LOOP's 5-Year Successes in Repair Cost Reduction and Uptime

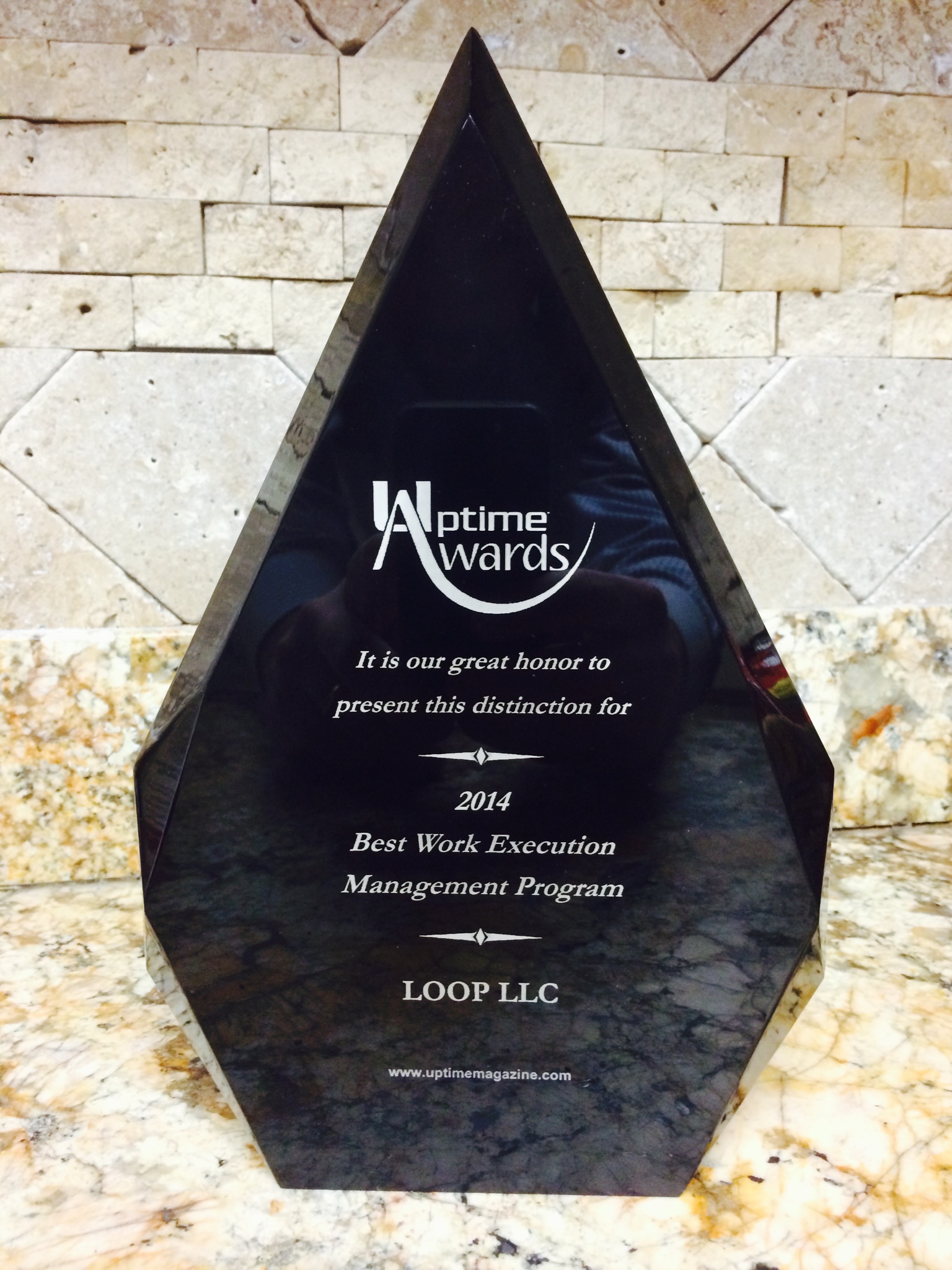
• Repair cost and equipment uptime are two metrics used to measure the effectiveness of reliability centered maintenance and related asset and work management programs and procedures.
• LOOP realized a 4-year low in repair cost in 2013, ending the year over $2 million less than 2012. Related expenditures dropped again by nearly 50 percent in 2014.
• Less reactive work allowed for more proactive work, reducing the maintenance work order backlog while improving our main oil line (MOL) uptime to 99.75 percent.
• LOOP's MOL uptime has exceeded 98 percent for over 5 years.
• Results are proving to be sustainable.
The Journey to Operational Excellence (OpEx):
LOOP LLC is a crude oil pipeline and storage company, with onshore and offshore facilities in southeastern Louisiana serving as a vital energy hub with pipeline connections to a significant portion of our nation's refineries. The majority of our operating facilities were designed in 1978 and placed in operation by 1981, so most of our MOL assets have been in operation for over 30 years. We can store over 60 million barrels of crude in below ground caverns and an additional 9 million barrels in above ground tanks. Our unique pumping systems can transport crude at rates in excess of 100,000 barrels per hour on multiple, interconnected pipelines.
