolling Field in Washington, D.C., in 1921. Of course, once radar was invented, these units were seldom heard of again.
Years ago, I was invited by NASA in Cape Canaveral, Fla., to give a demonstration in its Vehicle Assembly Building (VAB), as seen in Figure 4. I was to demonstrate the use of the 18-inch ultrasonic parabolic reflector (Figure 5a.) for detecting air leaks on engine bleed air ducts of a space shuttle engine from ground level during maintenance on the space shuttle's build-up phase.
The VAB is one of the largest buildings in the world. It covers eight acres and is 525-feet tall, 716-feet long and 518-feet wide. It encloses 129,428,000 cubic feet of space and has two space shuttle build-up bays - high-bay and low-bay. The area I was brought into was called the low-bay and contained Space Shuttle Atlantis' main engine maintenance and overhaul shops.
The parabolic reflector I was to demonstrate had seven fixed transducers in an array at the focal point of the parabolic dish. It was coupled to the ultrasonic receiver (pistol) by an auxiliary cable. The ultrasound receiver receives the high-frequency signal, amplifies and then heterodynes it to a low-frequency signal to be heard with headphones. The dish reflects the sound wave to the focal point.
I listened while my sponsor, an engineering technician, explained that during maintenance and build-up of the space shuttle, maintenance may include removal, installation, or repair of the engine bleed air ducting and associated piping. After installation or repair, it is necessary to pressurize and leak test the system. Due to the many floor levels situated next to the shuttle and engine during build-up, he would like to detect a leak from ground level (30- to 60-feet away). He would then like to enter one of the four elevators (each corner of the building) of the low-bay and exit onto the correct floor level and not keep changing floors to locate the leak.
While I stood at ground level below the engines scanning for leaks of the pressurized bleed air system, it became apparent that with the current configuration of the ultrasound pistol coupled to the 18-inch parabolic reflector, we could in fact detect a leak. But we could not correctly define the floor level from 30- to 60-feet away.
An ultrasound receiver is an excellent instrument to detect the high-frequency shortwave properties of the leak. It does not require line-of-sight to detect the leak either. But after several attempts, we were still unsuccessful in identifying the correct floor level. The massive amount of tubes in close proximity to each other, as well as reflection of sound, made it very difficult.
Fast forward a few months later. I was again invited to come back to the VAB's low-bay, but this time the engineer had what he described as a "parabola horn." This device looked homemade. It appeared to be a machined aluminum seven- to eight-inch horn with a three-inch opening at one end and a single piezoelectric transducer mounted at the other end, a battery pack and a cheap set of headphones. It resembled an electronic kit you might buy from a five-and-dime store.
However, due to the slightly more narrow focus of the parabola horn, it enabled us to detect both the leak and the correct floor level. However, the horn was not as focused as the dish for leaks at distances beyond 50 to 60 feet.
NASA later patented and exclusively licensed the parabola horn to an ultrasonic instrument manufacturer for commercial applications (see Figure 5b).
A year or so later, NASA's study of the parabola horn led to the development of an ellipsoidal3 horn (see Figure 5c). This was made by producing an ellipsoidal design (squashed sphere) and cutting it in half. This half-ellipse or half-horn (see Figure 6) is three-inches in length and has a one-inch opening. The purpose of the ellipse half-horn was to collect, reflect and direct ultrasound from the larger opening to the smaller end and onto the focal point (transducer) with significant increase in gain.
I have found the half-horn an excellent accessory for close-up leak detection of vacuum and compressed air/gas, and for scanning "open" electrical switchgear panels. It has a narrow field of view for several inches, making it very useful for close-up inspections.
Whether you are trying to locate compressed air leaks to save energy, find vacuum leaks, or perform an electrical inspection of switchgear or a substation, these ultrasonic accessories will save you time and money. Good hunting.

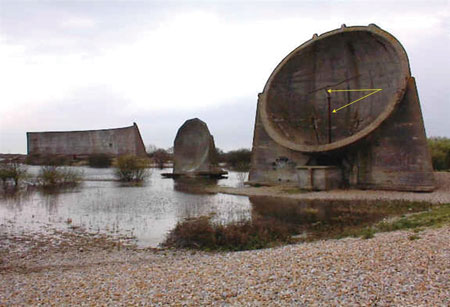
Figure 1: Sound Mirrors at Lade Pit, Dungeness near the town of Folkestone in Kent, England. Note a metal pole in the dish (Figure 5) that held the microphone. Background, a huge, 200-foot long rectangular sound mirror. Photo Credit: With permission from Keith Slade (http://www.castlekas.freeserve.co.uk/sound_mirrors.htm).
Figure 2: T3 sound locator, searchlight and transport vehicle (circa 1932) used by the U.S. Army Coast Artillery Corps. Photo: 98175 (public domain).
Figure 3: A two-horn acoustic amplifier system for locating approaching aircraft in use at Bolling Field, Washington, D.C. in 1921. Photo: Library of Congress/National Photo Company Collection.
Figure 4: NASA Vehicle Assembly Building (VAB) in Cape Canaveral, Fla.
Figure 5: Left to right (a) Parabolic Reflector for great distance, (b) Parabola Horn for long distance, (c) Ellipsoidal Horn for close-up (half-ellipse), (d) Conical Horn for medium distance. Photo: Courtesy of Jim Hall, Ultrasound Technologies Training Systems (USTTS).
Figure 6: The Ellipse is cut in half to make a half-horn. Photo: Courtesy of Jim Hall, Ultrasound Technologies Training Systems (USTTS).
Jim Hall is president of Ultrasound Technologies Training Systems (USTTS, www.Ultra-SoundTech.com), located in Woodstock, Ga. He has over 20 years of experience and is a "vendor-neutral" company providing onsite predictive maintenance consultation and training. USTTS provides Associate Level, Level I and Level II Airborne Ultrasound Certification. Jim is also the author of "Ultrasonic War Stories," a free biweekly newsletter, and a regular provider of online presentations at Reliabilityweb.com. He is a contributing editor for Uptime Magazine.