Does Merriam-Webster’s definition of revolution as “a sudden, radical, or complete change” apply to Industry 4.0 – the industrial revolution of the 21st century? If so, consider that in every revolution, new elites emerge at the expense of old power centers. The position that the expected long-term benefits of Maintenance 4.0 (e.g., environment, efficiencies, etc.) will outweigh the costs is deceptively simple. This article explores whether the benefits of Maintenance 4.0 will be disproportionately spread and how this will impact the industrial sector.
What Is Maintenance 4.0?
Maintenance 4.0 is a subset of Industry 4.0 that covers maintenance reliability activities. These include preventive and predictive maintenance, machinery repairs and inspections. The default scenario is run to failure, whereby industrial equipment is used until it breaks down. During the period of downtime, repairs are scheduled and tools and parts are ordered. Searching for the root cause while production has unexpectedly halted adds additional pressure to repair crews and increases the likelihood of error or short-term fixes.
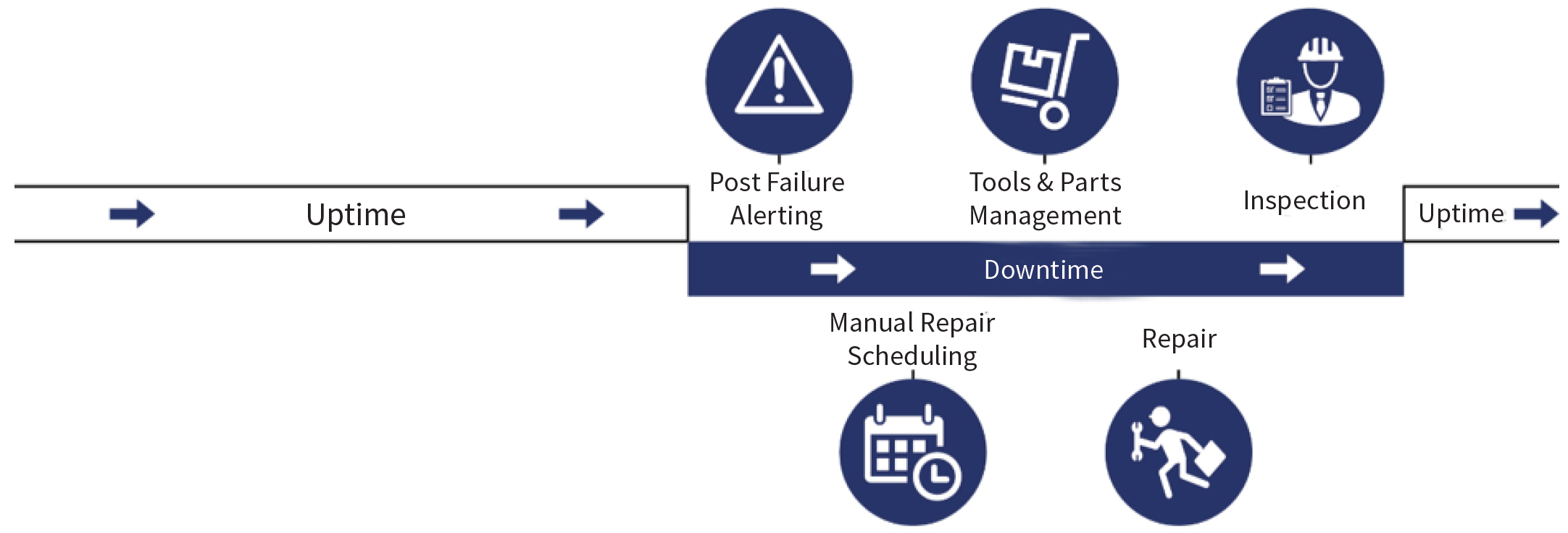

Figure 1: Reactive maintenance (Industry 3.0) Source: Presenso
If big data is the oil of the Maintenance 4.0 revolution, then machine learning is the accelerant. With Maintenance 4.0, machine learning algorithms are applied to the data that is generated from sensors embedded within industrial plants. These algorithms are trained to detect anomalous patterns and then identify threats of evolving failure. The seismic difference between run to failure and machine learning predictive maintenance is the advanced warnings machine learning provides to repair technicians. Tasks ranging from understanding the problem to finding the best skilled repair crews are executed before a shutdown occurs. The result? A significant reduction in unscheduled downtime and incremental revenue from increased yield rates.
