Algunos procesos industriales utilizan el ultrasonido para identificar las trampas de vapor, y todas las plantas obtienen beneficios de seguridad de su capacidad para encontrar fallas eléctricas. Recientemente, los profesionales de PdM han abierto sus ojos al ultrasonido por las ventajas que ofrece como una tecnología de predicción. El ultrasonido suele dar una alerta temprana a un problema que se avecina y se está desarrollando en un cojinete o ayuda a optimizar la lubricación de los equipos rotativos.
Todas estas aplicaciones valiosas contribuyen al ahorro de miles de millones de dólares de tiempo de inactividad, eficiencia energética, y la calidad de los productos. ¿Hay espacio para ahorrar aún más? Bueno, basta con considerar el hecho de que la mayoría de estas inspecciones se realizan en activos fijos solamente. Son posibles ahorros adicionales para los activos móviles? En muchas empresas, como la minería, la producción de cemento, canteras, contratistas de ingeniería civil, granjas industriales, flotas comerciales, y los buques oceánicos, el ciclo de producción depende de los vehículos pesados, cargadoras, vehículos todoterreno, y los buques de navegación marítima. Seguramente, debe haber beneficios que la inspección de ultrasonido podría realizar en estos activos móviles.
Estos vehículos tienen una amplia gama de aplicaciones como el transporte de las mercancías en tierra a los puertos marítimos y más allá. Se utilizan para sembrar, mantener y cosechar, para excavar la tierra y se mueven miles de toneladas de materias primas en las canteras y minas a cielo abierto. A pesar de su tamaño puede variar entre 30 toneladas a más de 350 megatones, que todos tienen en común un motor de combustión interna para proporcionar la energía para poder mover el vehículo y la hidráulica.
La mayoría tienen una cabina para mantener al operador seguro, seco, caliente o frío, mientras que otros tienen volúmenes de almacenamiento que deben ser a prueba de la intemperie, por lo menos, y herméticamente ajustados en el caso de transporte de contenedores refrigerados. Y en muchos casos, los sistemas de aire comprimido se utilizan para el frenado y sistemas de suspensión.
Para proteger la inversión en estos activos móviles, el mantenimiento preventivo y predictivo se realiza sobre una base regular. La mayoría de los gerentes de flotillas se basan en análisis de aceite para el mantenimiento predictivo, mientras que otras tecnologías de PdM (ultrasonido, vibración, infrarrojos) rara vez son considerados. Inversiones adicionales en estas tecnologías no se considera actualmente una prioridad. Hay varias aplicaciones importantes que se pueden combinar con la tecnología de ultrasonido, pero no se entienden actualmente, y definitivamente no son empleadas por la mayoría de los talleres de reparación de activos móviles. Estas aplicaciones caben en la caja de herramientas de PdM perfectamente para cualquier departamento de mantenimiento responsable de mantener una flota comercial funcionando a la perfección.
La mayoría de las tecnologías de PdM son simbióticas, es decir, que cuando se utilizan en conjunto ofrecen un panorama más completo, pero cuando se usan solas, datos vitales pueden pasarse por alto. El propósito de este artículo es educar acerca de algunas aplicaciones importantes, donde la combinación de las pruebas de ultrasonido y el análisis de aceite pueden predecir las principales fallas prematuras de motor, así como acelerar el tiempo de inspección para detectar y solucionar problemas. Este artículo también discute algunas aplicaciones secundarias que abordan cuestiones relacionadas con la seguridad de estos vehículos, la protección de la carga, y la comodidad para el operador. Esperemos, que conozca el importante papel que la tecnología de ultrasonido sirve para los gerentes de mantenimiento de flotillas y los mecánicos.
Prueba de Ultrasonido… Que es y cómo funciona?
Muchas personas en los departamentos de mantenimiento responsables de los activos fijos de las fábricas saben que la principal fuente de ondas de ultrasonido es un flujo turbulento, de fricción y descarga relacionado con problemas eléctricos. También saben que las ondas de ultrasonido son ondas de sonido vibrante de más de 20.000 Hz, que es imposible para los seres humanos escuchar sin la ayuda de la instrumentación ultrasónica especial.
