Orchestrating the performance of enterprise assets has become a critical enabler for a safe, productive, and profitable operation. Yet, for many companies, making properly informed asset management decisions remains a work in progress, hindered by incomplete data and limited insight.
In speaking with a large range of attendees at The Reliability Conference in May, the topic that received a lot of attention is the need to better appreciate why systems and equipment fail in the broader ecosystem, rather than at the equipment level, and how these insights are crucial in effectively managing future events.

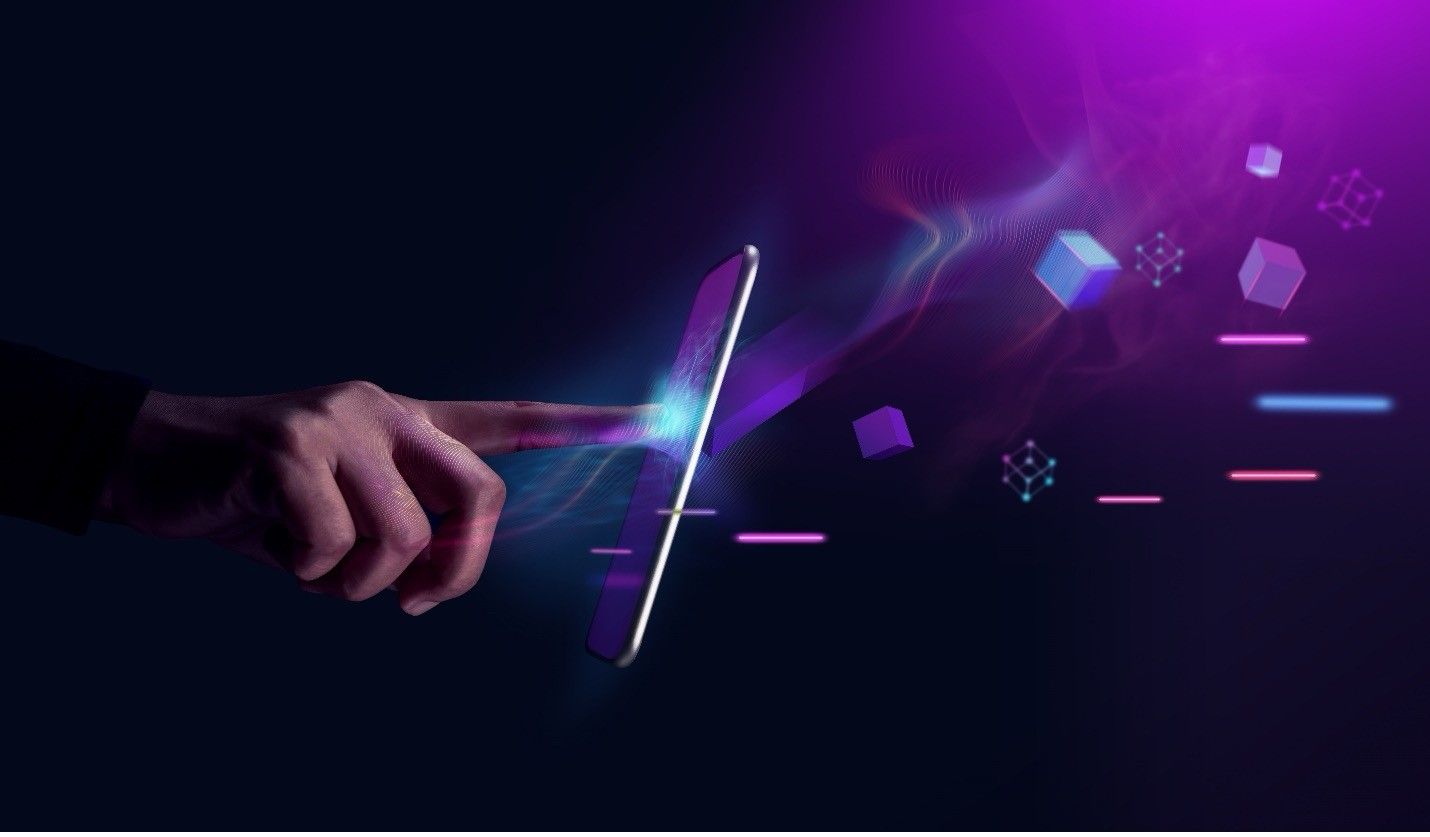
In this blog post, we examine the importance of analyzing assets holistically to understand which failures pose the greatest risk, what actions to take, and when. We also identify scenarios where asset downtime may be the best outcome for the bottom line.
Asset performance: The big picture
Today, enterprises must examine the health and output of assets in their totality. Along with immediate performance issues, the operations team must also consider the bigger picture, such as previous repairs and failures, performance history, and the impact of other assets on outcomes and events that have contributed to the current state of individual assets.
Rich data is required to develop such rich insights. Fortunately, there is plenty to go around. With the advent of IoT and connected devices, enterprises are swimming in data. In fact, by 2025, the world is estimated to generate 181 zettabytes of data volume.
Understanding the interrelationship of each asset within the overall operation, including dependencies and interdependencies, in addition to their own specific failure modes, is also essential. What does the asset enable? How is production impacted if the asset isn't performing optimally? Is the asset mission-critical in the moment?
