PolyOne Corporation
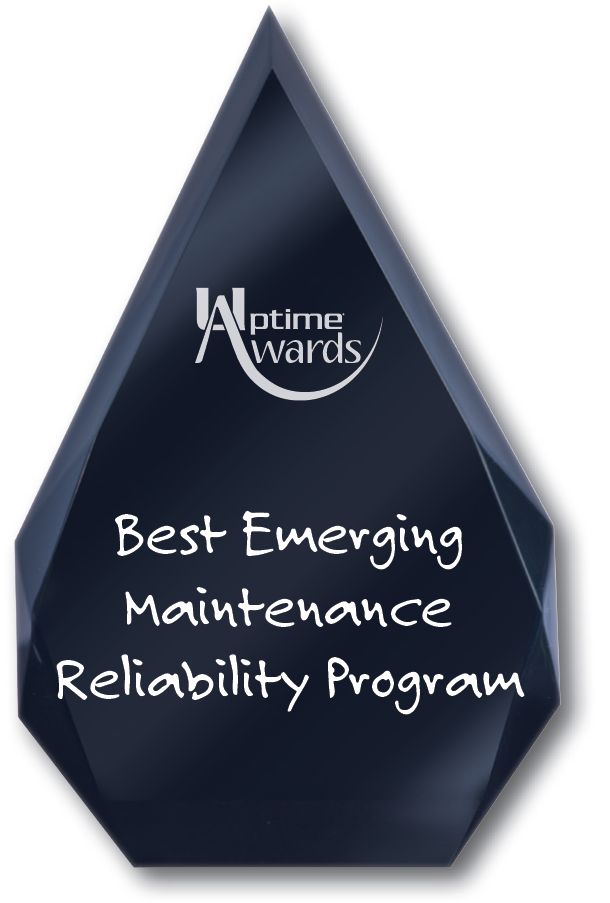

A strong business case was developed with executive leadership engagement that facilitated buy-in throughout our organization, which at the time consisted of 46 sites. Through extensive benchmarking and utilization of Lean Six Sigma skills and resources, we identified performance gaps and developed an implementation strategy to address them. The rollout plan, known as the "playbook," was in the form of waves, where a group of sites were brought together for one week of training and then returned back to begin the transformation at their respective locations. Sites took ownership and responsibility for their implementation plan and were supported by corporate to ensure consistency and speed of execution.
In 2013, PolyOne added over 30 additional sites through a series of acquisitions. With the PRP wave implementation strategy and related action plan, we have been able to quickly incorporate these new locations. We now have 55 sites implemented with three more waves planned within the next year that will result in the complete integration of our organization.
LOOP LLC
Since 2011, LOOP has created and followed a new vision of becoming "Market Driven and Operationally Excellent." After developing related strategies and tactical objectives, we've determined the two go hand in hand. The uptime or availability of assets is certainly one component of our business that touches both aspects of our vision. Our related, proactive asset and work management programs have changed our culture through the implementation of reliability centered maintenance best practices. Our Oracle OWAM CMMS system went live in 1999, and predictive technologies and condition-based monitoring initiatives have been phased in and enhanced since then.
The results have been rewarding, as we achieved 99.75 percent uptime on our main oil line assets in 2013 and have exceeded 98 percent for over five years. In 2013, we realized a four year low in ad hoc repair cost, which and are trending down in 2014. Less reactive repair work has allowed an increased focus on proactive work which has facilitated a work, order backlog reduction to four weeks for both onshore and offshore maintenance crews. Results are proving to be sustainable.
Work management guidance is documented and implemented through LOOP's Maintenance Policies and Procedures Manual. This manual includes high level and detailed roles and responsibilities of the organization, as well as instructions for our maintenance reliability processes. This guidance document also covers the regulatory requirements and details of our facility management of change process.
Maintenance planners & schedulers plan 100 percent of available maintenance manhours. Weekly and daily schedules are created with stakeholder input on priority, then distributed for review and execution. LOOP's preventive maintenance procedures address asset failure modes and defect detection. They provide guidance to the technicians for ensuring desired outcomes and repeatability. The reliability group is responsible for the execution of the predictive maintenance program. LOOP utilizes thermography, vibration, ultra-sound, oil analysis, PdMA electric motor testing and partial discharge among other technologies. KPIs and metrics are used for monitoring and managing asset health.
Our operator care program consists of a detailed operator checklist, which field operators use to note the device location, actual versus expected readings and a plan of action if expectations are not in tolerance.
LOOP stores some critical spare components in on-site warehouse facilities, and outsources the balance of off-site, climate controlled storage.
These proactive processes have assisted LOOP in becoming successful in our work and asset management programs. With an embedded culture and focus on "Getting it Right" and a passion for "Continuous Improvement," LOOP continues its journey towards operational excellence.