Since 2011, LOOP has created and followed a new vision of becoming market driven and operationally excellent. Related strategies and tactical objectives were developed and implemented. The uptime, or availability of assets, is a key performance indicator (KPI) for LOOP and considered a critical component of our business performance to our customers. Uptime, therefore, aligns with our vision. Our proactive asset and work management programs have changed our culture through the implementation of reliability centered maintenance (RCM) best practices. A work and asset management application for our computerized maintenance management system (CMMS) was implemented in 1999. Predictive technologies and condition-based monitoring initiatives have been phased in and enhanced since then, and we're now funding additional planned improvements.
Work management guidance is documented and implemented through LOOP's maintenance policies and procedures manual. This manual includes high level and detailed roles and responsibilities of the organization, as well as instructions for our maintenance and reliability processes. This guidance document also covers the regulatory requirements and details of our facility management of change process.
Figure 1: Did you know that if your company is not in regulatory compliance, you could be one audit away from a fine, or one incident away from going out of business?
We've come to realize that we must reach above and beyond regulatory compliance requirements to achieve OpEx in work management, as depicted in the Figure 1 graph.
Our operator care program consists of a detailed checklist which field operators use to document actual versus expected readings and a plan of action if values are not within tolerance. Our operators take pride in our facilities, as all of our employees do, and are viewed as our first line of defense in asset care.
Maintenance planners and schedulers plan 100 percent of available maintenance crew manhours. Weekly and daily schedules are created with stakeholder input on priority, then distributed for execution. LOOP's preventive maintenance (PM) procedures address asset failure modes, defect detection and elimination. They provide guidance to maintenance technicians for ensuring desired outcomes and repeatability. Reliability technicians and specialists are responsible for our predictive maintenance (PdM) program. KPIs
and metrics are used for monitoring and managing asset health.
The following proactive programs and processes have assisted LOOP in becoming successful in our work and asset management objectives.
Condition-Based Monitoring & PredictiveTechnologies
• Operator Care
• Vibration
• Thermography
• Oil Analysis
• Motor Testing
• Ultrasound
• RCM Practices
• Metrics / Reports to the Organization (Weekly
& Monthly)
• Others (Battery Testing, Partial Discharge,
B-Probe, SNAP, etc.)
Preventive Maintenance & Critical Spares
• Planning & Scheduling
• CMMS
• PM Compliance / Work Flow / Redline Process
• Work Order / Backlog Management
• Work Execution & Innovation
• Defect Elimination / Failure Reporting, Analysis
and Corrective Action System (FRACAS)
• Critical Spares / Warehousing / Off-Site Storage
Figure 2: N.J. Lefort, LOOP reliability technician, performing predictive PdMs
Figure 3: Jason Rogers, LOOP reliability technician, performing predictive PdMs
To help set our strategy and tactical objectives in an effort to sustain our proactive cultural shift, we created a "one pager," providing our office and field personnel with a succinct guideline and mission.
Figure 4: LOOP Leadership Team photo taken after a safety and environmental roundtable meeting in Larose, La.; not all members are present due to other obligations
When the one pager was introduced over two years ago to the reliability group after a Leadership Conference, we actually targeted an Uptime Award, which was later realized in December 2014. Thus, we view the award as a pertinent milestone in our quest for OpEx. While we appreciate receiving this prestigious award, we've already begun striving to achieve goals we've set for 2015 and beyond. Recognizing that 2014 was a historic year of successes for LOOP, we've made a commitment not to camp out at success and will continue to improve our performance through enhanced condition monitoring, asset management and reliability centered maintenance best practices.
Figure 5: 2014 Uptime Award for Best Work Execution Management Program presented to LOOP during IMC-2014.
Continuous Improvement
• There is always room for improvement!
• We continue to learn, every day and on every job
• We're learning from successes and failures alike
• We're keeping our priorities in check:
- Safety
- Quality
- Schedule
• We think of OpEx in Work Execution Management
as a journey and a vision, more so than a final destination.
• With an embedded culture, a clear focus on getting
it right and a passion for continuous improvement,
LOOP continues its journey towards operational
excellence.
Maintenance Planning for the Louisiana Offshore Oil
Port (LOOP LLC). Brian has over 26 years in the energy
industry, both oil and gas, and power. He served in the
U.S. Army and later worked in consulting engineering
as a co-op student while attending the University of
New Orleans, where he obtained a bachelor of science
degree in electrical engineering.
Special recognition to Chris Labat for providing the proactive and timeline perspectives for the article, as well as a final review.
Engineering & Technology at LOOP LLC, where he once
served as the reliability superintendent and helped
set up the department and related proactive work
practices. Chris has over 27 years in the oil and gas
industry and obtained a bachelor of science degree in
mechanical engineering from Louisiana State University.
- Reliabilityweb Developing and Implementing a Work Execution Management Improvement Process ›
- Reliabilityweb Right 6 Operate for Reliability: The 10 Rights of Asset Management ›
- Reliabilityweb DuPont Sustainable Solutions is now dss+ ›
- Reliabilityweb Connecting Operational Excellence to the Uptime Elements ›