Without this context, quantifying a compromised asset's immediate and longer-term impacts is impossible. Especially for asset-intensive operations that face hundreds of performance issues daily.
Asset reliability and availability
To deliver optimal value to the enterprise, assets must be reliable (able to perform as required without failure, for a given interval of time, under specified conditions) and available (capable of performing as intended).
Since the status of an asset is fluid and ever-changing, balancing reliability and availability requires active oversight and informed decision-making.
There is an implicit relationship between asset performance degradation (condition), production quality (wastage/scrap) and cost over time. In ISO55000 terms this could be viewed as performance vs cost vs risk.
By leveraging rich data stores, the computational power of AI, and other advances in technology, the team accurately determines the optimal timing and investment required to resolve asset performance issues. The advantage of data-based decisions is that they provide insights into when an intervention will minimize the overall impact on revenue and costs, not just reliability and availability.
The upside to downtime
There's no denying that downtime is expensive. As noted in my presentation at the aforementioned reliability conference, a recent report by Siemens estimates unplanned downtime will have cost Fortune Global 500 companies almost $1.5 trillion in 2023, about 11% of annual revenues.
While no one ever willingly signs up for unplanned downtime, there are some scenarios where the timing of that downtime makes the most sense for the bottom line.
Instead of rushing out to fix a problem as soon as it's detected, enterprises must apply a more considered approach, examining all variables, including costs, resources, impacts on productivity, and other factors.
Central to the decision-making process is understanding what caused the problem (failure mode) and the subsequent effects on productivity. These insights allow the team to assign a tangible value-versus-cost ratio to help determine when and how the asset will be restored.
In scenarios where multiple assets are at risk, those most central to productivity rank highest. In these situations, the team may decide that intentional downtime (run-to-failure) for non-critical assets makes the most sense, freeing up time and resources to attend higher-priority events.
Intelligent asset maintenance
The maturation of asset management and performance models is closely tied to the technology profile of an enterprise.
Typically, organizations will have some form of computerized maintenance management system that enables them to manage reactive and preventive maintenance, for example, an enterprise asset management (EAM) system.
For some asset intensive businesses these systems may impede advancement within the maturation curve, a fact borne out in the IFS asset management trend report launched at the 2023 International Maintenance Conference. When asked, the majority of participants assigned their organizational maturity at between maintenance 1.0 and 2.0, with technology cited as the blocker.
IFS Cloud EAM customers evolve their maintenance maturity from the typical Maintenance 2.0 legacy approach to integrated condition-based management that permits them to implement and execute on Maintenance 4.0 philosophies.
IFS Cloud delivers advances in industrial artificial intelligence that lead to predictive and prescriptive maintenance adoption, which in turn leads to Industry 5.0 outcomes through a transition to intelligent asset performance management.
Naturally, data volume and advanced analytics are baseline requirements when an enterprise evolves to predictive maintenance and, ultimately, intelligent APM practices.
Artificial intelligence, machine learning, and other inputs, for example, data from analytical methods such as FMECA, support the decision-making process. Real-time visualizations and insights are generated to help answer essential questions: Is the situation urgent? Is the asset critical to productivity, and if so, how? Are there more serious issues that require the investment of time and resources?
With inputs drawn from historical and real-time data, intelligent APM maintenance is enabled, allowing the team to confidently coordinate timing, schedules, people, and parts based on operational prioritization and productivity.
AI-powered Asset Performance Management
Enterprise assets and equipment don't operate in isolation. Instead, each cog, wheel, pump, etc., interacts with other components to produce the desired result.
IFS works with enterprises globally, helping them understand the interrelationship of every asset within the operation, including its history, immediate impact on productivity, and other factors. With IFS Cloud EAM, our customers leverage AI-powered capabilities to identify problems and predict outcomes, helping them make the right decision at the right time.
For more information on maintenance planning, view the infographic. To learn about IFS Asset Performance Management, visit our website or contact us.
About IFS
IFS develops and delivers cloud enterprise software for companies around the world who manufacture and distribute goods, build and maintain assets, and manage service-focused operations. Within our single platform, our industry specific products are innately connected to a single data model and use embedded digital innovation so that our customers can be their best when it really matters to their customers – at the Moment of Service™. The industry expertise of our people and of our growing ecosystem, together with a commitment to deliver value at every single step, has made IFS a recognized leader and the most recommended supplier in our sector.
Our global team of over 6,000 employees every day live our values of agility, trustworthiness, and collaboration in how we support thousands of customers. Learn more about how our enterprise software solutions can help your business today.
This Sponsored Industry Article is brought to you by
* The opinions expressed herein are not necessarily those of Reliabilityweb.com.
- IFS Named First-Ever Official Technology Partner of Big Ten Conference ›
- IFS Launches Compelling Industrial AI Capabilities in Latest Release of IFS Cloud ›
- IFS positioned as a Leader in IDC MarketScape for Worldwide Manufacturing Service Life-Cycle Management ›
- Indycar Racing team AJ Foyt Racing selects IFS Ultimo EAM software for critical Parts Management, Lifing and Maintenance processes ›
- IFS Acquires Poka ›
- IFS delivers 38% YoY revenue growth with sharp rise in demand for its AI capabilities ›
- Mark Moffat Appointed as CEO of IFS ›
- IFS acquires ULTIMO ›