The Importance of Machine Reliability in a Lean Manufacturing Setting
Lean manufacturing is a production philosophy of removing anything that does not add value to the finished product from the production process. It targets three areas: process inefficiencies, production variations, and processes not adding value to the customer. Machine reliability impacts each of these categories, placing maintenance at the forefront of creating a successful, lean manufacturing environment.
Quality of Production
Machine reliability and the production of quality products requires more from a machine than simply being operative. It must also be capable of adequately acquitting its function. When machining components to fine tolerances, bearing degradation, voltage transients, electrical interference, and voltage imbalance all potentially affect the accuracy and surface finish of a machined surface. Positioning errors, spindle rotation, guide rail, and transmission chain errors all create datum inaccuracy and geometric errors.
Not an immediately obvious reliability issue, the equipment will continue producing products out of specification until the production line stops to resolve the issue—leaving considerable quantities of the product requiring scrapping or rework. Such machine stoppages obviously affect production continuity, but quality also relies on steady-state production in many manufacturing processes.
Stopping the line in a steady-state production process creates a percentage of off-specification products, as does starting it again. Waste can also result from paints, glues, or raw materials that may need to be discarded due to the stoppage. Such systems are prime candidates for implementing a predictive maintenance strategy using critical effect analysis, IIoT technology, and predictive maintenance for early warnings of deterioration to preset thresholds.
Production Continuity
Frequent breakdowns disrupt production continuity, increase scrap rates, and endanger client deadlines—yet, there are less obvious secondary effects that are equally wasteful. When one production segment fails, other areas often stockpile products, either as work in progress or finished components requiring transport. Two of the eight identified wastes within lean manufacturing are unnecessary transportation and excess inventory. Unreliable equipment causes them both.
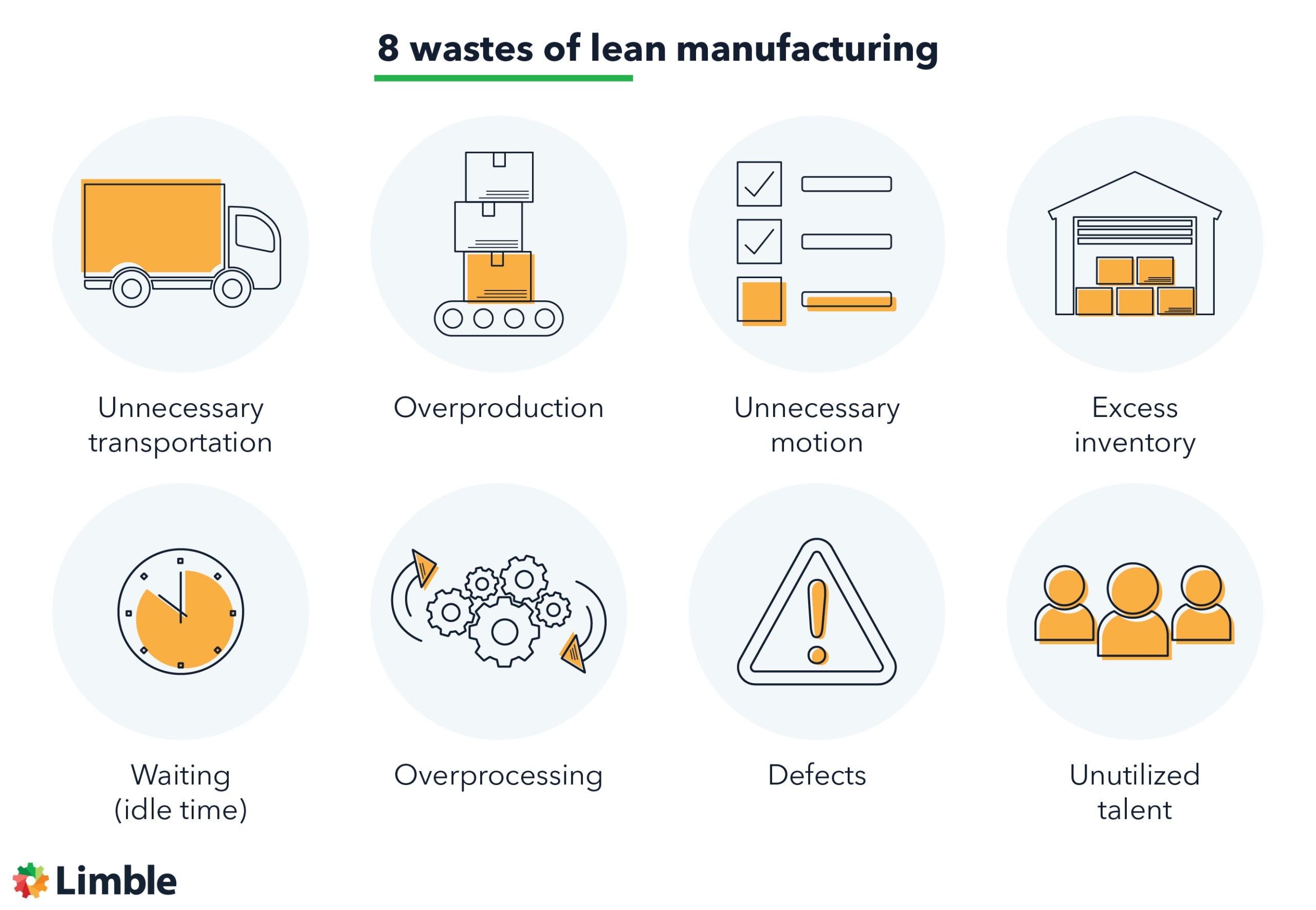
Equipment availability and breakdowns are not the sole measures of equipment reliability. In a lean manufacturing environment, Takt time is the heartbeat of the manufacturing process. It describes the pace at which you need to manufacture a product to meet client demand. Manufacture too fast, and you create excess inventory, one of the wastes within lean. Manufacture too slowly, and you risk failing to meet client expectations and are therefore not adding value to the customer.
