The eddy-current type non-contact proximity probes are typically installed on bearing housings of most critical turbomachinery equipped with fluid film bearings. Machinery utilizing fluid film bearings includes gearboxes, steam and gas turbines, compressors, expanders, generators, pumps, motors, forced draft (FD) and induced draft (ID) fans, etc. Don Bently of Bently Nevada (now GE Bently) developed the eddy-current non-contact probe system in the 1950s. In 1970, the American Petroleum Institute's (API) Mechanical Equipment Subcommittee adopted the eddy-current proximity probe as the measurement device for determining acceptable shaft vibration during factory acceptance testing. This requirement was added to API 617, the centrifugal compressor standard, which became the forerunner of API 670. As a result, shaft vibration measurement with eddy-current proximity probes emerged as the industry standard for turbomachinery acceptance testing and machinery protection.
The damping of fluid film bearings is significantly higher than that of rolling element bearings. In many cases, this high damping causes turbomachinery equipped with fluid film bearings to not transmit shaft vibration to the bearing housings very well. As a result, housing vibration measurements made via accelerometer do not accurately represent true shaft vibration. This is especially true for turbomachinery with relatively light rotors and massive bearing housings and supports. Casing or housing vibration measurements with accelerometers or velocity probes are still recommended to detect problems, such as structural resonance, loose bolts, foundation problems, etc.
Normal measurement involves two radial proximity probes (X & Y) installed 90 degrees apart at each bearing. When the probe signals are plotted against each other, the result is the orbital path of the shaft centerline within the bearing clearance, as shown in Figure 1. The average shaft centerline position within the bearing clearance also can be measured as shown in Figure 2. Adding another probe to measure a once-per-revolution event, such as a keyway, provides valuable phase information. Data plotted in Bode format from the #1 journal of a steam turbine during spin up through a critical speed is shown in Figure 3.

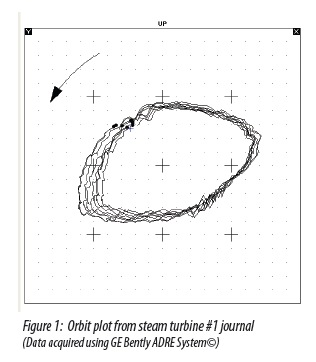

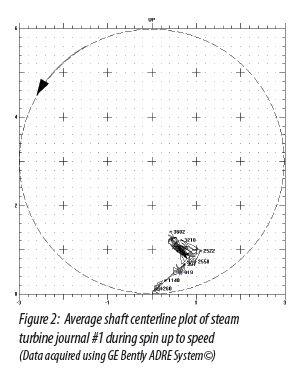
The coast-down data is considered more useful for plotting the amplification factor of critical speeds than spin up data since no torque is applied to the rotor. The amplification factor provides a measure of the damping of the rotor bearing system at a critical speed.
The shaft orbit and average shaft centerline position data are very useful to diagnose rotor dynamic problems, such as unbalance, misalignment, rotor rubs and bearing instability problems like oil whirl or oil whip.
As useful as the proximity probes are, there remains a large number of older equipment with fluid film bearings that has never been retrofitted with these probes. Installing permanently mounted proximity probes can be cost prohibitive due to requirements of an extended outage, machining bearing housings, running conduit and signal wire, as well as the cost of purchasing the systems themselves.
Many people (including the authors of this article) have attempted to solve this problem by temporarily attaching indicator brackets to a bearing housing. Magnetic bases, commonly found in machine shops, also have been used to temporarily mount the probes. Results from this type of mounting have been mixed due to occasional movement of the base itself and vibration of the arm holding the probe. Wooden shaft riders also can be used to briefly measure the shaft absolute displacement. The V-shaped stick with an accelerometer or velocity probe stud mounted to the end is held by hand against the rotating shaft. It is possible, although difficult, to hold two sticks at 90 degree angles to measure the shaft orbit. However, the sticks can only remain against the shaft briefly due to the heat of friction.
A recently introduced device addresses the problem of temporarily mounting eddy-current proximity probes. Removable proximity probe mounts (patent applied), as shown in Figure 4, have two powerful flat rare earth magnets that firmly attach the probe holders to the end of a machine's bearing housing. The removable proximity probe mounts in Figure 4 are installed on an ID fan. These mounts provide a means of installing X/Y proximity probes temporarily on important rotating machinery to measure data during startup, shutdown, or load changes. Permanently mounted proximity probes are no doubt preferred, but for those machines where this is not feasible, temporary probe mounts are a low cost, excellent alternative.
A bubble level with a rotating protractor (Figure 5) provides the ability to set the probes at exact angles, such as 45 degrees left and 45 degrees right. Extension brackets provide a means of locating the probe at various distances from the end of the bearing housing (Figure 6). This feature is particularly helpful when portions of the shaft are damaged.
Users have been very innovative with removable proximity probe mounts on non-traditional equipment that includes vertical pumps (Figure 7) and a balancing machine (using proximity probes to measure shaft run-out at the probe tracks). Typical equipment applications include FD and ID fans, steam turbines, generators, motors, boiler feedwater pumps and gearboxes.
Notable Features of Removable Proximity Probe Mounts:
- Adjustable bubble level with protractor angle gauge allowing accurate positioning of brackets;
- Two strong, flat permanent magnets hold the mounts firmly to the bearing housing;
- Machined surfaces on exterior of mount to allow ease of mount positioning;
- Two jacking screws provided for ease of mount removal;
- Extension bars provided to allow movement of the probe to a more desirable portion of the shaft;
- Anodized aluminum construction for lightweight, corrosion-resistant operation;
- Mounts fabricated to accommodate either 5 mm or 8 mm standard probe sizes.
Attaching proximity probes to the bearing housing of a machine for which data from the shaft is desired is just part of the setup. The proximity probes require a driver, -24 VDC power and cabling. Such a system can be provided by Custom Machinery Solutions (CMS) and utilizes a Connection Technology Center (CTC) brand NEMA enclosure, proximity probe drivers and a 120VAC/-24VDC power supply.
A typical application is shown by the schematic in Figure 8. Two removable probe mounts (X & Y) are mounted on each bearing of a machine. Extension cables are then connected to the probe cables and the probe drivers. The probe drivers are housed in a NEMA enclosure (yellow). The probe drivers are powered by a -24V DC power supply (grey) connected to 120VAC power.
The shaft displacement (AC & DC signal) is measured from BNC outputs on the probe drivers. A once per revolution signal is required to measure the phase lag angle. This signal may be generated by either an optical tachometer sensing reflective tape or a proximity probe sensing a keyway.
Typically, a multi-channel data acquisition system is used to record the data. Data acquisition may be for a few minutes, hours, or several days depending on the circumstances.
A simple, two-channel analyzer capable of generating orbit data also can be used. Data may be acquired from each probe set at each bearing for a given speed/load condition. Comparisons between proximity probe data and data from accelerometers at identical orientations also can be helpful. Coast-down data from two x-probes or two y-probes also would be possible using only a two-channel analyzer. Gathering true orbit data from each bearing allows easy measurement of the true maximum shaft displacement (Smax) preferred by standards, such as ISO 7919, for accurate measurement of machine condition. If the long axis of the orbit is not aligned with one of the probes, as shown in Figure 9, the maximum amplitude is greater than indicated by either the X or Y probe.
There are many fluid film bearing machines in service that were never equipped with permanently mounted proximity probes. Now there is a device available that will permit temporary attachment of proximity probes to measure the shaft vibration on many of these machines.