The Latest Technology for Asset Management in Oil & Gas
Combining Mechanical Integrity and RCM for Time, Cost Savings
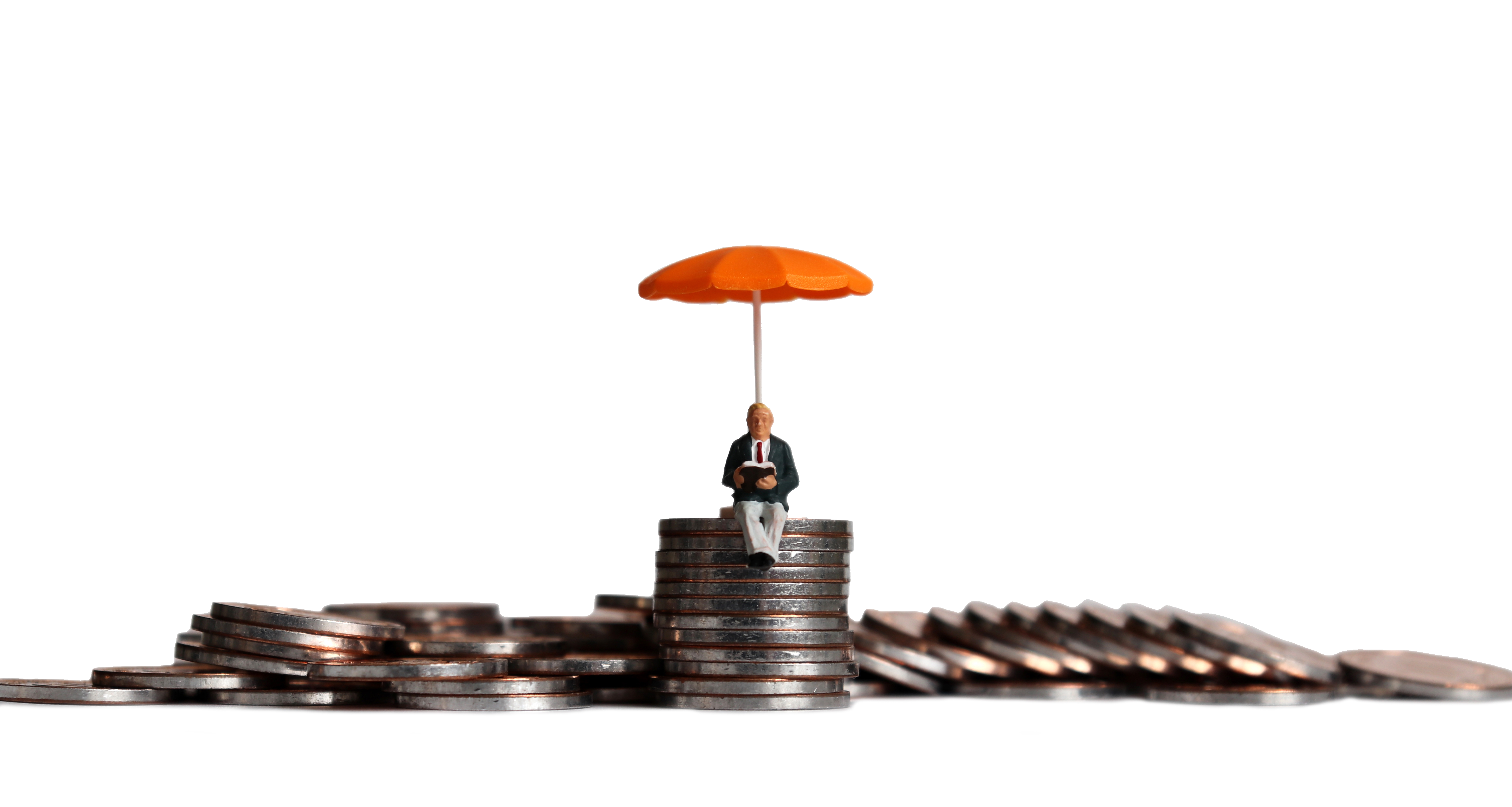

For owner-operators of oil, gas and chemical companies, mechanical integrity (MI) and reliability-centered maintenance (RCM) are pivotal components of any comprehensive asset management (AM) program. However, most companies tend to treat MI and RCM as separate programs, utilizing different tools for each – where MI is administered by the engineering organization and RCM is administered under maintenance. Yet, with the advancement of technology in this area, there is now a far more cost-effective approach. The truth is, MI and RCM both fall under the larger umbrella of asset management. These days, both can be efficiently managed with one software tool, improving transparency and efficiency, while significantly reducing costs overall.
