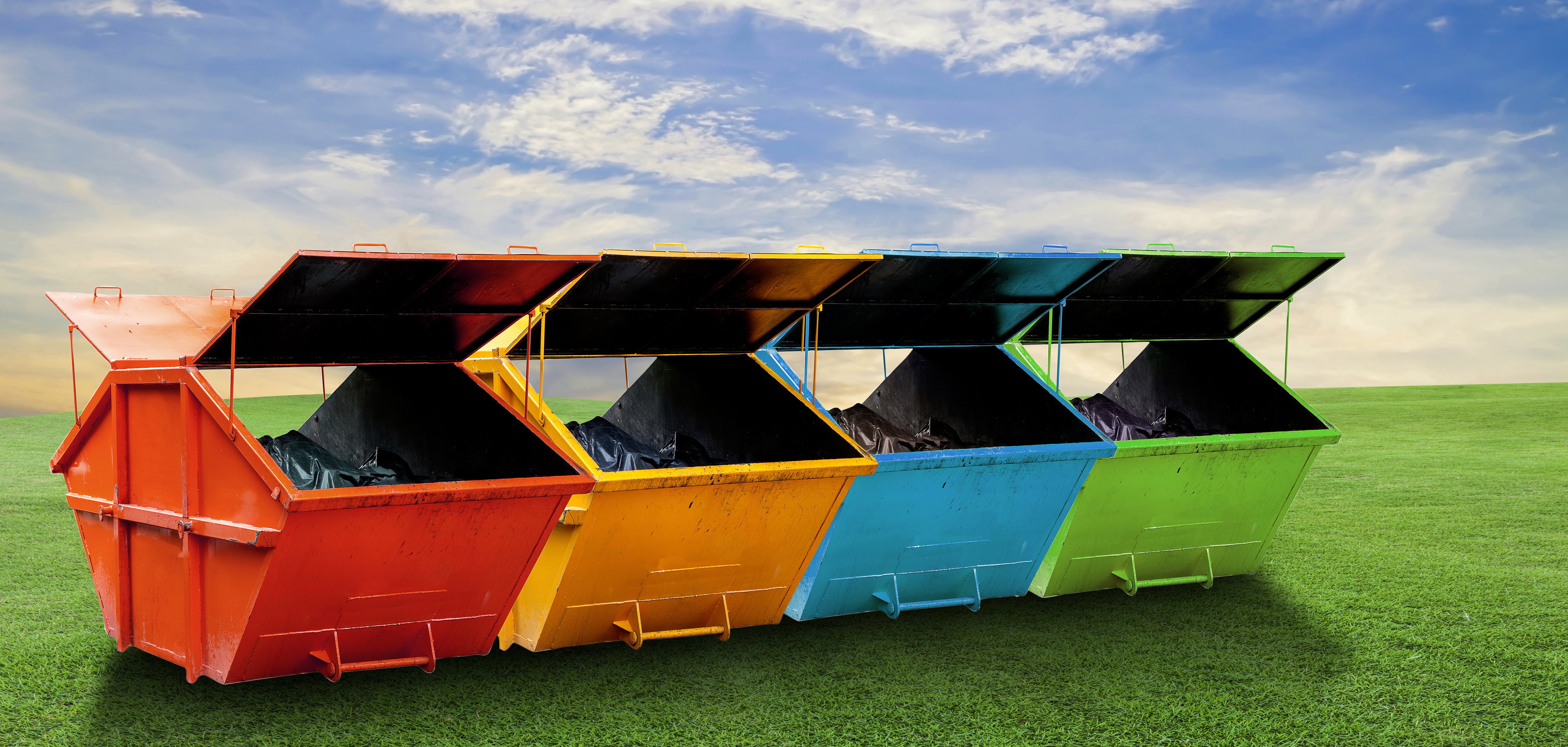
Author’s Note: Growing up in a home of meager means with an older brother very close in age, it was important to ensure that any special treats were distributed equally. Among other things, my brother and I learned to look in the trash if we were ever separated and you just might receive a special reward. This technique must have followed me to my industrial maintenance and reliability career. This article is an attempt to share a very simple, no cost method of assessing what is going on at a site or in a department. It’s a practice I call, “Look in the Dumpster.”
The definition and concept of reliability remains elusive in terms of application. Ask as many folks as you can to explain what reliability means to them or their situation and the responses will vary wildly. This can be especially nebulous among the decision makers for resource allocation, but what they usually want is lower costs and more quality output.
Much has been written and proven beneficial with respect to doing things right in terms of asset care. Most, if not all, methods and philosophies require dedicated resources of material, manpower, C-suite support, training and execution discipline to even get close to improving or extending industrial asset life and performance. If those resources are at your disposal, then apply them and continue your journey along the maturation path of greater mean time between failures (MTBF), utilization and overall equipment effectiveness (OEE). If the resources are not at your disposal, here’s a simple way to gain insight into what is happening at your site or department – look in the dumpster! What you learn may be valuable in gaining information to convert into action for improvement and better reliability.
