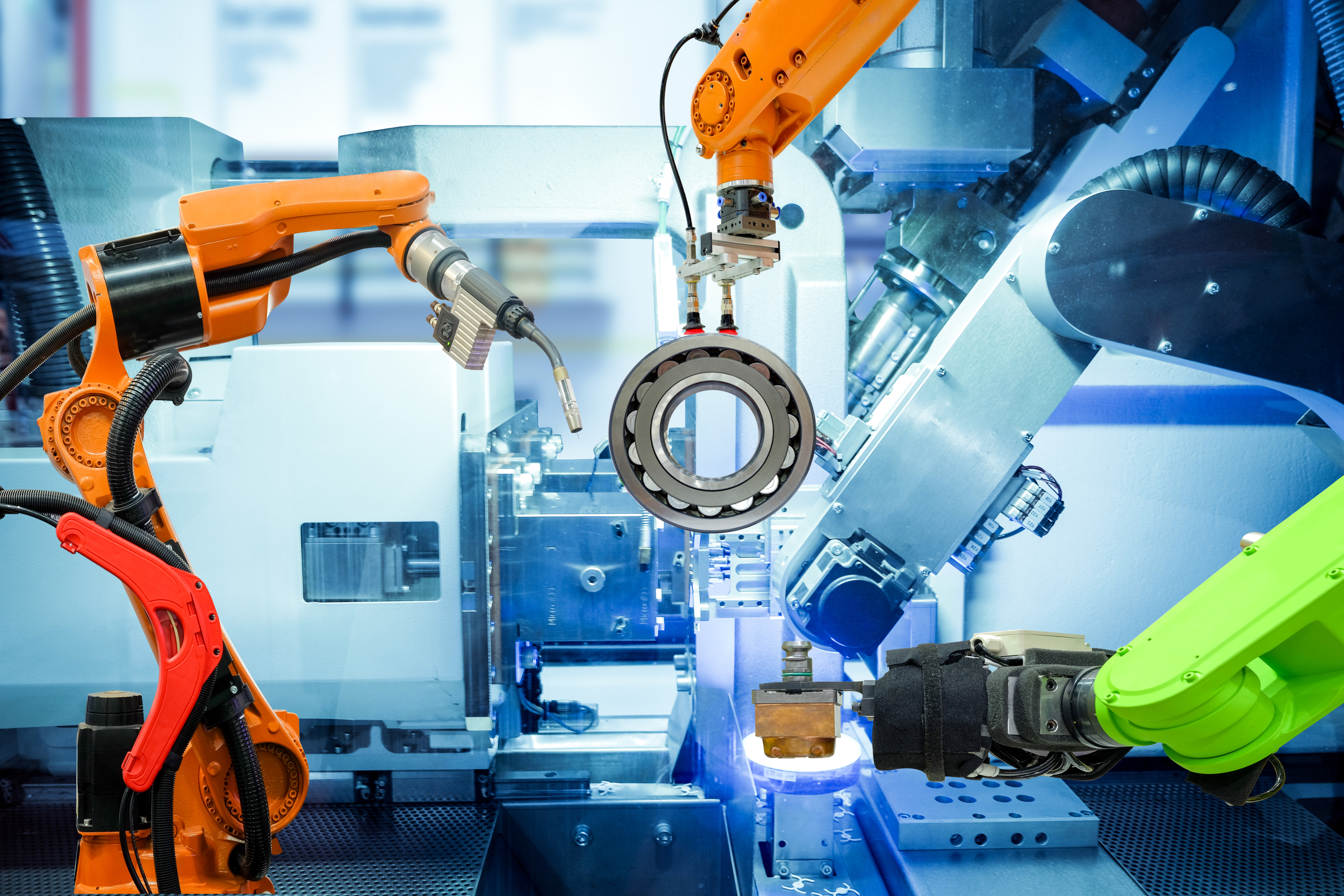
You are 17 times more likely to introduce defects during equipment start-up than during normal equipment operation. Additionally, over 90 percent of rotating equipment has defects at start-up that result in premature equipment failures. What’s causing these start-up defects?
