Would the foot spring up? This is a twisted base frame not a short or distorted foot. Remember, a motor is a hollow casing with a stator attached to it. The end bearings support the heavy armature suspended in it.
I believe that on large (heavy) motors with lightweight casings, the foot will not spring up when measuring a small amount of twist. If it doesn't spring up, it is natural to assume that nothing is wrong and no other action is taken. I also believe, although motors (machinery) are designed to be mounted on flat surfaces, many of them are clamped down on twisted or uneven bases. (Figure 1)

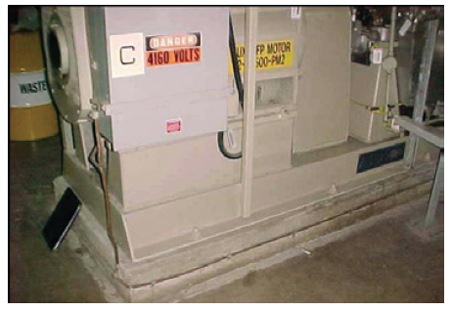
Figure 1
The question is, Where is the problem? Is it the foot or the base? We use the term soft foot to describe foot problems, but this is incorrect. The word is actually a description of the feeling you get when you are tightening a machine's foot. Although the foot appears to be down, you can still tighten it and pull it down some more. It feels soft or spongy. If you feel this, the foot is distorted and flexing as you tighten it. To find and correct this problem, we can quite easily measure it with a feeler gauge (Figure 2).

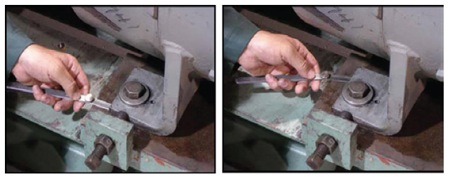
Figure 2
We have to make sure we measure under each corner of the foot so we can make the proper correction. We can do this as a rough measurement with the bolts loose and then tighten them and redo each foot tightening and loosening.
My point is you can't find distorted, twisted bases using a feeler gauge under the foot in the old traditional way. I think new large motors are more flexible than in the past. I think they will sag and conform to the base on which they are mounted. Obviously, if it is severe enough, there will be a gap under the foot. But are you measuring all of it? Even a small amount can make a difference.
If the motor casing is distorted because it is bolted to an uneven base, you now have an offset between the bearings. The offset tolerance for shaft alignment on an 1800 RPM motor is 0.002 inches to 0.004 inches, bearing in mind that you do have some flexibility from the coupling in this area. Now think about the offset tolerance between the two bearings in the motor. What should that be? Is the base creating internal misalignment of the bearings and motor shaft? A small amount of twist, say 0.010 inches, can give you a 0.005 inch of offset between the two bearings, which is too much.
This isn't angle or slope, as some say, where we are allowed so many thou per inch. This is offset. One company specification that I have seen says the base mounting pads shall be flat within 0.001 inches (yes, one thou of offset!).
The motor pictured in Figure 1 has a high vibration reading, indicating an electrical fault. The motor was sent out for repair and after reinstallation, including a soft foot check and shaft alignment, the same problem existed. A stress test was performed and the vibration level went down. A decision was made to remove the motor and measure the base. Before revealing the results, let's first explain how measurements were taken. (Figure 3)
Figure 3: Base Measurements Case Study: Using Easy-Laser's D525 Laser Shaft Alignment System and D22 Swivelling Laser
Although the base appears to be two long rails, the motor sits only on the shim packs positioned under the mounting pads on the motor. This means we only have to measure around each of the bolt holes. If we measure at each corner of every bolt hole, we would have about a 5′′ x 5′′ square area.
So first we set up a grid. Starting at the top left, the X axis goes down and the Y axis goes across. This makes the top left side X1-Y1 and each square box is where we place the laser detector. (Figure 4)
Figure 4
After the measurements were taken, the information was transferred to the EasyLink software program (Figure 5) and a line graph was produced. (Figure 6)
Figure 5
Figure 6
Figure 6 represents the wire diagram the software uses to display a picture of the measurement results. The center is colored, but you can still see the two rails down each side indicating that the #2 foot is high and the #4 foot is low. Figure 7 shows the full report in mils (1.0 mil = 0.001 inch.). The feet are numbered and the reference point where the highest and lowest measurements were taken is highlighted in red.
Figure 7
Based on these results, we were able to cut up shim stock and create a shim pack at each foot, thus making the base flat again so the motor now sits on a flat base.
This base issue is not as uncommon as many would think. I shared this information with a friend who is the vibration technician at a local plant. He recently e-mailed and wrote:
"We have recently (and still are) dealing with a very similar issue on a motor/base combination at our plant. In our case, it's a 250 hp (3600 rpm) motor driving a multi-stage boiler feed water pump. The motor was 'emergency' sourced from China when our in-service unit died in early February (severe stator damage). After spending a lot of time with coupling fit issues and alignment, we ended up having to run the motor with 3 feet/base bolts tight, one foot loose - we call it our 'tripod motor.'"
I have not seen this machine base as yet, but my guess is it was fabricated on site during the construction of the plant. I also think it's a large-sized base because a 250 horse power motor would be a good size. Again, my guess is the base was never stress relieved, so over 25 years of operation, it has become distorted and has a twist. The reason I think this is because the new light-weight motor is telling me so.
You might say the fix would be to add shim under the foot, but what if you try this and the vibration level is still high? Or, what if the motor is sitting high and you would actually like to lower it for a better alignment? You also might be adding shim under the wrong foot. The best way is to measure the base and make the correct call based on knowledge. This means you have to measure the base.
John Lambert served his apprenticeship in Mechanical Maintenance in Liverpool, England. After emigrating to Canada in 1973, he worked in the Aero Industry and Fiberglass manufacturing. In 1994, he started his own business, Benchmark Maintenance Services Inc., specializing in rotating machinery installation, training, service and equipment sales. He has conducted training on offshore oil rigs, paper mills, at chemical plants, cement plants and gold mines. www.benchmarkpdm.com
EasyLink™ is a registered trade mark