Los Instrumentos de ultrasonidos detectan problemas potenciales que pueden conducir a cerrar los procesos o la fábrica. Asimismo, detectan las fuentes de desperdicio de energía y las cuestiones que inciden negativamente sobre la calidad del producto (Figura 1). Muchos problemas de las primeras etapas producen señales de ultrasonidos que se transmiten desde la fuente como ondas de presión. Los Instrumentos de ultrasonidos detectan estas ondas y las traducen en una señal audible que puede ser escuchada por el inspector, todo esto mientras se mide la señal de ultrasonido para que pueda ser comparada y tendenciada para determinar el deterioro gradual. Incluso si esto suena complicado, la verdad es que no lo es.

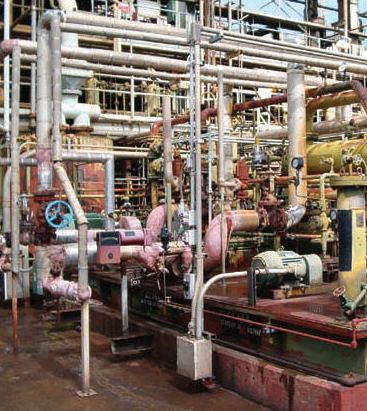
En la actualidad en las fábricas con activos fijos, hay miles de inspectores de ultrasonido capacitados trabajando que son extremadamente delicados y creativos a la hora de detectar las fuentes de ultrasonido dentro de sus procesos, y arreglar los problemas que encuentran.
Por desgracia, la demografía de inspectores de ultrasonido cualificados y capacitados, está pobremente representada en el taller de mantenimiento móvil, donde la tecnología es prácticamente desconocida. Lamentablemente, muchas aplicaciones de ahorro de costos no han sido reveladas. Si usted está trabajando en el departamento de mantenimiento y es responsable del mantenimiento de activos móviles, usted quedará gratamente sorprendido por las aplicaciones se revelan en este artículo.
Aplicando Inspecciones de Ultrasonido a Flotillas Móviles
Vamos a discutir el uso de técnicas de ultrasonido en varias aplicaciones diferentes en las flotillas móviles, incluyendo motores diesel, cilindros hidráulicos, frenos de aire, suspensiones de aire y tensión de la cabina.
Motores Diesel - Los motores de combustión interna queman combustible, independientemente de su tamaño, requieren de aire - preferiblemente aire limpio. El aire que respiramos es el mismo aire que los motores respiran. No importa dónde estamos en el planeta, el aire contiene partículas en suspensión. Algunas de estas partículas son inofensivas, pero otras representan un grave peligro. El sílice se ubica como uno de los elementos más duros en la tierra, sólo superado por el topacio, el corindón y el diamante. El sílice es muy perjudicial si llega el interior de un motor. El sílice también se ubica como uno de los elementos más abundantes en la tierra y siempre presente en la suciedad y el polvo, que es transportado por el aire en las condiciones en que operan las máquinas móviles. Por lo tanto, los motores están equipados con sistemas de filtración de alta eficacia para prevenir el sílice y otros contaminantes de llegar a la cámara de combustión (Figuras 2 y 3).
Todos los motores diesel tienen filtros primarios y secundarios instalados entre las salidas de aire de admisión y el turbocompresor (Figura 4). Cuando el motor está en funcionamiento una presión negativa se crea en el sistema de admisión de aire y cualquier orificio (pinzas sueltas, mangueras agrietadas, afinado de metal, agujeros de alfiler) en la dirección de los filtros, significa que el motor está respirando sin filtración. Esto significa que el aire lleno de sílice puede llegar a los pistones, aros, camisas y otros componentes del motor, ocasionando daños y fallas prematuras. Dependiendo de la cantidad ingerida de sílice, la vida del motor se reduce drásticamente, a veces duran sólo unos pocos días!
