Background:
In August of 2002, the reliability program at Kennecott was kicked off with a reliability study of the P&H 4100A shovels at the Bingham Canyon Mine. Under the guidance of ARMS reliability engineers, using RCM Cost software and a team of Operations and Maintenance personnel, the performance of the 4100A fleet was improved markedly. Following the 4100A study, studies were done on the CAT 793B fleet at the Mine, the Grind Plant at Copperton Concentrator, and on the Automatic Guided Vehicles and the Cathode Stripping Machine at the Refinery. All of these studies proved to be of significant value to Kennecott.
In late 2003, Kennecott Utah Copper decided to implement a Six-Sigma program to augment the APEX (Achieving Performance EXcellence) initiative that was already under way. Between then and June of 2004, extensive planning took place to make sure the program implementation was a success. An implementation champion was selected and a master black belt was hired. A six-sigma coordinator was also brought in from outside the organization. In June of 2004, the first wave of black belts and green belts began their training and first project. Since then, waves 2, 3, 4 have been completed and training is almost completed for wave 5. In short, the six-sigma program is well underway and so far looks to be very successful.
When six-sigma was first introduced, there was quite a bit of concern that resources needed for the reliability effort would be compromised, and the reliability effort would die. It is well known that six-sigma uses ad-hoc teams to accomplish much of the improvement, relying on "process owners" from individual areas to sustain the improvements once the "belt" moves on. This is very similar to what happens in a reliability study. That is, extensive team participation is necessary to produce a workable improvement strategy, and the improvements must be adopted by a "process owner" in order for the improvements to be implemented and sustained.
This paper is a comparison of the reliability methodology and six-sigma methodology, and how both can coexist in any organization.
Reliability and Six-Sigma Methodologies:
Reliability
Reliability is many things to many people. It is predictive maintenance to some and root cause analysis to others. Some think of failure elimination teams when they talk reliability while others think about RCM. The truth of the matter is reliability is a concept, a methodology, which uses many tools to accomplish the end goal. Predictive maintenance, RCFA, RCM, and teams are only tools used to accomplish reliable equipment operation.
Reliability is defined in the KMS (Kennecott Maintenance System) as the ability of an asset to perform its intended function in producing a quality product or service for the intended asset life cycle when operated under specified conditions. An effective reliability program is closely associated with the maintenance program and operating practices. It addresses the initial selection of assets, the quality of workmanship, the reduction of failures, and the care taken in operating and maintaining assets.
In short, reliability at Kennecott is understanding how critical equipment failures, operating practices, and maintenance strategy are intertwined, and maximizing the outcome to provide optimum value to the business through systematic failure elimination. Many tools, including RCM Cost, AvSim+, and RCFA are used to accomplish this goal.
The reliability process at KUCC is shown in Figure 1 below.

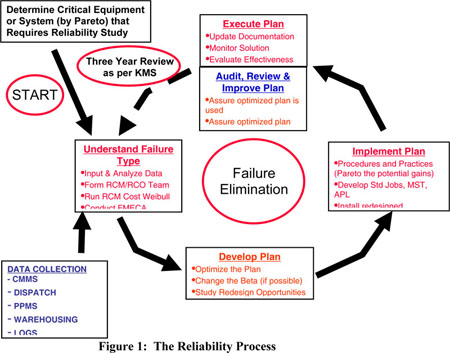
Six-Sigma
Six-Sigma is thought by many to be only a statistical measurement that represents 3.4 failures per million opportunities. Having a six-sigma program does not mean all of your processes need to reach six-sigma levels of performance. Six-Sigma is simply an improvement initiative aimed at reducing variation.
Aaron Breen, the master black belt at Kennecott Utah Copper comments that "Six-Sigma is an Attitude with a Tool Box." The attitude is problems are opportunities in disguise. The tool box represents strategies used to efficiently address and resolve the concerns. Common tools are TEAMWORK (brainstorming, information sharing, etc.), STATISTICS (data analysis to make decisions accurately, efficiently, and without emotion), LEAN (structured method to remove waste from processes), and MISTAKE PROOFING (designing process such that it is easy to do it right and hard to do it wrong).
Six-Sigma is nothing more than a survival strategy for today's fast paced, high pressure work environment. It provides a structured approach to address customer needs. Six-Sigma uses proven tools and techniques to address business concerns. It provides more rigor and structure than previous programs.
