by Doug Plucknette
Understanding where to apply reliability measures is a foundational element of reliability engineering. If you want to improve a process, you need to understand the present level of reliability, where the losses or deficiencies are located and what you can do to reduce or eliminate these losses. One of the biggest problems regarding reliability measures is there are so many of them, so much so that they have begun to overlap, adding further confusion to those who are in the process of learning and applying the measures.
As an example, when the term MTTR is used, does it refer to mean time to restore, replace, repair, or respond? Each of the four Rs means something completely different, so if you are asking someone to measure MTTR, you should specify which R you are interested in.
While organizations should be performing a failure modes driven reliability strategy on critical assets, they also should be measuring overall equipment effectiveness (OEE) and total effective equipment performance (TEEP) as part of their upfront tasks prior to starting an analysis to get a baseline for the reliability of the asset prior to reliability centered maintenance (RCM) task implementation. But as soon as the term OEE is mentioned, there is often pushback, with comments ranging from, "We started measuring that, but were never happy with the number" to "We argued so much over what belonged in OEE that we could never settle on a good measure." Perhaps the most common excuse is, "I don't think we are ready for OEE/TEEP; our organization is just starting out with our reliability journey."
Really now, you believe you are ready to perform and implement an RCM analysis, but you are not ready to measure the reliability of your critical assets? Interesting, really. Many reliability engineers find the measures to be extremely helpful in understanding where equipment losses are located and which reliability tool might work best to reduce or eliminate the losses. But it turns out the problem most people have with OEE is that they don't measure TEEP as well.
Confused?
Think about it this way: How many ways have you seen people measure OEE? Let's start with total productive maintenance (TPM) founder Seiichi Nakajima's definition: Availability x Performance x Quality = OEE. The three factors making up the calculation seem quite clear, but the problem people begin having is understanding what the following parts of the equation mean?
- Is the equipment available?
- How did it perform?
- Did we maintain product quality?
Availability is quite simple. The equipment is available to run 168 hours each week. In that same time frame, how many hours was it actually capable of running? This is where the confusion begins. What is the difference between available and capable?
Here's a clarification: In your schedule to make product each week, how often did you need the machine to run and did it, in fact, run when you needed it to? Now that you have the equipment running, how did it perform and did it make good quality product while it was running?
Confused? You should be. The problem with measuring OEE on its own is that too much critical information is often lost because people play with the definitions of availability, performance and quality. The reality is they want their OEE number to look good and if it's not world-class, or what they think it should be, the next thing you know, off-spec quality is the only measure for finished products, which doesn't include all the products that had to be reworked to meet the quality standard.
Well, it's time to relax and put away the excuses because there is a much easier way to measure both OEE and TEEP. This method will bring clarity to both measures and to the reliability of all your organization's critical assets. The greatest value in measuring TEEP is that it captures everything, so the game playing and excuses are gone when it comes to the asset because it captures every single minute of time on the calendar. So, regardless of whether you want to include the downtime for your preventive maintenance (PM) tasks, or the time it takes to perform a product change in your schedule as part of OEE or TEEP, it does not matter. When you account for every minute of time (TEEP), it has to be recorded; when you only account for scheduled time (OEE), it allows one to manipulate.
The importance of understanding OEE and TEEP is essential so you can accurately forecast, plan and schedule production. Regardless of what the numbers are, if they have been consistent, you can now, with a high degree of accuracy, schedule what you can manufacture for your customers. Once you understand these measures, you can then begin to look at each of the loss categories, speed, quality, operational and planned, and use the appropriate reliability tool to reduce the losses.
Looking at the bar chart in Figure 1, one can clearly see the similarities and differences of OEE and TEEP. If your present weekly schedule is designed to run the equipment 24 hours a day, seven days a week, then the OEE and TEEP numbers would be identical. If you decide to shut down the equipment for 20 minutes at the beginning of each shift to perform some TPM cleaning and lubrication tasks, then the one hour of lost time would be captured in the planned losses category. The key in measuring OEE and TEEP is to understand the true reliability of your assets.
Prior to beginning your effort to measure OEE and TEEP on your critical assets, you should first meet as a team with operations, maintenance and quality managers. Each organization should get an equal say regarding the composition of the loss categories.
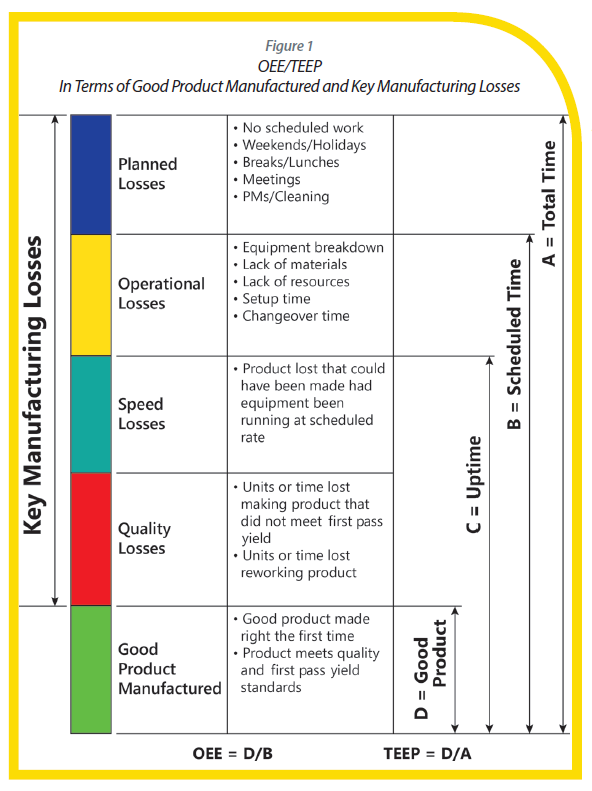

These basic definitions of the terms used in Figure 1 can be enhanced with details based on your business:
Planned Losses - Part of TEEP, planned losses represent the time or units lost because the equipment was not scheduled to run. Planned losses might include weekends, holidays, breaks, lunches, or lack of demand for the product. Time for PMs and capital improvement projects should be considered a planned loss.