Here’s a simple list of what to look for when rummaging through the dumpster and what could be suggested for improvement.
Is there anything new or unused?
If there are new items in the dumpster, question why:
- Were they ordered wrong?
- Were too many requested?
- Is it too difficult to return unused items to stores or suppliers?
- Is the bill of material (BOM) wrong?
- Has the machine or part been out of service for an extended period?
Are there items that appear to have remaining life?
If there are items that appear to have remaining life, question why they were replaced:
- Could there be other premature failure mechanisms?
- Could preventive maintenance (PM) plan intervals be excessive?
- Could there be poor definitions of failure?
- How premature are the failures?
- Can the age of the material be determined?
Is there more than one of the same part?
If there is more than one of the same part, question why there are two or more.
- Could this be a chronic issue?
- Could this be a design issue?
- Could this be an operational issue?
- Could this be a purchasing issue?
- Could this be a maintenance issue?
Is there any evidence of having the wrong material?
If there is evidence of wrong material, try to determine whether it is due to:
- Corrosion – Oxidation or chemical attack failure
- Erosion – Wear failure
- Fatigue – Cyclic failure
- Overload – Instantaneous failure
Have the components been disassembled for autopsy (root cause) inspection?
If assemblies have not been opened for inspection, question the support, expectation and encouragement to do so:
- Does the work order expect an autopsy?
- Is there any curiosity to examine for root cause?
- Does the work order closure debrief session determine what was observed?
- Does it appear to be a replace rather than a repair strategy? If so, why?
What are the differences in area dumpsters?
If there is more than one disposal container, check them all:
- Does one area discard components that appear newer than another?
- Does one area have more electrical related parts?
- Does one container have lubrication related evidence?
- Do multiple areas have the same components?
What crafts contribute the most content?
Try to determine who placed the material in the dumpster:
- Are the items mostly piping and related fittings?
- Are there a lot of shafts, bearings and belts?
- Are there wiring and fuses?
- Are there gauges and instruments?
- Is there insulation?
- Are there empty grease cartridges?
- Are there bolting fasteners?
- Is there sheet metal or ductwork?
Is there any evidence of poor craftsmanship?
Look for mishandling:
- Are there jaw marks on shafts?
- Are there old hammer marks?
- Is there evidence of poor rigging practices?
- Are there damaged tools?
This list of things to look for when examining a site’s maintenance dumpster is offered as a start to determine what is normally going on with current expectations and practices. If used as a checklist, it should lead to more specific questions and reveal any patterns, symptoms and opportunities for improving equipment reliability. Beyond what can be learned from a dumpster dive, the challenges of resource commitment could become a boundary. Once armed with physical evidence of poor practices, premature failures, chronic poor performance, inadequate training, or poor operation, support should be easier to obtain, especially if you link it to lower costs and higher output.
Here are some scenarios the dumpster may help reveal:
- There are pipe wrench marks on the shafts that may indicate the process is causing a blockage that needs to be manually cleared. If the process cannot be adjusted to prevent those occurrences, then a nondestructive tool, such as a strap wrench, could be used in lieu of a pipe wrench.
- If there is a broken shaft, it may be the result of a start-up issue or an overload condition. If it can be determined when it occurred, a solution could be offered that may include a soft start, rotate by hand technique before starting, or a variable frequency drive (VFD) to eliminate the start-up or overload condition.
- If all the bearings or seals have excessive grease or if there is grease everywhere, this could be a training opportunity. Excess grease creates excess heat and destroys the lubricant. Perhaps a bearing should have a red grease and the dumpster content has a green grease. Could that be the reason for the dumpster fodder?
- There are wear parts, such as seal materials, that could benefit from a material change or better installation instructions.
- If the dumpsters are always full and overflowing, this could be a manpower assignment or scheduling issue. What can you discern from a scenario where something should be in the dumpster, but is nowhere to be found? Could that be a culture that assigns blame or is there something to hide?
Here are some actual findings at dumpsters in manufacturing facilities:
- One area of the site had multiple 10 hp motors in the dumpster. Could these failures with a short MTBF be an operational issue or a design problem? Things that are chronic typically have a good payback when resolved.
- An aluminum tube manufacturer found a large amount of machine tool cutting inserts in the dumpster. Why are so many inserts being consumed? The answer has the potential to lead to an improvement.
- A medical device manufacturing site found a motor in its dumpster with the shaft exposed. When a gloved hand attempted to rotate the shaft to ascertain if it was in there because it had seized, the glove returned coated with oil. Why is a motor shaft oily?
Depending on your specific circumstances, practices, work management processes and execution discipline, there could be other revelations that are uncovered for no cost or additional resources by simply looking at a lagging indicator of what is going on based on hardware consumption.
Looking in the dumpster can provide quick insight into your site and its practices. Please share what you discover from your dumpster inspection: crm@reliabilityweb.com.