Aren’t EAM and CMMS the Same Thing?
The market for maintenance and asset management software is primarily dominated by two types of products: enterprise asset management systems and computerized maintenance management systems. The two terms are thrown around a lot, but it’s not always clear what the difference is, especially when you’re trying to decide which software system to purchase for your business. The confusion is not helped by the fact that many true CMMS products have started advertising themselves as EAM systems, or as EAM/CMMS hybrids.
On the surface, these products all make similar claims and seem to do similar things. They’re all geared toward maintenance; they all offer cloud-based subscriptions; and most of them provide additional features like inventory management and asset tracking. Some CMMS software packages even offer features that have traditionally been the domain of EAM systems, such as purchasing modules or multisite management tools. This raises two important questions. In today’s market, where web architecture and mobile apps are par for the course and multisite support is becoming more and more common, is there any noticeable difference between an EAM system and a CMMS? Have we reached a point where the lines are so blurred that they’re basically the same thing?
The answers are yes, there’s a difference, and no, they’re not the same thing. Let’s be clear: not every product that claims to be an EAM system has real EAM functionality. While it’s true the line between EAM and CMMS is not as clearly defined as it was 20 years ago, these two types of software still have big differences in approach and functionality.

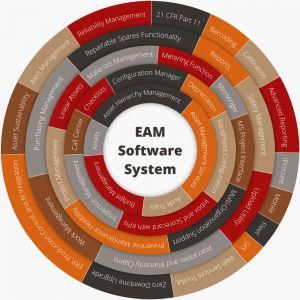
Figure 1: Anatomy of an EAM software system
What Is a Computerized Maintenance Management System?
A CMMS is designed to be exactly what the name says: a computerized maintenance management system. These systems came into being in the 1960s as technology for managing work orders with punch cards instead of paper and filing cabinets. They emerged as a computer software in the 1980s. As these systems evolved, more features were added to support a wider range of business needs. These days, most computerized maintenance management systems have some form of preventive maintenance, asset and inventory management, and mobile functionality. Many boast additional features, such as project management, multisite support, or the ability to purchase maintenance, repair and overhaul (MRO) parts from an online catalog without leaving the CMMS.
Despite their growing range of capabilities, maintenance management remains the heart of a CMMS software package. Smaller CMMS products focus exclusively on work orders and equipment records. Even the largest aren’t designed to provide much functionality outside of maintenance and MRO materials management. This limited focus makes sense given their history and, in some situations, it can even be seen as an advantage. Computerized maintenance management systems are dedicated, streamlined tools for managing maintenance operations. They aren’t supposed to service the asset management needs of the whole organization. This leaves gaps, but businesses can fill them by integrating their CMMS with other software systems that provide services, such as scheduling, purchasing and accounting.
A CMMS is an attractive solution for small maintenance operations that need a simple way to manage work orders, equipment records and spare parts. These systems can’t do everything, but they often have a smaller price tag than their larger and more powerful cousins—the EAM systems.
What Is an Enterprise Asset Management System?
As the name suggests, enterprise asset management systems were designed to be unified platforms for managing an organization’s physical assets across the enterprise. They came on the scene after computerized maintenance management systems, once network technology gave companies the ability to link computer systems across multiple sites. EAM systems include maintenance management capabilities, but they consider the total cost of ownership (TCO) for a company’s physical assets and provide a wider range of features to track, manage and analyze asset performance and costs through the whole asset lifecycle, from acquisition to decommission and everything in-between.
Because they are designed for the enterprise, EAM systems serve every facet of an organization that pertains to asset management. This includes functions like maintenance and MRO inventory, but also spans MRO procurement, engineering and project management, accounting, operations, reliability management, safety and compliance, and even business intelligence (BI) to support strategic planning at the enterprise level.
The result of this comprehensive design is a single system that contains all the information about an organization’s physical assets. Repair histories, energy usage, lifecycle costs, warranty records, parts catalogs, purchase orders, audit trails and more are all stored in the same system and accessible to any department. Maintenance can use the EAM system to manage work orders and equipment records. MRO materials management can use it to manage storerooms and inventory. MRO procurement can use it to manage requests for proposals (RFPs), contracts and purchase orders. Accounting can use it to manage MRO budgets and invoices. Because it’s a single system, everyone is accessing the same data—data that is aggregated from a multitude of sources across the organization and updated in real time.
Since they debuted in the 1990s, EAM systems have been the solution of choice for asset intensive organizations that need to manage a large portfolio of physical assets across multiple locations. However, in the last decade, these systems have seen increasing use by small and medium-sized businesses (SMBs) that want the added performance optimization and cost management features that EAM systems offer. With the rise of software as a service (SaaS) deployment models, the cost of owning an EAM system has become competitive with a CMMS and because of its additional features, an EAM system is often the most cost-effective choice, even for small operations.