Six Sigma is very hierarchical in it structure and work process. Everyone within the organization (from the CEO to shop floor workers) has a role to play in this process. (Breen, 6). The basis of the six-sigma methodology is DMAIC (Define, Measure, Analyze, Improve, & Control) as shown below in figure 2.
Figure 3 shows the reliability process and how the DMAIC process works in parallel with it at KUCC.
It seems the basic difference between Six-Sigma and Reliability is the scope and depth of the projects. In six-sigma, the "belt" is told to continually narrow the scope so that an in-depth and detailed analysis takes place. In reliability, the scope is wider by design. The scope must encompass an entire system.
In reality, reliability engineering and six-sigma use much the same approach in solving problems. In fact, at Kennecott Utah Copper, six-sigma classes are taught a reliability module, and many "belt" candidates are reliability engineers. At the Refinery, the Manager is so confident in the six-sigma program, he has made a commitment to have his Reliability Engineers all receive green belt training.
The similarities and differences will be seen in the following detailed analysis comparing the five phases of the DMAIC process with the Reliability efforts at KUCC.
DMAIC, Six-Sigma, & Reliability:
In order to compare the two methodologies, an actual completed six-sigma project will be compared to an actual completed reliability study. The six-sigma project was a process improvement project dealing with reducing same day requisitions within the warehousing and purchasing system. The reliability project will be the P&H 4100A reliability study.
Define Phase
Six-Sigma
In the Define Phase of a Six Sigma Project the main deliverables are a business case, problem statement, objective statement, primary and secondary metrics. In the same day requisition improvement project, the following were derived during the define phase.
Same Day Requisition Define Phase Summary
Business Case:
Based upon functionality concerns of the Logistics Operations Project , the
Concentrator has an opportunity to improve its materials management system effectiveness enabling an increase of uptime, reduced maintenance spend, reduced inventory level, and reduced materials spend (estimated value of $500,000).
Problem Statement:
"This project will decrease the number of same day requisitions as a % of total monthly requisitions from 50% to 20% by November of 2004 by improving the conditions and/or practices that drive same day requisitions."
Objective Statement:
"As a result of decreasing the percentage of same day requisitions by 30%, KUCC will save in O&M costs, $35 thousand dollars in 2004, and $215 thousand dollars in 2005."
Primary Metric:
Same day requisitions as a % of total monthly requisitions. This is the metric for which improvement will be judged.
Secondary Metric:
Service Level. This is the metric that should not be adversely affected by improving the primary metric.
Tools Used:
Data Mining
X/Y Matrix (MS Excel)
Problem Selection Pareto
Negotiation
MS Power Point
Reliability
The first step in a reliability project is to determine what area requires a reliability study. This can be done using simulation software, or simply by using a Pareto chart. The following was developed in the reliability study equivalent of the Define Phase.
System on which to focus:
Mine management determined, based on production data, that the P&H 4100A shovels were the main cause of below budget production. A CPQQRT (Context, Purpose, Quantity, Quality, Resources, and Time) analysis was developed to further direct efforts.
What to do about it:
Prior to the reliability study kick-off, a Pareto of the main causes of downtime were identified and a plan to address them was put into action.
The plan:
Perform a thorough Reliability Analysis on the five top contributors to downtime:
1. Crowd Machinery
2. Electrical - General/Misc
3. Electrical - Will Not Start
4. Dipper Sticks
5. Propel Machinery
Tools used:
CPQQRT
Data Mining (Ellipse & Excel)
Pareto
Negotiation
As can be seen, the two methodologies are very similar through the define phase.
Measure Phase
Six-Sigma
In the Measure Phase of a Six Sigma Project the main deliverables involve forming a team and completing a list of Input Variables that affect the primary metric (FMEA), developing a Baseline Capability Statistic (capability analysis) figure 4, Validating the Measurement System (measurement system analysis) figure 5, and developing a preliminary project plan.
Attribute Agreement Analysis for Week One, Week Two Within Appraisers
Assessment Agreement
Appraiser # Inspected # Matched Percent 95 % CI
1 8 6 75.00 (34.91, 96.81)
# Matched: Appraiser agrees with him/herself across Appraisals
Same Day Requisition Measure Phase Summary
At the conclusion of the Measure Phase, the following were in place:
- The Process Mapping and MSA identified fourteen variables for continued investigation;
- Using the process capability functions in MiniTab, the process capability was measured to be 91% of requisitioners exceeding goal (9% yield)
- Measurement system improvements were identified through the application of a data audit and Attribute Assessment Agreement analysis.