El Análisis de aceite se utiliza como una herramienta de predictiva que compara el contenido de metal y sílice en partes por millón (PPM) encontradas en la muestra de aceite contra los valores límite fijados de acuerdo con el fabricante del motor. El contenido de sílice aceptable es muy bajo, 15-50 ppm. Cuando una muestra contiene valores por encima del límite, es necesario encontrar rápidamente la fuente de contaminación, y el activo móvil debe ser retirado del servicio para evitar más daños costosos. Esto se suma a los costos de tiempo de inactividad y pérdida de productividad.
Encontrar las fugas requiere una inspección visual exhaustiva de todo el sistema de aire de admisión. Esto puede tomar varias horas para inspeccionar, y después de la inspección, no es raro que no se encuentre nada. La siguiente muestra de aceite seguirá mostrando niveles altos en sílice y aumento de los valores de metal de desgaste indicando que el problema de está empeorando. Como compañero de inspección visual, las pruebas de ultrasonido para encontrar las fugas ofrecerá resultados mucho más rápido, y también es útil para confirmar que la reparac4ión de las fugas se ha realizado correctamente. Los mecánicos móviles proactivos utilizan la inspección por ultrasonido después de que cualquier trabajo de servicio se completa en el sistema admisión de aire.
Existen dos métodos para encontrar los problemas en los sistemas de admisión de aire utilizando Ultrasonido:
- Inspección con la maquina encendida
- Inspección con la maquina apagada
Inspección con la maquina encendida - Utilizando este método de inspección se basa en la premisa de que cualquier flujo turbulento de una fuga potencial de ultrasonido produce ondas de presión sonora, que son, a su vez, detectadas con el detector de ultrasonidos. El flujo turbulento se produce entre dos volúmenes adyacentes cuando estos volúmenes tienen a) presión diferencial, y b) una ruta de escape. El flujo turbulento existirá en la ruta de fuga durante el tiempo que hay diferencia de presión entre los volúmenes.
Arranque el motor y dejarlo al ralentí. Con los auriculares atenuantes de ruido, ajuste la sensibilidad del aparato de ultrasonido de acuerdo a las fuentes de ultrasonido cercanas al motor. Utilizando los sensores flexibles para mayor seguridad (si tiene ese accesorio), inspeccione todo el sistema de admisión a partir del respiradero y termine en el turbocompresor. Cualquier entrada de aire produce una señal ultrasónica que suena como silbido, este sonido de rasgueo que usted conoce por una fuga de aire comprimido. Un oído entrenado tomará este sonido rápidamente, a pesar de los ruidos en competencia que pueden venir del propio motor. La capacitación adicional enseña a los inspectores de ultrasonido cómo lidiar con el ruido parásito y con los ambientes hostiles, y es altamente recomendado para los mecánicos móviles que están adoptando las pruebas de ultrasonido en simbiosis con el análisis de aceite. Técnicas conocidas como "blindaje", "cubierta", "bloqueo", y "posicionamiento" son claves importantes que ayudan a los inspectores en las zonas de alto ruido.
Inspección con la maquina apagada - El sistema de toma de aire también pueden ser inspeccionado para detectar fugas cuando el motor no está funcionando. De hecho, esto puede ser un método más conveniente porque el ruido parásito del motor es fuerte y puede interferir con la inspección.
Cuando el motor está apagado no hay diferencia de presión y en consecuencia no hay flujo turbulento. No significa que no hay un flujo turbulento de señales de ultrasonido naturales que están presentes en todos los sitios de fuga. En lugar de un flujo turbulento se pueden generar señales de ultrasonido artificiales directamente en el sistema de ventilación de aire. Esto se logra mediante un transmisor de ultrasonido, como el transmisor bi-sónico 200mW de la empresa SDT, que es un pequeño accesorio que genera una señal de 40 kHz, suficientemente potente como para llenar volúmenes pequeños. La señal de ultrasonido se puede escuchar y medirse directamente a través de las membranas que componen el sistema de ventilación de aire. Siempre que la posibilidad de ingreso de aire exista, la señal detectada por el receptor ultrasónico es mucho más fuerte. Esto se nota en los auriculares y el nivel de decibelios medidos por el instrumento.
