A call about a line outage or a message from an operator that “something’s wrong” is not a good start to the day. Early warning signs are there to be found. However, maintenance engineers can’t be everywhere at once. Time between data rounds is when something can go wrong, and some equipment isn’t even on a data collection route.
Many experienced maintenance professionals are at or near retirement age. With fewer replacements on the horizon, manufacturers are increasingly looking to industrial technology to maximize worker productivity to unlock capacity and improve overall equipment effectiveness (OEE). Better uptime starts with better data. These four technologies help provide better data quality and access to the teams that keep plants up and running.
Cloud- and Web-Based Software Technology
Isn’t it odd that monitoring professionals walk routes between equipment to gather data, yet there is consumer technology on the market to see inside a refrigerator from a cell phone?
This technology exists for turbomachinery. Analysts can decide which plant, line, or asset they need to visit to best impact reliability before grabbing their hard hat or car keys. The goal of remote diagnostics is to provide data that, as much as possible, alleviates the need for analysts to be on-site. The concept is simple: connect sensor data to an IT network so experts receive asset health data through a web browser, rather than traveling to collect data with handheld instrumentation and their own senses.
It’s important to note the distinction in data types needed for remote diagnostics. Many systems report overall feature calculations (e.g., root mean square (RMS), peak-peak, 1X/2X magnitude, and so on) and others report full waveform data. Overall, feature calculations alarm on general problems and are used to identify some failure modes. But, feature alarms need a follow-up with waveform data, typically captured by handheld devices, for more in-depth analysis, as seen in Figure 1. If waveform data is the goal, the systems that connect waveform data to the Cloud are the ones that most effectively improve productivity.

Figure 1: Vibration measurement layout showing RMS trend line, wave form, spectrum and envelope analysis.
Web access to waveform data and analysis helps experts remotely diagnose asset health. At minimum, remote analysis provides peace of mind without involving road trips, catwalks, ad hoc plant walk downs, or calls to the expert who is currently out of town. In some cases, remote analysis can prevent a profit draining outage.
Vibration data is one of the primary measurements for asset health, but it’s not the only sensor technology used to diagnose problems. Oil analysis, motor current signature analysis, infrared thermography, electromagnetic signature analysis, and others are used to capture a broader range of failure modes and conduct differential diagnosis. It is important that server software for asset monitoring manages data from multiple sensor technologies. This way, analysts can have more confidence in their remote diagnosis and know where to best focus their time. A more critical piece of equipment may be less of a risk to uptime than a less critical asset with a more devastating issue.
Experienced analysts use their senses to help diagnose equipment problems: does the machine sound, smell, or look off? Software technology exists to convert digitized accelerometer data into an audio file (Figure 2) so analysts can listen for problems as if they were standing in front of the equipment.

Figure 2: Software technology converts raw, digitalized accelerometer data into an audio file so analysts can listen for problems from across the factory or across the country.
Wireless Instrumentation
The biggest cost driver for permanently installed instrumentation is typically installation, including engineering design and a contractor to run conduit for power and Ethernet. Transmitting sensor data wirelessly greatly reduces this cost.
From a communication standpoint, there is no silver bullet. A wide variety of wireless standards and protocols (e.g., Bluetooth, Wi-Fi, ISA100, WirelessHART, LoRa, and several 900 MHz variants) can help vendors assemble wireless instrumentation to cost-effectively pull vibration data from 20 year old pumps, motors, fans and other assets.
Advancements in sensor digitization components, such as analog-to-digital converters, are bringing waveform quality data from the same piezoelectric sensors used with portable systems. These, however, are permanently mounted to the asset and wirelessly connected to an IT network to reduce or eliminate the need for routes (Figure 3).

Figure 3: Wireless instrumentation shown connected to standard, piezolectric accelerometers reduces the cost of high quality waveform data.
Microelectromechanical Systems (MEMS)
Silicon technology companies designing MEMS sensors for mass markets, like gaming consoles, consumer automobiles and smartphones, are using that same design expertise to target industrial markets. MEMS sensors, like most electronic technologies, are continuing to shrink, use less power and provide higher quality measurements. This makes them a good fit to measure vibration data for machine health.
Most MEMS sensors for condition monitoring (Figure 4) are complete with a sensor, signal digitization circuitry, if needed, a battery and wireless radio, all built into mechanical packaging for a specific operating environment. To install, the main difference from installing traditional piezoelectric sensors is the need for a few gateways installed around the plant.
Many MEMS vibration sensors are triaxial and include a temperature sensor. This makes them a relatively low-cost way to connect problematic assets that otherwise wouldn’t be worth adding to a collection route or running conduit to. Instead of having data visibility on only the top five percent of plant assets, maintenance teams can cover the top 20 percent of assets most likely to have issues and contribute to downtime risk.

Figure 4: MEMS-based sensor connected to a vertically installed motor wirelessly sends data to experts for analysis.
Edge Processing Technology
Asset health data is big data. A single pump motor skid with a few triaxial accelerometers connected to permanent instrumentation can generate over 20 GB of data per day. The Cloud essentially has infinite processing capability, however, a plant can’t feasibly push all its sensor data to the Cloud for processing.
Technology vendors in the condition monitoring market are packaging the latest in processing elements into rugged, passively cooled devices to help manage large amounts of raw sensor data before it leaves the plant floor. Most data from manufacturing equipment is benign and, if recorded, would serve only to bog down analysts as they seek the important artifacts within. Smart monitoring devices screen the data looking for predesignated features. When these features, such as RMS or crest factor limits, are found, the data is logged and sent to the server software for access by an analyst.
Route-based acquisition records data at a predesignated time, regardless of asset health measurements. Twenty-four hours after an asset is measured, it could start showing signs of bearing wear that wouldn’t be caught until the next route three months later. By contrast, continuous monitoring equipment records data for a predesignated feature, so teams only get the data they want.
Data captures from start-ups hold valuable information, but can be logistically difficult to acquire. Getting the right person with the right instrumentation in front of the asset at the right time can be difficult. This is especially true when manufacturers have more plants than reliability experts and more reliability experts than instrumentation. On top of those logistics, some startups are unplanned think peaking units for power generators or auxiliary equipment).
Edge processing technology helps manage the big data of asset health monitoring. By continuously acquiring and screening data, maintenance teams have less data containing more information to analyze, which makes more efficient use of their time.
Making Days Boring
Analysts need to take their expertise on-site to the plant. Asset monitoring technology is not replacing their years of experience in keeping turbomachinery spinning. Rather, it’s helping them spend less time collecting data and filtering through useless data and more time focusing on the equipment most likely to cause the next outage. Getting ahead of these problems prevents the excitement from calls about outages and operator messages regarding odd equipment behavior. It makes overseeing equipment boring. But in a good way.
Brett Burger
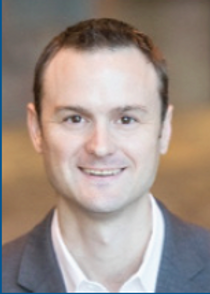
Brett Burger is the Principal Solution Marketing Manager for Online Monitoring at National Instruments (NI). He has experience in a variety of fields, including machine condition monitoring, smart grid technology, sensors, and data acquisition. Brett has been deeply involved with NI’s Industrial Internet of Things (IoT) and showing the value engineers can offer businesses through intelligent, connected, data-centric systems. www.ni.com/en-us.html