La termografía Infrarroja (IR) ha demostrado ser una herramienta valiosa para el mantenimiento predictivo y un sistema de monitoreo de procesos para muchas industrias - incluso en tiempos económicos difíciles.
La termografía infrarroja es la producción de imágenes infrarrojas sin contacto o calor de las cuales se pueden hacer mediciones de temperatura. Al detectar anomalías, a menudo invisibles a simple vista, la termografía permite acciones correctivas que deben tomarse antes de que ocurran fracasos costosos en los sistemas. Los Sistemas portátiles infrarrojos escanean los equipos y las estructuras, a continuación, convierten instantáneamente las imágenes térmicas de imágenes visibles para el análisis cuantitativo de la temperatura.
La termografía infrarroja está siendo utilizado por los fabricantes para el mantenimiento predictivo en una amplia gama de aplicaciones, incluyendo sistemas mecánicos, sistemas eléctricos, de construcción y diagnóstico - por lo que es una inversión inteligente por su versatilidad. Los sistemas mecánicos típicos monitoreados en un programa infrarrojo de mantenimiento predictivo incluye: rodamientos, motores, bombas, compresores y bandas transportadoras. Para aplicaciones eléctricas, la termografía de infrarrojos puede detectar conexiones flojas, corrosión, y desbalance de carga.
Los fabricantes están viendo favorables retornos de la inversión con los programas de termografía infrarroja ya que la tecnología les permite tomar medidas correctivas antes de que ocurran problemas - con el consiguiente ahorro de dinero y otros recursos. Los Tipos de ahorro incluyen: una reducción del inventario PM porque los problemas se detectan a tiempo, el ahorro de mano de obra mediante la adopción de medidas correctivas inmediatas, ahorro de energía - tanto de asegurarse de que el equipo está funcionando de manera óptima, y sellando las fugas del edificio, disminución de tiempo de inactividad, aumento de la producción, reducción de desperdicios, garantía de calidad durante el proceso a través de control de procesos en tiempo real, y mucho más. Este artículo proporciona ejemplos de cómo los programas de IR ahorran dinero, y se justifican por su retorno de la inversión.
Economia de las Inspecciones IR
Durante una recesión económica, una reacción automática en muchas empresas es reducir los gastos en general. Cuando se trata de las actividades de mantenimiento predictivo/preventivo (PPM), la filosofía puede ser: "Hemos reducido la producción, por lo que el equipo se está utilizando menos, y podemos hacer recortes en el PPM." Esta es una lógica cuestionable en general, pero especialmente en el caso de las inspecciones infrarrojas, cuando una recuperación inmediata es posible a partir de un mayor uso de la tecnología. Aunque las inspecciones de infrarrojos no han sido parte de una programa de PPM, la inversión en una cámara de infrarrojos puede proporcionar un ROI (retorno de la Inversion) casi instantáneo.
El PPM es como una póliza de seguros y las compañías de seguros no son conocidas por otorgar dinero innecesario. Una de estas compañías, CNA Seguros, ha hecho parte de su negocio el ahorrarle a sus clientes (y a ellos mismos) mucho dinero haciendo inspecciones IR como una parte integral de su servicios1. CNA lleva a cabo extensos análisis económico de los ahorros que se pueden obtener de esta actividad. Algunos de sus estimados de pérdidas/ahorro del 2008 aparecen en la Tabla 1.
La adopción de medidas correctivas antes de producirse fallos, ahorra dinero en muchas otras maneras. Estos incluyen:
- Reducción del inventario de piezas de mantenimiento
- Ahorro de Mano de obra al evitar fallas serias en los equipos
- Ahorro de energía mediante la optimización de la operación del equipo, y sellar las fugas del edificio
- Ahorro de tiempo de inactividad reducido (es decir, aumento de la producción)
- Reducción de residuos y desechos de piezas mediante la mejora de la operación del equipo
- Aumento de la calidad y/o la producción mediante el control de procesos en tiempo real
- Más seguridad en las condiciones de trabajo (es decir, la reducción de lesiones a personal de mantenimiento y de operaciones)
Ejemplo de un conmutador en una Fábrica de Químicos
Un escaneo IR en un conmutador en una planta química descubrió una alta temperatura en la superficie de la conexión en la Fase-A de un circuito compresor de aire (Figura 1, vista superior). Esta temperatura era de 215 ° C más caliente que la temperatura máxima de los alrededores. Según los criterios de la CNA, el termógrafo identifico esto como un fallo crítico. Si esta falla se hubiera traducido en un evento de arco eléctrico, o incluso "sólo" hubiera iniciado un incendio que destruyera el conmutador de distribución, la instalación podría haber perdido el 100% de sus operaciones por una semana. Que se estimó en un valor aproximado de $ 1 millón, además de decenas de miles de dólares en costos de reparación directa. Incluso sin un acontecimiento catastrófico, la mala conexión estaba costando dinero a la compañía en el consumo excesivo de energía por cada minuto de funcionamiento.

