Energy-Centered Maintenance: Leveling Up Reliability-Centered Maintenance
Currently, most manufacturing facilities and utilities are focused on reliability-centered maintenance (RCM) for their electric motor-driven machinery. While this is often the appropriate approach for super critical machinery, it is not necessarily the best approach for somewhat critical or less critical machinery (critical from a downtime point of view). As an example, a typical pump that had an impeller caused imbalance, which was detected within two weeks of installing a wireless monitoring system, but did not have high enough vibration to cause a concern, ran for two and a half years without any signs of catastrophic failure. As soon as the imbalance, which was a manufacturing defect, was removed, it decreased energy consumption by seven percent on a 250 horsepower pump. If this excessive power consumption was detected two and a half years ago, it could have saved over $100,000 in lost energy.
More than 90 percent of the lifecycle costs of motor-driven machinery are due to energy costs, while the cost of the motor, maintenance and installation itself are just five to seven percent of the overall lifecycle costs. Not every piece of equipment leads to downtime on an annual basis, thus downtime related return on investment (ROI) can take longer to justify. Because of this, to keep lifecycle costs of operating motor-driven machinery low, regular maintenance is required to ensure its energy consumption is as consistent or optimized as possible.
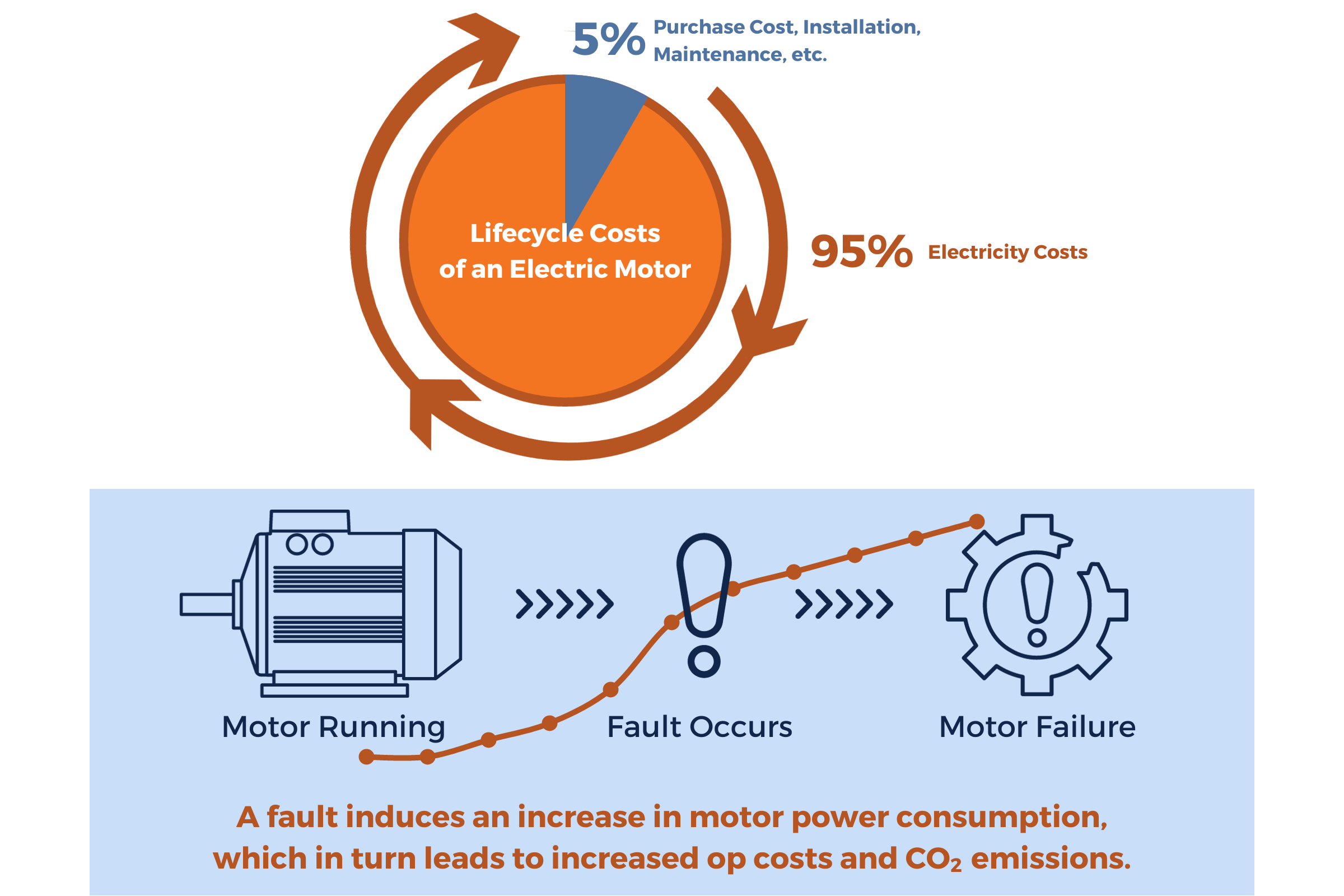
There are four kinds of maintenance programs for electric motor-driven machinery, such as pumps, compressors, turbines, gearboxes, fans etc.:
- Reactive – Run the equipment to failure and replace
- Preventive – Regular planned maintenance, irrespective of the condition of the machine
- Predictive – Predict the condition of the machine based on the current diagnosis and recommend a maintenance need for the machinery, alternatively called condition-based maintenance
- Prescriptive – Find out the root cause of the issue and prescribe an appropriate action to fix it. Figure 2 shows how maintenance approaches can be broadly categorized.
