Preventive Maintenance in Uptime Elements
Let's begin with a primer for review:
In Uptime® Elements Reliability Framework and Asset Management System™, a Preventive Maintenance [PM] program generated from Reliability Strategy Development [RSD] has four objectives:
- To realize the inherent safety and reliability levels of the asset
- To restore safety and reliability to their inherent levels when deterioration occurred
- To obtain the information necessary for design improvement of those items whose inherent reliability proves inadequate
- To accomplish these goals at a minimum total cost, including maintenance cost and the costs of failures or other optimum factor basis for your context
Note: There could be and probably are other reasons "why" for you personally and for your organization. It is a good idea to explore and discover those reasons early in the Reliability Strategy Development process.
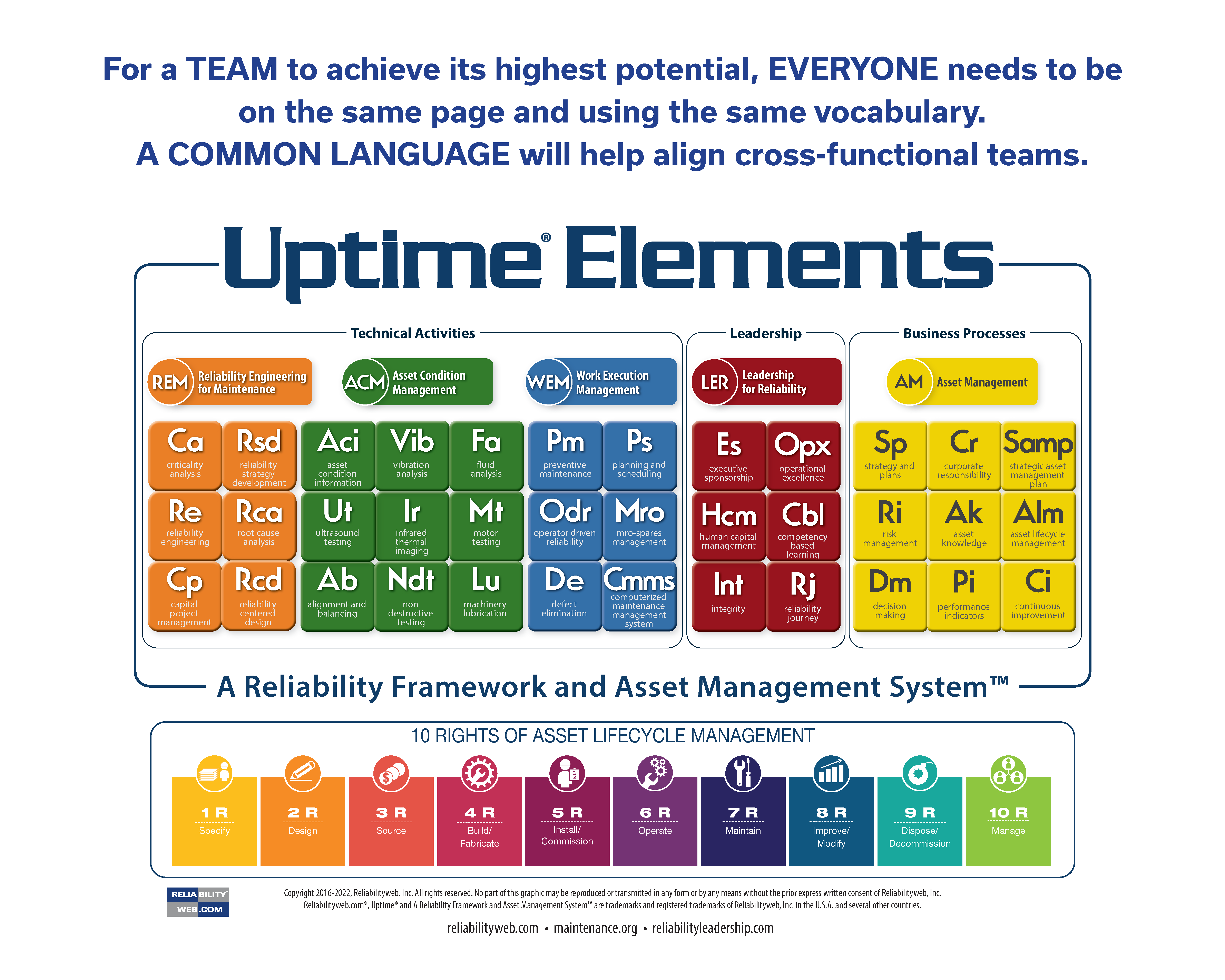
What Is Failure?
It is important for all stakeholders advancing the reliability journey to have a basic understand of the technical definition of failure.
Failure is an unsatisfactory condition.
A potential failure is an identifiable physical condition which indicates that a functional failure is imminent
There are essentially only four types of tasks in a preventive maintenance program that maintenance personnel could be asked to do:
- Inspect an item to detect a potential failure - a potential failure is an identifiable physical condition which indicates that a functional failure is imminent.
