When it comes to people and safety in industrial plants, maintenance teams are the ones who are most often in the line of fire and at risk for injury or death.
Why is that?
They spend the most time in the plant in different scenarios and in different plant areas. Whether it’s trudging around the darkened boiler room, crouching under the stalling conveyor, or on a ladder stretching for that leaking flange, they are very often face-to-face with multiple hazards and risks.
This is why if any department should be at the vanguard of safety, the maintenance team must be seen as the leaders of a positive safety culture and behaviors.

Unfortunately, this isn’t always the case. There are always clear warning signs when a maintenance team is exhibiting poor safety behaviors and culture. It is often the fallout of a wider organizational cultural issue, but it still needs to be addressed.
The Worrying Signs to Look for in a Maintenance Team
1. They don’t carry or use quick risk assessments at the job site.
You know, the typical Take Five risk assessment booklets. Most companies have them and most people use them. But if your team doesn’t, then you’ve likely got a serious problem. It may be that your maintainer has done the breakdown or performed the preventive maintenance (PM) task many times before. But hazards are fluid, new ones appear all the time.
Your team needs to stand back and risk assess first before diving in to fight the fire.
Keep an eye out for this one.
2. They often override safety guards or mechanisms when fault finding.
Although most plants have safe systems of work and physical barriers in place, some have loopholes or the potential for work-arounds. In a poor safety culture, the maintainers will exploit them. It’s not unheard of to see maintainers reaching over guards into moving machinery, using a piece of electrical cable to short out a safety switch or energize an electrical contact, or working on conveyor rollers without isolating and locking off the power switch.
These actions are dangerous and often illegal. If you witness these behaviors, you’ll need to intervene immediately.

Figure 1: Warning signs of poor safety behavior
3. They tend to ignore warning signs.
Personal gas monitors alarming. Walking under low conveyors to take a shortcut to the next job. Descending stairs with only two points of contact. Crossing into the forklift truck lanes to get across the storeroom quicker. Ignoring mandatory ear protection. Even when the warning sign is ringing in their ears, they often ignore it.
The list goes on.
Another common indicator is maintainers not reading the safety notes or risk assessment of a PM task before proceeding with the work. They’ve done it before, right? But environments change, sometimes quickly, sometimes gradually. This is why risk assessments are fluid documents that need reviewing on a regular basis.
It all comes down to behaviors, choices and culture.
4. They don’t challenge each other on poor safety behaviors.
One of the key elements of a positive and successful safety culture is people having the freedom and psychological safety to challenge each other if they witness unsafe acts. This can be difficult to do in practice as it may often be a cause of friction and confrontation. But in a team where no one regards each other’s safety as paramount, no one feels the need to challenge anyone. Or if they dare do it, they are made to feel like an outcast.
It is critical to instill a positive challenge mindset in your maintenance team. It’s difficult to do, but entirely worth it if it can save even one life or stop one serious injury.
5. They don’t always adhere to personal protective equipment (PPE) rules.
How many times have you seen it?
Not using hearing protection next to the air blower pump. Removing safety glasses to get a closer look at a steam leak. Not wearing the right gloves to handle blades. Loose sleeves at the lathe. Not bending those knees when lifting an oil drum. These are basics. Pure and simple. And there must be zero tolerance.
So, if you do see them, you need to be a catalyst for change.
And finally, leaving the goriest until last.
6. Several of them have a missing thumb or finger.
Ouch.
Granted, some of these injuries may be “imported” from previous roles and companies. But, it is often indicative of risk-takers being allowed to operate freely in a poor safety culture. And it ends up being expensive for everyone. If you’re like most people, you don’t want your fingers under a hammer blow, inside clamping jaws, or caught between a piston and a push plate.
What to Do If You See Any of These Six Signs
If you’re a maintenance or engineering manager, or even a safety manager, keep your eye out for these warning signs among maintenance teams. They are a sure sign you need cultural change at a local level. This is not to say these problems are confined to the maintenance team. Not at all. In companies and plants with a poor safety culture, it will be endemic and ubiquitous.

And this is where you should require strong, modern leadership to slowly turn around and orient those beliefs, behaviors and actions that will eventually result in positive safety outcomes. Safety leadership from the very top and from yourself.
Jamie Borley
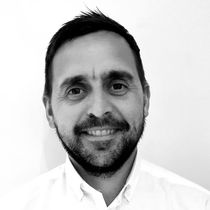
Jamie Borley, Director and Consultant at Assetivo, has more than 20 years of industrial experience in the automotive, steel, paper, FMCG, chemicals, and oil and gas sectors. With academic qualifications in Manufacturing Systems Engineering (BEng) and Maintenance Engineering and Asset Management (MSc), Jamie has a wealth of knowledge and experience in asset reliability, maintenance optimization, condition monitoring, RCA, planning and scheduling, CMMS, and work management. The majority of his work has been in the UK, but has also taken him across Europe and to the Middle East for consultancy, projects and training delivery. Aside from helping companies improve asset reliability and maintenance performance, Jamie collaborates with Dynaway on articles and blogs to contribute to the maintenance community’s body of knowledge and share his insights. www.dynaway.com
From Your Site Articles
Related Articles Around the Web