The Evolution of MI and RCM
In the U.S., MI and RCM evolved separately for many reasons. MI is driven mostly by American Petroleum Institute (API) standards, while RCM originated in the aerospace sector and the base standards come under the Society of Automotive Engineers (SAE). AM standards are relatively new and were driven by the International Organization for Standardization (ISO).
While MI was driven by safety and legal liability requirements, RCM was driven more by business needs to improve production certainty and reduce maintenance costs. Most maintenance organizations in the U.S. are still highly reactive due to a fear that vital work would fall behind immediate needs. Many maintenance groups’ preventive maintenance for critical equipment has lower schedule compliance.
The Challenge

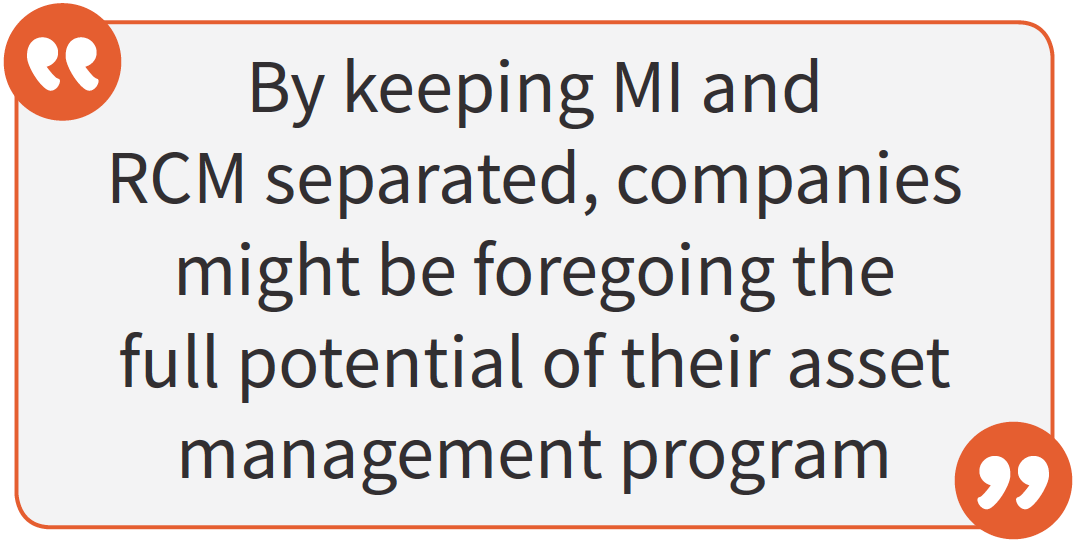

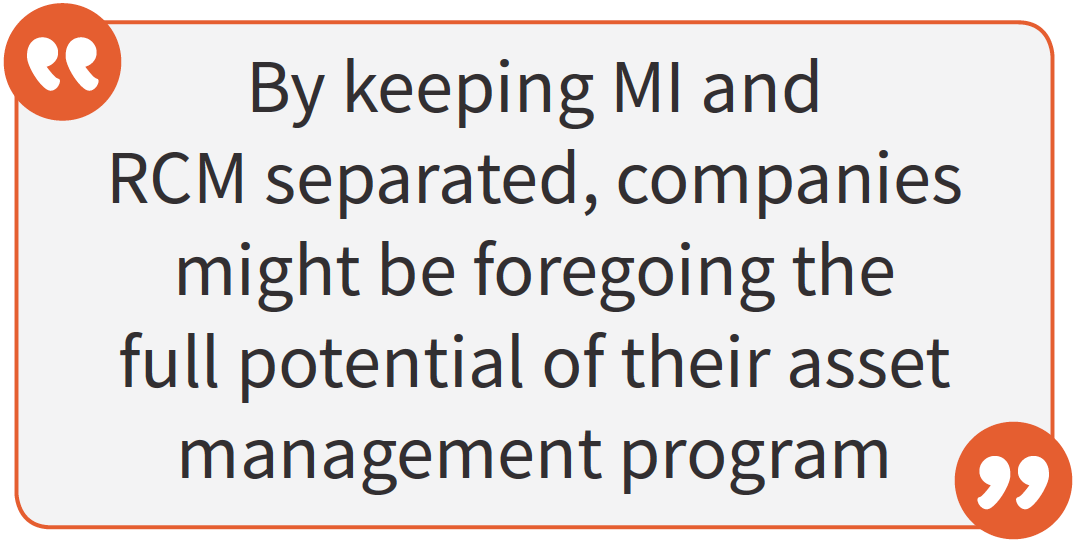

By keeping MI and RCM separated, companies might be foregoing the full potential of their asset management program. Take, for example, the factoring of complex asset types. Assets have long been divided into fixed or static equipment and rotating equipment, which often put control valves, instrumentation, electrical and other assets in limbo. Tanks, some piping and structures that are not specifically covered by standards could be missed either in inspection or maintenance plans. Piping is rarely listed in the asset registry unless care is specifically required by standards.