Equipment may continue to operate at the required quality, but if it fails to meet the expected takt time, it is unreliable within the context of the production process. Cycle times can be affected by myriad issues such as pressures, flows, friction, or voltage. They are often difficult to pinpoint, such as pressure relief valves in constant partial bypass due to seating issues. Trending equipment cycle times is one way to identify such insidious deterioration, allowing an inspection task to be raised for subsequent investigation.
Inefficient Maintenance
The eight wastes that apply to manufacturing apply equally to the maintenance department and directly affect reliability. Lean emphasizes overprocessing as a wasteful activity, with wasted effort and excess process costing money. It adds no value to the customer and potentially even reduces value. Over-maintaining equipment has a financial cost, but it also introduces the risk of reliability issues through human error while reducing equipment availability.
Other insidious effects are inefficient or poorly-phased maintenance programs that fail to level workload and resources. These inefficiencies are responsible for two more of the eight identified wastes—unutilized talent and waiting—which apply equally to maintenance and production technicians.
In a production environment, it's not uncommon for new equipment, changes in location, or modifications to cause planned maintenance tasks to become suboptimal. Such maintenance programs can fail to maintain equipment reliability or add no value while potentially causing equipment downtime.
Old manual maintenance systems may maintain reliability within an acceptable range, yet their effective operation often depends on experienced individuals within the organization. If staff turnover increases and corporate memory is lost, reliability can suffer rapidly and dramatically. Manual systems also risk human error, with documents misplaced or failing to revise maintenance data promptly.
Implementing a modern computerized maintenance management system mitigates many risks to equipment reliability posed by maintenance system inefficiencies. In addition, a regular rolling audit of the maintenance program can realign phased tasks, remove redundancies and duplicates, update task hours, and review frequency applicability.
Conclusion
Lean manufacturing is not the sole preserve of the production department, with machine reliability directly impacting the operating plant's efficiency. Maintenance and engineering departments implementing the lean philosophy while using modern monitoring technologies and an optimized maintenance program have a central role in improving equipment uptime, maintaining quality, reducing inventory levels, and lowering costs.