While the lines between these different strategies have been blurred over the past 10 to 15 years, at their core, they all focus on one fundamental tenet: Create efficiencies by improving business processes that eliminate waste. In this context, waste can mean anything from wasted time, wasted effort, or wasted raw materials.
Fundamental to waste elimination is the concept of 5S. Originally developed in Japan as a way for frontline workers to provide feedback on process improvements, the 5S concept was originally represented by five Japanese words, each starting with the letter ‘S.’ Today in North America, 5S is most often transliterated into five English words that have become the cornerstone of any lean-Six Sigma initiative. Those words are: Sort, Set in Order, Shine, Standardize and Sustain.
APPLYING 5S TO LUBRICATION
At its core, 5S is a methodology by which technology (engineering) and psychology (people) are optimized to achieve an efficient set of business processes. A business process is simply a set of steps, rules and practices required to complete any specific task. In this context, lubrication, like any other activity in a manufacturing plant, is just another process. It is the process of selecting, purchasing, storing, dispensing and applying the lubricant to the machine while maintaining (sustaining) the quality and cleanliness of the lubricant. As such, 5S principles can and should be applied to the process of lubrication for maximum efficiency. So let’s see how we can 5S our lubrication program, starting with sort.
SORT
With respect to lubrication, sort has two phases. The first is to organize which lubricant needs to be used based on application and operating context. The goal is to minimize the number of lubricants in use without compromising equipment reliability or performance. For plants that have been through a 5S process, the number of lubricants used have been optimized with a concerted effort put in place to consolidate to a single lubricant supplier and, where applicable, to eliminate unnecessary types or grades of lubricant through technical consolidation. 5S plants typically have a database (spreadsheet) listing each asset and the lubricant to be used, with this information readily available and published, often as a poster or wall chart. It may seem obvious, but knowing which lubricant is used in which machine is fundamental to future success, but so few plants even get to first base!
The second phase of sort is to create organization in how lubricants are stored, handled and made available throughout the plant. 5S is a highly visual process; everything in place where everything has its place. Lubricant storage areas need to be organized and ergonomic, with clear visual workplace management tools, like color coding, charts, shadow boards etc., used to denote what the desired state should be. Designating an “owner” of the lube room and other designated lubricant storage areas is often an effective means of making sure standards don’t slide over time and creating a sense of accountability while promoting pride in doing a good job.
SET IN ORDER
Central to the principles of 5S is efficiency. Requiring an operator or lube tech to walk several hundred yards or more to access the oil or grease they need is, at best, creating inefficiency in work processes and, at worst, encouraging lubricants to be stored behind the machine or for the wrong oil to be added since it’s closer. Lubricants and the tools necessary to do the job right need to be at hand. This may require satellite lube lockers at point of use or portable lubrication carts that can be moved around as work is performed. Visual workplace management needs to extend to all designated remote storage, with the same 5S principles used in the lube room. Accountability is the key for remote storage, with weekly inspections and check sheets used to ensure standards remain consistent.
More often than not, errors, like adding the wrong oil or applying the wrong grease, happen by mistake. To minimize the likelihood of mistakes happening, a highly visual workplace is a fundamental part of any lubrication 5S process at all levels. The lube room, lube locker, tools, machine etc., all need to be tagged with a color and shape to designate which lubricant is in use. Tags should be placed at all critical control points where lubricants are transferred from one point to another or to the machine. Ideally, lube tags should not specifically state the manufacturer or brand lubricant in use. While this may seem counter to 5S principles, including the brand name lubricant will cause problems if you decide to switch suppliers in the future.
With product brand names on lube tags, you’re just one vendor change away from violating the last “S” in 5S – Sustain!

