There is a lot of speculation as to the causes of this situation. The current environment is even more impactful since it comes on the heels of record highs for oil prices driven by increased oil consumption in growing nations, such as China, coupled with unrest and conflict in key oil supplying nations, such as Iraq. This caused conventional producers worldwide to struggle to keep up with demand. As a result, prices spiked and $100/bbl oil was the norm since 2010.
This increased demand, coupled with record, seemingly sustainable prices, made traditionally cost prohibitive methods of extraction viable. Shale or tight oil extraction in North Dakota and steam-assisted gravity drainage (SAGD) in the heavy oil sands of northern Alberta are now attractive to producers and investors eager to exploit the high market value of oil. In the U.S. alone, production has risen by four million barrels a day since 2008.
Capital project budgets reached record limits and finding human capital (i.e., skilled and experienced people to operate, maintain and manage these facilities) became increasingly difficult. Competition for employees drove salaries ever higher, supported by the need to produce and the high margins available.
All this was stable until demand started to taper off and supply was able to outpace it. This resulted in unsold oil being stockpiled until later and a worldwide surplus or glut of oil supply.
The Organization of the Petroleum Exporting Countries (OPEC) has typically been the balance in this equation. As the process of oil production is threatened, the curtailment of supply through OPEC nations ensured the supply side of the equation was in check and the price remained stable. However, this time, OPEC has refused to cut supply, citing a loss of market share to higher cost producers, such as shale and SAGD.
Now, producers have seen their margins reduced to razor-thin levels. Costs that were justifiable in a higher return environment are now threatening the viability of the business. Furthermore, cash reserves are quickly being consumed as organizations try to reduce their workforces to adapt to this economic reality.
One thing that hasn't changed is the need for organizations to fulfill their regulatory and social requirements to operate. They must ensure they remain vigilant in controlling risks that could endanger the health and welfare of their employees and the community, as well as ensure they do not create an event that could have an irreparable impact on the environment.
PHYSICAL ASSET MANAGEMENT
The importance of managing physical assets has grown as a strategic lever in asset-intensive companies over the past several decades. It is driven by a range of factors, including the need to ensure sound safety and environmental stewardship, obtain solid financial returns, apply advanced technologies and demonstrate value to the shareholders and the communities in which they do business. In early 2014, this culminated in the publication of the ISO55000 standard for physical asset management.
Asset management is defined in ISO55000 as "the coordinated activity of an organization to realize value from assets." Instead of a cost to be managed, asset management has become a strategic element for helping organizations weather uncertain economic times and ensure they are at the head of the pack in terms of competitiveness. But beyond all this, asset management ensures that owners and operators have the systems, policies, practices and people in place to ensure safe, reliable and environmentally responsible operations.
THE NEW IMPORTANCE OF ASSET RELIABILITY
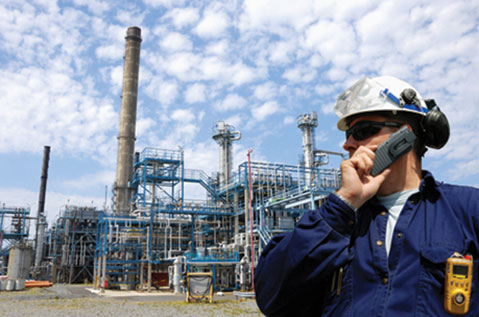
One aspect of asset management that is particularly powerful in a low margin oil environment is the implementation of business-focused equipment reliability programs. Reliability took root in low margin industries, such as paper production, where global competition, coupled with dramatically lower demands, meant only the lowest cost, most efficient producers would survive. Reducing the unit cost of production was essential, and reliability was one way to remain both competitive and viable. Oil production is not facing an alternative to its product, as was seen in the paper industry. However, the need to remain reliable will have a direct impact on profitability.