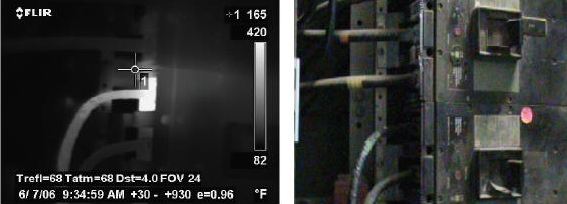
Mientras que sobre el tema del arco eléctrico, hay que señalar que estos eventos con bastante frecuencia pueden tener resultados catastróficos. Cada año, los eventos de arco en los EEUU, causan daños por millones de dólares al equipo, lesiones horribles, y muertes. Cuando los circuitos eléctricos se abren debido a un sobrecalentamiento, la corriente que fluye a través de la cámara de aire resultante forma un plasma de arco eléctrico (gas altamente ionizado). Esto puede resultar en una llamarada brillante, un calor tremendo, una explosión de alta presión, metal vaporizado, y metralla que viaja a más de 1,000 kilómetros por hora. La fuerza del arco depende de la cantidad de energía eléctrica disponible en el circuito que alimenta. No es raro que la temperatura del arco sea superior a 19.000 ° C y la presión de la explosión supere 3000psi.
Reparación de bajo costo de un Sistema Hidráulico
Los sistemas hidráulicos son otro ejemplo de equipo que normalmente se calienta a temperaturas excesivamente altas antes de la falla. Este fue el caso en una línea de transferencia en un fabricante de motores diesel (Figura 2).
Se llamó varias veces a los electricistas por las fallas de alta temperatura de la línea de bloque de cilindros en el sistema hidráulico. Todas las presiones y los flujos se encontraban dentro de las especificaciones. Un equipo de mantenimiento predictivo comprobó la temperatura con una cámara de infrarrojos y descubrió que la unidad motriz estaba operando cerca de los 47 ° C de establecimiento de falla, como se muestra en la Figura 2 (vista superior).
Análisis posteriores revelaron que el sistema hidráulico fue ligeramente inferior al permitido para esta aplicación en particular. Posteriormente, otra estación de calibre había sido añadido a la máquina, lo que aumentó la carga del sistema. Cuando la temperatura ambiente fuera lo suficientemente alta durante el verano, las fallas por alta temperatura se producirían.
Si bien esta es una situación bastante simple, los costos de la solución del problema puede ir desde el más económico a los caros, dependiendo de las circunstancias. Para convertir un sistema hidráulico que funciona bien 10 meses del año es caro.
Por lo tanto, la compra de una nueva unidad de enfriamiento para el sistema existente era una necesidad. Un termógrafo capacitado en el equipo de mantenimiento se le ocurrió una solución económica simple e ingeniosa de bajo costo. El termógrafo recordó una de las leyes de la termodinámica que se enseña en el nivel I de termografía, es decir:
El problema era que más energía se almacena en el sistema, indica una temperatura más alta que se quiere obtener. Así que si la tasa de producción de energía del sistema se podría mejorar, entonces la temperatura bajaba. Esto, básicamente, ascendió al aumentar la transferencia de calor desde el objeto. Una de las maneras más fáciles y más rentables de hacer esto es mediante el aumento de la emisividad de la superficie de un objeto. Con simplemente pintar la unidad de potencia hidráulica y todas sus tuberías de color blanco, la pintura aumenta la emisividad, permitiendo que el calor se disipe mejor, en lugar de estar atrapado en su interior. Por el costo de unas latas de pintura en aerosol, la temperatura del sistema se redujo en alrededor de 12 ° C. Esto fue suficiente para evitar las costosas alternativas, y siempre un buen retorno de la inversión para su cámara de infrarrojos.