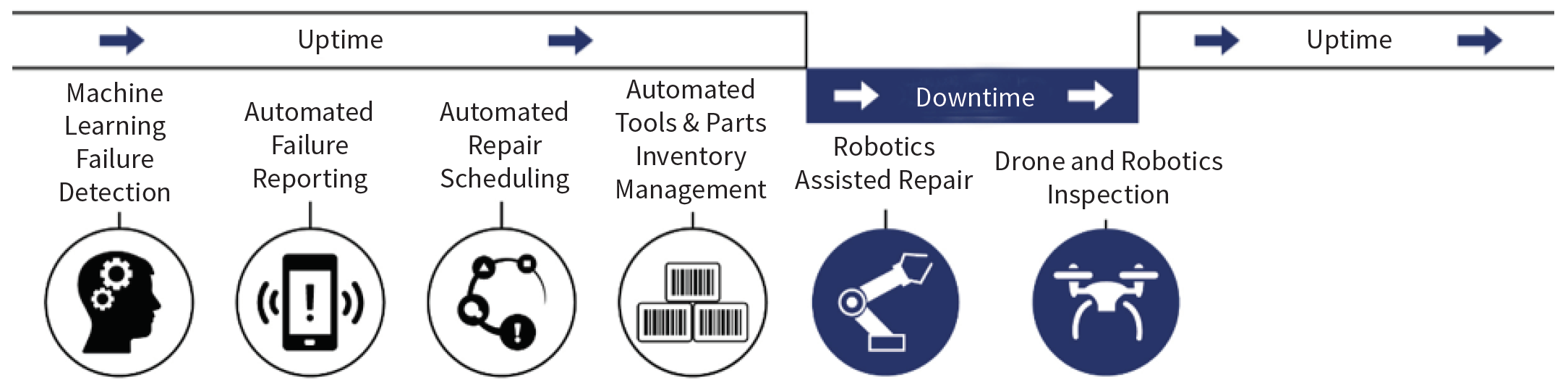

Figure 2: Automated machine-learning based failure prediction (Industry 4.0) Source Presenso
The Good News: A Rising Tide Lifts All Boats
To some extent, it can be argued that humankind is the beneficiary of Maintenance 4.0. Although this may sound hyperbolic, there is validity to this concept.
According to a 2018 U.S. Congressional Report, U.S. Manufacturing in International Perspective, the top 13 global manufacturers generated $9.1 trillion in manufacturing value added. Estimating that machine learning can reduce unscheduled downtime by five percent, then improvements in yield rates could add up to $455 billion a year to these economies.
Although there are no guarantees, there are two trickle-down effects:
- The potential impact on the environment by more efficient use of industrial plants and a reduction in energy consumption and raw material wastage;
- Opportunities to address systemic issues, such as global food waste and hunger. McKinsey & Company views big data and predictive maintenance as catalysts for improving food efficiencies in emerging economies.
Will Robotics and Automation Level the Playing Field?
As background, it is important to start with the role of robotics and automation as driving forces for Industry 4.0 and Maintenance 4.0.
The 2016 United Nations Trade and Development Report states that in 1970, 27 percent of the workforce in developed countries (e.g., the U.S., Europe, Japan) were employed in manufacturing. By 2011, this number had dropped to 13 percent. Conversely, the proportion in East Asia (e.g., China and South Korea) rose from 14 percent to 22 percent during this period. If the impact of automation outweighs the relative advantage of inexpensive labor costs, could manufacturing move closer to the end customer?
A partial answer is found in a Deloitte research study on Industry 4.0. Almost half of the representatives from the Swiss manufacturing sector indicated that digital transformation will be able to slow down the trend toward relocating to low wage countries. Only eight percent of survey respondents completely disagreed.
Since the collapse of the Soviet Union, Eastern Europe has become a manufacturing hub for Northern and Western Europe. With sunk infrastructure costs and supportive governmental policies, this is unlikely to change.
However, the outlook for parts of Asia is less predictable. The 2017 United Nations Trade and Development Report ranks South Korea and Japan as the highest in robotics density in manufacturing, followed by Sweden, Germany and the United States. China is now in catch-up mode, with only 49 robots per 10,000 humans, compared with a global average of 69.
In the short-term, drastic changes in manufacturing are not expected. However, by adopting a zero-sum game approach, it is likely that automation and robotics remove an important competitive advantage of low-cost manufacturing centers that are geographically far from the markets they serve.
Machine Learning and Big Data: The Untapped Resource of the Industrial Revolution
Deep within the exabytes of sensor data generated by industrial equipment are micropatterns that can be used to determine when a machine is likely to fail. Although this potential has been recognized by many industry observers, most industrial plants fail to use data effectively.
Why is this the case? First, there are technical barriers to accessing data. The World Economic Forum estimates that 85 percent of potential assets remain unconnected. More importantly, to understand the micropatterns within the big data requires the use of artificial intelligence (AI) and machine learning. Until recently, there were inadequate tools to access and analyze data in real time and provide actionable alerts of evolving failure.
Until recently, the machine learning discipline was primarily confined to academia. Today, the field is rapidly evolving so that vast amounts of data can be analyzed in real time. One significant development relates to the field of automated machine learning, whereby manual data science processes can be performed by self-learning algorithms.
Will advances in machine learning impact all manufacturers equally? Theoretically, the efficacy of a machine learning algorithm is not impacted by international borders and innovation can be shared rapidly. At the same time, insights from machine learning can be used to improve production processes and lower inefficiencies. In practice, the systemic application of machine learning to the manufacturing sector further narrows competitive advantages gained by plants in low labor cost countries.
Application to Operations and Maintenance
The confluence of robotics and machine learning has far-reaching consequences. As industrial nations are plagued by aging populations and skill set shortages, human labor can be replaced with artificial intelligence to detect evolving asset failures, and critical repair functions can be performed with partial or full robotics assistance.
These are not theoretical concepts and there are best practices emerging for multiple operations and maintenance use cases.
What is not yet apparent is the extent to which Maintenance 4.0 will change the manufacturing balance. Change is not expected overnight and there are multiple factors (e.g., Brexit, geopolitical turmoil, etc.) that are beyond the scope of this article. However, this industrial revolution may be consequential in ways that are unexpected for many and unwelcome for some.
NEW RELEASE!
Maintenance 4.0 Implementation Handbook
by David Almagor, Deddy Lavid, Avi Nowitz and Eitan Vesely
Order your copy: www.mro-zone.com