The machinery installation process is a fundamental (basic) maintenance process. The goal is to create a stress-free environment in which the machine units can run. With this achieved, you will obtain the optimum life from the machines.
The installation process includes various items, such as soft foot correction, coupling run out measurement, thermal growth compensation, pipe strain, keyway length, etc. It also includes, or should include, base measurement. The installation process is a lot more than just shaft to shaft alignment, yet this is where many organizations place their focus.
Machinery installation is critical to all maintenance departments. Before you can begin to maintain your machine, you must first install it correctly. Yet many plants focus on technologies that detect faults after the fact, such as vibration, oil analysis, temperature, ultrasonic inspection, etc.
Yes, you should expect your equipment to vibrate more, create more heat and run louder when it has not been installed correctly. I'm not against these technologies; in fact I like and use them a lot. My point is before we use them, the focus should be on the installation. And the installation has to be done right the first time - guaranteed.
Again, the goal is to create a stress-free environment for your machines to run in. This statement says it all for me. Stress is applied force and the cause can be shaft misalignment, pipe strain, distorted bases, distorted machines feet (soft foot), etc. Your job is to find machine stress and correct it. In theory, you should be confident enough in your equipment installation (when it's not running) to loosen all the hold down bolts on a machine unit and not see the machine move.
Now would you do that -or would you expect your machines to move?
Let's look at one of the major causes of machine stress: the base. We all know that a base has to be strong enough to support the weight of the machine. It also has to be able to withstand the large amount of torque the machine produces.
But what other requirements does a base need? For instance, does it have to be level? Does it have to be flat?

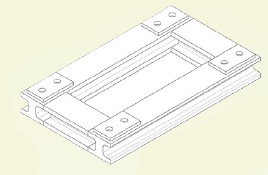
Figure 1: A machine’s base mounting pads should be flat (coplanar) within 0.001 inch.
A machines base has to be flat, as shown in Figure 1. Level is desirable - not necessary - but flatness is a must. If a base is distorted or twisted and you bolt a machine to it, you will distort the machine's casing and deflect the shaft. In a sense, you are creating internal misalignment by offsetting the bearings.
The problem is the machine's feet and the base are not in the same plane. In other words, the machine's feet sit unevenly on the base. When the feet are tightened down, the machine's casing becomes distorted, thus creating stress.
In many cases, this is more detrimental to the life of the machine than the shaft-to-shaft alignment. With shaft-to-shaft alignment, you have two shafts and a coupling that allow for some flexibility - not much, but a little. In a machine's casing, you have a bearing on each end and one solid shaft, which is not flexible at all.
It's not just large machines that have base issues; it's also small ones as well. In most plants, there are a lot more small motors than large ones.

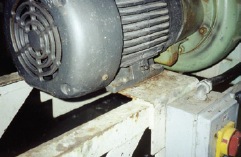
Figure 2: This motor is mounted on a piece of flat bar, which is flexing.
If you look at the base in Figure 2, you can see it's something that's been made in the welding shop or actually on the job site using an angle iron and flat bar. Who thinks that flat bar is actually flat?
Figure 3: A large base is leveled and bolted to the floor.
Now look at the larger base in Figure 3 as an example. It is a fabricated steel frame that has been leveled and bolted to the floor. It also has been grouted in and the grout has been allowed to cure. The frame has two solid steel rails welded to each side that the new motor will sit on. These rails are six inches wide and four inches deep and the tops were machined at the fabrication shop. Looks like a nice job!
However, that is a 0.012 inch feeler that is sliding under the foot.
Out of all the feet, there is only a gap under this one foot. So if you tighten all the hold down bolts, you would be pulling this one foot down by 0.012 inches. Doing this would, in turn, drop the center of the motor down 0.006 inches, which would happen regardless of the distance between the feet. This means you have created a 0.006 inch of offset between the two bearings in the motor. In other words, you have created internal misalignment.
In the case of an electric motor, distortion could alter the air gap and create a vibration that, in time, would cause the motor to fail prematurely. If the distortion is severe, it could even deflect the shaft causing a greater vibration.
Please do not make the mistake of thinking that this is soft foot. Soft foot is a term used to describe a machine's distorted (twisted) mounting foot. This is a twisted base. To correct the problem, we need to measure the base to make sure we know where the error is.
The question we need to ask is: Where did the error occur? Was it in the fabrication of the frame? The machining of the frame? The installation of the machine? All of the above? In this case, the installation is where the problem occurred. However, another point to take is that many base frames are fabricated and machined incorrectly. Many more are installed incorrectly and there is an even larger amount that have distorted over time because after the base frames are fabricated, they are never stress relieved.
When base frames are welded and machined during fabrication, residual stress builds up and should be relieved (usually by heat). If this is not done, the base may distort or creep over the years.
Unfortunately, because many companies do not have an understanding of this issue, or in most cases, a way of measuring a base for flatness, it is ignored. We also tend to look at bases that look good and make the assumption they are flat. I admit that I have done it as well.
In Part 2 of this article, I will show you a case study of a base measurement and explain how you can use a laser shaft alignment system to measure twist in the base.
In the meantime, I leave you with this little tip: You can use vibration instruments to find this type of problem. No, I'm not talking about vibration analysis; I mean vibration monitoring. All you need is a simple vibration meter, then locate the highest reading (obviously with the machine running) in the vertical or horizontal plane, and watch the reading as you loosen and tighten each of the foot mounting bolts. You may be surprised at what you see. Sometimes, the vibration reading will go down. This is because you have taken the strain off the motor. In other words, the motor is distorted and you are easing the strain. Some call this a foot resonance check. I call it a stress test. Call it what you will, but I recommend you do it; it may save you some work later.