Over time electrical infrastructure changes, facilities expand, load requirements increase and equipment becomes degraded with age or lack of maintenance. It’s not uncommon to find functioning electrical distribution equipment that hasn’t been maintained and tested, is obsolete, or is well beyond its designed service life. Electrical systems that were appropriate for the loads and incoming power when they were installed may now expose employees to life-threatening hazards. Often, there is no indication of a potential problem until a fault occurs and the overcurrent protective device fails to operate, resulting in injury or damage to equipment and property.
Safety, maintenance and reliability professionals can proactively change this scenario and enhance layers of protection (LOP) and sustainability of their electrical systems by deploying an integrated condition monitoring (CM) strategy with predictive maintenance (PdM) technologies.
Just a Few Numbers
Reviews of insurance/risk statistics and everyday media headlines remind us of the extreme failures and unfortunate circumstances caused by the mismanagement of electrical distribution systems. For example, insurance statistics between 1992 and 2001 identified that electricity was the leading cause of fires and explosions causing nearly 1,400 insurance losses costing over $788MM1 (~1 billion in 2009 dollars).
From a people perspective, Canada’s Ministry of Labor reviewed a decade of electrical incident records to find that 50 percent of the 1,200 electrocution deaths and critical and minor arc flash injuries came from performing basic maintenance and repair on or around energized equipment. An interesting statistic is that 79 percent of the fatalities involved occupations outside of the traditional role of electricians. These included maintenance workers, millwrights, apprentices, laborers, heat, ventilation and air conditioning (HVAC) technicians, equipment operators, supervisors and drivers.” 2
These events are a mix of management and human errors and equipment failures which weaken existing “barriers” or layers of protection for personnel safety. Successful organizations recognize that ensuring sustainable asset and safety cultures starts with understanding these gaps, the types of exposures, the electrical system failure modes, and associated hazard potentials that may increase the risk of an incident.
Failure Modes and Hazard Indicators
Any device involving electrical current can overheat and spark a fire. Before changing or deploying new LOP, facility leaders must understand how and why electrical assets may fail. The good news is that most systems have known failure modes and are accompanied by early warning hazard indicators.
1. Electrical Leakage –
a. Electrical Arcing occurs in all voltages. Extreme arcing
produces a stream of vaporized metal between conductors
and through air or bulk insulation systems, destroying
electrical equipment. Arcing can cause overloads,
defective contacts, uninterrupted faults and overheating.
b. Tracking is often referred to as “baby arcing” and follows
the path of damaged or dirty insulation across component
surfaces. Tracking occurs most often in medium voltage
(MV) to high voltage (HV) equipment of 1,000 volts (1kV)
or greater.
c. Corona is the partial discharge, electrical stress or leakage
of 1kV or more at sharp points along an electrical path. It
is commonly explained as being intermittent, unsustained
arcs which are shot off of the conducting material like a
stream of electrons. It occurs inside electrical components
such as transformers, switchgear, and insulated busbars.
The leakage ionizes the surrounding air, producing faint sparks, cracking, hissing, humming, frying noises, radio/TV interference, conductor vibration and ozone. In the case of visible corona, the conductor will glow with a blue or green light.
Corona also forms ozone (O3), which will conduct current and can follow a direct path to ground, resulting in catastrophic results, especially in enclosed switchgear. Corona also produces nitrogen oxides, and in an aqueous form, nitric acid. This further destroys the insulating material and metal components causing possible thermal problems.
2. Overheating: The Real Equipment Killer – Every 18°F (10°C) rise above equipment’s nameplate operating temperature will reduce the its operating and insulation life by 50 percent! Typically, this overheating is caused by high resistance within conductors or at overtightened or loose connections, uninterrupted fault currents, and environmental factors (see item #5). 70 percent of thermal anomalies are due to loose connections.
3. Uninterrupted Fault Current – This causes enormous amperage spikes which rapidly heat components to very high temperatures destroying insulation, melting metal, starting fires and even causing explosions if arcing occurs. These are caused when a circuit breaker, relay or fuse unsuccessfully interrupts current.
4. Voltage Irregularities – These are caused by an unstable utility supply, line surges, lightning strikes, transient voltage, unbalanced loads and harmonics.
