Designing for Reliability and Maintenance
by Bruce Dean, CMRP, Manager, Design Engineering & Ramesh C. Gulati, PE, CMRP, Manager, Asset Mgmt. & Reliability Planning
AEDC / ATA
Arnold Air Force Base, TN 37389
Abstract
One of the key factors in asset/system performance is its reliability- “inherent reliability” or designed in reliability. Are we designing the system with reliability and maintenance in mind? The O&M cost, which is typically about 80% of the total life cycle cost of the system, becomes fixed –whether intentionally or not- during the early design phase. Are we specifying the reliability and maintenance needs in our requirements document before the design phase begins? The reliability & maintainability are design attributes that should be designed into the assets to minimize maintenance needs by using reliable components, simpler replacements and easier inspections.
Introduction
Having high reliability of assets /plants is essential to the success of any organization, particularly with respect to its overall operations and maintenance cost. Understanding reliability and maintenance and how they’re interrelated is important.
Reliability focuses on the ability of an asset to perform its intended function to support manufacturing a product or providing a service. Reliability terminates with a failure —i.e., when unreliability occurs. Unreliability results in high cost to the organization.
Maintenance is an act of maintaining, or the work of keeping the asset in proper –operational condition. Maintenance is a “field” action and may consist of performing maintenance inspection and repair to keep assets operating in a safe manner to produce or provide the designed capabilities. So maintenance is to keep assets in an acceptable working condition, to prevent them from failing, and if they fail, bring them back to their operational level effectively and as quickly as needed.
Reliability should be “designed in” and is a strategic task. Maintenance is to keep assets functioning and is a tactical task. The reliability & maintainability should be designed into the asset to minimize maintenance needs. It could be accomplished by using reliable components that are easier to inspect and replace.
It has been found that the Operations & Maintenance (O&M) costs are about 80 % or more of the total life cycle cost of an asset. It is obviously important that there is need to minimize O&M costs. Also, a majority of the O&M costs get fixed during the design and development phase of the asset. Therefore it is highly important that during the design and building of the assets, we adequately address reliability, maintainability, and safety issues to reduce overall life cycle cost of the assets.
Examples of Unreliability & Maintainability:
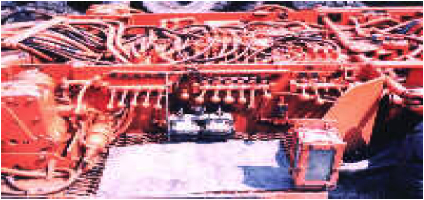
How somebody is going to perform maintenance on this
equipment?
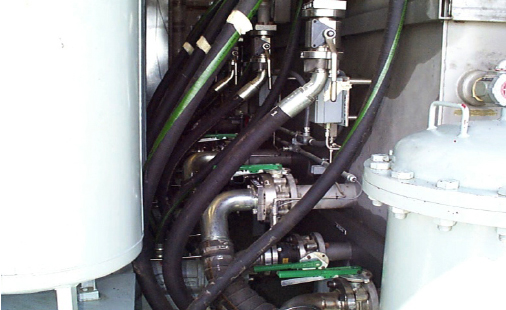
How long it will take to replace a leaky hose
on this equipment?
It will be a challenge to replace pump or motor
on this unit.
Maintenance had to cut a hole to make an
opening to reach hidden (broken) component.
Asset Performance and Designed Reliability
The objective of maintenance & reliability in an organization is to ensure that the assets are available, when needed, in a cost effective manner. The performance of an asset is based on three factors,
- Designed reliability ( Inherent)
- Operating environment
- Maintenance plan
Figure 1 Asset Performance “A Three-legged stool”: Reliability, Operating Environment, & Maintenance
Usually assets are designed with a certain level of reliability built-in based on an effective use of reliable components and their configurations. This level of reliability is called inherent reliability. We can’t change or improve reliability of an asset without redesigning or replacing its components with improved components. The second factor is considering the operating environment to ensure that operating conditions are considered during the design and also in the development of maintenance plan. The operators need to be trained with appropriate skills to operate the assets effectively. Several studies have indicated that 40 percent or more of failures are the result of operational errors. The third factor, an effective maintenance plan, is needed to detect or find potential failures before they create unscheduled downtime. This also requires doing the necessary service type actions such as replacing filters or performing the necessary repairs when a failure occurs. This maintenance plan should sustain the reliability and help to improve asset availability.