Una gran empresa minera en el norte de Canadá recientemente compartió su experiencia de la inspección de la toma de aire en un cargador de producción marca LeTourneau. En respuesta a niveles muy altos de sílice y de hierro a partir del muestreo aceite en uno de sus cargadores (figuras 6 y 7), se hizo un intento para determinar si habían fugas en el sistema de ventilación del cargador que pudiera haber causado el polvo tan severo. Una inspección visual del sistema de ventilación no produjo ningún resultado definitivo. Luego se realizó una segunda verificación del sistema de ventilación, esta vez usando ultrasonido con un transmisor. "Encontrar la fuga fue fácil", informó la empresa minera. Un transmisor ultrasónico 200mW fue colocado en el interior del filtro de aire interno. Ambos filtros de aire fueron reemplazados y el sistema de ventilación se sello. El sistema de ventilación entero desde los filtros hasta la maquina fue probado con el receptor de ultrasonidos (ver Figura 8). Todas las ubicaciones a lo largo de la tubería de ventilación y de las articulaciones mostraron lecturas de ultrasonido de 20 a 24 dBμV, a excepción de uno. La ubicación dentro de una pinza en el lado derecho del cargador dio una lectura de 34 a 38 dBμV. Esto supone un incremento de 14 decibelios. 38 decibelios es 5 veces más alto de 24 decibelios. Esta es una fuerte indicación de viruta fina de metal combinada con la posibilidad de escapes de pequeños agujeros en o alrededor de la abrazadera. Las imágenes que se muestran en las figuras 8 y 9 indican que las lecturas de base de ultrasonido 20-24 dBμV se registraron frente al sitio de fuga, donde se observaron 34-38 dBμV.
Los mecánicos en el taller de reparación móvil, informaron de que, una vez que se descubrieron las fugas, la solución era relativamente simple. Y encontrar las fugas con la inspección de ultrasonido fue mucho más rápido que cualquier otro método utilizado anteriormente. Había una soldadura en la tubería que había sido previamente reparada. Se quito y el parche existente fue inspeccionado y vuelto a soldar. El tubo fue reinstalado en el cargador, se reemplazaron los filtros y se recomendó que la maquina regresara a su operación por un período de 12 a 24 horas. Se volvieron a tomar muestras de aceite fresco, y se analizaron los resultados en busca de problemas referentes al polvo.
El aceite del cargador fue sometido a una nueva muestra el 22 de mayo del 2009, después de aproximadamente 48 horas de funcionamiento en el campo, y los resultados se recibieron de vuelta desde el laboratorio seis días después. Todos los indicios de polvo había desaparecido de los resultados de la muestra de aceite. Como puede verse en la Figura 10 comparando las muestras antes y después, se observaron caídas importantes en los niveles de aluminio, níquel, cromo, hierro, cobre, plomo y sílice (véase la figura 11), indicando que la fuga de aire se reparo con éxito, y que efectivamente la causa era el polvo. Se sospecha que los contaminantes en las muestras iniciales eran una combinación de entrada de polvo y partículas de desgaste de los componentes del motor.
Resultados finales en ahorros
Este es un procedimiento fácil de implementar en cualquier taller de reparación móvil por el costo relativo de una buena calidad de los equipos de inspección por ultrasonido. Digo "costo relativo", porque el dinero invertido en equipos de ultrasonido y en capacitación pueden ahorrar millones a la empresa. Como ejemplo, esta gran empresa minera del norte canadiense informó de ahorro muy por encima de un millón de dólares tan sólo unos meses después de la aplicación de las pruebas de ultrasonido.