5. Environment Factors – These include contaminating conditions like excessive dust, dirt and debris, high or low ambient temperatures, humidity, corrosive atmospheres, water, vibration, high-resistance connections and contacts.
6. Operational and Maintenance Factors – These include overloading, equipment malfunction, inadequate sizing, jumpered or modified systems and lack of maintenance. Based upon a review of fires caused by failed electrical components, 70–90 percent were due to lack of maintenance (Figure 1).3
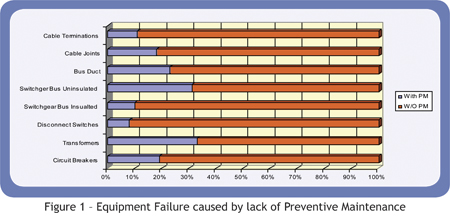
Condition Monitoring with the Integrated PdM Tool Box
Condition monitoring (CM) with predictive maintenance (PdM) technologies is an important maintenance strategy for management of components in the distribution system. CM is an early warning system only triggering maintenance activities based upon condition. This allows maintenance and reliability managers to identify maintenance priorities, plan work assignments and schedules, arrange for outside services, order necessary parts and materials and make repairs on a controlled outage basis.
Thus, it typically extends the interval between successive maintenance and therefore, incurs less cost. Self-induced failures (“infant mortalities”) caused by improper installations are also minimized. From a safety perspective, this equals fewer times personnel are working on or near energized equipment.
Summary of CM/PdM Toolbox Benefits for Program Leaders
• Increased Safety
• Greater System Reliability
• Increased Revenue
• Reduced Outage Costs
• More Efficient Inspections
• Improved and Less Expensive Maintenance
• Reduced Spare Parts Inventory
• Reduced Operational Costs
At this point, we know the typical contributing factors/failure modes and the equipment categories affected most. The next step is to determine which PdM technologies are the best at capturing equipment failure modes/indicators. Although there are numerous CM/PdM approaches, the following are discussed in detail: Common Senses, Infrared Thermography, Ultrasound, Oil Analysis and Motor Circuit Analysis.
Making “Dollars and Senses” of the Situation – One of the most important set of tools in a facility’s PdM tool box is each person’s common senses. From a reliability perspective, these include seeing, hearing, smelling, touching, taste and common sense. Merge the senses with a little awareness training and they can identify general early warning indicators in up to 70 percent of all safety and reliability problems.
When it comes to identifying potential OSHA and NEC violations and associated fines, these low-cost senses are unmatched by most hardware and software systems. Most of the fines carry a “minimum possible” fine of $2,000 each. This equates to an average exposure of $10,000 for every 100 pieces of electrical equipment inspected4. The findings are very apparent and are a great indicator of a site’s safety and reliability culture.
The drawbacks are that senses are subjective and identify late-stage failures increasing the hazard exposures and minimizing trending and early warning information.
The following lists basic physical conditions easily identified with “senses”:
• Discoloration of connections, terminations and live parts
on the air switches.
• Poor wiring practices (Figure 2) and conditions (Figure 3) such
as burnt and cracked wires, mismatched components, missing
covers, and “rats nest” of loose wires.
• Broken skirts on insulators and cracked insulation.
• Excessive vibration denoted by noise, which can cause loose
connections on live parts, laminations and improperly
supported buses inside transformer housings.
• Gray power on outside of cable indicating corona or arcing.
• Sounds of arcing are indications of corona, which leads to
ozone. Ozone puts a sharp taste in the back of your
throat. OSHA has limits on ozone - somewhere around
20 parts per billion (ppb) which is far below the level
at which it can be smelled.
• Poor Housekeeping – Excessive dirt, grease, dust, and fibers
on components. The surrounding area should be evaluated
for accumulation of trash or combustible storage, clearance
violations, component integrity, poorly sealed panels
allowing dust ingress, etc.
• Poor Operating Environment - Hot room temperatures,
corrosive and moist atmospheres.
• Lack of Documentation – Missing or outdated system/
component specification sheets, OEM manuals, service logs
and drawings.
Infrared Thermography (IR) – Normal operating electrical equipment radiates energy as heat, specific to that piece of equipment. This temperature range varies based upon the component size, rating, ambient temperature, and amperage loading. Infrared thermography is fast, accurate and picks up these temperatures and risk factors without interrupting service. IR is a recommended best practice by NFPA5. It helps facilities comply with insurance company recommendations, eliminates overheated connections from wasting energy6 and reduces carbon footprint exposures for every kilowatt not consumed.
