Heinz Bloch
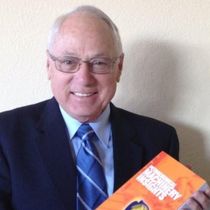
Heinz P. Bloch is a professional engineer with offices in West Des Moines, Iowa. He advises process and power plants worldwide on reliability improvement and maintenance cost reduction opportunities. Heinz is the author of 17 full-length texts and over 400 papers and technical articles. His most recent texts include "A Practical Guide to Compressor Technology" (2006, John Wiley & Sons, NY, ISBN 0-471-727930-8); "Pump User's Handbook: Life Extension," (2006, Fairmont Publishing Company, Lilburn, ISBN 0-88173-517-5) and "Machinery Uptime Improvement," (2006, Elsevier-Butterworth-Heinemann, Stoneham, MA, ISBN 0-7506-7725-2)