Greenfield Global’s ethanol plant in Varennes, Quebec, Canada, demonstrates the power of maintaining and evolving a strong reliability plan. Reliability is a key term in manufacturing that plenty of people talk about, but often find difficult to tackle in a practical way. Often, when discussing reliability, people imagine it to be achievable only for large scale, high capital organizations with a great deal of manpower. This misunderstanding stems from the misconception that reliability is a goal: just put the right equipment in place, spend enough money and somehow the plant will become reliable. This couldn’t be further from the truth.
Reliability is a journey, rather than a simple goal. The goal of reliability is not to reach the end, but rather to constantly evolve...
Reliability is a journey, rather than a simple goal. It is a cultural mind-set that must permeate every level of an organization to be truly effective. The goal of reliability is not to reach the end, but rather to constantly evolve, always looking for ways to improve organizational processes and assets with the goal of constantly doing better than before.
Building a Reliability Culture
The Greenfield plant in Varennes manufactures fuel grade ethanol, distillers grains, carbon dioxide (CO2) and corn oil, running on a lean staff of only 56 people. Over the years, Greenfield has managed to outperform hundreds of similar plants across the continent with larger staffs and bigger budgets. In the face of rising energy prices, the plant has consistently managed higher output at lower costs for years, all because of a focus on reliability. As a result, the Greenfield ethanol facility was chosen as Emerson’s 2016 Reliability Program of the Year.
When the plant was constructed 10 years ago, Greenfield knew from the very beginning that a focus on reliability would be essential to the way the company wanted to do business. Because the plant runs a small staff, Greenfield makes a concentrated effort to hire people who have a strong background and belief in the value of a reliability culture. A culture of continuous improvement is essential to operations, maintenance, logistics and production, and all other sectors work together to improve every part of the plant at all times. Even in top-level management, maintenance reliability is not considered an expense, but rather an investment.
Following the Map
From the very first day at the Varennes plant in 2007, it was clear that expansion would be necessary. Management’s goal is to increase the feed rate of the plant every year to produce more using the resources already in place. When the implementation team began a reliability program, the common tool for guidance was the reliability pyramid. While that system worked well in the early days, plans have evolved to follow a reliability road map developed in partnership with a local business partner. During an asset’s lifecycle, reliability enhancements integrate all the elements necessary to extend and improve its functionality.
But, reliability doesn’t stop with the initial plan for an asset. The reliability team constantly audits the system, looking at all the road map’s elements to see where functionality can be improved for the next year. For example, the thermal oxidizer is the heart of the plant. If the oxidizer doesn’t run, the whole plant shuts down. Developing a quality maintenance strategy for this asset was as simple as following the road map. The first step was a failure mode and effects analysis (FMEA) to determine the most common failure modes and their causes and effects.
The plant uses the FMEA information to determine what technologies will achieve the lowest possible risk for a given machine. As with many assets, an early warning of failure on the thermal oxidizer can come from abnormal vibration. Technicians detect such aberrations with portable vibration analyzers, which are used on monthly vibration rounds to ensure maintenance receives early warnings of any impending failures. The collected data is stored, tracked and analyzed.
Based on feedback received in the previous steps, the next step on the road map is to move toward preventive maintenance (PM) to keep the equipment functioning. PM tasks help ensure the plant is never caught off guard with catastrophic equipment failure, delivering peace of mind that unplanned shutdowns will be few and far between. By keeping a close eye on all the failure modes of the thermal oxidizer, it is possible to plan maintenance around scheduled shutdowns, avoiding unplanned downtime.
Finally, management follows up on all work with internal metrics. It is essential to know which techniques are providing results. The problems identified in the first stages of the road map shouldn’t be causing plant shutdowns anymore. If they are, the maintenance team knows there is more work to do in analyzing methods and technologies to ensure each plan is optimal for its piece of equipment.
Evolving Criticality
The Varennes plant also takes a few unconventional steps on the road map to reliability. One of these steps is a goal to constantly reassess asset criticality ratings. By continually updating the plant’s criticality assessment, maintenance ensures the criticality ratings assigned yesterday are still valid today. It may seem like a device is either critical or not, but in a constantly evolving plant, criticality status can change.
For example, an agitator installed in the early days was labeled non critical and allowed to run to failure (RTF). It was assumed that if the agitator failed, a couple of hours without agitation on the tank wouldn’t have a significant impact on production. However, after a couple of breakdowns, operations quickly learned that the device was far more necessary than first suspected. As such, the device rating was changed to allow for regular monitoring during rounds.
