It is estimated that almost half (45 percent) of global electricity is used by electric motors. Electric motors drive a considerable amount of equipment in almost all industries, from power generation to water and food supply to consumer products. The importance of electric motors in modern society cannot be understated. It is because of this vital role that it pays huge dividends to keep your electric motors running efficiently through a quality reliability program that includes energized and de-energized electric motor testing (EMT).
Electric motor test instruments have become extremely effective reliability and diagnostic tools for motor and motor circuit testing. Significant improvements in motor longevity and overall plant reliability may be achieved through proper implementation of this established technology. But, as with any new program, there will be growing pains. These start immediately upon receipt of your test equipment.
Who should conduct the testing?
When should testing be conducted?
Are procedures in place?
If not, what procedures need to be developed?
What should be tested?
There are eight steps that, if followed, will enable successful and effective EMT for your reliability program.
Personnel Preparation
As with any endeavor, the key to success is knowledge of the task to be performed. With EMT, this means a thorough understanding of the equipment to be used, including test capabilities, diagnostic strengths and weaknesses, and in-depth knowledge of the equipment to be tested.
Equipment capability information is usually provided by the motor tester manufacturer through initial training. A comprehensive knowledge of motor operation and failure modes is also necessary, but it’s not something easily obtained and is rarely provided by test equipment manufacturers. Apprentice training, experience and specialized training are the most effective means of gaining the necessary knowledge.
Developing proficiency is another challenge. This is where you don’t want to learn by your mistakes. Making erroneous calls and missing significant problems will detract from the credibility of the equipment, the technician and the reliability program. Most industrial facilities have spare motors on hand, so when first starting to test, test warehouse spares, then expand to acceptance testing. This will provide you with the time to learn software and test capabilities and develop the proficiency to test operational motors with competence and expedience.
Preparation for Equipment to Be Tested
What equipment should be tested? Perspectives can vary widely in answer to this question. Criticality is in the eye of the functionary at your facility. What is critical to production may not be as critical to the maintenance or safety departments. The best way to address criticality isj from four basic perspectives:
Operational criticality – Straightforward and based primarily on operating voltage:
- Medium / high voltage / frequent starts;
- Medium / high voltage;
- Low voltage / frequent starts / high horsepower;
- Low voltage / high horsepower;
- Critical variable frequency drive (VFD) powered motors;
- Nonredundant critical motors.
Medium and high voltage equipment cost significantly more to repair or replace and may require prolonged lead time for replacement. Frequently started motors, at any voltage, fail more regularly than motors that run continuously or start infrequently. Motors driven from VFDs normally run hotter and are subject to more rapid thermal degradation of the insulation. Some motors of fractional horsepower may be critical. For example, a 1/4 HP lube oil pump for a 6000 HP sleeve bearing motor is as critical as the 6000 HP motor.
Safety criticality – Quite simply: Can someone be killed or injured if this equipment fails?
Logistical criticality – This is based on availability of repair facilities and replacement parts. In this world economy, parts may have to be manufactured halfway around the globe. This creates a prolonged downtime for the failed equipment and a possible significant effect on the process.
Environmental criticality – Asks the question: Will failure of this equipment cause environmental damage, such as a toxic effluent release or excessive air pollution?
Get all the key players involved to determine equipment criticality. Sit down and discuss priorities, maintenance difficulties, safety and logistical issues and come up with a list of critical assets. Once an equipment list is developed, it should be organized into routes. Plan so a maximum number of assets can be availed in each location. Jumping around reduces productivity. Routes should have a recurring periodicity based on criticality.
Figure 1: De-energized testing is important as it provides an opportunity to test insulation

Figure 2: Surge and Hipot testing tests insulation between turns, coils, phase and to ground
Preparation of Test Equipment
In order to perform motor testing effectively, the test equipment should be in optimal condition. The tester should be in calibration with the most recent updates to the operating software. (Note: When updating software, be aware of possible compatibility issues. New software updates should clearly explain any operating system (OS) that is and is not supported.)
Software upgrades are essential. Many times, they correct inaccuracies or provide important safety procedures or steps. The associated equipage should be inspected and tested, as applicable, to prevent problems when in the field conducting tests. Conduct a check of the equipment the day before testing is scheduled. A simple generic checklist will help with the readiness of the equipment:
Checklist for Effective Testing
- All batteries operable and charged
- Deep cycle batteries as required
- Test leads are free of any nicks or cuts in the insulation
- Voltage clips or test clips are clean and free of any foreign debris or corrosion
- Voltage clips or test clips are snuggly threaded or make a tight fit on test leads
- Current probes have good batteries, if applicable
- Inspect power cords for nicks and breaks in the insulation
- Current probes’ jaws are clean and free of any foreign debris at both the top and hinge point
- Current probe spring tension is good
- Test lead connection points on the test instrument are clean and free of dust and foreign debris
- All electrical and data port cables on your test instrument are properly connected
Check Operational Status of the Tester
Prior to the acquisition of any test data, a quick operational test of the motor test instrument should be conducted. The use of a small test motor or stator will verify that the acquired de-energized test data is accurate or repeatable.