Unplanned equipment downtime erodes profit. It is a common mistake to think that unplanned downtime is less important when product margins are low. People think, "We are only making $18/bbl, therefore, the equipment does not need to be as reliable because the consequences aren't as severe." In fact, the opposite is true. The need to provide raw material, labor and energy to processes to produce products does not change. The best strategy for becoming a low cost producer of any product is to produce greater volumes at the same cost. Reliability accomplishes this. Unplanned, unreliable operations cause unrecoverable loss of salable goods and increased costs of labor, energy and materials, and will quickly result in an unsustainable business model.
The elimination or control of unplanned events is the greatest financial return that asset management can yield for your organization. By understanding the causes of unplanned events and focusing efforts on eliminating or avoiding preventable losses, organizations can quickly increase production values while lowering overall cost per barrel.
Historically, high margin producers were often lucky. In the new environment, low margin producers must be smart.
REDUCING COSTS
Reducing overall costs must be done, however, broad-brush cost-cutting measures will not ensure viability given that the timing of a return to higher margins is not guaranteed and the damage done by taking such an approach will be felt for years to come. Instead, the need is to ensure that the integrity of the operation remains intact and there is no increase in the risk associated with less maintenance. Robust reliability centered maintenance techniques, as outlined in SAE JA1011, are suitable to help understand the appropriate maintenance strategy for complex or tightly coupled operations. However, if the goal is to reduce cost while maintaining current performance and you need to do this quickly, a maintenance program optimization (MPO) review may be the answer.
Over time, maintenance programs tend to grow. Often the genesis of the program is an original equipment manufacturer's recommended maintenance program that has had a cursory review by the EPC (Engineering, Procurement, Construction). From here, the addition of new technology, techniques and responses to poor asset performance cause the maintenance program to grow. Experience shows that about 30 percent of the existing maintenance program is of low or no value. This is often for a number of reasons:
- The cost of the maintenance task often exceeds the cost of the failure it is trying to prevent. It is simply not worth doing.
- There are duplicate tasks, for example, changing oil based on a time schedule or cycles, as well as performing a lube analysis program.
- The tasks are inappropriate for the equipment. Often, legacy tasks remain in the system after component upgrades or capital improvements to the system, resulting in work that cannot be completed. This becomes an annoyance to the maintenance staff, who simply close the work as completed. This work is especially costly, as it still goes through the planning and scheduling processes and, in some cases, requires the purchasing of spare parts that will not be used. It is not technically feasible to do the work.
- The work does not reduce the risk of equipment failure. The work is not effective.
- Work that is poorly planned or too vague. For example, maintenance on an elevated motor that requires scaffolding or work that is simply labeled "inspect and repair as required."
- Work that is currently performed based on a schedule can be migrated to a condition, allowing your organization to increase the life of its equipment, yet still plan the repair in enough time to avoid the consequences of the failure.
- The identification of the risk associated with not performing preventive maintenance work. In most organizations, there is not enough personnel to do all the work. By understanding the risk associated with the work task, the organization can defer or cancel low risk tasks and focus on those that are the most effective.
- Reduction of reactive work. When the work is categorized based on risk avoidance and effectiveness, the amount of reactive work will decline. Reactive work is usually two to four times more costly to perform than proactive work.
UNDERSTAND RISK
When operating budgets shrink and resources that were limited before become even scarcer, understanding where to spend limited dollars is critical. Unfortunately, in many organizations, this decision is more emotional rather than quantitative.
Risk management provides a framework to ensure that:
- All levels of the organization understand the tolerance for risk and make decisions based on that known value.
- The identification of risk is consistent and based on the goals of the company (e.g., safety, the environment, production, etc.).
- Decisions to spend or defer money have a rational basis and consider the organization's exposure to risk.
- The development of mitigation, elimination and acceptance strategies are based on their impact on the organization.
- The organization allows capital spending decisions to be better planned.
- Senior management understands the current risks facing their business and provide the information needed to make critical business decisions.
No one knows how long low oil will last or how bad it will get before it stabilizes. However, producers need to react now. Cutting fat is the first logical step, but it must be done with care and precision. Asset management will help weather this storm while maintaining a profitable, competitive business that is ready to capitalize when the markets begin to turn.