Solución de problemas de líneas condensadas y vapor
Además de los componentes eléctricos obvios, las centrales de generación de energía tienen una gran cantidad de equipo de qué preocuparse. Una de estas estaciones en el suroeste de EE.UU. comenzó a notar síntomas preocupantes en uno de sus generadores de vapor de turbina. La primera indicación fue una disminución de la carga eléctrica. Las válvulas de control se abrieron más de lo normal, y se produjo un aumento en el flujo de vapor para generar la misma carga que antes de que se observara el problema. Junto con estos problemas, se puso de manifiesto que con el aumento del flujo, todas las presiones de la turbina también aumentaron, incluyendo la contrapresión del condensador.
Como un primer paso para solucionar el problema, se realizo una inspección termográfica infrarroja de las tuberías de cruce y dos lados del condensador, y posteriormente se analizo. La figura 3 contiene tres termogramas con un patrón anormal de calor en las partes del condensador de la turbina. Todas las indicaciones, medidas, y las imágenes de infrarrojos señalaron una violación de vapor en la región inferior de la baja presión (LP) de la turbina. Debido a que este problema podría provocar graves daños, la unidad fue puesta fuera de servicio para efectuar las inspecciones y reparaciones.
El problema detectado fue que una junta de expansión de la extracción # 3, a un calentador de agua de alimentación había fallado en la turbina LP, causando que el vapor invadiera las paredes del condensador, el cuello y las tuberías adyacentes. La junta de expansión fallida arrojaron metralla en todo el cuello del condensador que marcó otros tubos y componentes. Las piezas sueltas de metal y un gran volumen de vapor de agua a 260 ° C, en un recipiente que normalmente opera a 43 ° C, podría haber causado un grave evento en caso de ocurrir. La metralla de la junta de expansión, también podrían haberse presentado en el tubo del condensador y causar fallas inmediatamente, o en el futuro, debido a la vibración y la abrasión constante de las piezas de metal contra los tubos.
Posteriormente, todas las juntas afectadas por el fallo de la articulación de extracción # 3 fueron remplazadas en un esfuerzo por evitar cualquier otra falla. El personal de mantenimiento señaló que había tomado imágenes infrarrojas cuando la turbina se instaló originalmente, esto habría proporcionado datos de referencia para escaneos posteriores IR. Las imágenes de referencia permiten la solución de problemas con mayor celeridad y ayudan a los problemas in situ antes de que sean más severos.
Así, la intervención temprana reduce al mínimo los daños a los equipos que pueden costar millones de dólares para reemplazar o reparar. Una lección importante aquí es que los escaneos IR para establecer los parámetros de referencia IR son una mejora tremenda al ROI de la cámara de infrarrojos.
La Termografía IR complementa el diagnostico mecánico
Muchas empresas sólo escanean sus equipos eléctricos con cámaras de infrarrojos, porque tienen otras tecnologías para la prueba de motor y otras máquinas de rotación. Sin embargo, mediante imágenes infrarrojas de los componentes mecánicos, mejora el retorno de la inversión de la cámara IR mediante la capitalización de una de las ventajas de la termografía. Rápidamente se puede detectar diferencias de temperatura en el equipo mecánico a través de las lecturas de temperatura no-destructiva, sin contacto (Figura 4). Usando cámaras portátiles infrarrojas, la termografía es un método muy rápido y eficiente para escanear muchas piezas de equipo rápidamente, en busca de anomalías térmicas. Con registros de referencia de escaneos, el tendencionar el análisis de motores y de los cojinetes, proporciona una alerta prematura de los problemas inminentes.
Si bien la termografía no siempre apunta a la causa raíz de un problema, le permite saber de que existe uno. Por lo tanto, se complementa con el ultrasonido, y las herramientas de vibración y de análisis de circuitos eléctricos. Se trata de un potente arsenal en manos de los técnicos competentes. El uso inteligente de estas herramientas tiene un efecto sinérgico sobre el retorno de la inversión en todos sus equipos de diagnóstico PPM.
Justificando el Costo
Si usted no está utilizando la termografía de infrarrojos en sus operaciones de PPM, la parte más difícil de iniciar un programa es justificar el costo de la cámara, el software y el entrenamiento para hacer las inspecciones infrarrojas. Naturalmente, la administración desea una idea del retorno de la inversión del programa. La recopilación de datos para proporcionar una estimación razonable puede llevar mucho tiempo, pero sabiendo dónde mirar puede ayudar a acortar el proceso. Comience por buscar en Internet ejemplos de casos de negocio de otras compañías.