Reliability-Centered Maintenance (RCM)
RCM is a maintenance planning approach that ensures systems continue to do what’s required of them in their present operating context. Successful implementation of RCM leads to an increase in cost effectiveness, reliability, machine uptime, and a greater understanding of the level of risk that the organization is managing. With RCM, maintenance is done mostly to keep the machine running. Unfortunately, an RCM specific approach that also monitors energy efficiency has never been done.
Total Productive Maintenance (TPM)
TPM is when “productive maintenance carried out by all employees through small group activities....” with the goal of maximizing equipment effectiveness. To achieve this, TPM starts by identifying the six losses with respect to equipment. The overall equipment effectiveness (OEE) is used as a key performance indicator in TPM implementation. However, in recent TPM development and implementation, there are 16 loss types that fall into four categories:
- Losses that impede overall equipment efficiency
- Equipment loading time
- Worker efficiency
- Efficient use of resources
The last category includes yield loss, consumable loss and energy loss. Recent case study examples for the implementation of TPM show a manufacturing company in Japan reducing energy consumption by 30 percent and a steel manufacturing plant reducing its energy cost between eight and 27 percent.
More than 90% [1] of the lifecycle costs of motor-driven machinery are due to energy costs, while the cost of the motor, maintenance and installation itself are just 5-7% of the overall lifecycle costs.
Energy-Centered Maintenance (ECM)
ECM is a maintenance concept focusing on energy consumption reduction. Energy consumption excesses or energy waste are used as the primary criterion in determining the specific maintenance or repair needs. ECM consists of six steps:
- Energy-related equipment identification
- Data collection and baseline prediction
- Development of an ECM inspection plan
- Equipment performance monitoring and baseline comparison, with any deviation requiring a root cause analysis for improvement
- Selection of required maintenance action to restore equipment efficiency
- Improvement of maintenance plans
A recent case study of ECM application in a facility claimed that it could help reduce energy consumption by as much as 30 percent.
More than 60 percent of global electricity consumption is due to motor-driven machinery. Around 25 percent of the energy consumed by motor-driven machinery is due to frictional losses, which are unavoidable, but this increases to 35 to 40 percent or more as soon as there is a fault in the machinery. Table 1 provides a range of energy consumption increases due to various fault modes. Measuring this requires a high-quality, incredibly accurate solution that leverages both a custom hardware and unique software that does not need too much time to learn the equipment’s patterns.
Ideally, an ECM hardware solution would be a wireless Industrial Internet of Things (IIoT)-based sensor that features:
- The ability to solve connectivity issues without depending on a router or gateway
- Optimized power consumption with a large, built-in battery and edge programming
- The overall sensor housed in a form factor that makes it easily installable in more than 95 percent of machine locations
- A single sensor that gathers data using a wide variety of parameters, such as acoustic emission, magnetic flux, vibration, revolutions per minute (RPM), temperature and humidity
ECM software should have the following key attributes:
- The ability to consider the physics or domain knowledge behind the various fault modes
- Driven by artificial intelligence (AI) so that detection, prediction and prescription is fully automated
- Highly accurate anomaly detection, with more than 95 percent confidence
- Accurate fault diagnosis, with more than 99 percent confidence and the ability to predict remaining time to failure based on fault mode
- The ability to pinpoint the root cause and associated action point so action can be taken to prevent future faults in the short term
- The ability to detail the incremental energy consumption caused by the fault mode as compared to the baseline energy consumption after accounting for load changes
- In the following case study, one can see why energy-centered maintenance can achieve the kind of savings that may not be possible with standard RCM techniques
Case Study
A 250 horsepower pump was running in an airport for almost two years without issues. However, as soon as the IoT-based wireless sensor was installed on the motor and pump, a peak on the vane pass frequency (VPF) in the vibration fast Fourier transform (FFT) spectrum from the pump drive end side was noticed in the first two weeks.
