The end result of a diaphragm alignment is to have all of the diaphragms lined up when the turbine is running. All of the diaphragm centers have to sit at a certain horizontal and vertical deviation from a reference line to within 0.005" when the rotors are in and the turbine is closed up. This is easier said than done because you cannot perform the diaphragm alignment when the turbine is assembled. First you have to determine what the alignment reference line will be. The alignment reference line is made up of several components. First there is the catenary curve of the turbine rotor. This is the natural sag that occurs in the turbine rotor that will not spin out of it when the rotor is at running speed. Next there is the thermal growth that occurs at turbine components that will affect where the rotor sits. Thermal growth will cause the rotor to rise up or come down at a bearing which will move the entire alignment line. The catenary curve and the thermal growth have to be considered with the turbine completely assembled. This is the effective alignment line that the diaphragms have to conform to. The catenary curve and thermal growth data should be provided by the turbine OEM, you have to determine the rest of the alignment line and combine all of the data together.
Rotor disassembly readings should always be performed before the rotor is removed from the turbine. These readings are taken at two points that are immovable, this way the rotor can be installed back into the turbine the same way it was taken out. The oil deflectors are ideal positions to take the rotor disassembly readings. During the diaphragm alignment the line can always be referenced to the oil deflectors. This makes confirming moves during the diaphragm alignment simple and less time consuming because only three measurements will have to be taken, the two oil deflectors and the diaphragm that needs to be measured.
Before any diaphragms are measured they all have to be locked into place. The diaphragms should either all be moved to one side of the shell and locked into place or Garlock can be placed into the gaps in between the diaphragm and the shell to prevent the diaphragms from moving during measurement. It is necessary to measure the diaphragm centerline deviation with the top halves of the diaphragm on and the turbine case on and torqued down. This is how the diaphragms will sit when the turbine is reassembled. Every effort should be made to take all diaphragm centerline deviation readings with the top on. Sometimes this will be difficult to do in the high pressure end of smaller turbines (under 150 MW), given the small diameter of these bores. The centerline diaphragm deviation will be different in the tops-on state than when the turbine case and top halves of the diaphragms are off. This tops-on diaphragm centerline deviation is recorded and used to adjust the centerline reference line when the tops-off measurements are recorded.
The rotor catenary curve must be incorporated into the diaphragm alignment process. The sag amount of the rotor at each diaphragm should be provided by the turbine OEM. If this information is not available it can be calculated or measured during turbine disassembly. It is only acceptable to measure the previous sag deviation during disassembly if the turbine was in operation without rubs prior to the shut down. Figure one displays a typical catenary curve of a turbine rotor.

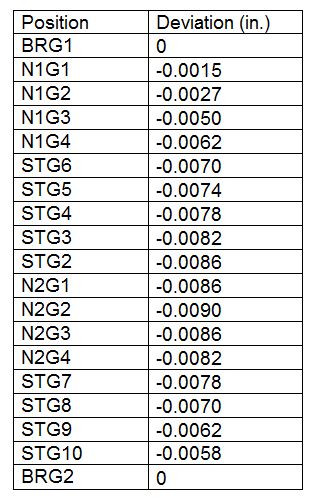
The above catenary curve data shows the rotor vertical deviation from centerline. Each diaphragm will have to be adjusted vertically to account for the rotor sag at its respective point.
During the alignment process it is important to pay close attention to which readings are taken shaft to bore and which are taken bore to shaft. Each method of measurement reference is 180 degrees out of phase with the other. A shaft to bore reading measures where the shaft is in relation to the bore or the rotor in relation to the diaphragm. A bore to shaft reading measures where the bore is in relation to the shaft or where the diaphragm is in relation to the rotor. A shaft to bore reading would note that the rotor is low to the diaphragm, the same situation taken as a bore to shaft reading would note that the diaphragm is high to the rotor. The shaft to bore reading would result in a negative value and the bore to shaft reading would result in a positive value. This is important to keep in mind when the catenary curve data is combined with tops-on/tops-off data and considered as alignment targets for the diaphragm alignment. Rotor disassembly readings and catenary curve data will be recorded in shaft to bore format. When diaphragm misalignment alignment readings are acquired with a laser alignment system or optically they will be in bore to shaft format. A sign conversion must be performed before combining the data.
The tops-off alignment readings are taken using the same reference line as the tops-on data. This will provide for a constant reference line to correlate the two sets of readings. Generally the tops-off data will show the diaphragm sitting higher than the tops-on data and the diaphragm will be in the same location horizontally. This is because the diaphragm tends to expand horizontally when the top is off. This will cause the bottom of the diaphragm to rise up. The original set of tops-off data is referenced to the tops-on data and is used to create the alignment target for the diaphragms. This should be calculated and recorded immediately after the first set of tops-off readings are acquired and before any moves are made. The tops-on/tops-off deviations are combined with the catenary curve, thermal growth, and rotor disassembly reading data. This data will create the final alignment reference line. All diaphragms will be moved and measured in the tops-off state from this point forth. The diaphragms will all be moved into alignment according to the calculated alignment reference line.
After all of the diaphragms are within 0.005" of their alignment positions the diaphragm alignment is complete. A final check of the diaphragm to rotor clearance will be performed when the rotor is installed. The rotor disassembly readings are taken again. The values should be identical to the readings taken before the rotor was removed. Gap checks should also be performed between the rotor and the packing at each diaphragm location. Remember that the gap on the bottom may be smaller than what is acceptable, but this gap will increase in the tops-on state. If you are diligent in all of your calculations and pay attention to the method used to acquire data you will be able ascertain an appropriate alignment reference line. Consequently you will be able to perform a diaphragm alignment to within acceptable alignment tolerances.