The rigid or solid coupling makes taking meaningful alignment measurements virtually impossible. When this coupling is left connected (and tightened), misalignment cannot be measured conventionally (by rotating both coupled shafts), because no relative movement between the shafts is allowed to occur, as would be the case with a flexible coupling. Instead, the solid coupling makes a rigid connection between the shafts, resulting in deflection of the shafts if misalignment exists. Angular misalignment between the centerlines of rotation is often evidenced by excessive vibration and wear at the first guide bearing of the pump shaft. If the coupling is completely disconnected, the pump shaft settles on the bottom of the pump pit and may be impossible to turn, even if (as is done occasionally) it rests on a specially fitted conical seat to assist in controlling pump shaft play at the bottom of the shaft. How to overcome these difficulties and properly measure, as well as correct, the misalignment?
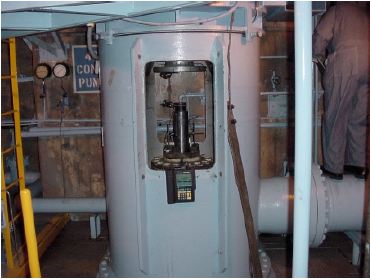
Figure 1
Traditionally, this is done with dial indicators. However, this tedious process takes much time, and is thereby very costly. One key concern is that the shimming corrections for angularity that are to be performed at the motor flange must not result in changing the axial position of the pump shaft; in other words, if all positive shimming is done, the pump shaft may be lifted off of its conical seat at the bottom of the pump pit and impose an excessive axial load on the motor's bearings. Ideally, the shimming corrections should not result in any axial movement of the shafts while still accomplishing the alignment. The whole process can be greatly sped up with the use of a good laser shaft alignment system.
The laser system must be able to supply corrections that eliminate this undesirable axial movement. Additionally, it must, at a minimum, be able to take readings uncoupled, and offer range extension for severe misalignment. One such system is Prueftechnik's ROTALIGN® PRO, which was found to be ideal for this application. The following procedure illustrates how this tool was used to accomplish the task and help the plant save nearly a day of unscheduled downtime.
First, the shafts were uncoupled, and the pump shaft allowed to rest on the bottom of the pump pit. Next, the pump shaft was centered in the stuffing box by monitoring radial travel with the ROTALIGN® PRO's actual coordinate values function; however this can also be done using dial indicators, as follows: Install two dial indicators radially against the top of the pump shaft, at ninety degrees to each other, let's say at 3 and 6 o'clock.
Now monitor shaft movement as follows: First, push the pump shaft all the way in one direction by tightening the adjustment screw on one side while backing off the screw on the opposite side (let's say you go from 12 to 6 o'clock.) Now zero the indicator in that position and move the shaft back towards 12 o'clock by the fullest extent of its travel range. Note the indicator reading in this position. Next, bring the shaft back toward 6 o'clock by one half of the indicated amount. Repeat this procedure for the 3 to 9 o'clock direction. The pump shaft should now be centered in the stuffing box and in its guide bearings. The process with ROTALIGN® PRO is identical, except that the adjustment is monitored by observing beam movement in the coordinate display screen. Now the shaft alignment measurement procedure can begin.
Since the pump shaft can not be turned when uncoupled and resting on the bottom, the laser readings were taken using the ‘Static' measurement mode, which is a process that permits a reading to be taken in any cardinal or subcardinal position. Additionally, this mode disables the internal automatic inclinometer, which is necessary in a vertical shaft orientation, as the inclinometer is gravity operated. The laser and receiver components are rotated separately. Since the motor shaft can be rotated freely, the laser emitter was installed on this shaft. This was done by attaching a magnetic bracket with offset support posts to the face of the rigid motor coupling, as shown in Figure 2
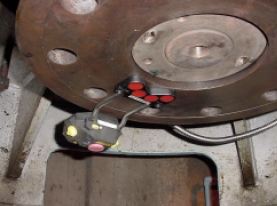
Figure2
The receiver is to be mounted on the pump shaft, normally using a special magnetic sliding bracket, since the pump shaft cannot be turned. However, in this case a non-magnetic shaft prevented this, so the standard chain bracket was used, as shown in Figure 3. Care was taken not to hurt the threads on the shaft. The laser beam was adjusted and an initial reading was taken.
Figure 3
Next, the motor shaft with laser emitter was rotated to a new position, the receiver bracket was rotated to the same position, and another reading was taken. This sequence was repeated until eight readings were taken. Three readings are sufficient to obtain results, however, the more the better. Alignment results were now obtained and the entire measurement process was repeated to obtain a second set of results. This is done to establish repeatability. The results can be averaged together if desired, as shown at the bottom of the measurement table in Figure 4. In this case, three sets of readings were averaged together (as indicated by the checkmarks in the first three lines of the measure table.)
Figure 4
Repeatability was found to be very good, and angularity was found to be out of tolerance in the 3 to 9 o'clock direction. This meant that the motor flange would have to be shimmed at the hold-down bolts. A graphical representation, to scale, of the alignment condition was also provided by the ROTALIGN® PRO, as shown in Figure 5.
Figure 5
The "smiling" or "sad" faces indicate whether the displayed alignment condition fell within tolerances or not, for the RPM involved. The ideal shimming solution for the motor flange is one where half of the corrections are positive and half of them are negative, so as to avoid the undesirable axial movement of the pump shaft discussed earlier. This ideal solution was provided by the ROTALIGN® PRO, which additionally possesses a capability to supply all positive or negative flange-shimming solutions, as well as minimized shimming solutions. The results are shown in Figure 6:
Figure 6
In addition, the exact flange bolt-pattern, flange shape and dimensions were configured, as shown in Figure 7. This capability is believed to be unique to the ROTALIGN® PRO.
Figure 7
Once the shimming was completed, alignment readings were retaken to confirm that the angularity was now within tolerance. The Measure Table in Figure 4 presents a documentary history of the events as they ocurred in this alignment job. The fourth line in the table shows the measured alignment result after the shimming corrections were carried out to correct the angularity. It can be seen that angularity was now excellent but that an offset correction was still necessary in the 3 to 9 o'clock direction. If offset misalignment between the shafts is out of tolerance, corrections are performed by pushing the motor laterally with jackscrews. This movement can be monitored using the ROTALIGN® PRO's Move function, or with dial indicators positioned radially against the motor flange. The fifth line shows the results of the move that was performed using the ROTALIGN® PRO's Move function.
Lastly, a final set of readings was taken to confirm the results of the move and document the ‘as left' alignment condition.
The motor was quickly and successfully aligned, attaining a final alignment result that fell within the excellent tolerance standard for the speed of rotation involved, as shown in the sixth line of the Measure Table in Figure 4, and by the results graph in Figure 8:
Figure 8
The entire job file was then saved to a PC using ROTALIGN® PRO COMMANDER software (from which most of the illustrations in this report were obtained), and a color report was printed for the record.
ROTALIGN® is a registered trademark of Prueftechnik AG, Germany.
By Alan Luedeking, Ludeca, Inc., Miami, FL USA