Misalignment and unbalance are two of the most commonly overlooked conditions that lead to these unwanted statistical results, according to a study by a leading industrial equipment supplier. Misalignment in equipment leads to increased vibration levels, bearing failures, coupling wear, seal failures, shaft fatigue, increased power consumption and other negative effects. Unbalance in equipment can introduce structural-related issues, bearing defects and other problems. Both conditions can create unwelcome safety concerns. Additionally, both conditions can be present on the same equipment and, working in concert, can unfortunately amplify the referenced failure conditions.
So, how do you prevent misalignment and unbalance conditions from making your equipment part of these negative statistics and placing your company at financial risk?
The answer is to apply condition monitoring technology and procedures, such as laser alignment, equipment balancing and vibration analysis, to your equipment.
These condition monitoring activities will lead to reduced equipment downtime, reduced equipment failures, improved safety, reduced financial risks, increased equipment uptime, lower operating costs and increased profits for stakeholders.
What reliability improvements can you make in your facility that do not require expensive or complicated actions? Start with the basics, such as:
- Align: shaft, coupling, etc.;
- Balance: rotating components, such as fan blades, impellers, rotors;
- Tighten: eliminate looseness and excessive vibration;
- Lubricate: correctly, meaning not too much or too little;
- Inspect;
- Apply condition monitoring;
- Understand where your efforts should be focused.
Don’t wait until the equipment has been installed and is operating. These basic functions must be included in the specification, design, purchase and routine operation of your equipment. Failure to address these vital aspects from the beginning through operation of your equipment will result in higher maintenance costs and reduced equipment reliability.

Figure 1: Protective coatings can help increase the efficiency and extend the service life of a gas turbine
Sustaining Bearing Life
Like any mechanical device, bearings wear out over time. This is an unavoidable fact of life. Yet, there are ways of getting the maximum life out of the bearings in your rotating equipment.
To start with, there are five simple things you can do to maximize bearing life. These five steps are: keep your bearings clean, dry and cool, and keep your equipment balanced and aligned.
- Clean, dry and cool means addressing the lubrication issues of the equipment. For instance, circulating oil systems are used when the heat buildup at the bearing is more than a static oil system can radiate away. In this case, the system provides external cooling. However, just like in a car, circulating oil must be changed periodically. Oil deteriorates over time from heat, oxidation, catalytic reactions, and dirt or water contamination. It is a good idea to change the oil whenever it becomes dirty or cloudy.
- Grit and dirt contamination act as abrasives and over time will remove the hard facing of the bearing. Once the hard facing is removed, the bearing will quickly deteriorate to failure. Therefore, it is important to keep the dirt contamination out.
- In wet environments, keeping bearings dry can sometimes be difficult. It is also important since water will separate the lubricant. If you notice a milky look to the grease being purged from the bearings, it is an indication of contamination by water.
- Balanced and aligned refers to minimizing the destructive energies present when imbalance and misalignment are allowed to continue. Keeping these forces to a minimum greatly adds to extending bearing life. Many companies use vibration monitoring equipment to determine the severity of these forces or shut down the equipment if these energies get too large. As an example of vibration levels seen in the field, it is not uncommon to see vibration velocities of 0.10 in./sec or lower for initial operation, 0.30 in./sec for an alarm setting and 0.45 in./sec as the shutdown setting for a heavy duty fan. However, as there are many applications, it is always best to check with your fan supplier on these matters.
Achieving Long-Term Reliability
Long-term reliability is a common goal for all plant operators. Achieving it requires a considered approach that takes into account a range of contributory factors and makes use of the most appropriate technology and manpower available to them.
Rotating equipment that is in direct contact with the process media and under constant attack presents a major challenge. It is possible, however, to reduce degradation to a minimum by selecting the correct coating system.
Generally, turbines, compressors and pumps are all subject to a variety of environmental conditions that contribute to corrosion, erosion, fouling and various temperature-related issues.
