A reliability program is only as strong as the reliability culture. There are six common culprits that can rob a reliability program by creating a disengaged and adverse workforce. Employees do not start out this way, but become so as a reaction to these six offenders. Thankfully, once they are identified, corrective actions can be taken to positively reengage the workforce.
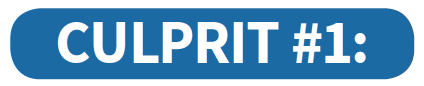

Craft Employees’ Input Is Unheeded
Maintainers and operators likely know the equipment better than anyone at the plant. Yet, when they have suggestions, they notice when nothing is done with their ideas. For example, one technician stopped annotating his preventive maintenances work orders with any notes or suggestions. His response as to why will change your way of thinking about reliability: “When I first started my career, I used to add notes and redline work orders for any errors. These work orders would come back again and again with none of the changes I suggested. After doing that for a few years, I just stopped doing it.” Another tradesperson recalled his boss telling him his job was to do and not to think! It’s no wonder a recent Gallup poll found that less than a third of employees are engaged with their work. When the workforce observes their input is not valued, they begin to disengage. Additionally, ignored feedback begins to feel like unwelcome feedback, thus justifying a culture of disengagement.
If your organization honors and respects craft employees’ suggestions, are the employees who make them given any feedback or credit for those suggestions? If not, why not? Many organizations fail to give feedback simply because there is no protocol to ensure meaningful feedback is provided. Leaders must focus on what messages are being sent to craft employees based on their words and actions.
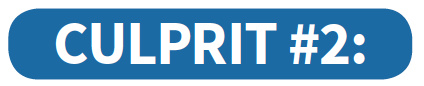

Reactive Work Is Predominant and Rewarded
Many organizations like to celebrate and reward employees who work extra hours and do a great job bringing the plant back into operation after a breakdown. Yes, these folks should be rewarded, however, when do you hear of a celebration because the plant was more reliable and nothing broke down? Imagine a scenario where you do not proactively look at the wear on your automobile tires. Instead, you celebrate because you had a flat and were able to change to a spare in record time. Sounds a little backward, doesn’t it? A celebration would be more appropriate if you did not have a flat at all. But, how do you celebrate when nothing happens? Using reliability metrics, such as mean time to repair (MTTR), mean time between failures (MTBF) and ratio of proactive to reactive maintenance are some of the ways you can celebrate when these metrics show improving trends.
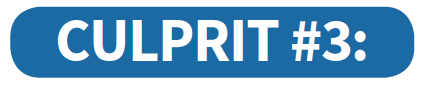

Fake Metrics
When using metrics, you have to be honest with yourself. Many organizations tout their preventive maintenance (PM) completion rates as being close to 100 percent. But when you look closer, they either cancel PMs to make the metrics look good or schedule so few PMs that 100 percent completion is meaningless. If you include integrity as part of the reliability culture (and you should), the message you send when you fake your metrics is that fudging or even lying is acceptable as long as the numbers look good.
Another issue with metrics is not setting a challenging goal. When you set the bar too low, the message is that the status quo is fine, when in reality, it is not. Authentic metrics are motivational to the organizational culture and provide a source of pride when they are trending in the right direction. Their meanings and trends should regularly be communicated to your technicians. Metrics are supposed to drive behavior. If no one sees the metrics or understands the meaning of them, how are they going to help drive a change in culture?
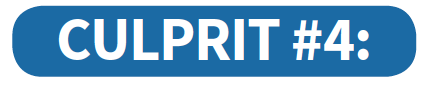

Lack of Clear Procedures and Over-reliance on Tribal Knowledge
Many PM job plans lack details about the work. For example, a job plan may say, “inspect pump on a monthly basis.” But, what does that mean? To one individual, it may mean closely check for leakage, proper operation, listen for bearing noise, and more. To another, it may mean walk by and make sure it is still there. That may be an exaggeration, but the point here is that unclear job plans lead to inconsistent inspections. Some might argue that the craftspeople are experts and know what they need to do. This is what is known as tribal knowledge. However, if details are not captured in job plans and procedures, what happens when the “tribe” retires? Additionally, if enough details are not provided, PM performance becomes inconsistent. If failures were to occur, how would you know if the inspection was actually performed or if anything was missed?
Mission, Vision and Goals Are Not Disseminated or Understood
Most organizations have high-level mission, vision and goal statements; yet often, these statements are not translated to the branch level. Knowing how each branch can promote and effectively help the enterprise’s mission is critical to having a good reliability culture. Maintenance technicians should be able to answer the question on how their work contributes to the corporate mission. This promotes a unifying message that can be used to keep work on track and accomplish steady improvements. Everyone in the organization should know the mission, vision and goals of their branch and how it relates to the overall enterprise.
Bad Housekeeping Is Tolerated
Housekeeping is highly indicative of the success of reliability programs and, for that matter, the safety culture. Within minutes of walking into a plant, a reliability professional can get a sense of whether the culture is engaged or not. Too often, management accepts bad housekeeping because the technicians are too busy to clean up. If management accepts this, it sends a debilitating negative message to their team. Think about the time it takes to find tools or parts when areas are not organized. Organized and clean areas save time and reduce the potential for injury. In fact, if a manager wants to pick one area to improve, housekeeping sends the quickest and best message that a culture change is about to happen.
Awareness Is Key
To change the reliability culture, you must be aware of how a bad culture is created. One way to do this is to identify whether any of these six culprits, or any others, are going on at your plant. Once becoming more aware of these behaviors, new strategies can be created to turn around the performance and exemplify a new cultural direction.