How to Gain Timely and Accurate Data Insights to Optimize Asset Performance and Reliability
Data-driven decisions are those backed up by hard evidence; reliable and trustworthy data, rather than intuition, gut instinct, or guesswork. However, the abundance of data that is generated from Industrial Internet of Things (IIoT) devices and multiple siloed sources makes it difficult to analyze. The worst thing that can happen is that critical data is missing, remains hidden, or is incorrect. So, how do you know you have the correct information to make the right decision at the right time?

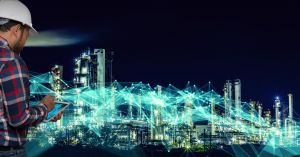
Figure 1: Raw data is generated in plants from many IIoT sources
The Tipping Point for IIoT
The Industrial Internet of Things is at the tipping point. The cost of sensors, data connection and data storage is now a fraction of what it used to be. As a result, the amount of raw data being generated in plants from IIoT sources is growing exponentially, and many organizations cannot keep up.
For most plant managers, the vision of a completely autonomous plant is still a pipe dream. Every sensor added produces thousands of additional data points. As a result, making sense of the data to gain meaningful insights and get to the right decisions can be time-consuming and difficult if you are not sure of its relevance or accuracy.
Industry 4.0 can connect physical assets in the plant to their digital counterparts to improve automation of plant operations and maintenance. Using edge computing to implement artificial intelligence and automated rules is a fast and easy way to alert personnel of problems that must be addressed. However, edge computing is still a silo and might not monitor all aspects of every asset over the long-term, nor understand interdependencies. To fully oversee a facility, you need a systematic, sustainable approach for tracking asset performance over time, with visible, accessible and trusted engineering data.
Figure 2: A facility that has implemented a systematic, sustainable approach to track asset performance
The Ugly Truth
Plant managers have embraced IIoT out of a desire to eliminate human senses from inspections, such as seeing a leak or hearing a malfunctioning motor. Even with the explosion of sensors that can detect changes in operating conditions, the ugly truth is that plants remain highly people-dependent. To improve automation, plants need an efficient, effective and comprehensive program that fully defines organizational and business processes, proactive and predictive asset management practices, and the right technology that enables the implementation and execution of real-time asset performance.
What prevents organizations from making fast and accurate decisions?
While big data was expected to make decision-making easier, it has been difficult for organizations to tap into big data’s full potential because they have not learned how to harness and leverage their data in a way that validates it as trustworthy. Additionally, organizations are not analyzing the data in a timely manner to gain insights. Data problems include:
- Availability – data simply doesn’t exist.
- Accessibility – data is hidden away, stuck in departmental silos, in disparate databases, or software spreadsheets.
- Relevancy – data pertinent to the problem isn’t relatable.
- Reliability – data is not trusted or reliable.
- Processing – data is not in the correct format.
- Volume – there is too much data to manage.
By not having the right and necessary data in place, making the correct decision seems impossible. But when the right data is in place, after it has been collected, managed, analyzed and shared, it provides critical information to decision makers, giving them:
- Goal Alignment: Ensures that goals and targets are met by first identifying your goals and then asking what the data can do for you to achieve them. You can then build a strategy around the data. This saves time in the long run because you are only using the data related to the goals.
- Confidence: Eliminates guesswork and estimates and enables you to make the right decisions with the knowledge they are being made with facts, straight from your trusted information sources. This not only makes decision-making easier, but faster.
- Insights: Allows you to dive deep into your data and uncover patterns and events that would have otherwise remained undiscovered. With the addition of machine learning and artificial intelligence, you can gain more insight into future predictions and forecasts.
- Real-Time Information: With a constant source of real-time or near real-time data consolidated and analyzed from multiple sources, you will always keep up-to-date with asset performance, thereby eliminating late reports and unscheduled events.
- Situational Awareness: Enables you to make data-driven decisions knowing what is happening and how to be prepared, including an understanding of what’s working and what’s not, how assets are performing, and how reliable equipment can be. With a digital twin, you can see the effects of decisions made both in the past and in the present, as well as simulate and forecast into the future.
- Contextual Visibility: With trusted information, you have the ability to bring your data to life. This doesn’t just apply to operations and maintenance data, it applies to design and engineering data, from 2D process diagrams to complex 3D/4D models and reality meshes within digital twins.