The first step is to understand the operating environment of the machinery. From there, the sources of degradation can be classified and specific coating systems can be used to increase efficiencies, lengthen the interval between scheduled maintenance and reduce the occurrence of unscheduled maintenance events.
In the case of a gas turbine, the flow path of air and fuel presents a number of different conditions that can have an adverse effect on the performance of the turbine. The combination of heat, microscopic abrasives and a gradually increasing concentration of corrosive elements can cause significant damage to a once smooth airfoil surface. As the surface finish slowly degrades, the efficiency of both the compressor and turbine is reduced.
Compressor Section
This process can be arrested in the compressor section of the gas turbine and the surface finish restored by the application of suitable metallic coatings. There is a range of options open to suit the specific duty of a gas turbine, but all include a type of metal deposition where a tough corrosion-resistant surface is created.
An aluminium base layer is typically used in gas turbine compressors for corrosion protection of ferritic/martensitic steel components in moist conditions. It provides galvanic protection, which means that small scratches to the surface layer are less likely to cause corrosion. It is produced by spraying a slurry of aluminum and an inorganic binder, rendered insoluble by a medium-temperature baking process. This layer can be then covered by a harder layer that might include metals, such as chromium.
The harder layer is usually applied using a spray coating method, such as chemical vapor deposition (CVD), atmospheric plasma spraying (APS), low pressure plasma spraying (LPPS), or high velocity oxygen fuel (HVOF). Which one is applied will depend on the coating thickness required and the sensitivity of the part to heat, as some processes are hotter than others.
By applying corrosion inhibiting and surface finish enhancing coatings to the compressor section, it is possible to increase the efficiency and extend the service life of the gas turbine.
Hot Section
Modern gas turbine hot section components are made using nickel or cobalt based super alloys, which are designed to operate in high temperatures.
However, these alloy compositions are not as well suited to providing corrosion and oxidation protection and need to be supplemented with custom coatings that can deliver the hot corrosion and oxidation protection required for extended service lives.
The process of oxidation causes a layer of metal-oxide to form on the surface, which, in general, protects the underlying material. Therefore, the oxidation process slows down as the thickness of the oxide layer increases. This process can be replicated with the intentional formation of oxides that provide a protective layer, preventing further atmospheric attack.
Corrosion of a gas turbine component usually occurs in one of two ways. Hot corrosion may take place between 788°C and 899°C and it attacks the entire surface of the component. Alternatively, corrosion at cooler temperatures is more localized and, therefore, tends to create distinct layers of oxide and exposed metal. Further damage can be caused by erosion, which involves repetitive mechanical abrasion by particles in the air stream.
Stand-alone high velocity oxygen fuel applied MCrAlY coatings are sufficient to combat corrosion/oxidation at lower firing temperature gas turbines. For newer technology, higher firing temperature gas turbines, the combination of a MCrAlY bond coat coupled with a ceramic thermal barrier coating, reduce the surface temperature of the substrate, thus reducing the degenerative effects of oxidation and corrosion.
Compressors
Pumps and compressors account for more than 20 percent of the world’s electricity demand and the energy costs to run them represent 95 percent of the running costs. Therefore, it is essential to minimize these costs by improving performance and efficiency. These efforts also will have the beneficial effect of improving reliability and service life.
While turbines extract energy from a gas expansion process, turbofans and compressors are used to increase the energy of gases. As such, the main issues with these components are corrosion, erosion and fouling.
Conclusion
Proper equipment function and sustainability requires a properly aligned and balanced machine. Allowing a machine to operate with an unbalance situation can result in coupling damage, bearing damage, cracks, loose components and many other costly maintenance issues.
Bearings should be clean, dry and cool. Loose debris can dislodge and impact the balance quality of a machine/equipment. Debris buildup on the impellers/blades and other rotating parts can create unbalance conditions.
Before balancing the machine, it is very important that the rotating surfaces (e.g., blades, etc.) are cleaned of any debris. Removing buildup will help ensure that the machine can be properly balanced and remains in a balanced condition.
Special Thanks to Travis Cockrell, Component Superintendent of the Coating Department at Sulzer, Houston Service Center, Texas, for contributing information to this article.