That is a very interesting comparison when we consider that between 50 percent and 70 percent of equipment failures are likely due to infant failures resulting from either maintenance or commissioning errors.
An April 1999 study of misalignment versus bearing life by the University of Tennessee’s Maintenance and Reliability Center showed that as little as 5 mils/inch of misalignment when using a grid coupling could reduce bearing life by as much as 50 percent.
It could be said that the most important periods in any asset’s life are the installation and commissioning phases. Equipment will achieve 100 percent of its design capability if the job is done well. Conversely, equipment will start life in a degraded state if the job is done poorly.
THE PURPOSE OF QUALITY MANAGEMENT
A quality management system (QMS) consists of two types of activities. Quality assurance (QA) is activities designed to ensure that quality is built into the process. Quality control (QC) is activities designed to ensure that desired quality levels are actually achieved by the process. It takes both types of activities to reach desirable quality goals. It is unreasonable to expect that quality assurance will be 100 percent effective in preventing maintenance and commissioning errors. The activities are a human endeavor, which means mistakes will be made regardless of how rigorous the procedures are. It is also uneconomical to inspect every defect using quality control methods.
Aircraft | Naval Vessels | Manufacturing | |||
Failure Curve | 1968 UAL | 1973 Broberg | 1993 Surface** | 2001 Submarine* | 2005 Plucknette |
A - Bathtub | 4% | 3% | 3% | 2% | 3% |
B - Wearout | 2% | 1% | 17% | 10% | 3.5% |
C - Fatigue | 5% | 4% | 3% | 17% | 6.5% |
D - Break-In | 7% | 11% | 6% | 9% | 7% |
E - Random | 14% | 15% | 42% | 56% | 13% |
F - Infant | 68% | 66% | 29% | 6% | 67% |
Table 1: Results of Reliability vs. Age Studies (Nowlan and Heap, Nicholas, Pau, Allen, et al.)
*The data was gathered after over 30 years of implementing the SUBSAFE Program
**The data was gathered approximately 15 years after the naval surface force adopted maintenance strategies similar to those used in submarines.

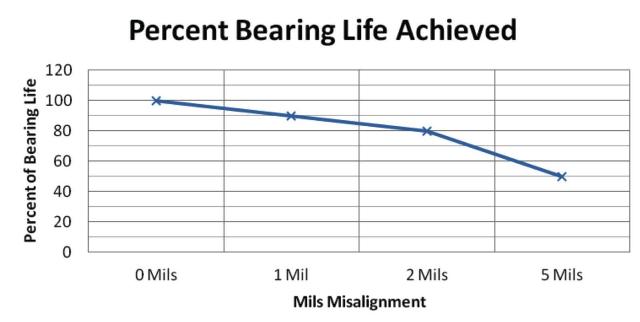
Figure 1: Percent Bearing Life Achieved
Figure 2: The Equipment Lifecycle
PRECISION MAINTENANCE AND QUALITY ASSURANCE
Precision maintenance is achieved by well-trained people using precision methods and well-written procedures. Quality assurance is achieved by inserting steps in the procedures that require the person doing the work to record a number and the person supervising the work to approve the number. This is not an easy assignment. It will probably make jobs last a bit longer, which nobody likes, but if it makes the installation (I) to potential failure (P) interval longer, it will be well worth it.
Figure 3: I-P-F curve from Doug Plucknette
QUALITY CONTROL IN MAINTENANCE
Quality control means having the discipline to come back at the completion of the job to take what have been referred to over the years as baseline readings for condition monitoring. Admittedly, this is an important step for the condition monitoring program, but changing the focus from just getting baseline readings to quality control of the work done will result in a greater return on those condition monitoring tools. The use of vibration analysis, thermography and ultrasonic tools will enhance your organization’s ability to find misalignment, close couplings, leaking fittings, missing insulation, loose electrical connections and other installation faults after maintenance work.
WHERE TO START
Figure 4
Decide to Do It
The first step in making any change is to decide to make the change. Nothing happens without this critical step.
Build Organizational Support
Support from all levels of the organization is crucial to the success of this program. Management has to be shown the potential value, and the rank and file has to be shown what is in it for them. Evidence from a 1986 Electric Power Research Institute study suggests that a precision maintenance program has significantly lower costs than either preventive or predictive maintenance alone (see Figure 5).
Figure 5
Create Policies & Procedures
Policies and procedures are an important way of institutionalizing any new program. They establish what will be done, how it will be done and who will do it. Everyone’s roles, goals and responsibilities will flow from these, so they should include a RAS/CI table to summarize responsibilities. The RAS/CI table is a quick visual summary of the responsibility level of different organizational roles for a given process.
Determine Critical Jobs
Jobs, like equipment, have some level of criticality. Criticality is a function of probability of occurrence and business impact. High impact jobs that are performed frequently would pop to the top of your list and should be examined for improvement using QA and QC methods to ensure reliable performance.
Write and Implement New Procedures
Pick a procedure and begin working on it. The procedure writing process should be an inclusive, facilitated process that includes the people who will actually have to perform the work. The beginning of this process is a visual breakdown of the job called a job map. A job map is similar to a work breakdown structure for the job, but it has steps that identify dangers to people and equipment, job impediments, resources and job performance standards. The actual writing of the procedure can take place once the team agrees that the map is complete.
Monitor and Adjust
Quality management is a continuous improvement process. It is important to monitor both the process and the work product to ensure the new program is working. Establish key performance indicators (KPIs) to measure progress in creating and implementing the new procedures and to measure whether or not the procedures are effective.
CONCLUSION
There is a lot of evidence showing that the quality of maintenance and commissioning of equipment needs to improve in almost every industry. Hardly any manufacturing or service organizations create their products and services without some sort of QMS in place to ensure the customers get a quality product at a reasonable price. The maintenance department is a service organization whose goal is to deliver uptime at a reasonable price. A well-designed QMS will enable them to do that.