The biggest problem we find in bearings is the fact that they are over greased. The maintenance man doing the greasing usually does not know how much grease is put into the bearing. In the past we just pumped a few strokes into the bearing and then said well that ought to do it. Usually that was too much grease and the following pictures will show the results of that style of greasing.
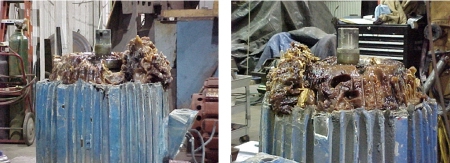
We can actually here the grease hit the bearing. When it sounds like air escaping we stop the greasing and leave it alone. No need to put anymore grease in there it will only do more harm than good. We then go and check other bearings and return to this on in about 10 or 15 minutes. In checking it again if the smooth sound is still there then great we caught this one in time, if the noise has returned then this bearing is marked for attention and or replacement. Usually this bearing will be watched and when the noise starts to get loud enough we can here it with our own ears and the temperature starts to rise then it is scheduled for replacement.
In the case of this motor there was no attention paid to how much grease was being put into the bearing. The old days of grease until it oozes out are long gone but people do actually still grease that way. This motor actually had shielded bearings in it and there was no grease getting into the bearing, so it never cooled down and never got any quieter so they just continued to grease it. After a point there was so much grease in it that the motor started to heat up. What did we do then? WE GREASED IT SOME MORE.
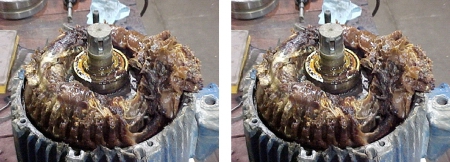
This is the results we get when we over grease a motor. Also notice that these are sealed bearings. WHY was the grease zirks not pulled to keep this from happening?
With the bearing program that is offered from Peterson Predictive Maintenance this could never happen. We would be able to tell when the bearing had enough grease or even if the bearings were shielded bearings. If there is never a decrease in noise, from the grease getting into the bearing, or in fact an increase in noise then the bearings are most likely shielded and greasing will do no good.
By running all the critical machines bearings on a quarterly basis that allows us to insure proper lubrication and it will also allow us to trend the bearings giving us data to predict a potential failure in the future. With the Ultrasound Bearing Program we can actually hear the chrome flaking off of the balls in the bearings before vibration will pick it up. We have documentation where we have predicted problems in bearings 3 to 5 weeks before vibration has picked it up.
Let's review what can be accomplished with our bearing program
1. Proper lubrication of motor bearings
2. Early prediction of potential problems in bearings
3. Trending and data gathering to back up these predictions.
4. All data and records are downloaded to your computers so you have it at your fingertips
5. Never over grease another motor.
6. Repairs are now scheduled and not completed in a very expensive down time situation.