Internamente, utilice el CMMS de su compañía, el cual rastrea el mantenimiento de inventarios, órdenes de trabajo, compras, etc. Busque información sobre fallos de los equipos, las causas de los fracasos, y el costo de las reparaciones efectuadas. Si tienes la suerte de tener acceso a esta información, ordene todos los fallos de los equipos durante un año en equipos mecánicos y eléctricos. Tan sólo los datos sobre el material eléctrico a menudo pueden justificar el costo de un nuevo programa de infrarrojos.
Por ejemplo, totalice el costo de todos los equipos y materiales eléctricos. No incluye el costo de las reparaciones, sino sólo el costo del equipo de reemplazo. Utilice el costo del equipo de reposición más bajo cuando hay una serie de costos. No considere los costos por mano de obra para reemplazar el equipo averiado ya que esto compensa el costo de mano de obra por repararlo (por ejemplo, las conexiones eléctricas sueltas o malas en el equipo antes de que falle). Esta categoría de antes de la reparación, generalmente, implica "desmontar, limpiar y volver a apretar según las especificaciones del fabricante", que son actividades relativamente baratas. En promedio, alrededor de dos tercios de los fallos de los equipos eléctricos se deben a conexiones flojas o inadecuadas que son fácilmente identificables con escaneos infrarrojos. Por lo tanto, multiplique el total de los costos eléctricos reemplazo del equipo por dos tercios, porque usted está encontrando esas malas conexiones antes de que los componentes se quemen. Es posible que desee este factor un poco abajo si se asume que algunas de esas malas conexiones no se encontrarán.
Ahora pregúntese: ¿Es la eliminación de costos totales suficiente para justificar un programa de infrarrojos? Teniendo en cuenta este eliminación de costos, un programa de infrarrojos se amortizará en 6 meses, 1 año o 2 años? (La pregunta ROI). Este cálculo es muy conservador, y lo más importante, puede ser verificado por el contable de la empresa. Recuerde, esto es sólo una pequeña parte de la imagen del retorno de la inversión. Ni siquiera hemos considerado la pérdida de producción, tiempo de inactividad, la seguridad o los costos de equipo mecánico. Aunque estas otras piezas del rompecabezas del retorno de la inversión suelen ser mucho mayores en número y totales, también son menos cuantificables, por lo que son una fuente potencial de discordia.
Si su empresa no hace un seguimiento de fallos de los equipos y los costos de reemplazo, o si necesita otros números de reducción de costos, vea que rutinas de mantenimiento preventivo implementa actualmente su empresa. Dos procedimientos de mantenimiento preventivo a mirar de cerca son:
- Apriete todas las conexiones eléctricas una vez al año (muchos problemas de conexión eléctrica son causados por este método).
- Periódicamente renovación de los equipos antes de que fallen, incluso si no tienen un problema (supuestamente para evitar interrupciones no planificadas).
Un programa de escaneo de infrarrojos puede eliminar o reducir el costo de estas actividades PPM preventivas.
Incluso si su empresa trabaja con el equipo hasta que falle, los escaneos de IR pueden proporcionar una alerta sobre qué equipo tiene un problema o está a punto de fallar, permitiendo a la compañía tener un inventario de piezas de repuesto para cuando se necesitan.
Para los programas establecidos de infrarrojos, asegúrese de llevar un registro de reducción de costos y otros beneficios de costo del programa. Estos deben ser reportados a la administración por lo menos una vez al año, preferiblemente antes de las actividades de presupuestarias. Los ahorros obtenidos a través del programa, proporcionarán un recuento de su retorno de la inversión. Estos números son importantes en cualquier momento, pero especialmente durante una recesión de los negocios.
David Doerhoff es gerente de ventas de FLIR Systems, líder mundial en diseño y manufactura de cámaras infrarrojas, el Sr Doerhoff puede ser contactado en david.doerhoff@flir.com o al teléfono 816-884-3021.
Referencias
- Gray, Thomas A., “CNA Saves its Clients More Than $80 Million over 3 Years of IR Surveys from March 2005 through 2008”, in Infra Mation 2008 Proceedings, Volume 9 (ITC 126 A 2008-05-14); conference of Nov. 3-7, 2008, Reno, NV, available at http://www.flir.com/WorkArea/showcontent.aspx?id=23398.
- Hays, Deborah, “In Manufacturing, Little Things Mean a Lot”, in InfraMation 2008 Proceedings, Volume 9 (ITC 126 A 2008-05- 14); conference of Nov. 3-7, 2008, Reno, NV, available at http://www.flir.com/WorkArea/show content.aspx?id=23400.