When adding new equipment to an RCM program, some equipment is assumed to be tracked under an engineering inspection program. While a critical system can include vessels, exchangers, piping, tanks, etc., failure mode and effects analysis (FMEA) and care plans are rarely entered into the computerized maintenance management system (CMMS) for planning, scheduling, or compliance tracking by the maintenance organization.
MI can address the inspection planning of all asset types. Care plans are tracked in engineering databases or specialized software and, with the right product, can be seamlessly connected to a company’s CMMS for planning, scheduling and compliance tracking.
The Solution: One Software for Both
Changes are occurring that will encourage the integration of MI and RCM programs and benefit the care of all assets.
Most companies now recognize that operational excellence requires all stakeholders in the facility to be on the same team driving performance for the betterment of safety and financial success. More and more, finance/accounting, engineering, inspection, procurement, operations, maintenance and other organizations within the facility are working together to improve and sustain the business.
The ISO55000 asset management standard is educating all about what assets make up a business and how all stakeholders need to be held accountable for them. The Industrial Internet of Things (IIoT) and the Digital 4.0 revolution are providing tools that make information sharing and performance tracking easier for all.
Specifically, there are now software and digital data systems that enable tracking of all assets, helping a company manage both MI and RCM from one software platform.
The Benefits
Managing all facets of a company’s asset management program with one software facilitates immediate cost and time savings benefits to owner-operators. By combining both services into one program, the operator will experience substantial cost savings in program maintenance, training and software updates. Having all data, for all asset types, for both integrity and maintenance in one digital database results in heightened transparency and readily accessible actionable intelligence. Digitizing and streamlining processes into one program improves efficiency, security and reliability. Moreover is the added benefit to end users, who no longer have to learn and maintain functional knowledge of many different software programs. As an added bonus, selecting a software that connects to the company’s existing CMMS helps complete the loop for work order management.
Selecting the Right Software
Modern day inspection data management software (IDMS) has evolved to include a wide range of features and functionality that can address the requirements of both MI and RCM. At its core, a comprehensive IDMS software already addresses MI, so it’s important to find one that can also support the specific requirements of RCM. When looking for software capabilities to address RCM specifically, consider its four components: reactive, interval, condition-based maintenance (CBM) and proactive. The right software should:
- Reactive: Allow for the management of the reactive component by enabling a user to manage small, noncritical items that are either unlikely to fail or may be redundant (i.e., run to failure);
- Interval (preventative maintenance): Monitor equipment that is subject to wear or has known failure patterns and maintain it on specific frequencies or intervals;
- CBM: Allow for equipment with random failure patterns or ones not normally subjected to wear to be assessed on risk and managed accordingly;
- Proactive: Retain inspection results, such as root cause failure analysis and FMEA, with appropriate maintenance and further inspection scheduling, all managed within the software.
From there, to ensure both RCM and MI are being supported, seek an IDMS that has the following features:
- All asset types from a single platform – Includes rotating and fixed/static equipment, as well as tubes, piping, offshore structures, valves, etc.;
- Configurable risk-based inspection (RBI) – Supports inspection planning based on RBI methodology, allowing owner-operators to prioritize critical assets over noncritical; Ideally, seek a software that allows the company to configure its own RBI model according to its unique needs;
- General trending– For specific measurement trending;
- Scheduling – Planning inspections with the ability to retain photos and attach inspection documents; Further aids in equipment management and simple data retrieval;
- Seamless adherence to all major regulatory standards– Includes ISO and API to facilitate regulatory compliance in the case of an audit
- Flexibility– Accommodates the various components of RCM while also providing an efficient solution for equipment management; Helps keep costs at a minimum;
- Key performance indicators (KPIs)– Allows the operator to produce management reports on equipment failure frequencies, operational availability and maintenance scheduling;
- Integrity operating windows (IOW)– Allows for monitoring of specific equipment variables that have a direct impact on equipment performance (e.g., for rotating equipment, if vibration monitoring is tied into the DSC, the IOW can track preset, high vibration alarms).
Conclusion
The evolution of technology delivered by the IIoT has resulted in more options than ever before for the asset management needs of oil, gas and chemical companies. There is no need to continue running RCM and MI as separate programs when both can be supported by one software, delivering tangible time and cost-saving benefits.