Reliability, a design attribute, is a broad term that focuses on the ability of an asset to perform its intended function. Maintainability is another design attribute which goes hand in hand with reliability. It’s ease of maintenance. The objective of maintainability is to ensure that maintenance tasks can be performed easily and effectively.
There are a number of reasons why reliability & maintainability are important asset attributes, including:
- Reputation - highly reliable asset and if it fails, it can be fixed quickly
- Customer Satisfaction - meets quality and schedule
- Repeat Business -- resulting from above factors
- Competitive Advantage
A reliable plant means that the plant and its assets are available, as and when needed, to meet customer’s needs on schedule and at cost.
Asset Life Cycle Cost:
Life cycle costs (LCC) are all the costs expected during the life of an asset. It refers to all the costs associated with acquisition and the ownership, specifically operations and maintenance, of the asset over its full life, including disposal. Fig. 6.14 shows a typical asset life cycle chart. The total cost during the life of an asset includes:
- Acquisition Cost
-Design and Development
-Demonstration and Validation – ( mostly applicable to one of a kind, unique systems)
-Build and Installation ( including commissioning) - Operations and Maintenance (O&M)
- Operating cost including energy
- Maintenance cost
-PM
-CM - Disposal
Based on several studies reported, the distribution of estimated LCC is:
It has been found that the operations and maintenance (O&M) cost is about 80 percent of the total life cycle cost of the asset. It is obviously important that we need to minimize O&M costs. As shown in the chart, the major portion of the O&M cost are fixed during the early design and development phase of the asset. There are ample opportunities to reduce the LCC during the design, building and installation of the assets.
Reliability requirements / specifications:
In order to develop a reliable asset, there must be good reliability requirements and specifications. These specifications should address most, if not all, of the conditions the asset has to operate, including mission time, usage limitations, operating environment, etc. In many instances, this will require a detailed description of how the asset is expected to perform. Use of a single metric, such as MTBF, as the sole reliability metric is inadequate. Even less effective is the specification that an asset will be "no worse" than the existing or previous model. An ambiguous reliability specification leaves a great deal of room for error, and this can result in a poorly-understood and unreliable asset in the field.
Financial concerns will definitely have to be taken into account when formulating reliability specifications. What reliability can we afford? How many failures can we live with? Do we need to have zero failures? It’s a great goal but, can we justify in achieving zero failures. A proper balance of financial goals and realistic asset reliability performance expectations are necessary to develop a detailed and balanced reliability specification.
Key elements of reliability specifications:
- Probability of successful performance
- Function (mission) to be performed
- Usage time ( mission time)
- Operating conditions
-Environment
-Operators / maintainers skill
Designing for Reliability:
It has been found that as much as 60 % of failures and safety issues that can be prevented by making changes in design. We need to ensure that assets are:
- Designed for fault tolerance
- Designed to fail-safety
- Designed with early warning of the failure to the user
- Built in diagnostic system to identify fault location
- Designed to eliminate all or critical failure modes cost effectively if possible
The following analyses are recommended to be performed during design phase, from conceptual design to final design.
- Reliability Analysis
-Lowers asset/system failures over long term
-Asset/System reliability depend on robustness of design, and component quality and reliability - Maintainability Analysis
-Minimizes downtime – reduces repair time
-Reduces maintenance costs - System Safety and Hazard Analysis
-Identifies, eliminates or reduces safety related risks throughout its life cycle - Human Factors Engineering Analysis
-To prevent human-induced errors / mishaps
-To mitigate risks to humans due to interface errors - Logistics Analysis
-Reduces field support cost resulting from poor quality, reliability, maintainability and safety
-Ensures availability of all documentation including PM plan, spares and training needs
The following design reviews check list is recommended to be used as guide to ensure design is adequately addressing reliability, maintainability, and safety issues;
Design Reviews Checklist:
- Are reliability, maintainability, availability, and safety analysis performed?
