
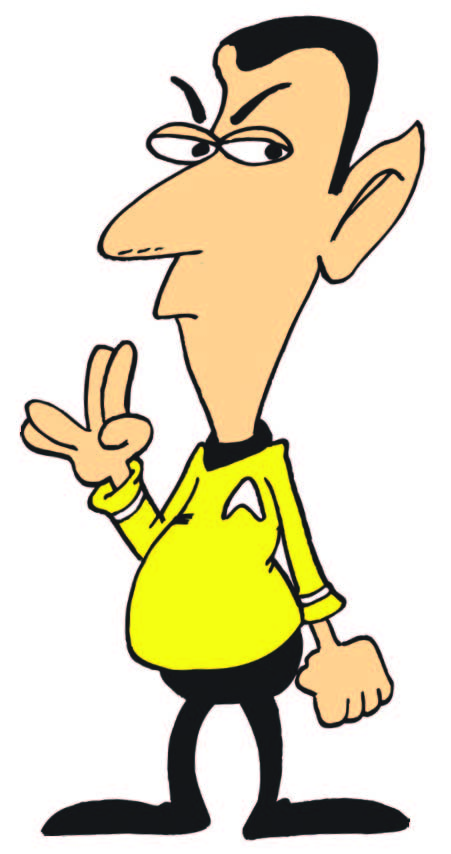
Seeing it listed among ultrasonic instruments for predictive maintenance (PdM) reminded me of the opening of the “Star Trek” television series: “Space, the final frontier. These are the voyages of the Starship Enterprise. Its five-year mission: to explore strange new worlds, to seek out new life and new civilizations, to boldly go where no man has gone before.” -- Captain James T. Kirk of the Starship Enterprise.
Within the past 15 years, ultrasound instruments for predictive maintenance have seen phenomenal changes as they evolved from analog to digital instruments. Today’s ultrasonic instruments are performing analysis that’s far from just trending decibels over a period of time. But, has ultrasound reached its final frontier? Are we at the point where we say, what’s next?
Within the past 12 years in airborne ultrasound instruments for predictive maintenance, we saw the introduction of an instrument with its internal recorder storing and displaying data on a never before seen large 2 x 2.5 inch screen. It included decibels (db), frequency (kHz), data point, sensitivity and more all visible on-screen at one time. It was viewed as the latest and greatest.
Yet, in June 2010 came an ultrasound device with touch screen, onboard camera, laser pointer, internal MP3 recorder, temperature and decibel readings, and unique only to this instrument, a massive display screen that supports in-field viewing of time series (TS) and fast Fourier transfer (FFT), separately or simultaneously. The “wow” factor was there! See Figures 1a-d.
Figure 1a: Fast Fourier transfer (FFT) displayed on a touch screen ultrasound unit during an in-field motor bearing inspection.
Photo courtesy of UE Systems, Inc.
Figure 1b: A photo and database report captured by an ultrasound intrument with advanced technology features.
Photo courtesy of UE Systems, Inc.
Figure 1c: Typical touch screen.
Photo courtesy of UE Systems, Inc.
Figure 1d: Time series (TS) and fast Fourier transfer (FFT) simultaneously displayed on touch screen ultrasound device.
Photo courtesy of UE Systems, Inc.
Four months later in October 2010, the latest in ultrasound for predictive maintenance instruments was introduced, featuring an on-board SQL database to capture and manage survey data in the field and synchronize with PC data, providing in-field alarms and analysis. It was described as a "building blocks" concept that set the stage for even further progressive and smart ultrasound instruments that get used every day, including the addition of an accelerometer to measure vibration severity measurements. See Figure 2.
Figure 2: An ultrasound instrument with accelerometer.
Photo courtesy of SDT North America
With more changes in the past three years then in the past 12 years, you can’t help but wonder, where do we go from here?
The skill level of today’s maintenance technicians vary from general maintenance techs to certified techs in the various mechanical skills to mechanical engineers with hands-on real-world maintenance experience. So it’s no mistake that today’s ultrasound instruments offer various models that can perform various tasks, such as temperature, rpms, record and store wav-files and capture digital pictures, and are equipped with laser pointers, Bluetooth, touch screen display panels that can simultaneously display time domain (TD) or FFT and now even take vibration severity measurements. The latter, offered as an accessory, can be considered the next major step forward for ultrasonic condition-based monitoring. Oh dear, did I write, ultrasonic? Maybe I should have written “high frequency” condition-based monitoring?
I know of a few vibration and ultrasound technicians that for the past 25 years have been performing Ultrasonic Down Conversion (UDC). That is, transferring the Ultrasonic Down Converted (UDC) high frequency signal from the headphone jack of an ultrasound receiver and playing the sound file through spectra analysis software.
It was in the early 1990s that I first experienced UDC, when a leading manufacturer of ultrasound instruments published an article detailing the process of linking a portable ultrasound to a vibration analyzer by simply taking the signal from its headphone jack (output) to the vibration analyzer.