- A project plan was formed in order to assign, coordinate, and track progress.
Tools used:
MiniTab statistical software
FMEA
Team building
Microsoft Excel
Microsoft Power Point
Reliability
In the reliability equivalent of the measure phase, a reliability improvement team is formed, training for the team takes place, a mission statement is developed, data is input into the statistical analysis software, an equipment hierarchy is developed, and an FMEA/FMECA are conducted. The output of this stage is a listing of areas that could possibly be improved. This is very much like the list of variables developed in the six- sigma process.
4100A reliability improvement team Phase Summary
- Two Day Team Building Exercise - Held August 8th and 9th, 2002
- Cross Functional Team Members:
- Team Sponsors
- Assets & Services Manager
- Material Prep & Technical Manager
- Team Leader
- Lynn Nelson - Maintenance Support Superintendent
- Team Members
- Shovel Maintenance Supervisor
- Engineer
- Planner
- Shovel Runner
- Shovel Mechanic
- Bill Keeter - BK Reliability, Inc.
- PLC & GUI Engineer
- P&H OEM Representative
- Shovel Operations Supervisor
- Mission Statement Development
- We as a Team support the people who do the work. Relying on Bingham experience, fresh ideas, capabilities and tools we will safely improve the reliability of 4100A shovels. We aim to be the BEST! Zero failures between PMs and an optimized production cycle, sustainable after 9 months, will measure our success and help ensure our survival. We will share the knowledge gained through our hard won successes within KUC and with our partners.
- The team participated in a two-day RCM Skills Building Course
- An equipment hierarchy was constructed
- An FMEA was conducted on the 4100A shovel identifying Systems, Sub-systems, functions, functional failures, and failure modes
- A hierarchy incorporating the entire FMEA was then constructed, figure 6.
Figure 6: FMEA Hierarchy
Tools used:
RCM Cost statistical software
FMEA
Team building
Microsoft Excel
Microsoft Power Point
Once again, the process is very similar to the measure phase in the six-sigma same day requisition project.
Analyze Phase Six-Sigma
The purpose of the Analyze Phase is to scrutinize each input variable identified during the Measure Phase. As a result of this examination, the "critical few" inputs are identified for optimization in the Improve Phase. For the same day requisition project, the following tools were used: FMEA, MSA, Hypothesis Testing (Variance Testing, Tests of Proportions), and Simple Regression.
As a result of this work effort, the list of 14 potential "X" variables identified in the FMEA was reduced to 7 critical input variables in Table 1 (below). To focus work efforts on these input variables, a project plan was created.
Analyze Phase Critical Input Variables |
Training |
System Modification (Priority Code Usage) |
Logistics Project (Parts Issues) |
Operations and Maintenance Procedures |
Focused Communication |
Same Day Requisition Report |
Failure Mode Detection |
Table 1: Analyze Phase Critical Input Variables
Tools used:
FMEA
MSA (Minitab)
ANOVA (Minitab)
Tests of Proportions (Minitab)
Simple Regression (Minitab)
Team Process
Microsoft Excel
Microsoft Power Point
Reliability
In the Plan Development phase of the 4100A reliability study, a FMECA (Failure Modes and Effects Criticality Analysis) was done on the hierarchical model developed in the previous phase. The purpose is to scrutinize each failure mode (known as input variables in six-sigma) identified during the FMEA using the failure effects that were identified in table 2.
During the 4100A project, RCM Cost was used extensively to analyze the failure modes. The above effects were input into the model as were labor costs, material costs, equipment costs, and operational costs. Using Weibull data from the CMMS, and Monte Carlo simulation, the resultant RCM Cost model was used to identify the critical failure modes for analysis. As a result of this analysis, the "critical few" failure modes are identified for optimization.
Tools used:
FMECA
RCM Cost
Weibull Analysis
Monte Carlo Simulation
Team Process
Microsoft Excel
Microsoft Power Point
At this point it is very easy to integrate six-sigma tools and reliability tools. Depending on the project, ANOVA, testing of means and tests of proportions could be used to validate results of the FMECA. Conversely, RCM Cost, Weibull analysis, and Monte Carlo simulation could be used in the six-sigma study to quantify gains and optimize strategies.