Ultrasound – Ultrasound is extremely valuable for inspections of medium and high-voltage electrical systems. Ultrasounds occur in wavelengths above 20,000 Hz frequency, which are higher than human hearing. Loose connections and the deterioration of high voltage insulation, cables, broken sheds or contaminated porcelain produce an electrical leakage known as corona and tracking. This leakage creates turbulence, friction or “white noise” in the air which is picked up by the ultrasound receiver.
Ultrasound is also a great resource when operational or safety factors prevent the use of infrared on enclosed, energized electrical equipment. The receivers have rubber cone-shaped adapters to scan through door gaps and air vents helping to detect the presence of arc flash hazard potentials.
Transformer / Switch Oil Analysis – Oil is used to cool and insulate the internal components of transformers and certain types of switches. Because it bathes every internal component, the oil contains a great deal of diagnostic information. Just as a blood test provides a doctor with a wealth of information about the health of a patient, a sample of transformer oil can tell a great deal about the condition of a transformer.
The oil analysis is broken into two parts:
1) Physical, electrical and chemical tests that evaluate oil for
indicators of dielectric (insulation) breakdown, power factor,
interfacial tension, acidity and color.
2) Dissolved gas analysis (DGA) looks for certain gas quantities
and combinations that can determine the likely failure mode
(see Figure 4).
Motor Circuit Analysis – Motor circuit and motor current analysis (universally termed MCA) evaluates the integrity of the cabling and insulation starting at the motor control center (MCC) components on down to the motor’s rotor and stator windings and grounding. Defects and faults include developing shorts, resistive unbalances, insulation to ground faults, cable defects and rotor defects. MCA can be applied to any size or voltage motor, capturing over 50 percent of all potential electrical and mechanical motor faults.
Figure 5 shows a matrix of the PdM technologies and which electrical equipment each technology can evaluate effectively.
Facility Survey Highlights
For purposes of this article, a typical facility distribution system includes medium voltages (MV) at a property’s substation or pole/pad mounted transformer on down to 120 volt branch circuits. This voltage range covers hundreds of system types but for simplicity, the equipment and PdM concepts are segmented into the following key equipment categories: main medium-voltage incoming service, transformers, conductors, circuit breakers/fuses/disconnects and motors.
Main Medium-Voltage Incoming Service
A facility’s main service is comprised of equipment that transfers high- or medium voltages down to lower voltages used within the facility. This equipment includes bushings, insulators, steel support structures, high-voltage lines, step-down transformers, and switchgear (interrupting, control, metering, protective and regulating devices/assemblies). This equipment is designed to be outdoors either directly or in weatherproof housings.
Typical issues include dirt, dust, debris, and salt residue (coastal regions or equipment near salted roads) coating connections and lines increasing the chances of corona, tracking, and arcing (Figure 6). Partial discharge accounts for the largest percentage of disruptive failures of medium-voltage switchgear. Look for broken bushings, insulators, arrestors, vandalism and weather damage.
Failure Example: Lights Out During Peak “Sold Out” Production – In the example shown in Figure 7, mist from cooling towers caused the pole insulators to become dirty, in turn, causing arcing and tracking across the insulators. The pole caught fire which weakened the transmission line supports. The top “T” section tipped 90 degrees causing phase-to-phase shorting. The plant was in a “sold-out” condition. It was completely down for eight hours and didn’t get full production for over 24 hours. The new procedure requires quarterly IR and ultrasound and semiannual PMs with qualified contractors cleaning the “live” insulators.
Transformers
Facilities use dry-type or oil-filled transformers to step-up or step-down voltages to meet the specific needs of a site. Transformers have an estimated 20-30-40 year life expectancy under normal operating conditions. Transformers run hot and require proper air and/or fluid circulation to ensure they don’t overheat.
Step-down transformers are comprised of insulated primary windings (higher voltage) and secondary windings (lower voltage), iron core laminations, tap changers, bushings, and connections, but typically, no mechanical moving parts. The physical design of transformers presents the potential for primary-to-secondary shorts from insulation failure. As they age, their ability to withstand heat, and stresses such as being exposed to mechanical vibration, switch surges, line surges and limited short circuits also reduce life expectancy.