Operational Losses - These represent product losses associated with unscheduled equipment downtime due to equipment failure, lack of resources, lack of materials, product change, or cleaning.
Speed Losses - This loss category includes all product lost due to being unable to run the equipment at the desired or scheduled operating speed.
Quality Losses - This category represents product lost from being unable to meet first pass yield quality standards. It should be noted that even if the product is reworked in any way and sold, it still should be counted as a quality loss.
Good Product Manufactured - This represents good product made right the first time within the schedule. This product must meet all first pass yield quality standards and the number cannot exceed the scheduled rate.
With these generic statements, your business can now add language to make each category more specific to your business. Once you have agreed upon what belongs in each category, the trick here is to never change it for any reason.
Setting Goals Around OEE and TEEP
As stated earlier, the objective of measuring OEE and TEEP is to be able to understand the reliability of your critical assets and determine where your losses are located so one can use the correct reliability tool to reduce those losses and improve reliability.
While continuous improvement always should be your goal, be cautious regarding some of the traps of OEE and TEEP. Back to the late 1980s, one can find examples where someone made the statement that if your equipment had an OEE of 85 percent or better, you had world-class equipment reliability. However, there are two solid examples as to why this statement is nonsense:
- If Company A is a utility that provides electric power to hundreds of thousands of people some place in the world and the OEE of its power supply equipment was 85 percent, the company would no longer be in business.
- Company B is a food company that manufactures a batch product that requires cleaning between batches. If it did everything correctly every day for 30 days, the best OEE it can achieve is 78 percent. This is well above world-class for its industry.
Again, the key to setting goals around OEE and TEEP comes down to continuous improvement and understanding what tool/tools to use to reduce or eliminate the losses. Once you have reduced or eliminated your losses, your goal should be to sustain the improved number. Remember, one of the greatest benefits of reliable equipment is the ability to accurately plan and schedule production. If you can accurately plan and schedule production, you then should be able to easily plan and schedule your PM and predictive maintenance (PdM) tasks as well.
Who Should Collect and Post OEE/TEEP Numbers?
Nothing is more shocking than seeing a reliability engineer collecting OEE and TEEP information and reporting the numbers to plant managers, all the while failing to include the operators and maintenance technicians who collectively have the greatest ability to impact the numbers.
OEE and TEEP data collection and reporting should be performed by your operations team leaders and reported at the end of each shift. Doing so will result in the best shift exchange your company has ever experienced because your lead operators now have some data and information to discuss. As an example, if the average OEE for a given asset is between 81 and 83 percent and the next shift comes in and notices that the prior shift ran at 76 percent, don't you believe these lead operators will have something to talk about?
Collecting this information at the correct level is a key part of engagement at all levels of the company. Collecting the data at the correct level engages the equipment operators and maintenance technicians. You then need to understand the data and this is where your reliability engineer comes in. Upon analyzing the data and understanding the losses, he or she can now engage people and managers from all aspects of the business to reduce losses.
OEE and TEEP Losses = What Tool, When
What's most beneficial about measuring OEE and TEEP in this format is they can very easily lead reliability engineers to the correct tool for reducing or eliminating the loss. The following list features various reliability and quality tools and the types of losses they will eliminate.
Reliability Centered Maintenance (RCM) - Reduces or eliminates equipment, process, or human-based speed, quality and operational losses experienced across a wide variety of machine components.
Root Cause Analysis (RCA) - Reduces or eliminates equipment, process, or human-based speed, quality and operational losses that can be attributed to a specific part, component, or incident.
Statistical Process Control (SPC) - Should be used along with OEE data to reduce quality losses that are human, process, or equipment based.
Total Productive Maintenance/Manufacturing (TPM) - Used to develop operator care tasks, TPM can drastically improve reliability and reduce planned losses.
Lean Manufacturing - This warrants caution as far too many companies try to implement lean manufacturing techniques before they have achieved equipment reliability, resulting in a failed lean manufacturing effort. One should only begin to implement lean manufacturing once there has been a sustained OEE and TEEP for three to six months. With that being said, lean manufacturing techniques can further eliminate process-based operational and planned losses.
There you have it! The first key to a successful reliability initiative should always start with measures. Understanding where you are today is an important part in charting the course for your journey.
Purchase at www.mro-zone.com
- Reliabilityweb OEE: How Do You Use It? ›
- Reliabilityweb Right 4 Build and Fabricate for Reliability: The 10 Rights of Asset Management ›
- Reliabilityweb Right 4 Build and Fabricate for Reliability: The 10 Rights of Asset Management ›
- Reliabilityweb SICK’S Monitoring Box Opens a Window to Better Machine Performance ›
- Reliabilityweb Overall equipment effectiveness (OEE) ›