Metropolitan Sewer District of Greater Cincinnati
With this in mind, MSDGC built a two-tiered ACM program consisting of a centralized predictive maintenance (PdM) team with sophisticated tools and decentralized teams with affordable technologies. A PdM vendor and a subject matter expert provided training and support to get the program up and running.
The centralized ACM team employs ACM hardware and computer software for vibration, IR, ultrasound and MCA\MCE that is fully functional and capable of detailed diagnostic analysis leading to accurate identification of defects, affected parts and evolving conditions. This allows more precise repair planning which, in turn, reduces lifecycle repair costs, decreases downtime for operations and shortens active repair time for maintenance, and ultimately minimizes required capital investments by deferring expansion projects by increasing asset useful life. ACM team members are trained and certified to collection data and perform advanced. This capability provides MSDGC WWT with the ability to anticipate critical repairs with a high level of confidence, minimizing expensive plant outages or permit violations. This allows the scheduling and completion of economically efficient repairs at times determined by personnel - not the equipment.
The decentralized portion of the ACM program employs maintenance crew members at WWT plants equipped with low cost, easy-to-learn and easy-to-use vibration, ultrasonic and infrared thermography instruments. These instruments have proven useful in a wide variety of applications in confirming the presence or absence of defects and are relied upon to quickly confirm whether or not a repair has been completed satisfactorily, allowing for timely return of equipment to service.
The ACM program is sustained through a five year master plan that establishes the training, communication, budgets and processes used by the two-tiered approach. The plan is a living document used to sustain performance throughout each fiscal year and make further progress using an annual auditing/planning exercise. One key communication item contained in the plan, the Find of the Week email, supports a culture of proactive effort and focus on value by sharing maintenance successes and cost avoidance on a monthly basis. The ACM program also tracks and communicates the overall return on investment of asset condition monitoring activities. To date, MSDGC has seen a total cost avoidance of $961,131. This significant savings provides a compelling business case to upper management for continued program support.
In two years, MSDGC has moved from external ACM services to an effective internal ACM program that delivers results. With the two-tiered approach, a sustainable master planning process and consistent demonstration of added value, the ACM program is a key element of MSDGC's success and an opportunity to continue achieving increased benefits in the future.
Hibbing Taconite Commpany: Managed by Cliffs
The reliability engineering department at Hibbing Taconite Company has always maintained the vision that strong PM and PdM programs minimize environmental and economic risk and protect the safety of our workforce. This emphasis formed its roots in the lubrication program. The goal of the lubrication program has always been to keep our lubricants clean, cool, and dry. Embedded into this philosophy is that well-maintained lubricants, along with well-maintained machines, allow the lubricant to stay in the assets until the lubricant has reached its maximum use. To extend the life of lubricants, Hibbing Taconite has switched many of the mineral oil based lubricants to synthetic oil based lubricants. Minimizing the amount of lubricant handling from storage to machine to disposal minimizes the risk of spills and exposure to the environment. To minimize costs of synthetic lubricants, many of the synthetic lubricants are reprocessed and repurchased at a reduced price. Another intended benefit of switching from mineral oil to synthetic oil in applications was the lubricant's ability to decrease the amount of energy consumed to move the machines. This, in turn, results in reducing the carbon footprint of the site.
Economic return has been harvested from these efforts by our ability to keep assets in production for longer intervals, decreasing labor hours by extending preventive maintenance intervals, and decreasing overall energy consumption.
Environmental stewardship is not just a buzz word at Hibbing Taconite; it is a means to the future of the mine, a core value of Cliffs Natural Resources, and a way of life.
Marathon Oil Corporation
From the Alba Field, condensate and natural gas are extracted from the offshore platforms and sent to the onshore gas plant for processing into various products, including propane and butane. In addition to the hydrocarbon production and extraction facilities, the industrial complex includes terminals and export facilities for liquid hydrocarbon products. It also includes a liquefied petroleum gas (LPG) plant, a methanol production facility and a liquefied natural gas (LNG) production facility.
Marathon established the Alba exploration and production area in early 2002. When the company entered Equatorial Guinea in 2002, we took a long-term view of our investment. Our intent was not only to develop the country's oil and gas resources, but to develop its people resources, as well. Today, we work with local communities, government ministries, non-governmental organizations (NGOs) and other stakeholders to address critical social issues in Equatorial Guinea. Our efforts are focused on strengthening transparency, national capacity, workforce development, public health and formal education. We have initiated and participated in social responsibility initiatives addressing critical health, social, education and other issues in Equatorial Guinea. Some of these programs include:
- Bioko Island Malaria Control Project (BIMCP), an innovative and successful approach to eradicating malaria.
- Education, training and development of Equatoguineans to work in our facilities.
- Build new and refurbished school and clinic facilities for local communities.
- Provide scholarships for high-potential Equatoguinean nationals.
- Support Equatorial Guinea's participation in the Extractive Industries Transparency Initiative (EITI), an international organization which assesses levels of transparency around countries' oil, gas and mineral resources.