Constantly revising criticality ratings also allows maintenance to keep an eye on moving bottlenecks in production processes. Often, a change in one sector of the plant, usually with the goal of removing a bottleneck, will cause a new bottleneck further down the line. When throughput is increased in one sector of the plant, other equipment may become more critical to accommodate the increased feed. Monitoring criticality allows plant staff to make the changes necessary to keep processes moving smoothly.
Ready for Anything
When the Varennes plant opened, the status quo was multiple planned shutdowns a year. By 2010, the reliability team had reduced the number of shutdowns to two and in 2011, the number was reduced to one. Future plans will allow for one scheduled shutdown every 18 months. Much of this improvement is a result of the reliability plan elements that are constantly improving. But, some came directly from new methods put in place in later years.
To keep an eye on critical equipment, technicians began using wireless gateways coupled with transmitters that allow intermittent online monitoring of problem assets. The use of wireless devices allow technicians to keep a piece of equipment running during examination so they can use a monitoring program to get a clearer picture of what is causing any malfunction, as well as avoid process upsets with failures on critical equipment.
A kitting plan speeds maintenance during both planned and unplanned equipment outages. In the computerized maintenance management system (CMMS), all jobs have extensive part lists and clear work orders. The goal is to anticipate all possible steps of the maintenance task. Kits stand ready with a printout of the work order for a maintenance task and all the parts necessary to complete the job. When a planned shutdown happens, these kits are moved in advance to the assets where they will be used. In the case of an unexpected shutdown, everything is in one place, making the kit grab and go, saving critical time.
Before the kitting plan, a common maintenance task, such as a sheave and V-belt replacement, would take significantly longer. Often, a technician would go to the repair with just the belt and no sheave or bushing in hand. Depending on the equipment, it could take five to 10 minutes to travel back to the shop and grab more parts. Before the kitting process, changing a belt and sheave could commonly take two and a half hours. With the kitting process in place, maintenance has cut that time down to one or one and a half hours.
The Value of Constant Learning
Reliability success has not only come from process changes and equipment improvements. At the heart of any good reliability program are the people responsible for implementing the program. Greenfield was lucky to start with a staff that understood the value of reliability, and reliability teams have helped to cultivate that understanding into a culture.
The core of the plant’s reliability culture is developed from training. Two times a year, each person at Greenfield undergoes an evaluation. The evaluations determine what kind of training will help individuals be better at their jobs. The goal is for all employees to constantly strive for a higher level of experience and performance.
At the heart of any good reliability program are the people responsible for implementing the program.
Both external and internal training play a role in the reliability culture. Greenfield has used outside vendors to help develop and roll out training courses for employees to help them better understand the components they are working with. These experts help operators and technicians get the most out of the equipment they are using.
Greenfield gains even more advantages when those same employees use their training and experience to cross-train other employees throughout the plant. For example, an operator and a maintenance technician on a pump might cross-train each other. The operator learns how the equipment runs, why it does what it does and what can damage the equipment when it is run improperly, leading to better troubleshooting. The maintenance technician learns how the equipment is used and how the process works so it becomes easier to diagnose issues, such as underperformance or intermittent failures. At the end, everyone is speaking the same language, which makes for more efficient and accurate diagnosis and repair of issues on the plant floor.
....Every failure is a learning opportunity
that improves the reliability program.
Turning Action into Results
The ultimate result of a constantly evolving reliability improvement plan has been less downtime and improved production throughout the plant. In eight years, production increased by 80 percent, while maintenance costs only increased by 14 percent. In addition, energy costs have decreased significantly. Overall, energy costs are 74 percent of what they were in the plant’s first year of operation, even though energy cost increases should have them at 180 percent.
The motivation of the Greenfield team is much higher than it was in the early years. The plant no longer operates in reactive mode, meaning the team can work on improvements rather than constantly trying to put out fires.
The goal is not perfection. Greenfield experiences failures just like every other plant. The difference is, with every improvement, the team’s reaction gets faster. At Greenfield, every failure is a learning opportunity that improves the reliability program. Users learn from
everything and dedicated people make them successful. The reliability team is positive, takes initiative and brings good ideas. Many key improvements came from people on the plant floor. Winning Emerson’s Reliability Program of the Year is a direct result of the hard work and innovation of those people. Because of a dedicated and innovative staff and a vision for the future, the Varennes plant continues to improve every day and will only run leaner and with greater efficiency as time goes on.
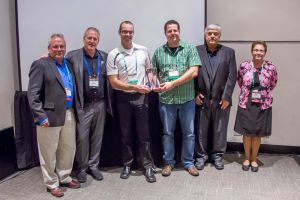
Thivierge and Fyfe-Leblanc with the Emerson Reliability Program of the Year judges