Oil-filled Transformers - Oil-filled transformers have radiators, cooling fins filled with mineral oils or insulating fluids. The windings are wrapped with pressboard paper and have spacers to provide physical dielectric clearance distances to withstand movement. The insulating fluids are cooled by fans and/or ambient air which ensure oil’s dielectric strength and preserve transformer paper and windings. Larger or utility transformers may also have pumps to circulate fluids. The preservation of windings, load tap changers, and accessories is crucial to transformer performance, but still end up being 50 perceent of all failures and insurance losses7.
Oil-filled Transformer Issues - Mineral oils are the most common insulating fluids and present the greatest fire hazards due to their flammability. Incipient faults, internal arcing and overheating produce explosive gases, increasing the probability of tank rupture, which could lead to an ignition of transformer insulating fluid. Many oil-filled transformers are sealed with an inert blanket of nitrogen. Ultrasound is used to identify failures of the rubber bushings, allowing nitrogen to escape and be replaced with oxygen.
Visual Inspections - Make a thorough inspection of the transformer and the surrounding area, looking for possible incident indicators such as animal carcasses, bulged tank or cover, discolored tank, fallen tree limbs, vegetation, vandalism, oil leaks, burnt oil aroma, cracked or broken bushings and any short circuits in the secondary or service-side. Additional information to consider includes extreme weather conditions (storms, lightning, snow, ice, outdoor temp and air humidity), excessive loads, lack of maintenance, ageing, and wear out.
Infrared Thermography - Similar to the switchgear, use thermography to examine high- and low-voltage external bushing connections, as well as external surfaces such as cooling tubes, fans, and pumps. IR testing is great for identifying low and high-temperature areas caused by a fault, bad oil or foreign materials blocking cooling passages in an oil-filled transformer (Figure 8).
Dry Transformer Hazard Indicators - Dry-types use ambient air and convection currents (sometimes fans) to keep laminated windings cool. Check for maximum ventilation air flow by ensuring air intake grates are not obstructed. Observations of dust, dirt and debris on windings, which prevent cooling, could combust causing a fire (Figure 9).
Conductors (Cables and Bus Bars)
Cables and bus bars are the crucial superhighways of power distribution in facilities as they quickly and efficiently carry power throughout a facility to do useful work. Power can only be distributed safely through conductors with tight, clean, cool and dry connections with proper insulation or metal clad covers. The main conductor hazards are poor connections and insulation breakdown. Connections, terminations and splices are usually the weakest points in cable and bus bar systems. Loose or corroded connections will generate high resistance and heat, therefore both are great candidates for infrared inspections.
Insulation is King - The insulation is rated at a specific dielectric (insulating) strength. Premature insulation failures are due to absorption of moisture, dirt, dust, grease, excessive heat, sunlight, vibration/abrasion, loose connections, oily deposits, loss of polyvinyl chloride (PVC) oil and compounds, power surges, overvoltage and aging. These contributing factors cause insulation to become brittle and crack, which allows current to have a low resistance path outward or shorting to ground.
Any arcing can ignite the combustible insulation under the sheath. The PVC insulation provides fuel for the fire and continues to burn even though the initial arc may be stopped by the operation of the overcurrent device. Research has shown that even heat generated by faults in low voltage signal wiring may generate damaging off-gases and burn adjacent combustible materials8 and horizontal cable trays9.
Moisture and dirt also allow tracking and even flashover. Another problem with moisture and the overheating of insulation is the creation of off-gases. One of the off-gases is hydrogen chloride which when mixed with water forms hydrochloric acid. This highly corrosive acid damages sensitive relays, instruments, control apparatus, copper bus bars and base metals such as iron, brass, aluminum or zinc alloys. It can cause significant fire and nonthermal damage. Lastly, manufacturing deformities during the insulation manufacturing process create high electric field stresses and can cause insulation failure.
Circuit Breakers / Fuses / Disconnects
A circuit breaker (CB) is a protective device that carries load, and if it senses a higher circuit load than the established setting, it rapidly opens the circuit interrupting the flow of electricity to/or within electrical equipment (i.e. transformers, motors, switchgear, etc.). It can be reset. CBs come in many types, sizes and voltage ratings.
