Westar Energy is an investor-owned electric utility headquartered in Topeka, Kansas. The company serves more than 680,000 customers in Eastern and Central Kansas with reliable low cost energy. Our energy centers in 11 Kansas communities generate more than 7,000 megawatts of electricity and employ about 2,400 people. Westar uses a variety of electrical generation technologies, including coal (48%), natural gas (38%), nuclear (8%) and wind (6%).
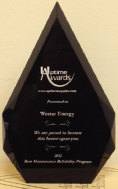

Employees at the company’s power plants execute more than 35,000 work order tasks, 7,000 schedules and 16,000 purchase orders annually and have worked accident free over the year and a half, which is about 1.7 million man-hours.
Managing a generating fleet in the utility industry today provides many challenges, some common to other industries and some unique. The maintenance professional’s daily charge is to appropriately balance the needs of the customers, shareholders and employees. Shareholders benefit from maintenance cost savings, while customers benefit mostly by reliable and efficient operation. The operations and maintenance workforce must make the most effective use of maintenance dollars while ensuring reliable operation.
Murray Gill Energy Center - Natural Gas
“Westar believes deeply that good reliability programs benefit our customers, employees and our shareholders. Planned maintenance identified by predictive methods is simply less expensive and safer than unplanned work," says John Bridson, VP Generation.
Some of the realities at play in our work environment today emphasize the need for a comprehensive reliability strategy.
Gordon Evans Energy Center - Natural Gas
- Worker safety is our highest priority. A planned, proactive maintenance strategy is critical to success.
- Dramatic increases in regulation dictate the use of financial and human resources toward compliance, sometimes at the expense of reliability.
- Nearly half of our workforce will retire in the next five to 10 years. There is a need to capture and pass along the knowledge of an aging workforce.
- There is very low growth in electric demand. Commercial and industrial demand is down. Costs are rising, but revenues are not increasing.
- Maintenance costs are the highest controllable costs in most companies today. There is pressure to hold operations and maintenance costs flat year after year.
- Construction, operations and maintenance strategies must maximize uptime and minimize lifecycle costs for increasingly complicated systems.
- All activities, including reliability initiatives, must be effectively targeted to provide the greatest value for customers and shareholders.
This article will outline some of the strategies Westar is using to address these challenges in its effort to move toward maintenance excellence.
Post Rock Wind Farm
Predictive Maintenance
The Westar generation department’s predictive maintenance program began in 2001 with two vibration technicians and an oil analyst. The effort was focused on building a comprehensive program with routes and defined alarm points. Over the years, other technologies have been added to the program. The predictive department has grown to five vibration analysts, one thermographer, one oil analyst, two electrical testing personnel and two boiler inspection coordinators. The practitioners are typically certified in multiple technologies.
The following sub-programs make up the Westar generation predictive maintenance program.
VIBRATION ANALYSIS
Vibration analysis is routinely conducted on over 16,000 points across the fleet using six 2130 analyzers. Vibration analysis is a widely used predictive tool for a number of reasons. Vibration anomalies are detected early on the P-F curve. The technology is non-destructive and detects a wide array of mechanical and electrical anomalies. Analysts also use operational deflection shape software to show 3D modeling of the various stress points. It has proved to be a great tool for a less technical demonstration of vibration issues.
LUBRICATION EXCELLENCE
Lubricant storage, handling and testing are major parts of the Westar reliability effort. Consolidating lubricant types, labeling lubrication points and routine testing are all components of the current five-year lubrication plan. An on-site lab provides particle count and monitors lubricant health for the entire fleet. The lab provides full analysis of about 2,000 samples annually. Analyses includes viscosity, particle count, water content, total base number and spectral analysis capable of identifying 20 different metals. The oil lab also provides Ruler™ and varnish potential analyses on approximately 600 samples annually. Westar has over 30 certified machinery lubrication technicians (MLT1).
THERMAL IMAGING
Thermal imaging is used in a variety of applications. The technology is non-invasive and can evaluate a lot of assets quickly.
Electrical infrared (IR) is used throughout the plant’s electrical distribution systems.
Mechanical IR is used to assess slag buildup in coal-fired boilers. Insulation assessments on the boiler are also conducted using thermal imaging.
Emporia Energy Center - Natural Gas
Infrared imaging is also used for leak detection. Scans of hydrogen and natural gas piping systems have detected leaks that could have resulted in fire or significant loss. We also scan for sulfur hexafluoride (SF6) leaks from high voltage electrical apparatuses.
Most recently, we have added a camera that detects corona in substations. Invisible to the naked eye, corona is micro-arcing that occurs on electrical apparatuses that can indicate faulty equipment.