To verify accurate energized data, perform a quick power quality test. Place all current probes on one phase cable and run the test. Compare bus phase voltages to acquired voltages and confirm all amperage readings are the same. Once you feel comfortable that you are collecting reliable data, begin your testing route.

Figure 3: Samples of hand-held instruments
Maximize the Amount of Circuit Under Test and the Amount of Load on the Circuit
If you are devoting the time to conduct testing, you should test as much of the circuit as possible. De-energized testing is usually conducted downstream of the de-energized contactor. With de-energized testing, connections made upstream will identify circuit anomalies between the connection point and the motor. Once identified, circuit isolation can be conducted and the source localized.
Energized testing should be performed from the starter cabinet. Connections should provide at least one local level of circuit protection above the point of connection; for example, connect on the load side of the main breaker or load side of the fuses. Energized testing can be used to observe voltage and current fast Fourier transform (FFT) data to isolate spectral peak sources from upstream or downstream of the test connection point.
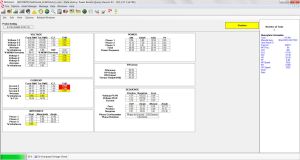
Figure 4: Power quality data showing high harmonic distortion in phase to phase and neutral voltage
Verify or Confirm Identified Anomalies
When a potential problem is identified, it is just that, a potential problem. You should take steps to validate that it is, in fact, a problem. Sometimes, erroneous data or unique characteristics of the equipment under test may give indications of a fault. You should perform all possible equipment checks and run additional correlative tests to validate your indications. Let’s say, for example, your test data indicates a possibly high resistance connection. Check your test lead connections and rerun the resistance tests. If you get a current unbalance, check equipment loading to ensure the unbalance is not due to insufficient loading. If the load is sufficient, save the data and run a quick power quality test, with all the current probes on one phase to make sure you do not have a defective probe. If you have field pole pass (Fpp) frequency sidebands indicating possible rotor bar anomalies, check for swirl effect, current modulation, increased current draw for a given load and reduced inrush current with longer start duration. These simple checks and correlative measures can prevent erroneous data that leads to bad calls, which can cast doubt on either you, the technology, or both.
When Possible, Correlate with Other Technologies
When possible, you should correlate acquired data with other technologies. This helps confirm the existence of a problem and helps quantify the severity. Sometimes, reliability technicians tend to try to be a “one-man band.” But, working together as a
reliability group will yield immeasurable results. Reliability technologies are like a set of wrenches or sockets, they all have specific purposes, but overlap.
When different wrenches or sockets are used together, you can work on most anything. The same with reliability technologies; when used together, you can diagnose most any problem. The proper use of vibration, ultrasound, oil analysis, infrared and electric motor testing can provide a maintenance environment that has minimal undiagnosed failures, resulting in maximum productivity and/or reliability.
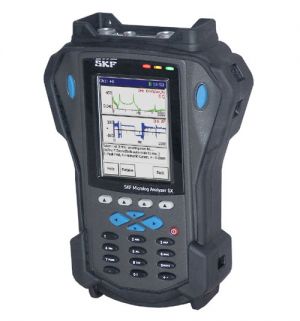
Figure 5: Vibration monitoring is a great correlative test
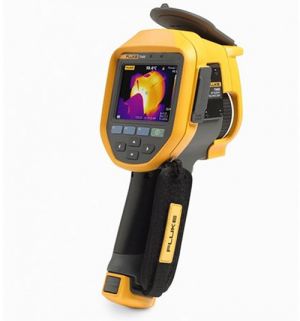
Figure 6: Infrared provides correlation for indications of unbalanced resistance or current
Generate Effective Reports and Communications
Believe it or not, reporting is probably the most important aspect of an effective motor testing program. The report is your deliverable. It can be the basis on how you are judged as a motor test technician. If you are a service-oriented company, you already know or should know this. In-house programs tend to sometimes neglect or minimize reporting, which works to the overall detriment of the program. Budget expenditures are based on perceived value of the desired item. If your motor testing program does not appear effective, you may not receive the funding level you require.
Not only do you have to generate effective reports on identified anomalies, you need to generate updated reports on the overall success of the program. Work with management to establish performance metrics or key performance indicators (KPIs). Bar graphs showing the number of identified and corrected anomalies should be posted in high visibility venues. Display monthly and yearly discrepancy counts; hopefully, it shows a marked decrease. Display the budget reductions for motor rewind and replacement or the number of rejected motors not put into service that may have failed prematurely. Specific examples will help you illustrate your point. Use the data you gather to not only identify and repair problems, but also to demonstrate the effectiveness of the program.
Communication, in addition to effective reports, is key to your program’s success. You should have a network of communication established between you and middle and upper management, maintenance and production departments, and other predictive maintenance (PdM) technology personnel.
Communications with planning, safety and logistics departments are also important for procedural and material support. Integrate your electric motor testing results into the site’s enterprise asset management (EAM) reporting to further support these types of communication. Other areas where communication is important are with the motor shops, motor manufacturers, the tester manufacturer and your electric motor testing knowledge provider.
An effective motor testing program should be part of an effective reliability program. The use of these steps will provide your program with a significant and highly effective tool as part of a world-class maintenance program.