Concerns - Typical CBs are installed, sit in place supplying power, and then are forgotten for years. This is contrary to the regular maintenance requirements of the OEM, NFPA 70, IEEE and National Electric Manufacturers Association (NEMA). Several studies by IEEE show that up to 50 percent of low voltage CBs can fail within five years, if not maintained properly.
Most power system failures and hazards are caused by short circuits and failure of a circuit breaker/fuse to open the circuit during overload, electrical fault or other abnormal operating condition. If it can’t interrupt the fault it may fail, destroying the enclosure and creating a hazard for anyone working near the equipment. In some instances, arcing can occur and ignite combustible materials due to the delay. The combustible insulation tied to CBs, and oil inside certain high voltage CBs, become fuel sources for a fire which can spread to adjacent circuit breakers, fuses or other combustibles.
Some warning signs of an aging or faulty power distribution system include breaker nuisance tripping or main breaker failure. The problem is that after high level fault, “it is not always clear to investigating electricians what damage has occurred inside encased equipment.”10 By design, CBs can be reset, but nuisance trips may see the CB being reset three to four times. Numerous authorities having jurisdiction (AHJ), like OSHA, no longer allow the multiple resets since numerous burns resulted from explosions.11
Failed Barrier Example: “Human Error and Disregard for Safety”12
In February 2001, an operator made an extraordinary attempt to close a molded case circuit (MCC) breaker to start a 100 HP, 480 volt, 3 phase power roof vent. The operator received a massive “arc flash” and burns to unprotected parts of his hands, arms, and face. Injuries were aggravated due to the fact that the operator had opened the module door so that he could apply added force to close the breaker, after attempts from the outside had failed due to apparent linkage binding.
Fuses & Disconnects - Fuses and fused disconnects are common electrical protection devices that provide overload and/or short circuit protection. The fuses are secondary protection in the event circuit breaker contacts don’t trip. If a fuse shows up hot on a thermal scan, it might be at or near its current capacity. However, not every problem shows up as hot. A blown fuse, for example, exhibits a cooler than normal temperature.
Motors & Motor Control Centers
The electrical condition of plant equipment is as important as its mechanical condition.
Motors - Motors are electrical rotating equipment that convert electrical energy into mechanical energy. Motors and associated windings and insulation are typically classified based on enclosure type, speed, efficiency and service factor.
Motor Concerns - Analyzing insurance related motor failure and loss data from 1989 to 2005 indicated that 65 percent of the failures and 71 percent of the losses were related to windings and electrical connections.13
Motor Control Centers (MCC) - Motor control centers house the control and protective devices for motors that drive equipment. To evaluate a motor control center under load, open each compartment and compare the relative temperatures of key components: bus bars, controllers, starters, contactors, relays, fuses, breakers, disconnects, feeders and transformers. It is important to measure the amperage load of each phase at the time of each scan, and to trend and evaluate your measurements against normal operating conditions.
Infrared thermography and motor circuit testing of MCCs and motors is an excellent combination since they can be applied to all types of motors to detect problems like poor connections in the motor terminal box and overheating windings, bearings, and motor couplings.
Poor electrical connections in the motor terminal box (Figure 12) and overheated bearings (Figure 13) often signal active breakdown and potential failure. Thermography accurately pinpoints which areas of the motor are overheating and by how much.
Overheating is caused by inadequate air flow which can be caused by clogged air intake grills. Fault current motors may experience single-phase ground faults which increase temperatures and go undetected. Figure 14 shows an example of where the intake screen was plugged because oil from the bearing got on it and collected dirt. Over time it clogged and overheated the motor and windings.
Electric motor testing provides both offline (Motor Circuit Evaluation) and online (Motor Current Analysis) testing of the motor and circuits to determine the motor’s health and identify any potential operational concerns. Typical tests performed include resistance and capacitance to ground, phase resistance and inductance to ground, current and power quality analysis, voltage unbalance and total harmonic distortion. Unbalanced voltages and overloading are usually caused by a high resistance connection in the switchgear, MCC or disconnect.
It is a good practice to regularly trend reference temperatures, comparing the operating temperatures of like equipment performing similar functions, to OEM requirements and previous readings on that unit. This helps you see abnormal readings when they occur.