Improve Phase Six-Sigma
The purpose of the Improve Phase is to identify and verify optimal operating conditions for each of the critical process variables identified during the Analyze Phase. This is typically done through the application of structured analysis tools like DOE (Design of Experiments), Pugh Analysis, system constraint analysis, or modeling. Table 3 summarizes the work completed during the Improve Phase of the same day requisition improvement project.
Tools used:
Brainstorming
Modeling
Team Process
Microsoft Excel
Microsoft Power Point
Reliability
Once the RCM Cost model from the previous phase is completed, it is possible to determine the optimum maintenance strategy. Strategies such as: Run-To-Failure, performing Preventive Maintenance Tasks, or Predictive Maintenance Tasks are considered. Picking the correct strategy is crucial since over-maintaining assets costs excess maintenance dollars and often leads to decreased availability due to induced infant failures, and under-maintaining assets results in more frequent failures, higher levels of chaos, and higher overall costs. The goal is to find the point where the combined costs of maintenance activities and costs of failures are minimized. The RCM Cost model, using Monte Carlo simulation, makes this task possible (Keeter, 10). This minimized point from RCM Cost for Swing Blower failures is illustrated in Figure 7
Three models were generated for the 4100A shovels. The first was Run-To- Failure, the second was current practice, and the third was the optimized strategy. The model was generated over a lifetime of 100,000 hours of operation. Table 4 below shows the results of comparing run to failure, the current maintenance strategy, and an optimized maintenance strategy.
In addition to optimized tasks, the reliability study targets areas for possible redesign, and items/issues that required RCFA. Many of the items requiring RCFA will become more focused six-sigma projects.
Tools used:
RCM Cost
Modeling
Team Process
Microsoft Excel
Microsoft Power Point
Once again, the two initiatives have similar tools and methodologies, the difference being the scope and depth of the project.
Control Phase
Six-Sigma
The five deliverables of the Control Phase are:
1. A completed project plan that focused work efforts upon placing the critical input variables identified in the Analyze Phase to their optimal operating set points determined in the Improve Phase.
2. An active Control Plan that ensures critical process variables remain at their set point levels across time, crew, and environmental change.
3. A well-defined Response Plan that focuses corrective actions in the event that a critical process variable drifts from its optimal setting.
4. A data based verification of project improvements / gains (i.e. comparison of current performance against stated goals).
5. The submission of KOIS Project Initiation forms for potential projects / improvements that were identified as a result of this work effort.
Completed Project Plan
During the Improve Phase, work efforts defined the optimal set points for the critical input variables. These actions were incorporated into the existing Project and all required work was completed.
Control Plan
The Control Plan is a formal document that summarizes the minimal activities / responsibilities that are needed operate the process in a state of control (i.e. the process output always meets or exceeds customer expectations
Response Plan
When the Control Plan detects a process drift or an out-of-control condition, corrective action must be taken. Response Plans direct and focus these actions to minimize COPQ losses (downtime, lost product, etc.).
Verification of Gains
After implementing the identified improvements for the same day requisition (SDR) project, a second capability analysis was performed to verify gains. Graphs illustrating BEFORE and AFTER performance of the process are shown in Figure 8. The reader will note that process yield increased by a factor of 5, (9% to 46%). This is an impressive improvement, but in and of itself does not show the annualized financial gain to the concentrator.
However, Figure 9 shows the improvement in the primary metric before and after the project started.
A two-proportion test was then run on the summarized data. The null hypothesis was that the SDR% was equal before and after the start of the project. The alternative hypothesis was that the SDR% before was greater than the SDR% after. The P value was low, so the null hypothesis was rejected. The SDR% before the project started was statistically greater than the SDR% after the project started.
The concentrator cost accountant was in agreement that each 1% drop in SDR% is valued at $480.38 in monthly savings. This means the 30% decrease associated with this project is worth $173,000 on an annualized basis. In addition, the secondary metric was not negatively affected by the improvement as shown in Figure 10.
Identification of Potential Future Projects
While working on this project, two potential improvement efforts were identified. Facts about these projects are provided in Table 5.
Tools Used:
Minitab
Microsoft Excel
Microsoft Power Point
Control and Response Plan
Reliability
In the final phase of the reliability study, the goal is to assist in executing the plan while working to turn it over to the maintenance department (process owner). This is done by updating documentation, providing guidance in modifying the CMMS, monitoring the solutions, providing training/communication, and evaluating the effectiveness of the optimized plan.
