by Jarrod Potteiger
In the average plant, many mistakes are made with respect to grease selection, application amount and application frequency. The key to optimum grease lubrication for bearings is to add the maximum amount of grease without causing harm.
This maximum amount is based on the bearing's size and speed. In most bearings, grease will have a very long service life, thereby maximizing the required interval for reapplication, which, in some cases, could be years. There are, however, many factors that can curtail grease life, such as bearing type, operating temperature, vibration and contamination. When the combined effect of these factors is great enough, grease service life can be reduced to mere days or even hours. In these cases, it makes sense to employ automatic application systems to lessen the burden on lubrication technicians, freeing them up to deal with other issues. There are other situations where automatic application is attractive, such as the sheer number of grease points, accessibility issues and safety. Yet another potential benefit of automatic application is consistency. Assuming a system is designed and tuned correctly, one can be relatively sure that the correct amount of grease will be maintained in each point. Conversely, manual application injects the human factor, which is subject to the opinions and actions of individuals. Regardless of the reasons, once it is determined that automatic application is the right path, the next step is to decide which type of system to install.
While compact, single point lubricators are appropriate in many applications. However, the focus of this article is on centralized, multipoint systems. Centralized application systems are those that lubricate many points from a single system. They can be categorized into three primary categories: single line parallel (non-progressive), single line series (progressive) and dual line parallel systems. Each of these systems has advantages and drawbacks in the areas of cost, versatility, maintainability and durability.
Single Line Parallel (Non-Progressive)
Single line parallel systems are the most simple and inexpensive. In these systems, a pump pressurizes a main supply line and fills a number of injectors, all of which operate independently of one another. Once the injectors have been primed, they utilize a spring to deliver the grease over a short interval. Application rates can be adjusted by changing the pump cycle time or adjusting the stroke of the injector cylinder. The units are well suited for smaller, compact machines where the length of the primary supply line is limited to a relatively small area. However, these systems don't do well with very viscous lubricants over long distances. Major advantages of these systems are they're easy to repair and modifications, such as adding additional lube points or changing delivery volume are relatively simple.
The fact that the injectors operate independently can be a good or bad thing, depending on the system being lubricated. Independent function means an individual failure of one injector doesn't disrupt the rest of the system. On the other hand, there is no central signal that provides an alarm when a failure does occur. This lack of a central signal makes rigorous inspection that much more important. If technicians are vigilant and proper preventive maintenance (PM) inspections are in place, the problem will be neutralized.
Single Line Series (Progressive)
Single line series systems utilize a very different distribution method. In a series progressive system, the pump delivers grease through a network of divider blocks that contain a complex system of interconnected spool valves. As the grease flows through the block, it subsequently fills one cylinder while moving a piston to deliver grease to a lube point. At the end of the stroke, another port is revealed and the flow is redirected to the next cylinder and so on. In this way, grease is delivered to each lube point in succession so that if grease is delivered to the last lube point, it may be assumed that each point received its specific amount. These systems are capable of delivering grease further distances than the non-progressive systems, but they require more extensive engineering up front. It is somewhat difficult to add lube points and adjusting the delivery volume requires either new, larger valves or increasing the cycle rate for the entire system.
With respect to system monitoring and failure isolation, the series system is the opposite of the parallel system. In this case, a central signal can be generated from the end of the system that alerts the user to a failure, thus making fault detection easy. A failure at any point in the system, upstream or in the divider blocks, will be propagated through the rest of the system, allowing for easy monitoring. The downside of this is that a failure at one point will result in lubricant starvation for all subsequent points. If the nature of the lube points is such that a failure to deliver grease could cause immediate harm, this may be a big problem. When this is the case, it is necessary to define the response to a failure accordingly. It is also important to note that one of the most common failure modes of all automatic grease systems is line breakage between the injector and the lube point. In this case, the only way to identify a failure is a complete system walk down, no matter which type of system is installed.
Dual Line Parallel
Dual line systems are the most complex and expensive systems, but they offer several advantages. Dual line systems can accommodate hundreds of lube points and cover large areas. In these systems, the lubricant application rate is determine by the cycle time and the displacement of the valve cylinders.
The dual line system uses two pressurized feed lines to deliver grease to the injectors. Each time the system cycles, one of the lines is pressurized to both fill one side of each injector and deliver grease from the other side to a lube point. When the appropriate pressure is generated at the end of the line, a diverter valve is signaled, which redirects the grease flow to the other side, reversing the process. In this way, half the system's lube points are lubricated with each cycle. These systems typically utilize very powerful pumps and are capable of delivering large volumes of very viscous fluids over long distances, making them a common choice for systems with many large bearings, such as paper machines and many steel mill applications. It is also fairly simple to add lube points to an existing system.
The most significant downside of dual line systems is that they are relatively expensive due to the component's cost, installation and twice the use of tubing and fittings compared to a single line system.
Maintenance of Centralized Grease Systems
The drawback of most automatic lubrication systems is the natural tendency to ignore them. Because they are designed to eliminate work, people tend to install them and consider the problem solved. Although most centralized grease systems are very reliable, they are not maintenance free. They require proper maintenance just like any other critical asset and should be subjected to rigorous inspections with defined corrective actions for abnormal conditions. Proper maintenance for these systems is really quite simple. Daily and monthly inspections should uncover any common problem that would likely arise and provide ample warning to take corrective action. The following is an example of a good grease system PM program.
