Six Questions to Consider Before Answering:
- Is there a Compliance Standard/Organization for your industry?
- Is Enterprise Asset Management (EAM) a factor in your success?
- Are Competitive Pressures growing in your industry?
- Is this pressure squeezing Operating Budgets?
- Are you being challenged to find and retain competent Skilled Personnel?
- Is protecting your investment in assets/personnel important to your Continued Success?
If you answered “Yes” to these questions, it is safe to assume that you are a business that expects to have a future. Your future, expressed in terms of today, is preparing for and performing in a competitive environment and is not just surviving, but thriving. To survive and thrive you need a computerized maintenance management system (CMMS).
A CMMS is the Data Backbone for Documenting Industry Compliance and Responding to Audits
In our global economy, standards and compliance have become a way of life for manufacturing organizations. Audits are commonplace today to ensure compliance and failing an audit is unacceptable and often has an immediate impact on current and future business.
The CMMS is the repository for data that documents the maintenance program, availability of maintenance spare parts and work order history. The history maintained in the CMMS also supports root cause analysis, resulting in improved engineering and manufacturing solutions. Bottom line, the CMMS is the cornerstone of supporting current operations, trending failures and providing knowledge for improvements that impact the bottom line.
The CMMS Data Supports the Metrics Needed for Improved Operations
The impact of the CMMS on the future of a business is brought to light when you consider that “maintenance management generally makes up 40 percent to 50 percent of operational budgets; the savings made possible from increased efficiency and reduction of waste is staggering.” 1 This reality has been clearly demonstrated in assessments following implementation and use of a CMMS. It has been my experience that equipment reliability can increase from 35 percent to 50 percent; better workflow management leads to further savings of five percent to 15 percent of overall maintenance costs; cost savings from optimizing inventory and purchasing are as high as 20 percent of the total inventory cost; and a 20 percent gain in equipment uptime results in improved productivity and resource allocation.
A CMMS Strengthens Asset Management
The need to capture and maintain historical, accurate and meaningful information about assets leads companies to invest in the CMMS. This interactive information database is the continuous medium that is the lifeblood of the maintenance function. In an era of increasing global competition, organizations today are in a constant state of change. Key trends driving this change include rapidly expanding technology, increased demand for individual and organizational competencies and capabilities, ever decreasing cycle time and changes in skilled personnel requirements. The CMMS is the vehicle for meeting these needs and allows for the planning, measuring, evaluating, operating and maintenance practices, and provides information on the condition of critical assets.
A CMMS Buffers Labor Transitions
The condition of assets isn’t the only issue; there’s the skilled personnel to maintain them. Consider the amount of information that can leave a company when a key maintenance employee leaves. Years of critical technical information can be lost the moment the employee walks out the door. And walking out the door will be happening with greater frequency in the coming years. “The baby boom generation will retire in large numbers, ongoing in the 2000s and peaking in 2012 and they’re not being replaced by sufficient numbers of highly skilled workers.”
The U.S. Bureau of Labor Statistics estimates a shortfall of about 10 million workers within the next six years and the number of prime age workers—those between the ages of 25 and 54—will shrink dramatically.
As far back as 2004, a report from the Herman Group titled , “Top Ten Work Place/Workforce Forecast 2004,” indicated that, “As the economy picks up, employers will face the most severe shortage of skilled labor in history.” Underlying the looming workforce shortage is a demographic shift of historic proportions. Businesses needing skilled labor—positions traditionally held by tech-savvy workers—could be particularly hard hit unless they begin attracting older workers. A labor shortage could also throw a wrench into the workings of small manufacturers. “A talent shortage could not happen at a worse time,” says Jerry Jasinowski, past president of the National Association of Manufacturers. “Unchecked, a shortfall could quickly hobble our manufacturing competitiveness once the global economy recovers in earnest.”
In the larger scheme, a labor shortage could mean a brain drain for companies. Employers of every size in every industry who ignore the statistics and predictions could risk the future success of their businesses. In the 2012 forecast, the number one concern was: Recruiting will intensify among smaller employers. Employers attempting to recruit experienced people will find their challenges increasing. The number three concern was: More communities will wake up to the critical need for workforce development. More communities will become aware that they will simply not grow economically without having an available skilled workforce---with the skill sets their prospects seek. 2
A CMMS doubles as both the best defense and offense by placing important historical and cultural knowledge in a safe, standard repository, while simultaneously making this information available to the incoming labor force.
