Since its inception in the 1960s, reliability-centered maintenance (RCM) has radically changed the maintenance paradigm. Despite its success, approximately 85 percent of RCM projects do not achieve the full benefits of the analysis, according to a Reliabilityweb.com survey. RCM implementation must be strategic for it to succeed and be sustainable. The Uptime ® Elements framework is ideal for building the support, reasoning and process for an RCM effort.
Figure 1 summarizes how an RCM program is carried out using the Uptime ® Elements framework. At the start, significant steps to plan for success must be taken and then immediately followed up with RCM sponsorship steps to ensure stakeholder support. Proper RCM systems analysis training must also take place to ensure informed implementation of the RCM process.
“RCM implementation must be strategic for it to succeed and be sustainable.”
After completion of an analysis, RCM results implementation must proceed to the step that may defer and cause project failure: implementing results in the computerized maintenance management system. Finally, an RCM living program is put in place to periodically update RCM decisions as the plant and technology change.
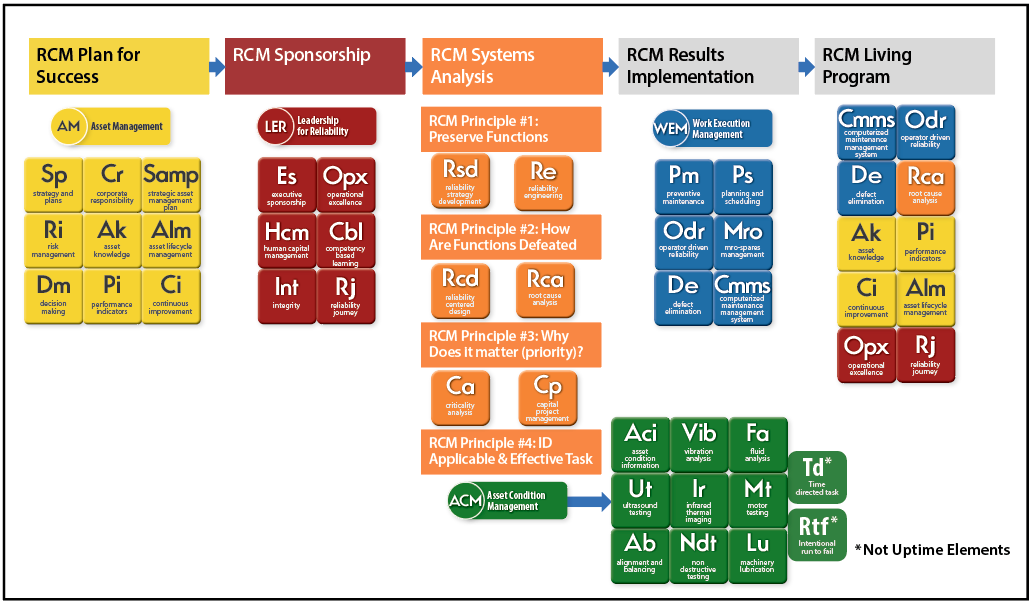
RCM Plan for Success
Benjamin Franklin famously said, “If you fail to plan, you are planning to fail.” While planning does not guarantee success, it does serve as a road map for understanding the overall objective and direction of a project. There must be a clear understanding of the strategic plan (Sp), achieved by creating an asset management (AM) policy that defines risk management within an operating context. The AM category of the Uptime ® Elements includes developing a strategic asset management plan (Samp) and translating the requirements of stakeholders to a lower-level document that defines the strategy for bringing together asset knowledge (Ak), risk management (Ri) and other aspects in the AM category. The Samp document should define how RCM fits into the overall reliability strategy.
“If you fail to plan, you are planning to fail” - Ben Franklin
A well communicated and understood Samp is likely to have the support of stakeholders, upper management (and thereby funding), and staff needed to carry out the plan. Historically, Uptime ® Award winners have a well-defined AM strategy. The four key themes for a strategic asset management plan, as shown in Figure 2, are: Alignment of risk-based decision-making, long-term strategy, transparency of decision-making, and aligned objectives.1
RCM Sponsorship
Executive sponsorship is critical to sustaining any RCM program. The leadership for reliability (LER) elements include executive sponsorship (Es), which ensures the RCM project is funded and has a leader to oversee the team. The leader ensures risk management is not decided simply off a predetermined template, but rather based on the plant’s operating context.
“Executive sponsorship is critical to sustaining any RCM program.”
The LER category supports the team’s shift toward operational excellence (Opx) by putting the best team together for the project with human capital management (Hcm) and providing training with competency-based learning (Cbl).
RCM Systems Analysis
At this point, the team is prepared to execute RCM systems analysis. RCM follows many of the elements found in the reliability engineering for maintenance (REM) category. Ideally, RCM is best performed during the design phase using reliability-centered design (Rcd) and criticality analysis (Ca). Unfortunately, most of the time, the maintenance community is handed a design not of their own choosing and instead must do their best to maintain it in the best operating condition.
To select the most applicable and effective tasks, the team must understand the asset condition management (ACM) group of the Uptime ® Elements. Knowing when to use vibration analysis (Vib), ultrasound testing (Ut), or other ACM techniques is critical to making sound preventive maintenance (PM) decisions. The team should consult with an ACM expert to review their ACM decisions.
Although it is encouraged to use ACM when selecting tasks, sometimes the most appropriate tasks are time directed or run to failure. For this reason, liberties were taken to add two “unsanctioned” tiles to the Uptime ® Elements, specifically the Time directed task (Td) and Intentional run to fail (Rtf).
RCM Results Implementation
Once PM tasks are selected, a plan is put together to modify the existing PMs to RCM derived tasks. This involves the work execution management (WEM) category of the Uptime ® Elements. PM tasks are organized and packaged into work orders for efficient execution. Planning and scheduling (Ps) is required to effectively execute the new PMs.
Spare parts management (Mro) is necessary for timely performance of PM tasks. RCM participants decide which spare parts are needed by considering the PM mitigation strategy. For example, expensive assets do not need to be stored for years if the health of the asset is assessed with ACM tools. Rather, a just-in-time (JIT) strategy is used to purchase the assets when ACM methods warn that a failure is looming. RCM software should include spare parts analysis using PM strategy selection criteria, thus avoiding needless expenses.
Defect elimination (De) is critical to the RCM strategy. Tasks that introduce defects, such as intrusive maintenance or using contaminated lubricants, are not beneficial. RCM encourages the use of less intrusive ACM tasks.
Capturing the RCM PM tasks in the computerized maintenance management system (Cmms) must be completed. This ensures timely execution of the RCM tasks. Cmms tracking will provide metrics to show the effectiveness of the new tasks.
RCM Living Program
Once the RCM results are implemented, an RCM living program is initiated. It is used to determine how well the results are performing. Are reactive actions being reduced? Were the appropriate PM frequencies chosen? Are performance indicators trending in the desired direction? These results are determined by tracking work using the Cmms. The living program is considered a continuous improvement (Ci) effort over the entire asset lifecycle (Alm). Looking for root causes of failure (Rca) and eliminating them is part of the reliability journey (Rj) toward operational excellence (Opx).
References
1.Reliabilityweb.com. “AM Asset Management Passport.” Certified Reliability Leader Uptime® Elements Passport Series. Fort Myers: Reliabilityweb.com, 2017.
2.Smith, Anthony M. and Hinchcliffe, Glenn R. RCM Gateway to World Class Maintenance. Oxford: Butterworth-Heinemann, 2003.