Figure 2: An EAM system serves all business functions that play a role in asset management.
EAM and CMMS: Different Approaches to Asset Management
As you have seen, CMMS and EAM systems have similar purposes and some of the same functionality, although EAM systems offer a broader range of features. What really distinguishes them is philosophy and scope. A CMMS focuses on maintenance, while an EAM system takes a comprehensive approach, incorporating multiple business functions. A CMMS starts tracking after an asset has been purchased and installed, while an EAM system can track the whole asset lifecycle, starting with design and installation. A CMMS is designed to manage a single location or offer limited multisite support, while an EAM system comes with extensive features for managing multiple sites and businesses.
An EAM system is more than just a beefed up CMMS. It’s a comprehensive tool for managing physical assets and maximizing their performance across the business. It’s a CMMS combined with an inventory management system, a purchasing management system, a document management system, an accounting system, a project management system, multisite management tools, performance management tools and BI tools, all rolled into a single, integrated piece of software.
Organizations that are serious about asset management rely on EAM systems to get the job done because they offer the broad, powerful, unified feature set that asset intensive operations need to make the most of their physical assets. This is also why it’s misleading to describe a CMMS as an EAM system; the difference between them is more than just a few extra features. They are two different kinds of software products that represent two different approaches to how an organization manages its assets.
Features | EAM | CMMS |
---|---|---|
Table 1: Side by side comparison of EAM and CMMS software features | ||
Asset Hierarchies | ||
Asset Tracking | ||
Automatic E-mail Alerts | ||
Budget Management | ||
Calibration Monitoring | ||
Condition Monitoring | ||
Customizable Configuration | ||
Document & Image Management | ||
Energy Monitoring | ||
Fleet Management | ||
Interactive Maps, Floor Plans, and Schematics | ||
Inventory Management | ||
Linear Assets | ||
Maintenance-as-a-Service | ||
Mobile Platform | ||
Multi-Site Management | ||
Preventive Maintenance | ||
Process Management | ||
Project Management | ||
Purchasing & Requisition Management | ||
Reliability-Centered Maintenance | ||
Repairable Spares & Rotating Assets | ||
Reporting, Visual Dashboards, and KPIs | ||
Role-Based Security Controls | ||
Safety & Compliance Management | ||
Warranties & Warranty Claims | ||
Work Orders & Requests | ||
Work Planning & Scheduling | ||
Zero Downtime Upgrade |
Which One Is Right for Your Business?
For large organizations with multiple sites and many assets, EAM systems are the obvious choice. They’re the only tool on the market that combines powerful maintenance and asset management capabilities with advanced features for lifecycle cost tracking and analysis, enterprise grade support for multiple locations and businesses, and functionality for non-MRO departments like accounting and engineering. EAM systems also offer a wider range of integration options than computerized maintenance management systems, connecting the enterprise from BI systems at the top to supervisory control and data acquisition (SCADA) systems and building automation systems (BAS) at the bottom.
For SMBs, however, the choice isn’t always so clear. Most computerized maintenance management systems are more than capable of handling maintenance management needs and even MRO inventory requirements of smaller operations. They are generally priced lower than EAM systems. If you are just looking to put in a preventive maintenance (PM) program, a CMMS may be your best choice. But even for smaller operations, there are strong reasons to consider an EAM system.
If you have plans for growth, you need a tool that can grow with you. A CMMS is great for small operations, but not as good in supporting the needs of a growing business. If you’re thinking about adding another site, for example, you need the enterprise functionality of an EAM system. Or, if you decide next year to implement a reliability-centered maintenance (RCM) program, you’re going to want the failure analysis tools provided by an EAM system. A CMMS may serve your immediate needs, but an EAM system will give you tools to keep improving performance over the long term.
If you want to take a comprehensive approach to asset management—one that considers TCO and seeks to maximize value throughout the asset’s lifecycle—then you need the deep functionality and enterprise mentality that come with an EAM system. Asset management is not just about maintenance, but about all business functions working together. You need a software platform that serves the needs of the whole operation, not just one function. An EAM system provides the tools to track costs, manage resources and optimize performance across the whole organization.
- Reliabilityweb Asset Performance Management Software ›
- Reliabilityweb How To Reduce Reactive Work With Oracle Maintenance Solutions ›
- Reliabilityweb Asset Performance Management Software ›
- Reliabilityweb Asset Performance Management Software ›
- Reliabilityweb Asset Management Technology Vendors Create Market Disruption ›
- Reliabilityweb Asset Management Technology Vendors Create Market Disruption ›
- Reliabilityweb 6 Ways CMMS Supports Employee Retention ›