Sus números son estimaciones prorrateadas basadas en la vida del motor restante y no incluye ningún costo adicional por mano de obra. En otras palabras, el valor restante de sólo los motores después de la depreciación. El equipo fue el cargador de producción Letorneau 1850 que acabamos de mencionar y cuatro Camiones de transporte Komatsu 830E. Todos los motores son Cummins QSK60 y las cuestiones sobre el polvo fueron descubiertas y reparadas, entre mayo y noviembre del 2009 utilizando una combinación de análisis de aceite e Inspección ultrasónica. La cooperación de estas dos tecnologías predictivas contribuyeron a un ahorro de 1.147.029 dólares durante este período de tiempo. En realidad, los analistas de negocio de la empresa, calcularon una cifra mucho mayor, ya que incluyeron todos los costos posibles, tales como mano de obra, piezas, y el tiempo de inactividad, etc .., pero este ahorro de costes adicional no podía ser revelado.
Vamos a analizar ahora los camiones de transporte Komatsu 830. Para darle una idea de lo difícil que es encontrar estos escapes de aire pequeños con la inspección visual, eche un vistazo a las figuras 12 y 13.
Los dos tubos que están en contacto en la figura 12 se supone que están separados por al menos una pulgada. Sin embargo, en el campo, en realidad están en contacto, lo que causó fricciones. Veamos ahora la figura 13. Estos tubos de ventilación son de 10 "de diámetro. Una vez que el sitio de fuga se detectó con ultrasonido, se separaron con una barreta. Esto podría haber causado cientos de miles de dólares en daños en el motor más el tiempo de inactividad. La inspección de ultrasonido de los sistemas de admisión de aire es ahora una práctica estándar en esta mina canadiense, al igual que algunas otras aplicaciones interesantes.
Cilindros Hidráulicos
Los Cilindros hidráulicos (Figura 14) se utilizan en los sistemas hidráulicos móviles y fijos. Ellos proporcionan la fuerza a través de una carrera lineal. Su funcionamiento se basa en la Ley de Pascal, que establece si se aplica la presión de los líquidos confinados a continuación, los fluidos transmiten la misma presión en todas direcciones a la misma velocidad. Los Cilindros hidráulicos son una forma eficaz para multiplicar la fuerza y mover cargas pesadas.
Los sellos son uno de los componentes más importantes de los cilindros hidráulicos. Ellos crean una barrera entre la cámara de alta presión y la cámara de baja presión. Cuando se ve comprometida la integridad de los sellos, el cilindro ya no transmite toda su fuerza potencial.
Síntomas de los Problemas en los Cilindros
Un síntoma seguro de que el cilindro tiene problemas es una pérdida de poder y/o operación lenta. En casos graves, el cilindro puede frenarse incluso con cargas ligeras. Un aumento en el ruido de la bomba y en la temperatura es también un signo de fugas en los cilindros. La principal causa de fallas en el sistema hidráulico es la contaminación del fluido hidráulico. Contaminantes sólidos en el líquido, como el sílice, gastan el barril y los sellos lo que hace difícil para la bomba hidráulica mantener la presión necesaria.
Como diagnosticar el Sistema
Un método convencional para comprobar si hay fugas en los cilindros hidráulicos requiere que un operador envíe al pistón a un extremo de su carrera y dejarlo estancado en esta posición a presión (figura 15). Luego abrirá la montura en el mismo extremo del cilindro y revisará por fugas de líquido, que indicaría si el aceite hidráulico ha pasado el sello del rascador. Después de comprobar, la montura se vuelve a apretar y se repite el procedimiento en el otro extremo, y a la mitad de la carrera. Este procedimiento es muy lento y requiere que el bien este fuera de servicio durante más tiempo de lo necesario.
El ultrasonido acelera el tiempo necesario para la inspección, y en muchos casos, la inspección se realiza en el campo, evitando el costo y la demora de trasladar el equipo a la bahía de reparación. Esto tiene un beneficio adicional si la inspección revela una fuga, y la fuga puede ser reparada en el campo.