VPF = RPM * No. of vanes on the pump impeller
More than 60% of the global electricity consumption is due to motor-driven machinery.
Although there was an excitation at pump vane pass frequency, the overall vibration was still within reasonable limits, as shown in Figures 4 and 5.
The maintenance technician opened the pump during a normal planned maintenance window and observed that one of the vanes on the pump impeller was not constructed properly, causing a slight imbalance when the pump was running at high speed (1780 rpm). The imbalance was not high enough to show high vibration overall, but was strong enough to show a peak at vane pass frequency.
The technician did some metal work and shaved off the extra piece of metal and made all four vanes symmetrical from all sides. Coincidentally, this not only resolved the vibration at vane pass frequency due to imbalance, but also reduced the energy consumption of the pump and motor by as much as seven percent.
ROI from ECM vs RCM
In examining the numbers, it clearly shows why energy-centered maintenance would have flagged this within the first few weeks of operation, while RCM would have let it go unnoticed. Also, it explains why ECM would have provided much more ROI, as compared to a standard RCM approach.
- Correlation between power consumption or magnetic flux and amplitude at vane pass frequency > 95 percent
- Time to prove this correlation and notify airport technician ~ 2 weeks
- Let’s reasonably assume that user takes an action two weeks after notification
- Cost of the pump and motor assembly – $25,000
- Percentage decrease in power consumption after correcting impeller manufacturing defect – seven percent
- Time since the pump installation and airport installed condition-based maintenance system – 24 months
- Total energy savings for the airport if monitoring system was installed to achieve ECM:
- (24-1) months * 30 days/month * 24 hrs/day * 0.07 (seven percent increase in power consumption) * 250 HP
* $0.20/kWh)/0.65 (average efficiency of the pump during these two years) = $100,000
Since correlating fault mode to energy consumption, any increase in fault mode can easily make the software trigger the alarm in advance and help to save the potential unbalanced downtime that could be caused due to the pump vane pass failure.
- Total cost of downtime – $10,000 (at max as there is a standby pump, cost of the pump is $10,000)
- Cost of condition monitoring solution to user – $1,400/annum/equipment
Assuming the failure happened within two weeks of installation, monitoring system after two years, and notification and action taken by customer based on RCM approach:
- ROI from RCM in saving downtime – 3.57x
- ROI from ECM in saving energy and downtime ~ 40x (best case scenario)
- ROI from ECM in saving energy and downtime ~ 20x (best case scenario if the pump was changed one year after the monitoring system was installed)
To keep lifecycle costs of operating motor-driven machinery low, regular maintenance is required to ensure its energy consumption is as consistent or optimized as possible.
Conclusion
The merits of energy-centered maintenance over traditional reliability-centered maintenance are too big to be left unexplored. Users can expect the following advantages from an ECM approach:
- Energy consumption reduced or, at the very least, optimized
- Manufacturing defects can be easily identified
- It helps to justify a much stronger ROI case, and time to ROI is greatly reduced and valid for all equipment
- It helps to justify ROI, even if the machine has already gone to downtime
An ECM approach provides more than five times the ROI from an RCM approach, and almost 10 times in a best-case scenario. Even in the worst-case scenario, an ECM-based approach will deliver as much ROI as an RCM approach because the objectives you want to achieve through RCM will be easily achieved with ECM if the appropriate technology is used.
References
- Singh, Gurmeet, Kumar, T.Ch. Anil, and Naikan, V.N.A. “Efficiency monitoring as a strategy for cost effective maintenance of induction motors for minimizing carbon emission and energy consumption.” ScienceDirect, January 31, 2019. https://www.sciencedirect.com/science/article/abs/...
- Firdaus, N., Samat, H.A., and Mohamed, N. “Maintenance for Energy Efficiency.” 2019 IOP Conference Series: Materials Science and Engineering. https://iopscience.iop.org/article/10.1088/1757-899X/530/1/012047/meta