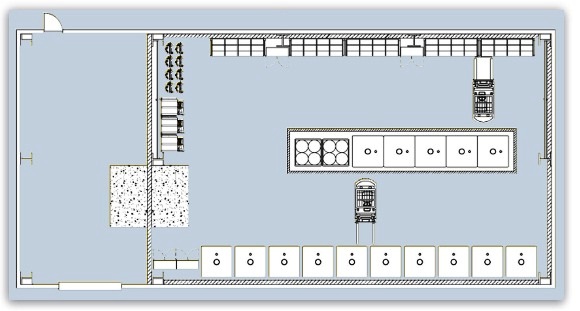
Figure 1: Lube storage areas need to promote ergonomic work flow while promoting best practices through visual work management (labels, color coding, shadow boards, etc.)
Finally, machines need to be configured to allow preferred practices to be deployed. Denoting that all new oils need to be pre-filtered before use without setting up the machine with quick connects or a proper breather defeats the purpose. Making the easy way the right way (transfer oil from the barrel using a portable filter cart and quick connects on the barrel and machine versus open the fill port and use a hand crank oil transfer pump) is a critical step towards making sure buy-in occurs at all levels.
SHINE
Cleaning and inspections are important in creating consistency and continuity. In addition to assigning responsibility to keep lube storage areas clean through weekly inspections, machines need to be kept clean, free from leakage and routinely inspected. Any leaks that are found should be noted and immediately put into the work management system for corrective action. Basic lubrication inspection should be included as a daily task. Oftentimes, operators can be trained to do these basic checks. Make inspections simple and easy to do and they get done. Allow opportunity for individuals to interpret what you want and shortcuts will happen. Lube inspections need to include simple, basic questions and binary answers (e.g., oil level: high or low?; desiccant breather: blue or pink?; filter differential pressure <20 psi: yes or no?).
STANDARDIZE
Having standard work procedures is a must for any maintenance team. I often get asked how a company can get 50 different mechanics, technicians and operators all functioning at the same level. The answer is standardization. Commercial aviation is by and large an efficient, safe business process that works because every task from pre-flight checks to refueling, baggage loading and flight plans is choreographed on checklists and standard operating procedures. If United Airlines can do it with hundreds of people all capable of influencing the success of flying from Chicago to Houston in a multi-million dollar machine flying at 37,000 feet, surely adopting a similar approach can work for us on the ground. While we may not need quite the same degree of rigor, a standard work process, checklist and documentation all feature heavily in successful 5S plants.
But it’s not just about having documents that serve as preventive maintenance (PM); it’s how the PM is written that counts. Having a PM worksheet that states “lubricate the motor” is not a standard operating procedure, it’s a wish! The PM should include specific details, such as which lubricant to use, basic steps to ensure compliance with best practices (e.g., clean the grease fitting, allow three to five seconds/ shot, etc.), as well as task specific details, such as the quantity of grease in shots or ounces.
Figure 2: PM procedure should include enough instruction to ensure the task is completed consistently each time
SUSTAIN
I visit a lot of plants each year in many different industries. But no matter the plant or industry, they all have something in common: basic metrics for safety (“we have worked 243 days without a lost time accident”) or production (“OEE year-to-date = 94.7%”). Do we really need reminding to work safe and hit production quotas? The answer is an emphatic “yes!” Without standards by which we’re measured and consistent reinforcement of those standards, it’s inevitable that things will slip over time.
For lubrication, basic metrics like lubrication PM compliance (ratio of completed lube PM on time/total number due), compliance with contamination control targets (ratio of machines that meet our targets vs. the total number of machines), or compliance with lubricant health (number of machines “in the green” from oil analysis vs. the total number sampled) serve as the “scoreboard” by which lubrication success or failure can be measured. By tracking metrics and posting them conspicuously, the message is clear. We expect everyone to take seriously a set of performance standards around lubrication, with clear, actionable remedies if we’re in non- compliance.
PUTTING IT ALL TOGETHER
Having taught literally hundreds of lubrication classes over the past 20 years, it always amazes me the number of companies that send good people to training classes expecting that simply sitting through three-days of lubrication training will turn the plant’s performance around. While it’s true having knowledgeable and committed people is key, it’s only with a proper system in place built around solid 5S principles of sort, set in order, standardize, shine and sustain that we can maintain performance over the long haul. True competitive advantage comes when great people work in a great system. When that happens, great things occur!