Utilizando el ultrasonido, el inspector coloca el sensor de contacto o un sensor magnético sobre el cañón cerca del pistón (ver Figura 16). El sistema está bajo presión y el sensor escanea todo el barril 360 ° mientras se escucha el sonido característico producido por una fuga cuando el líquido pasa de la cámara de alta presión a la cámara de baja presión. Este sonido podría ser realizado por pequeñas burbujas de aceite reventando en el lado sin presión de los rascadores. En el caso de grandes fugas, el sonido es más parecido a un sonido aplastante mientras el aceite es forzada a través de un pequeño orificio en el sello. El punto donde la señal es más intensa indica la violación de la integridad del sello.
Sistemas de Frenos de Aire
Los sistemas de frenos de aire que se utilizan principalmente en todo tipo de camiones, autobuses y vagones de ferrocarril (véase figura 17). Para una operación eficiente y segura, el sistema debe ser absolutamente hermético. Los fabricantes de sistemas de frenado establecen directrices para la presión, y esta presión de trabajo debe mantenerse en todas las circunstancias.
Los sistemas de frenos de aire tienen varias partes que incluyen el compresor, un secador de aire, válvulas, tanque de depósito de aire, tubos, y el sistema de frenos en sí. Todos estos componentes son susceptibles a fugas. El compresor está diseñado para funcionar cargado hasta el 25% del tiempo de funcionamiento del motor, pero las fugas de aire pueden causar que el tiempo de ejecución aumente, añadiendo costos operativos en forma de combustible y mantenimiento. Por supuesto, esto no es tan importante como el hecho de que las fugas ocasionan que el sistema de frenado puede ser un riesgo de seguridad.
Resolución de problemas del sistema de frenos
Buscar fugas en el sistema de aire comprimido en cualquier equipo móvil es fácil y rápido. De hecho, muchos fabricantes, incluyendo Volvo Trucks y Mack Trucks ya utilizan los detectores SDT170 en la línea de montaje para garantizar que no existan fugas en los sistemas de frenado. Arranque el motor y deje que el compresor trabaje hasta que la presión requerida es alcanzada en el sistema. Apague el motor, y utilizando el instrumento de ultrasonido con el sensor flexible, escanee desde el lado del compresor a los frenos en las ruedas. El silbido de una fuga será fácil de escuchar, y, porque es ultrasónico, es direccional, y, por tanto, fácil de localizar.
Sistemas de Suspensión de Aire
Los Sistemas de suspensión de aire (ver Figura 18) proporciona una marcha mucho más suave, la cual puede agregar protección de la carga que es sensible a las perturbaciones del transporte. El resorte de aire es, básicamente, un fuelle lleno de aire comprimido y trabaja con el mismo compresor que utiliza el sistema de frenado. Las Fugas en el sistema de suspensión neumática afectan la conducción suave, pero también puede basarse en el sistema de frenos, haciéndolo poco confiable, y, por lo tanto, inseguro. Por supuesto, esto se suma el riesgo de que el vehículo transportaba varias toneladas de carga. Cuando el resorte pierde su presión existe la posibilidad de pérdida de equilibrio y que pueda volcarse.
La Solución de problemas de sistemas de suspensión de aire es esencialmente el mismo procedimiento que el utilizado para los sistemas de frenado.
Hermeticidad de la cámara
La última aplicación que vamos a discutir aquí es otra igualmente importante en donde la inspección de ultrasonido es de utilidad para garantizar la hermeticidad de las cabinas y habitáculos. En los vehículos mas pequeños la hermeticidad es importante para prevenir ruidos internos de ruido del viento y fugas de agua. En los vehículos más grandes como cargadores y tractores, el mantener las partículas de polvo fuera de la cabina es una cuestión de comodidad y de salud para los operadores. En los buques y otras embarcaciones oceánicas, la hermeticidad contra el medio ambiente es vital para garantizar la seguridad de la tripulación y evitar daños a la carga.