Daily Inspections
- Inspect the system's pumping station for any alarms.
- Check the grease reservoir level.
- Perform a general inspection of the pumping station and note any abnormalities
Monthly Inspections
- Perform an entire system walk down to check all grease lines, header lines and grease fitting lines.
- Check doser/injector operation. While performing line checks, note the status of the flags/pins on each injector (e.g., up/down or in/out). Next, energize the system and then make sure each flag or pin has moved to the opposite position.
- Perform a general inspection of the air and electrical supply to the pump and other components to ensure they are in good working order.
Different systems may have unique inspection or maintenance items that apply, but, in general, these are the main steps required to ensure trouble-free operation. The criticality of certain components or the criticality of components receiving timely lubrication may elevate the need for individual line checks, so inspection frequencies should be adjusted accordingly.
Whichever centralized grease application system is ultimately chosen and installed, the reliability of the system and the assets it lubricates will be largely determined by the quality of the inspection and the maintenance process for the system.
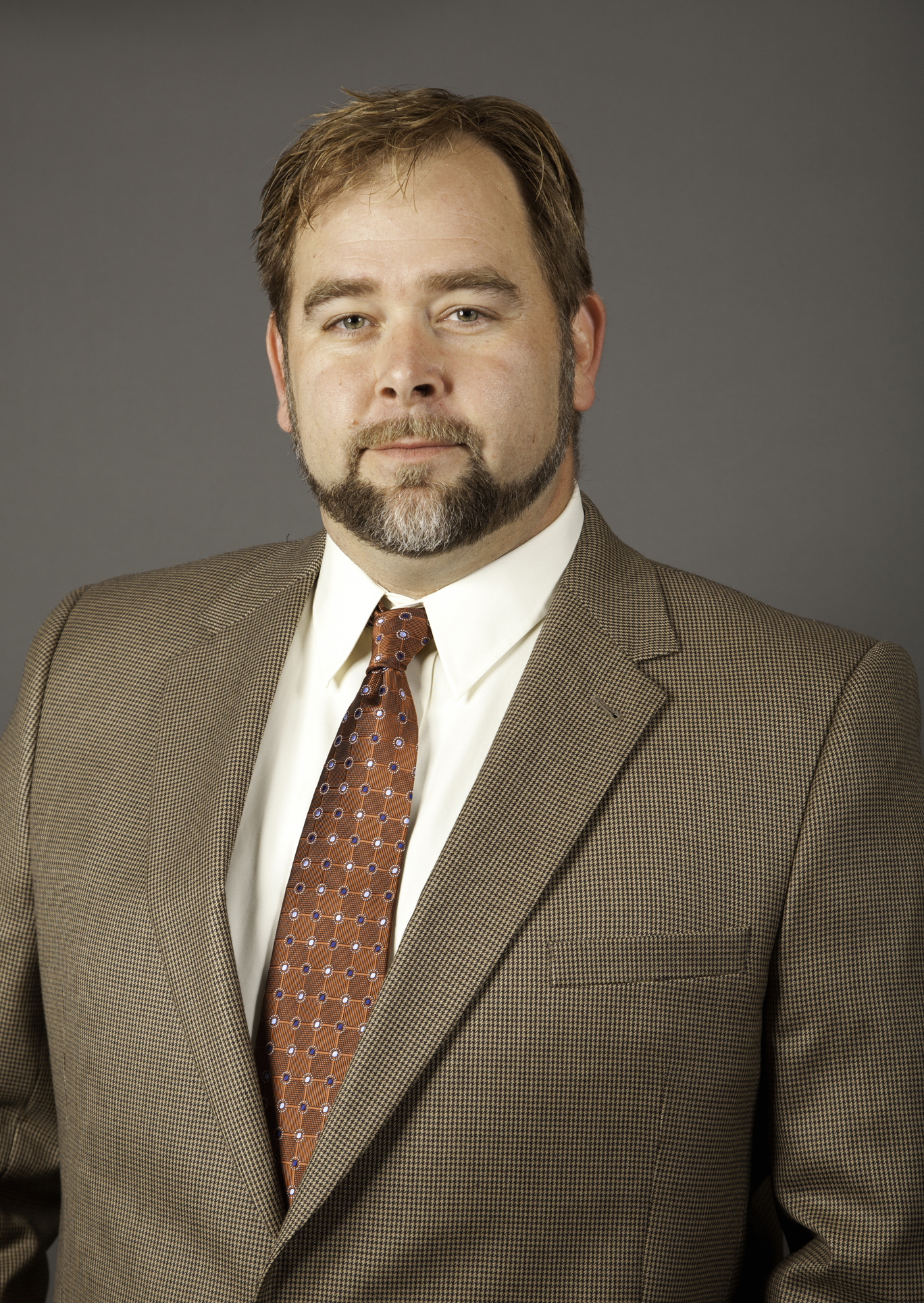