A perfect storm of technological advances is spurring technician productivity, allowing them to spend less time on their screens and more time on valuable maintenance work.
The percentage of hands-on work performed by technicians each day is referred to as “wrench time”. Most organizations we speak with say their wrench time average falls between 18%-30%.
So what’s are they up to for the rest of the workday? Instead of performing valuable maintenance work, technicians are spending over 60% - more than half their day - searching systems for tools and parts and completing administrative requirements (filing reports, inventory records, and other paperwork).
While screen time represents most tasks that don’t provide value, waiting is another time inefficiency with up to 39% of the day spent waiting on information, equipment, and people. And we haven’t even got to the time spent driving to and from work sites—more low value activity.
And this is what we mean by the perfect storm. Advancements in asset and maintenance management and other technologies optimizes maintenance technicians so they work more efficiently throughout their shift, freeing them to do the highest value work. Here are some real-life examples:
Planning through predictive maintenance
I think we can all agree that maintenance work is complex, particularly when it’s done reactively. Technologies such as predictive maintenance planning break through the reactive cycle with advances in artificial intelligence (AI) and machine learning for operational insights that inform how and when a technician’s time is best used.
Predictive maintenance planning ensures all the tools, equipment, and support are identified and organized in advance, allowing technicians to spend most of their time doing hands-on maintenance tasks and improving asset reliability.
Read the Predictive Service Technology brief from Futurum Research to learn more.

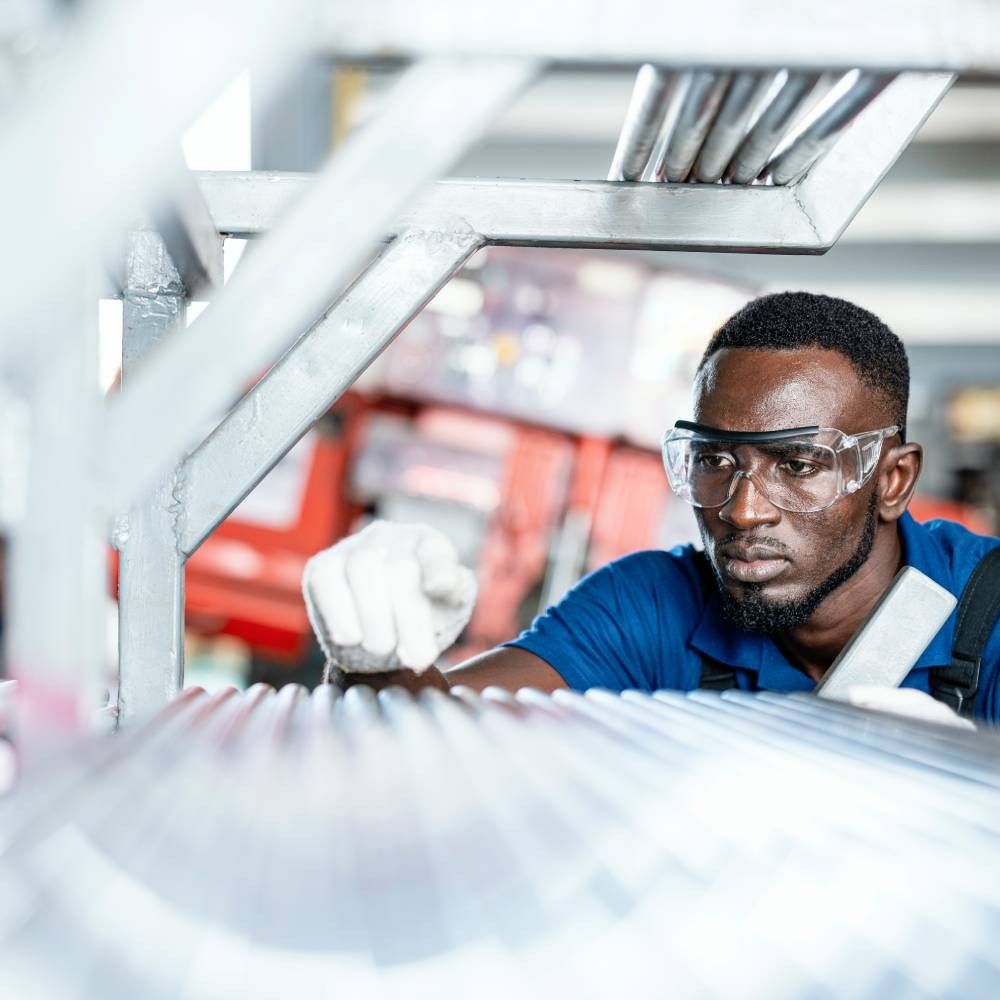
Optimizing technician planning and scheduling
Another advancement in asset and maintenance management technology is leveraging AI-powered automation to continuously improve your maintenance schedules. AI helps prioritize technician work based on work type and precedence, and the critical nature of the work. This automated prioritization is an advantage for asset-intensive industries including refineries and manufacturing plants, where reliability is critical to the business.
This technology can identify the location and availability of the required parts and even considers the best route for the maintenance technician to travel in order to reduce drive time. The efficiencies gained through optimized technician planning and scheduling include increased wrench time and lower costs, not to mention better operating margins. Maintenance details – including parts used and time spent - are automatically brought into backend systems, providing even greater efficiencies by eliminating these administrative tasks.
Read the Planning & Scheduling Optimization paper to learn more.
Providing technicians with remote assistance
In the midst of COVID, one of the most talked-about and widely leveraged digital toolsets was augmented and merged reality tools that enable remote interaction, collaboration, and service. Many had started using augmented reality and remote assistance technologies prior to the pandemic, but those conditions accelerated adoption by organizations that had not yet considered its role in their operations.
Remote assistance technology connects technicians with an expert to guide them through repairs and maintenance work when required – allowing them to continue with high value-added tasks. Without this, the technician is back to wasting time with online searches for manuals and repair information. Along with instant access to an expert, the lessons learned are applied to future jobs, shortening repair times while increasing first-time fix rates.
Read the Remote Service Strategy paper from Future of Field Service to learn more.
These are just a few examples of the technologies that are advancing technician productivity and helping them to spend less time on their screens and more time on valuable maintenance work. By ensuring the workforce is delivering maximum value, organizations can drive better profits, increase operating margins, and improve reliability – and ultimately exceed customer expectations.
Author:
Jon Mortensen, Global CTO EAM, IFS
As Global Chief Technology Officer for Enterprise Asset Management, Jon Mortensen is responsible for setting the vision and direction of asset management at IFS. Jon's software journey started over 30 years ago within the local government utility space where he garnered an appreciation for asset intensive businesses with huge service deliverables and constrained revenue streams. This knowledge drives Jon’s passion for leveraging data with explainable technology to drive efficiency and reduce risk, while improving the reliability and availability of the assets that drive business outcomes.
This Sponsored Industry Article is brought to you by
* The opinions expressed herein are not necessarily those of Reliabilityweb.com.
- IFS positioned as a Leader in IDC MarketScape for Worldwide Manufacturing Service Life-Cycle Management ›
- Indycar Racing team AJ Foyt Racing selects IFS Ultimo EAM software for critical Parts Management, Lifing and Maintenance processes ›
- IFS Acquires Poka ›
- IFS delivers 38% YoY revenue growth with sharp rise in demand for its AI capabilities ›
- Mark Moffat Appointed as CEO of IFS ›
- IFS acquires ULTIMO ›