La inspección es similar, y tan sencilla como el procedimiento utilizado para la inspección de los sistemas de ventilación de aire con el ultrasonido artificial. Coloque el generador de tono 200mW dentro de la cabina y cierre todas las ventanas, puertas y rejillas de ventilación. Utilizando el instrumento de ultrasonido y un sensor flexible, escanee los sellos en todas las ventanas y puertas. La fuente de ultrasonido artificial es lo suficientemente potente como para llenar toda la cabina, pero también es lo suficientemente potente como para transmitir directamente a través del cristal y del acero. Utilice el siguiente procedimiento para entender la diferencia entre una fuga y una no fuga.
1. Coloque el transmisor 200mW dentro de la cabina.
2. Tome una lectura de dBμV en una ventana o puerta abierta. Este es su OHV (open
hatch value, en español valor de escotilla abierta).
3. Ahora cierre las puertas y ventanas y tome una lectura de dBμV en un área donde sería imposible que hubiera una fuga (a la mitad del cristal de la puerta será suficiente). Este es el CHV (closed hatch value, valor de escotilla cerrada).
4. Ahora escanee alrededor de puertas y sellos con el sensor flexible. La lectura de referencia revoloteara alrededor de las CHV. Escucha en los auriculares y cuando usted escuche una señal más fuerte que CHV obsérvela. ¿Se parece a la de OHV? Si es así, ha encontrado una vía de fuga potencial.
En este artículo ha cubierto cuatro razones para aplicar la inspección de ultrasonido para los principales centros de mantenimiento de flotillas. Las inspecciones discutidas tuvieron un impacto positivo para la reducción de costos a través de inspecciones más rápidas en comparación con los métodos tradicionales. También ayuda en la prevención de fallas prematuras en los motores diesel que, como hemos aprendido de nuestra operación minera canadiense, ahorro más de un millón de dólares durante un período de siete meses. La inspección de ultrasonido ya comparte una relación simbiótica con las vibraciones y la inspección de infrarrojos de los activos fijos. Los ejemplos aquí citados son un excelente argumento para casar la inspección de ultrasonido y los datos del análisis de aceite para un mejor control de los motores de combustión interna
Encontrar problemas del sistema hidráulico lleva mucho tiempo. Si la inspección de ultrasonido puede aislar las fugas en los sellos, tiene sentido implementar la tecnología para ganar más tiempo de inspección y encontrar nuevos problemas más rápido.
Por último, inspeccionar cabinas de control en busca de hermeticidad, aumenta la comodidad y seguridad para los operadores. La hermeticidad de las unidades de refrigeración significa menos carga para el motor del compresor y una mejor eficiencia de combustible. La hermeticidad de las escotillas en barcos de carga la carga llegara seca al puerto en barcos más seguros.
Mientras gran progreso se ha hecho al aplicar el ultrasonido para las inspecciones de los activos fijos, hemos aprendido de este artículo que hay igualdad de victorias que pueden obtenerse de las aplicaciones en activos móviles. Al proliferar la tecnología de ultrasonido en todo el mundo, no podemos dejar de preguntarnos qué otras aplicaciones sencillas hay que ahorraran el próximo millón de dólares.
Gustavo Velásquez tiene más de 20 años de experiencia profesional trabajando en varias compañías en América Latina y Canadá, como Mobil Corporation, Saybolt Consultores, Lubrication Engineers of Canada, Battenfeld Grease Canadá, LubriSupport, y últimamente como Gerente de Cuenta para la Región de América Latina con SDT North America. Gus es un miembro de STLE y SMRP. Vive en Cobourg, Ontario con su esposa y dos hijas.
Allan Rienstra es el director general de SDT Ultrasound Systems. Él ha estado involucrado con los métodos de ultrasonido durante casi dos décadas y ha ayudado a miles de inspectores de ultrasonido a alcanzar la grandeza de la inspección a través de sus técnicas únicas de capacitación. Es coautor de dos manuales de certificación, fundador de la formación para la certificación de SDT y la guía de aplicación. Su obra aparece en revistas de mantenimiento en todo el mundo. Vive en Cobourg, Ontario, Canadá con su esposa y dos hijos. Allan puede ser alcanzado en 905-377-1313 905-377-1313 x 221 o allan@sdtnorthamerica.com