- Is failure-mode, effect, and analysis (FMEA) performed during the design – at preliminary design reviews (PDR), Critical design reviews (CDR) ?
- Can fault-free analysis be used to improve the design?
- Is fault-tolerant design considered?
- Are components interchangeabilities analyzed?
- Is modular design considered?
- Are redundancies considered to achieve desired reliability?
- Has the design been critiqued for human errors / mistakes?
- Ease of maintenance or maintenance-free design considered?
-Is Reliability-Centered Maintenance (RCM) considered in design?
-Throwaway type design considered instead of repair (e.g., light bulbs)
-Have considered built-in testing / diagnostics?
-Is self-monitoring and self-checking desirable?
-Are components & assets easy accessible for repair? - Do components need corrosion protection?
- Is zero-failure design economically feasible?
- Is software reliability specified and considered in design?
- Do electronic circuits have adequate clearances between them?
- Has software coding been thoroughly reviewed?
- Is self-healing design feasible or required?
- Are redundancies considered for software?
- Are the switches for backup devices reliable? Do they need maintenance?
- Are protective devices such as fuses, sprinklers, and circuit breakers reliable?
- Does the asset need to withstand earthquakes and unusual loads? If yes, are design changes adequate?
- Can manufacturing/fabrication or maintenance personnel introduce any defects? Can they be prevented by design?
- Can the operator introduce wrong inputs – wrong switching etc.? If so, can the asset be designed to switch to a fail-safe mode?
- Can a single component cause the failure of a critical function? If yes, can it be redesigned?
- Are there unusual environments not already considered? If hazardous material being used, how it will be contained or transferred safely.
- Are safety margins adequate?
- Are inspection provisions made for detecting cracks, damage, and flaws?
- Are production tests planned and reviewed?
- How reliability will be verified?
Summary
Assets should be designed so that they can be operated and maintained easily with minimum operations & maintenance needs. Reliability and maintainability are the design attributes and should be designed in, rather than added later.
To have reliable and easy to maintain assets, we need to ensure that asset owners, including operators are involved in developing the requirements as well as in reviewing the design. In designing for reliability and maintainability, attention should be focused to:
- Reliability requirements /specifications
- Designing for reliability & maintainability
-Proper component selection and configuration to ensure required reliability & availability
-Review design for maintainability - Logistics support - Maintenance plan and documentation to reduce MTTR
Maintenance cannot improve the inherent reliability. It is dictated by the design. Maintenance at best can sustain it. Get involved early in the concept phase of the design to ensure reliability; maintainability and safety are being addressed. Develop a maintenance plan for the asset using FMEA/RCM to mitigate failure modes which cannot be eliminated through design
Design your assets / systems for RELIABILITY and MAINTENANCE in mind!
- Reliabilityweb Designing for Reliability in Capital Projects and Supporting Operational Excellence ›
- Reliabilityweb The 10 Commandments of RCM - Keys for the Success of an RCM Implementation Project ›
- Reliabilityweb The 10 Rights of Asset Management, 1 Right Specify ›
- Reliabilityweb Right 2 Design for Reliability [DfR]: The 10 Rights of Asset Management ›
- Reliabilityweb Right 1 Specify for Reliability [SfR]: The 10 Rights of Asset Management ›
- Reliabilityweb Right 1 Specify for Reliability [SfR]: The 10 Rights of Asset Management ›
- Reliabilityweb Right 1 Specify for Reliability [SfR]: The 10 Rights of Asset Management ›
- Reliabilityweb Incorporating Reliability Centered Maintenance Principles in Front End Engineering and Design ›