The CMMS Projections Define Key Skill Needs
The skills required by the workforce of the future are changing in virtually all occupations, but by and large, employees are not obtaining them sufficiently. Science, math and computer skills will be in the greatest demand, but far too small a percentage of today’s students focus on those areas. Enrollment is down at many technical schools and vocational programs, a troubling development because they do a better job preparing young people for technical professions than four-year colleges.
Skill set requirements vary by occupation, of course, but in the future, almost all jobs will require some degree of technical expertise, even those not traditionally viewed as requiring higher-level knowledge. For example, topping the list of employers’ key expectations for administrative staff is that they be skilled in new and emerging technologies, according to the International Association of Administrative Professionals (IAAP), based in Kansas City, Missouri. In addition, employers want proficiency in the Internet, intranets, e-mail, online services and a wide variety of PC software. Knowing what you need and how much of it better prepares employers for meeting the future training and technical demands of their business.
A CMMS Provides the Competitive Advantage for EAM
Every business is based on profit and profit comes from the very simple equation, W=PT, where W stands for wealth (profit), P for physical resources (traditionally land, labor, assets) and T for technology. 3 With resources as an available equivalent, the variable driving wealth and creating success is the application of technology-based knowledge. Knowledge is the source of all sustainable competitive advantages.
According to figures supplied by James Appleberry, cited by José Joaquín Brunner, internationally recorded discipline-based knowledge took 1,750 years to double for the first time, counting from the start of the Christian era; it then doubled in volume every 150 years and then every 50. It now doubles every five years and it is projected that by 2020 knowledge will double every 73 days. 4 Utilization of existing technology and the acquisition of new enabling technology provide the competitive advantage for the future. Timing for capital investments, when to repair, when to replace and when to upgrade processes are all knowledge intensive actions that require an informational database that can support the decision-making process. The CMMS is the platform to maintain this database and provide key information in a timely manner.
The CMMS Mitigates Government Regulatory and Compliance Issues
Government regulatory compliance and exposure to health and safety liability are major factors in the business environment today. A CMMS can be used to schedule training, record training schedules, monitor attendance and provide audit trails supporting compliance training. In addition, safety requirements can be transmitted to employees with work orders verifying proper methods of work performance and documenting company practices that are to be followed. Reduction in work-related accidents and the liability exposure the company is subjected to can be greatly reduced by proper documentation and communication of safe work practices. Finally, summary reports and the supporting documentation can be produced to certify compliance with required standards that conversely reduce liability exposure and lost business opportunities due to non-compliance claims.
A CMMS –Sophistication or Survival?
A computerized maintenance management system is not simply an “add-on” or a “nice addition” to your list of productivity enhancing tools; it is a necessity! Large or small, you need what the CMMS has to offer. Your competition is using it and if you lose the knowledge-based technology battle, you have lost your competitive advantage.
With a CMMS, you’ve enabled that winning advantage.
References:
1. Mather, Darly. “The Future of CMMS.” Como, Washington: Plant Resource Maintenance Center, 2002.
2. Entrepreneurial Connection. “The Looming Labor Crisis.” http://www.entrepreneurialconnection.com/skills/module29/one.asp
Adapted from Pilzer, Paul. “ God Wants You To Be Rich.” New York City: Simon & Schuster, 1997.
4. Paper produced for the UNESCO Forum Regional Scientific Committee for Latin America and the Caribbean Paris, December 2003, http://portal.unesco.org/education/es/file_download.php/697c33597621cdab0b77507d31da8cf8Tunnerman+(English).pdf
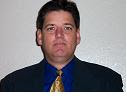
Gary Brown
Gary Brown,CET, MBA, CFP, is the President and Owner of Manufacturing Asset Solutions (MAS) an Arizona-based Maintenance and Facilities EAM/CMMS implementation company and Express Maintenance - Maintenance Management Software create by Maintenance Professionals for Maintenance Professionals. For the past 15 years, he has been engaged with hundreds of companies as a Systems Engineer and Expert Consultant on the Asset Management Lifecycle. Websites: expressmaintenance.com and mas.systems