ULTRASOUND
We continue to find new uses for airborne and contact ultrasound. We routinely use ultrasonic emission lubrication to lubricate electric motors. An experienced lubrication tech using a UE “grease caddy” typically can pick up bearing defects before vibration analysis. Over-greasing of motors has been largely eliminated where UE lubrication has been applied.
Lawrence Energy Center - Coal
Periodic ultrasonic audits are conducted to detect internal and external process leakage.
BOILER TUBE THICKNESS TESTING
The boiler tube thickness program has had perhaps the largest impact of any of our predictive efforts. Time between unplanned outages caused by tube leaks has increased exponentially. The program uses ultrasonic thickness testing of boiler tubes in areas that are known to have higher rates of erosion or corrosion. Plant operations personnel using modern, route-based data collectors collect between 5,000 and 20,000 ultrasonic thickness readings as early as possible in a planned outage. The program identifies tube wall thinning early in the outage to ensure that identified tubes can be repaired before outage completion. The data is stored in a database that is used to compare historical failure data and predict future maintenance needs.
CONVEYOR BELT THICKNESS TESTING
Ultrasonic thickness testing is also performed on conveyor belts. Trending belt thickness on more than seven miles of conveyor belting has provided data to plan future belt replacements. We expect the result to be elimination of catastrophic belt failures.
MOTOR CURRENT ANALYSIS
The first motor current analysis test set went into service in 1999 and we now use six PdMA MCEmax™ sets in the fleet. Currently, 1,189 motors are in the program. The motor current analysis test is able to detect cable faults, winding faults, insulation to ground faults, air gap problems and rotor bar problems.
GENERATOR ELECTRICAL TESTING
Partial discharge testing began at Westar in 1994 and is used for monitoring and assessing the condition of generator stator windings. Stator winding insulation failure is normally the result of a deteriorated winding that has been subjected to extreme stress, such as lightning strikes, out-of-phase synchronization, excessive starts, or system imbalance. It is virtually impossible to forecast when a failure will occur, however, by monitoring the partial discharge characteristics of a stator winding, it is often possible to determine which machines are more susceptible to failure so maintenance activities can be prioritized.
Flux probe analysis has been in use since 1998 and is used to pinpoint the number and location of shorted turns in the rotor. Shorted turns will cause an increase in the field current at any given load. The higher field current will result in heating that impacts the life of the rotor insulation. Flux probe rotor information is vital when determining generator maintenance strategies.
MOTOR-OPERATED VALVE TESTING
Motor-operated valve testing began in 2006. The diagnostic test uses a strain gauge to determine the condition of the valve and actuator by monitoring the signals representing stem thrust and torque, spring pack displacement, motor current, control switches, differential pressure and flow rates. The data is used to determine operability and to pinpoint problem areas in the valve and actuator that require maintenance.
Tecumseh Energy Center - Coal and Natural Gas
CONTROL VALVE TESTING
The ValveLink™ testing program is administered by instrument and control technicians at each plant. It is used to assess control valve performance. Asset criticality of the valves governs the amount and interval of testing. The process calibrates and diagnoses the condition of each valve and can be performed online.
STATION BATTERY TESTING
Battery impedance testing is a non-destructive test to evaluate the condition of battery cells. Assessment of over 70 battery sets in the fleet is crucial in maintaining emergency capability. The data is used in forecasting needed maintenance and replacement.
TRANSFORMER TESTING
Transformer testing is conducted on all major oil-filled transformers. The oil-filled transformer test analyzes the transformer oil for dissolved gases. The analysis provides an indication of insulation breakdown. High potential testing is only conducted on new or reconditioned windings.
Oil-filled transformers are desirable for their efficiency, smaller footprint and longer life. However, more stringent fire codes have driven the installation of more dry transformers. A dry transformer test program was recently developed to evaluate insulation integrity, as well as winding resistance and impedance.
COAL MILL ROLL BOWL TESTING
“Roll Bowl Cop” testing is a predictive technology that uses linear displacement transducers to assess the condition of coal grinding equipment. The coal mills powder the coal that is burned in coal plant boilers. The tests provide early indication of problems with the coal mill rolls and springs. These problems can impact combustion efficiency and can lead to load reductions, unit outages and major damage to the coal mill.
Jeffrey Energy Center - Coal
Reliability Engineering
The reliability engineering group was formed in 2004 with three engineers. Today, the group has grown to four engineers who develop and evaluate effective maintenance tactics aimed at doing the right work at the right time. The group seeks continuous improvement and is driven by sound reliability principles. The engineers employ a number of reliability tools in the program.
RELIABILITY CENTERED MAINTENANCE (RCM)
To date, we have completed around 50 analyses. Some analyses were done on a more generic, fleet-wide basis and adapted to fit each plant’s specific application. Reliasoft RCM++ was used on all analyses. Completed analyses are accessible to all plants through a common website. Going forward, RCM will be performed primarily on “A” criticality assets and a design RCM will be performed on new equipment and systems.