IR troubleshooting tools and/or a motor circuit tester can perform power diagnostics and quality analysis to pinpoint the issues. IR is also great for identifying mechanical issues such as bearing failures and alignment issues.
KISS the Program for Optimum Results
Safety, maintenance and reliability professionals can enjoy significant reductions in personnel exposures and enhanced reliability of electrical distribution systems by deploying an integrated condition monitoring (CM) strategy with predictive maintenance (PdM) technologies (see Figure 15).
Achieving these results requires discipline and applying the KISS (Keep It Super-Simple) strategy which ensures program data is small, accurate and manageable. You have limited resources and time. Initially, focus on the assets that have the best and highest probability of success. Your efforts and communication strategies must build a return on investment (ROI) case for investing in your program, personnel and PdM technologies. Some thoughts to include:
1. Use simple MS Access database or MS Excel to track and
analyze specific information.
2. Use simple reports with easy to understand pictures and
graphics to help stakeholders understand the failure modes
and hazards, the magnitude of the risk with comparative
failure data and the potential people, production, and time
impact of a loss.
3. Regularly and consistently “blow your own horn” about the
program’s successes and challenges.
4. Document everything within your program.
5. Don’t give up – These programs can require multiple data
points and time, but will significantly drive down electrical
system exposures and losses over time.
Dale P. Smith, CMRP is the Corporate Programs Manager for Predictive Service. He has 20 years of experience within the engineering, risk/safety, facilities management and reliability consulting industries designing, implementing and running successful multisite corporate safety, reliability and energy programs for medium, large and Fortune 500 companies such as Alcoa, General Motors, Kaiser Aluminum, ADM, Schering-Plough, Wyeth and many others.
Dale formerly served as the Director of Technical Sales/ Marketing for a global engineering consulting and safety services firm. He managed combustion system safety and asset reliability programs with three global automotive, aluminum and pharmaceutical clients which represented over 300 facilities worldwide. His current projects include overseeing the development, management and growth of facility roofing and reliability programs for over 250 facilities, the associated roofing assets and 100,000 electrical / mechanical assets. The focus is ensuring that clients achieve the most cost effective, reliable, safe and competitive facility capacity.
Dale is also regularly published within the safety, risk and reliability industries and delivers numerous technical papers and training sessions at national safety, energy optimization, reliability and risk conferences. He is a Certified Maintenance and Reliability Professional (CMRP) through the Society for Maintenance and Reliability Professionals (SMRP). Dale can be reached at 216.263.7493 or at dsmitty2@cox.net.
References
FM Global. 2004. Field Engineering Equipment Hazards Fundamentals. Ontario Ministry of Labor. October 27, 2008. Safety Blitz Targets Industrial Workplaces Mcguinty government committed to eliminating workplace injuries (retrieved February 10, 2009) (http://www.labour.gov.on.ca/english/news/2008/08-99.html). Institute of Electrical and Electronics Engineers (IEEE) 1998. IEEE Guide for Maintenance, Operation, and Safety of Industrial and Commercial Power Systems. Piscataway, NJ. Taken from Predictive Service’s inspection / asset management database of with over 1,000,000 pieces of electrical equipment. National Fire Protection Association. Recommend Practice for Electrical Equipment Maintenance, Section 18-16.5. Smith, Dale P. Predictive Maintenance (PdM) Centralization for Significant Energy Savings.ReliabilityWeb (https://reliabilityweb.com/articles/pdm_centralization_for_significant_energy_savings/) FM Global. January 2007. Transformer Property Loss Prevention Sheets. 5-4 Factory Mutual Insurance Company. Chan, Kai Foo. Understanding Fire Hazards in Computer Rooms and Data Centres. Asia Pacific Fire. June 2005: 5-8 National Fire Protection Association. March 1994 Telephone Exchange Fire Los Angeles, CA. Fire Investigations. Quincy, MA “NEMA offers MCCB inspection and testing guidelines”. EC&M Jan. 1995 Occupational Safety and Health Association. OSHA 29 CFR 1910.33 4 (b) (2). Nicholas, Jack and Young, R. Keith. 2008. Root Cause Failure Analysis, 6th edition, NetexpressUSA.com. FM Global. January 2007. Motors and Adjustable Speed Drives Property Loss Prevention Sheets 5-17. Factory Mutual Insurance Company.