With data continuing to grow at an exponential rate, accelerating your digitalization strategy is key to moving forward and remaining competitive. Digital twins help you make trusted data-driven decisions with confidence. With digital twins, you can:
- Capture all asset information sources;
- Improve data quality from CapEx to OpEx;
- Ensure operational readiness and superior asset performance;
- Lower operational costs;
- Make information easier to find;
- Ensure information is up-to-date;
- Interpret, manage and analyze data from one central source;
- Improve the way information is presented;
- Gain intelligent insights to make fast and accurate decisions.
Digital Twins Are Crossing the Chasm
In asset-intensive industries, digital twins are crossing the chasm to support operational excellence. Within a plant, digital twins empower engineering, operations and maintenance to collaborate and capitalize on the opportunity of Industry 4.0. Digital twins help to overcome common pitfalls, such as data overload, systems integration and interoperability, and siloed data.
Digital twins are open and connected data environments that can become a sustainable competitive advantage in the age of IIoT.
Figure 3: A digital twin enables the implementation and execution of real-time asset performance management
Gain Insights to Make Effective Decisions
Automated rules, calculations, artificial intelligence and machine learning are all valuable methods to enable faster and more effective decisions. However, engineering information for each must be complete, accurate and available to ensure you are making the right decision at the right time. Otherwise, it becomes harder to mitigate costs and downtime when the asset fails.
In short, effective decision-making depends on always knowing the current state and status of the asset and becoming informed immediately when that state or status changes. This knowledge should include essential engineering information, as well as how to bring the asset back to the as-built, as-commissioned, or as-designed state when necessary.
Asset lifecycle information management is the backbone of the digital twin. Components, structures, systems and operating states all change over time due to wear and tear, operator decisions and overall plant conditions. Changes in any single asset can negatively impact wider systems and processes. Trustworthy engineering data enables plant engineers to determine why a change occurred and who caused the change.
Raw sensor data alone might not be useful as the complexity and interconnections of piping and process equipment, systems, instrumentation and control devices increase. Operations technology relies on analytics visibility, as well as subject matter experts who can act based on the massive amount of data being generated. Digital twins can harness that raw data and create a trusted system of systems. They can connect data with processes and identify, consolidate and analyze all relevant sources of data to make asset health more visible, drive informed decisions and provide measurable business results.
As assets are designed, commissioned, operated and then redesigned, modified, or added to, the digital twin and asset information model need to be kept evergreen. The convergence of information technology (IT), operations technology (OT) and engineering technology (ET) feeds the digital twin. In addition to communicating the current state of the asset, the digital twin can perform operational and engineering simulations to model the performance of an asset over time and evaluate options to improve performance. Essentially, the digital twin connects the data from IT, OT and ET in a single view, allowing the team to validate, visualize and analyze all plant data in any format and from any data storage location. A digital twin environment that is open, interoperable, connected and contextualized enables true collaboration between engineering, operations and maintenance.
Digital Transformation
Digital twins are transforming plants to keep them ahead of the competition. Everyone from the plant floor to the boardroom needs insights to make more informed, data-driven decisions. Digital twins provide a necessary, federated view of all necessary systems and data, giving workers at all levels the insight needed for overall success.
- Reliabilityweb Mapping the Uptime Elements to Your Asset ... ›
- Reliabilityweb Asset Performance Management 4.0 and Beyond ›
- Reliabilityweb Redefining Asset Performance Management ›
- Reliabilityweb Digitalizations Strategies for Reliability and Asset Management ›
- Reliabilityweb Matterport To Showcase Impact of Digital Twins at Space Jam Competition ›
- Reliabilityweb Refinery of the Future initiative provides advanced decision-making capabilities to reliability teams ›
- Reliabilityweb Asset Performance Management Software ›
- Reliabilityweb Asset Performance Management Software ›
- Asset Performance Management - APM software | ABB - Industrial ... ›
- Asset performance management: Driving value beyond predictive ... ›
- Asset Performance Management Software | Emerson US ›
- Asset Performance Management Software | AVEVA ›
- Asset Performance Management Software & Solutions | IBM ›
- Asset Performance Management (APM) Software Solutions ›
- What is Asset Performance Management (APM)? | ARC Advisory ... ›
- Definition of Asset Performance Management (APM) - IT Glossary ... ›