ROOT CAUSE ANALYSIS (RCA)
Westar uses the TapRooT® system and sets criteria for triggering RCA. Around 200 triggered RCAs have been completed. The RCA meetings are data driven and include the participation of multi-disciplined teams whose goal is to permanently resolve the identified issues.
MONTHLY REPORTING
The reliability engineers perform analysis and generate monthly reports that show trends in corrective work based on cost, work order count and labor hours. They also show progress on current RCA and RCM analyses. The report includes updated “bad actor” rankings and trend analyses on targeted equipment.
STATISTICAL MODELING
Weibull analysis and Crow-AMSAA have been used to help develop maintenance strategies based on the component failure data. Weibull has proved to be a good tool to determine maintenance strategy at the component level and Crow is typically used to assess reliability growth after changes have been implemented.
The reliability engineering department is leading Westar’s “reliability initiative” in generation. The initiative is a multi-year effort designed to build a framework to support continuous improvement that consists of:
- Database development – ensuring that assets and components are set up properly to support further development of procedures, specifications and bills of material.
- Asset criticality ranking of over 8,000 assets – establishes the mission criticality of more than 8,000 assets.
- Predictive maintenance optimization - uses criticality scores to determine which PdM technologies to apply to each piece of equipment and at what interval.
- Preventive maintenance optimization (PMO) – evaluating all existing PM tasks to make sure they add value. If the failure mode a PM is trying to address is appropriate for a time-based PM, the team will determine if the right personnel are doing the right work at the right interval.
- Failure coding – failure codes and root cause data are under development to apply to work order closeout coding. This coding will support statistical analysis and be used to evaluate efficacy of maintenance tactics.
Key Performance Indicators
The saying, “If you can’t measure it, you can’t manage it,” has become cliché in management circles today. The saying may be cliché, but to a degree it’s true. Measuring progress toward defined goals has proved a valuable tool in managing change at Westar.
Westar managers have put mechanisms in place to affect improvement. Armed with a vision for the future, managers agreed upon the characteristics that mark exceptional performance.
Bottom Row – Left to Right - David Ent, Bruce Sackman, Sue Gordon, Tyler Stahly, Jennifer Bisel, Allen Halderman, Lee Pendleton, Joe Brown, Rayme Collins, Jeff Zirkle, Brad Diederich
Top Row – Left to Right - Ken Smith, Mark Mayworm, David Walter, Stacy Warden, Pete Oberthaler, Jennifer Brennan, Ken Rankin, Wes Mizell
Not Shown - Russ Matzke, Afshin Jalilzadeh, Randy Bilderback
Measures used to track progress include:
- Equivalent Unplanned Outage Rate (EUOR)
- Equivalent Planned Outage Rate (EPOR)
- Maintenance rework
- Schedule compliance
- PM/Predictive compliance
- Proactive/Corrective work percentages
- Inventory turns
- Backlog
- PM/PdM results
- Lost margin opportunities
- Benchmarking against industry peers.
The past year was the best in the history of our company in terms of industry standard indicators of reliability. System EOUR hit a record low in 2011. The fleet’s mean time between forced outages continues to increase despite declining budgets. Some of the units have recently achieved record run times.
Sustaining a Culture of Reliability
Changing the generation department’s culture has been no small task. The company has a long and proud tradition of maintenance based on commitment, employee involvement and strong leadership.
“Important business attributes, such as safety, workmanship and leadership, improve with good reliability, along with an overall better culture for continuous improvement and success,” points out Mark Mayworm, Director, Generation Support.
Each employee needs to understand the behavioral changes demanded by the reliability culture. To that end, policies and procedures have been written that communicate the responsibilities of each player in each process. Procedures developed include asset and database development, maintenance workflow, outage planning, RCM, RCA and preventive maintenance.
Upper management supported the vision. With policies and procedures in place, maintenance practices began to change and the culture followed. Today, most employees and all managers are personally involved in some form of a reliability improvement effort. Some of the strategies that led to improved employee commitment are:
- Multi-disciplined teams participating in the reliability initiative (RCM, RCA, asset criticality, PMO, etc.)
- Corporate leadership seminars and training
- Success posters showing team participants and the results of the analysis
- The annual “Reliability Summit” for key players and new employees
- The Reliability Game®
- New engineer reliability training sessions
- Exposure to reliability tools during apprenticeships
- Planning and scheduling interface meetings with all departments.
The correlation between safety and reliability are well established. The generation department recently passed the 1.7 million man-hour mark without a recordable injury. We are very proud of this safety accomplishment and are confident that our continued focus on reliability will yield similar results. The Uptime award does not define the finish line for us. It strengthens our resolve to continue to improve our business processes to ensure that we provide reliable, low-cost energy to our customers. It’s the people of Westar who are making this work. www.westarenergy.com