Then in the late 1990s, we saw the introduction of a set of headphones as an accessory to vibration analyzers to listen to high frequencies above 20 kHz. Many vibration technicians found it useful to listen to ultrasound to aid them in the diagnostics of a motor. Other ultrasound instrument manufacturers/users were most likely performing similar tasks utilizing the UDC. I personally was not familiar with the other manufacturers until the late 1990s.
I once wrote about the use of ultrasound and vibration in a previous “Ultrasonic War Stories” newsletter (UWS No. 58 titled: “U.S. Submarine Fleet Listening to Valves Opening & Closing”).
In the article, I wrote: "While visiting with a vibration tech at the Performance Monitoring Team at Naval Station Pearl Harbor Sub Base in Hawaii, I was shown how he used an ultrasound device with his vibration box to assure the valves of the main ballast tanks were closed completely and not bleeding air or allowing water intrusion. He stated a valve gives off high amplitudes of noise as the valve is closing and is completely quiet as the valve is ‘fully’ closed. During this application the Time Domain (TD) or Fast Fourier Transfer (FFT) signal easily detects the condition”.
Simplicity… Leonardo da Vinci was quoted as saying, "Simplicity is the ultimate sophistication." The meaning is not to be mistaken as simply a simple tool is better. But perhaps as Albert Einstein put it, “Everything should be made as simple as possible, but not simpler,” is a better interpretation to da Vinci’s quote.
Many have looked at ultrasound as being that predictive science that does not require a college degree or two years of advanced calculus to understand it. Rather, it’s an instrument that a technician could simply pick up and be very familiar with its use within minutes.
Ultrasound, as I have stated many times, is for the technician, the reliability engineer and those individuals who just want to lower plant utility costs or reduce downtime yet still interface and/or complement all other PdM technologies, such as vibration or infrared thermography. But ultrasound should never be mistaken for “just” a leak detector.
Sitting in on one of the many breakout sessions at the 2012 International Maintenance Conference sponsored by Reliabilityweb.com this past December in Florida, I was reminded of how many of you are still not familiar with ultrasound theory, complex applications, or even some of the more general applications as it pertains to predictive and preventative maintenance inspection, particularly electrical inspection.
One presenter in a breakout session mentioned that he was unsure if ultrasound would have detected the corona discharge they had discovered with the corona camera. Almost assuredly, from what I saw in his presentation, the decibels would have been loud and clearly discernible.
Uptime magazine’s “Best Maintenance Reliability Program Awards” recognized several companies for their very deserving reliability programs. The programs using ultrasound ranged from little experience to expert. Don’t kid yourself. A world-class reliability program is not without an ultrasound program. A great reliability program starts with knowledge; knowledge that your average salesman or distributor may not be able to provide.
In the future, I would like to see all the winners of the “Best Maintenance Reliability Program Awards” return again and again with more success stories, more cost savings and more familiarization regarding the ultrasound program within their reliability program.
With advances in technology, circuitry, firmware, software and data acquisition, ultrasound may empower today’s technicians to move laterally or vertically as their role as reliability technicians changes. Some technicians may simply move laterally, combining vibration or signal analysis with the use of ultrasound. Others with no previous understanding or knowledge of ultrasound, vibration, or signal analysis may have to seek out training for a better understanding of how they all pertain to high frequency condition- based monitoring in order to move vertically. But regardless of technical experience, the average person or the average technician of any skill level can certainly use an ultrasound instrument to locate compressed air leaks.
What’s next? Will vibration boxes have accessories capable of performing an infrared scan or detecting an air leak? Will the next generation of instruments be able to perform those monotonous tasks of trending bearings, scanning electrical switchgear and locating compressed air leaks in some strange and effortless new way never seen before?
I contracted with a pulp mill recently to locate vacuum leaks within the evaporator system. I asked what ultrasound instrument they had on-site and they replied that they have none. A major pulp and paper facility and there is no ultrasound instrument on-site? Come on! When I heard this, I could only imagine the missed opportunities for cost savings. Compressed air, steam leaks, steam trap diagnostics, acoustic lubrication and motor bearing inspection, just to name a few. Not to mention the electrical inspections of switchgear or substations for corona, tracking, or arcing. Electrical inspection, in particular, could save the life of someone, or at the very least, prevent an unscheduled shutdown.
Define your goals, define your reliability program, define your ultrasound program within your reliability program and define what you really know about ultrasound theory and applications. Then get the training you need to meet the goals.
I am excited about the future of ultrasound and predictive maintenance. I am hopeful, in a time when manufacturing is down and we are seeing cuts in technology and research, that designers will become even more creative by defining the wants and needs of the reliability technician.
- Reliabilityweb Ultrasonic Electrical Inspection: Corona, Are You ... ›
- Reliabilityweb Using Ultrasound And Infrared As Complimentary ... ›
- Reliabilityweb Condition-Based Monitoring and Acoustic Lubrication ›
- Reliabilityweb Ultrasound Worth It's Weight in Gold ›
- Reliabilityweb Ultrasonic Condition Monitoring ›
- Reliabilityweb Ultrasonic Superheat Bypass Valve Inspection ›
- Reliabilityweb Vibration & Ultrasound Technologies: A Possible ... ›