In addition, long-term support is needed to embed the changes in the maintenance organization. The reliability engineer will audit, review, and improve the plan until it is embedded. The engineer will assure the optimized plan is used, assure the optimized plan works, conduct RCFA on failures, update documentation in the RCM software, and document actual savings.
The implementation plan was developed by examining the current maintenance practices and comparing those against the optimized program. By subtracting the optimized lifetime cost from the current practices lifetime cost, the lifetime opportunity savings was found. There were 35 practices identified as having an opportunity savings. These 35 were put into a Pareto analysis. It was discovered 85% of the savings could be realized by completing the first 16 tasks. In addition, the optimum PM interval was determined and is part of this implementation. The A-PM (long) and B-PM (short) principle was also implemented. Figure 11 shows a Pareto of these opportunities. Table 6 shows a list of the optimized strategy and RCFA opportunities on the 4100A shovels. Table 7 shows the Redesign Opportunities. Figure 12 shows the improvement in 4100A fleet Availability.
Fig 12: 4100A Fleet Availability
In the end, the final step of the reliability study looks much like the output of the six-sigma control phase. The two main differences are 1) Scope, and 2) the Kennecott Maintenance System requirement that calls for the reliability study to be performed on critical equipment every three years, thus ensuring the optimized strategy is followed and continually improved.
Conclusion:
Six-Sigma and Reliability have much in common. Both use statistical analysis to base decisions. Both rely heavily on teamwork, and involvement of the end user. Both have a structured approach to problem solving that is very similar. In addition, both have an audit, or control, phase to assure long term sustainability of optimized solutions. In fact, many of the tools used are sometimes very similar, and in many cases interchangeable. It is the author's opinion that it would be wise to integrate six-sigma tools into reliability, and reliability tools into six-sigma, as is being done at Kennecott Utah Copper. In fact, at the Refinery, the Manager is so confident in the six-sigma program, he has made a commitment to have his Reliability Engineers all receive green belt training. Recently, the Smelter requested a special green belt wave be launched for all reliability engineers.
The main difference is in the scope of the projects. Six-Sigma focuses on a very specific problem while Reliability looks at a wide area. In six-sigma, the black belt is taught to narrow the focus. In reliability engineering, the reliability engineer sets system limits on his project based on the largest area of focus that can be practically analyzed. Regardless of the process used they both have a place, and coexist, at Kennecott Utah Copper.
About the Author:
Lynn Nelson began his career at Kennecott in 1969. His first position was in the clean-up department at the Magna concentrator. Lynn worked various operations and maintenance jobs over the years until 1984, when he became the victim of layoffs caused by a depressed copper market. While on layoff status, Lynn continued his education earning a bachelor degree in Electronic Engineering from Weber State University in 1989, where he graduated Cum Laude. He returned to Kennecott's Bingham Canyon Mine in 1990, where he has since held the positions of Maintenance Engineer, Senior Electrical Engineer, Field Maintenance General Supervisor, Electrical Superintendent, Maintenance Support Superintendent, and Senior Reliability Engineer. He is presently working as a Six-Sigma black belt and Master Black Belt in training with ties to maintenance and reliability. Lynn recently graduated with honors from the University of Phoenix with an MBA degree in Technology Management. Lynn served as President of the Western Mining Electrical Association from 1999 through 2001. In October 2002, Lynn was recognized by the Society for Maintenance and Reliability Professionals as a Certified Maintenance Reliability Professional (CMRP). In May of 2006, Lynn was also recognized by Rio Tinto / Kennecott as a Certified Six-Sigma Black Belt.
References
1. Breen, Aaron (2004). An Overview of Six Sigma. Internal KUC training material, pp. 1 - 10.
2. Keeter, Bill (2003). P&H 4100A Modeling Report for KUCC. ARMS Reliability Engineers report of KUCC project, pp. 1-20.
- Reliabilityweb Stop Making New Year’s Resolutions and Start Scheduling New Levels of Reliability Performance ›
- Reliabilityweb Managing the Risk of the Schedule Using Monte Carlo Simulations ›
- Reliabilityweb It is impossible to improve any process until it is standardized ›
- Reliabilityweb Right 2 Design for Reliability [DfR]: The 10 Rights of Asset Management ›