ROOT CAUSE ANALYSIS
Improving existing plant performance requires the elimination of repeat failures or emerging failures. Root Cause Analysis (RCA) is undertaken as a search for the "Root Cause" of the problem. Effective RCA is really about seeking effective solutions that control the causes of problems. Like a detective we look for causes from the effects. Each cause produces the next effect. When we define a problem and begin looking for causes, we ask why of the effect, and answer with a cause. Effects become causes as we continue to ask why, and a cause and effect chain is established. The solution we select is the one that is attached to one of the causes that prevents the problem from recurring.
Understanding the cause and effect relationships of equipment and operational problems, is an essential part of an effective maintenance program. The best way to institutionalize RCA is to train all levels of an organisation, so that seeking effective solutions is applied at the workplace and capturing "good" failure data for analysis is a normal requirement.
LIFE DATA ANALYSIS

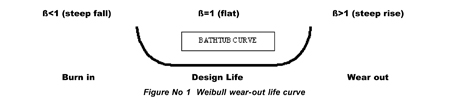
It is now one of the most commonly used methods for fitting equipment life data and has been used extensively in the aviation industry. The essence of Weibull's work was to discover he could represent the Bathtub Curve of Figure No. 1 using one mathematical formula. The three zones of the bathtub curve can be represented using Weibull parameters beta (shape parameter), eta (life) and gamma (location).
Understanding the Weibull shape parameters provides the owners, users and maintainers of equipment with a tool to predict the behavior of engineering components and select effective maintenance strategies.
β<1 implies infant mortality. Electronic and mechanical components often have high failure rates initially. Some components are ‘burnt in' prior to use, others require careful commissioning after installation.
β=1 implies random failures. These failures are independent of time where an old part is as good as a new part. Maintenance overhauls are not appropriate. Condition monitoring and inspection are strategies used to detect the onset of failure, and reduce the consequences of failure.
1<β<4 implies early wear out. Failures of this type are not normally expected within the design life. Failure mechanisms such as corrosion, erosion, low cycle fatigue and bearing failures fall in this range. Maintenance often involves a periodic rework or life extension task.
β<4 these are wear out or end of life failures. They should not appear within the design life. Appropriate maintenance is often renewal. An ideal profile for equipment is to have a negligible failure probability throughout its design life followed by a steep b where the replacement age can be predicted. Age related failures include stress corrosion cracking, creep, high cycle fatigue, and erosion.
Today Weibull analysis is commonly being used to predict safe intervals for operation in applications such as warranty periods, shutdown intervals and increasingly in setting maintenance and inspection intervals. With more sophisticated CMMS in use, the collection of failure mode data is more reliable and data analysis can be handled electronically.
Many organizations have been keeping records of failures manually or in computer systems, but not using the data in any useful way. Failure data is the best source of reliability information available. It has relevance and is easy for site people to relate their own experience to. By transforming it into useful information from which failure forecasts can be made it can then be used to model the benefits of alternative strategies or to analyze the reliability of current systems and the capacity to meet operating needs.
LIFE CYCLE SIMULATION
Having determined the Weibull parameters that best represent failure mode behavior, they can be used to simulate performance over extended periods of time. Modern simulation packages involve a simulation engine that generates random numbers in accordance with the Weibull parameters over a specified system lifetime. Used in conjunction with Reliability Centered Maintenance (RCM) principles, the process of selecting maintenance and inspection intervals becomes a process of playing "what if" by comparing different reliability strategies.
Article submitted by by: Mick Drew of ARMS