
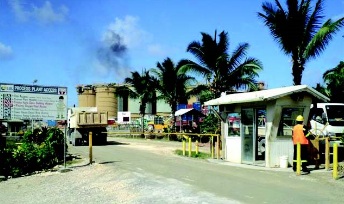
Figure 1 (top): Entrance gate to Newcrest Gold. Technical Training Center, Lihir Island.

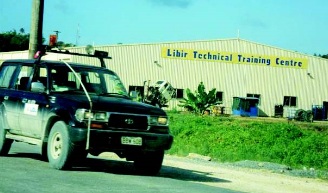
Figure 2 (left): Newcrest Gold (formerly Lihir Gold, Ltd.)
The Lihir Gold operation is located on Lihir Island, in the New Ireland Province of Papua New Guinea (PNG) (Figures 1 and 2). Gold deposits are located in an inactive volcanic crater known as the Luise Caldera on the east coast of Lihir Island. The mine produces over (800,000) ounces of gold per year. Upon arrival I met several of the Lihir Gold (now Newcrest Mining, Ltd-Lihir) technicians. Three of the key personnel were Mr. Trevor Black, Coordinator Condition Monitoring/NDT; Mr. Dominic Kalua, Field Training Officer-Maintenance; and Mr. Jimmy Romalus, Coordinator Process Plant Maintenance. All were attendees in the Ultra-Sound Technologies Level I Training Class. During theultrasound training session walk-around of the plant I was told of a poorly performing GEHO slurry pump (Figure 3). Instinctively, I used an ultrasound instrument (a CSI 7100) to listen to the cylinder walls (Figures 4A and 4B) while listening for an abnormal sound or condition that might help identify a problem. One cylinder when compared to the others sounded distinctly abnormal (see Figure 5).

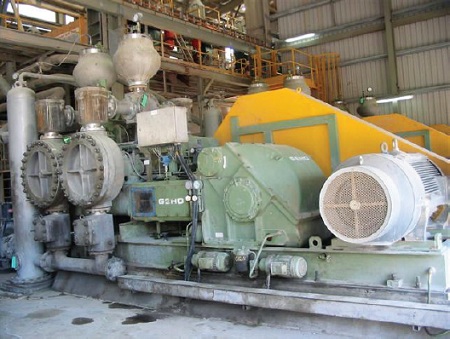
Figure 3. GEHO Pump: ZPM-800, Gold Ore Slurry. Min:62.5 cubic/hr, Norm: 176 cubic/hr, Max: 270 cubic/hr. High pressure is built from the piston moving back and forth on the eccentric flywheel, which moves the piston back and forth horizontally.
Figure 4A. Technicians using the ultrasound instrument on the external cylinder walls from beside and between the bolted diaphragm housing.
Figure 4B. A CSI 7100 being used to monitor cylinder walls of the GEHO Pump and showing a normal signature.
Figure 5. The results of utilizing a CSI 7100 ultrasonic receiver to listen to cylinder PU801 of the GEHO Pump.
I needed to know more about GEHO pumps, so I contacted Roger Collard, Chief RCM Engineer of Wyle Laboratories, who I knew had previous relevant mining experience. I believed that, together, my recent experience at Lihir and Roger's 18 years of mining experience on similar equipment could me offer a more complete view of this unique situation.
Roger explained to me that GEHO pumps of this series are powerful piston diaphragm pumps that allow slurry material to be conveyed with much lower water content. Through timing of the diaphragms and piston movement, extremely dense material can be conveyed. The design is very dependent on product density, system pressure, and temperature. Diaphragm leakage is a concern as mixing can occur. If this is the case, any or all three of the previously mentioned parameters can be affected.
Listening to each valve and diaphragm at the end of the piston stroke, a bad ring or piston problem would have a distinct signature. The trick is that the diaphragms, valves, and pistons are all in the same area, so leaking valves, leaking diaphragms, leaking rings, and broken pistons may all sound alike. Slurry passing through a good valve can sound like a leak. You have to time the component's "noise" signature with the pump timing to know if the valve is operating correctly or leaking. Monitoring for an energy change, either up or down, may indicate cavitation, leakage, or regurgitation.
Ultrasonic technology offers the ability to detect these potential failure conditions before extensive damage has occurred.
Mr. Trevor Black from Lihir explained that what we were listening to at Cylinder PU801 with the CSI 7100 ultrasound device was the sound of fluid passing into the other chamber via the damage on the roof-shaped seals worn area (Figure 6A) from chamber 3 to chamber 4. This was confirmed via the instrument panel monitoring the inlet filling times on chamber 3 and outlet times on chamber 4. A possible explanation for the phenomena is a previous chamber 3 diaphragm rupture. The slurry that entered into the chamber may not have been cleared out completely. More evidence of damage was seen in the cylinder liner (sleeve) from the 6 to 9 o'clock position of the sleeve (Figure 6B).
Figure 6B. Evidence of damage to the cylinder sleeve, seen from the 6 to 9 o'clock position of the sleeve.
Figure 7. The new SDT North America, SDT-270 instrument with intensity meter and the new U.E. Systems, Inc., UE15000 with intensity meter.
Most ultrasonic instruments today have an intensity meter and/or read in decibels, so this inspection can be accomplished using most ultrasound instruments (Figure 7). An illustration in the many uses of this technology is to measure and trend the ultrasound from the discharge and suction valves of the GEHO pumps on the autoclaves. The potential cost savings from the early detection of these valves passing (being able to plan and prepare) is as follows:
Approximately 5 hours reduction in turnaround time @ $7k/hour deferred production + a valve body @ $10,400 = $45,500. The average ultrasound instrument in the marketplace weighs roughly 2 pounds. That's approximately $41k in gold. Most plants can easily show a return-on-investment of $41k or more just in air and steam.
Roger Collard, CMRP, has 20 years of experience based in reliability centered maintenance. His background is strongly suited in manufacturing, heavey industrial applications, and mining, with a focus on stationary and mobile equipment. Roger Collard is the Chief RCM Engineer at Wyle Laboratory (Jacksonville, FL). He graduated from the University of Utah with a Bachelor of Science degree in Mining Engineering.
Jim Hall is the president of Ultra-Sound Technologies (UST), a "vendor-neautral" company providing on-site predictive maintenance consultation and training. UST provides Associate Level, Level I, and Level II Airborne Ultrasound Certification. Jim is also the author of Ultrasonic War Stories, a free bi-weekly newsletter. www.Ultra-SoundTech.com