(FYI : This is so clear it is why we use the term Asset Condition Management and do not use the term Predictive Maintenance. "Inspect to detect with certainty an identifiable physical condition- which indicates that a functional failure is imminent" NOT "predict" it. It is 100% clear - why muck it up with crystal ball and palm reading and weather forecasts? - TOH) - Rework an item before a maximum permissible age is exceeded.
- Discard an item before a maximum permissible age is exceeded.
- Inspect an item to find failures that have already occurred but were not evident to the equipment operating crew.
Each preventive maintenance task in an Uptime Elements developed Reliability Strategy is generated for an identifiable and explicit reason.
The consequences of each failure possibility are evaluated, and the failures are then classified according to the severity of their consequences and the risk to organizational objectives.
The 3 Laws of Preventive Maintenance
Preventive Maintenance Law 1
Preventive maintenance is required for any item whose loss of function or mode of failure could have safety consequences. If one of the four type of preventive preventive tasks (inspect to detect, rework before maximum age, discard before maximum age and inspect to find hidden failures that have already occurred but are not evident) cannot reduce the risk of such failure to an acceptable level, the item must be redesigned to alter its failure consequences. Law 1 exists because you cannot leave a safety consequence unaddressed.
Preventive Maintenance Law 2
Preventive maintenance is required for any item whose functional failure will NOT be evident to the operating crew and therefore reported for corrective action.
Law 2 exists to address two kinds of "hidden failures". Hidden failures are failures that are not evident to the operating crew.
An evident function is one whose failure will be evident to the operating crew during the performance of normal duties.
A hidden function is one whose failure will not be evident to the operating crew during the performance of normal duties.
Hidden functions may be of two kinds:
- A function that is normally active but gives no indication to the operating crew if it ceases
- A function that is normally inactive, so that the crew cannot know whether it will be available when it is needed (usually the demand follows some other kind of failure).
The fire detection system in a power plant falls into the first category. The system is active whenever the gas turbine is in use, but its sensing function is hidden unless it detects a fire. If it fails in some way, its failure is also hidden. The fire extinguisher system that backs up this unit has the second kind of hidden function. It is not activated unless a fire is detected, and only when it is called upon to operate does the crew find out whether it works
The Maintenance crew must not only inspect for potential failures, Maintenance crew also inspect the hidden function items for functional failure.
Preventive Maintenance Law 3
In all other cases the consequences of the failure are either economic or line of sight to organizational objectives and scheduled maintenance tasks directed at preventing such failures must be justified as economically feasible (just because you can prevent it does not mean it is worth preventing).
Law 3 or the Sanity Law is "the Common Sense Law", demands that we ONLY perform preventive maintenance tasks that can be proven to be beneficial. Tasks that add significantly more value than they cost to perform in time, labor and other factors.
This is not only due to economic factors but due to the fact that unnecessary maintenance can actually induce failures, increase safety risk and reduce environmental sustainability.
Note: You could make these laws tighter for certain consequences (i.e. environmental) in your organizational context however you should never relax them.
Do we need more laws to assure effective preventive maintenance? We like things that are simple and easy to understand but we are open to improvement as well.
Reference Sources:
1: Uptime Elements Body of Knowledge, December 2015
2: Nolan and Heap, Reliability-centered Maintenance, November 1978
- Reliabilityweb Maintenance of Hydraulic Systems ›
- Reliabilityweb 7 Ways to Ensure Better Maintenance of Electric Motors ›
- Reliabilityweb Why Your Preventive Maintenance Program Isn't ... ›
- Reliabilityweb PM Optimization: Challenge and Transform Your PM ... ›
- Reliabilityweb Maintenance Management: A New Paradigm ›
- Reliabilityweb The 10% Rule of Preventive Maintenance ›
- Reliabilityweb The Technology for Better Preventive Maintenance ... ›
- Reliabilityweb The Importance of Preventive Maintenance ›
- Reliabilityweb Preventive Maintenance (PM) or Corrective ... ›
- Reliabilityweb 3 Techniques for Optimizing Preventive Maintenance ›
- Reliabilityweb Definition of Preventive Maintenance (PM) ›
- Reliabilityweb Hidden Failure Q&A - Henry Ellmann ›
- Reliabilityweb Maintenance Management: A New Paradigm ›
- Reliabilityweb PM Optimization: Challenge and Transform Your PM Strategy ›
- Reliabilityweb PM Optimization: Challenge and Transform Your PM Strategy ›
- What Is Preventive Maintenance? The Beginner's Guide to Running ... ›
- What is Preventive Maintenance & Preventive Maintenance Examples ›
- What is Preventive Maintenance? Types, Benefits, Cost, and Examples ›
- What is Preventive Maintenance? What Benefits Does PM Offer? ›
- What is Preventive Maintenance? And Why it's Crucial for Success ... ›
- What is Preventive Maintenance? - TWI ›
- What is Preventive Maintenance? The Complete Guide to PM | Fiix ›